Pryme Group Opens Manufacturing Centre
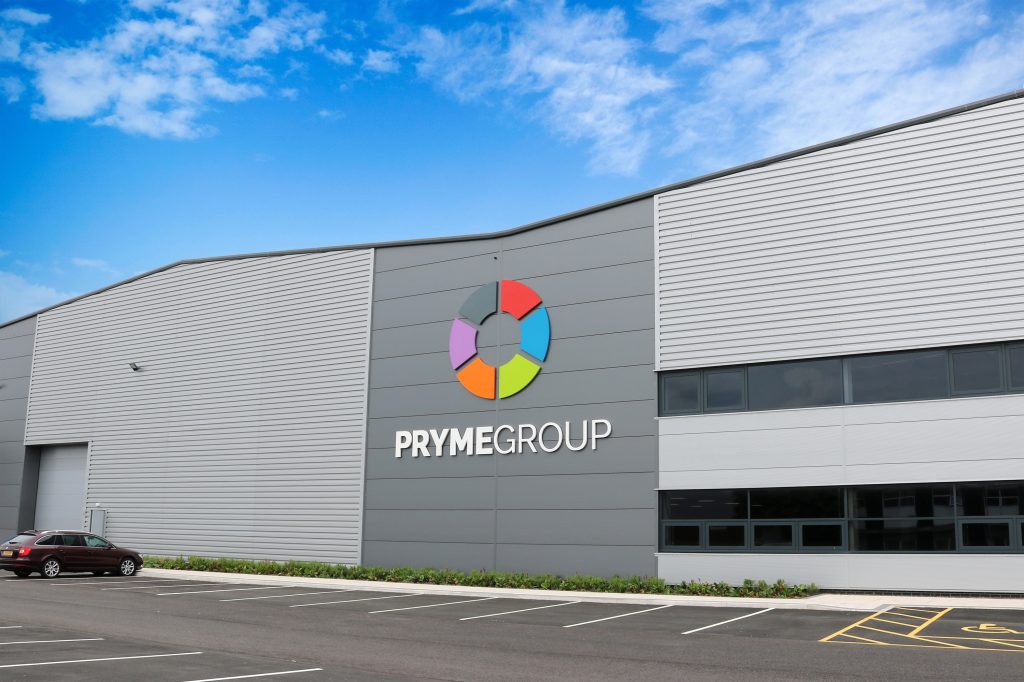
The new, state-of-the-art facility of integrated manufacturing specialist, Pryme Group has been officially opened by Norma Redfearn CBE, elected mayor of North Tyneside. Following £10 million investment, the company has been relocated from nearby Ryton to a purpose-built engineering services and manufacturing centre at the Tyne Tunnel Estate. “We are extremely grateful that Norma took time out of her busy schedule of looking after the interests of the North East business community to visit Pryme Group and find out more about us as a company,” said Angus Gray, CEO of Pryme Group. “I’m excited about what the future holds for the business and the local area. While work is still continuing to allow the site to operate at full capacity, we’ve taken the decision to move staff into the new building slightly earlier than planned to meet demand for our services,” Angus added. With operations across the UK and headquarters in Dundee, Pryme Group provides integrated manufacturing solutions for the oil and gas, aerospace and defence industries. The business expects to more than double its current workforce in North Tyneside from 70 to 150 in the next five years and is actively recruiting for new personnel, including CNC operators. To date, Pryme Group has invested £4.2 million in equipment and CNC machinery with new technology and increased efficiencies expected to result in a boost to revenue and improved on-time delivery .The North East LEP has also provided additional grant funding of £1.35 million through the government’s Local Growth Deal; allowing UK Land Estates to build the unit in North Shields speculatively at a cost of £4.5 million. “I am delighted Pryme Group has invited me to be part of its official opening on Tyne Tunnel Estate. This facility marks exciting times for the company and the prospect of new jobs being created is also great news for our local residents. The council look forward to working with Angus and his team as they continue their growth plans in the region,” said Welcoming Pryme Group to the borough, Norma Redfearn CBE. Pryme Group recently signed new contracts with energy sector clients – totalling more than £3.5 million – for fabrication and machining services with all work to be carried out at the new facility.
Bradford Manufacturing Week Inspires Young People
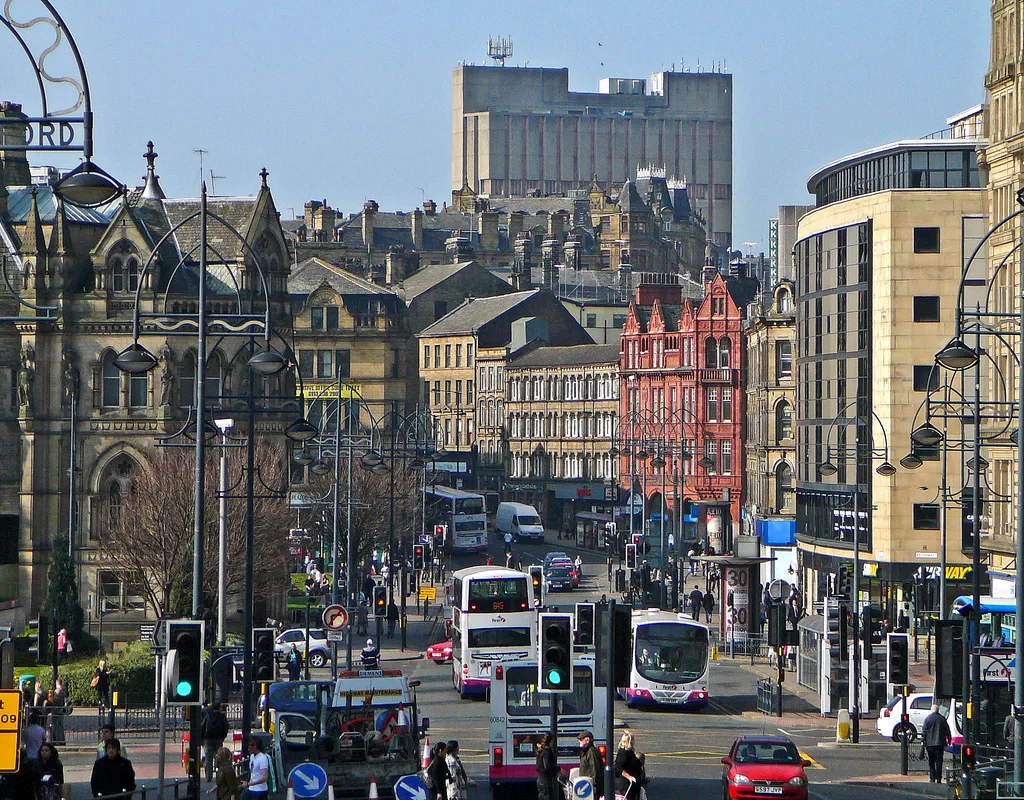
A coalition of manufacturers, commerce groups and social enterprise organisation in Bradford have decided to work together towards inspiring young people to forge a career in the manufacturing industry. Bradford Manufacturing Week, which took place for the first time from the 8th to the 12th of October, aimed to introduce, educate, and persuade teenagers at local schools to consider working in the manufacturing and engineering sector. The initiative, sponsored by Barclays, Gordons LLP and Naylor Wintersgill, welcomed more than half of local secondary schools and provided over 3,000 manufacturing experiences, including workshops, factory tours and work experience. “It really got the pupils thinking, talking and asking the questions that were important to them. The students had really done their research, and many addressed the big issues in manufacturing such as employing women, attracting young people to the sector and whether apprenticeships are the right route to take,” said Nick Garthwaite, president of the Bradford Chamber of Commerce and founder of Bradford Manufacturing Week. Garthwaite also pointed out the role social media had in spreading their message: “Between social media and the interactions in the room, we answered around 20 questions put to us – we were euphoric by the end of the session and agreed, it’s certainly an event to be repeated during Bradford Manufacturing Week 2019.” Among the manufacturers who took part in the event were Whitakers Chocolates, Airedale Chemicals and Seabrook Crisps. Careers guidance firm Aspire-igen was the most prominent social enterprise involved in Bradford Manufacturing Week, helping connect students with local employers. Although Bradford’s manufacturing sector has undergone a long-term decline from the days when 70,000 people walked through the factory gates of the town’s textile mills, it still comprises a sizeable component of the local economy. Around one eighth of all jobs in the Bradford district are in manufacturing compared to 8% nationally. Gross Value Added per manufacturing worker is higher than any other city in the Northern Powerhouse, with a total manufacturing GVA output of £1.5 billion in 2016. Manufacturing & Engineering Magazine | The Home of Manufacturing Industry News
Connected Manufacturing Leaders Summit 2019
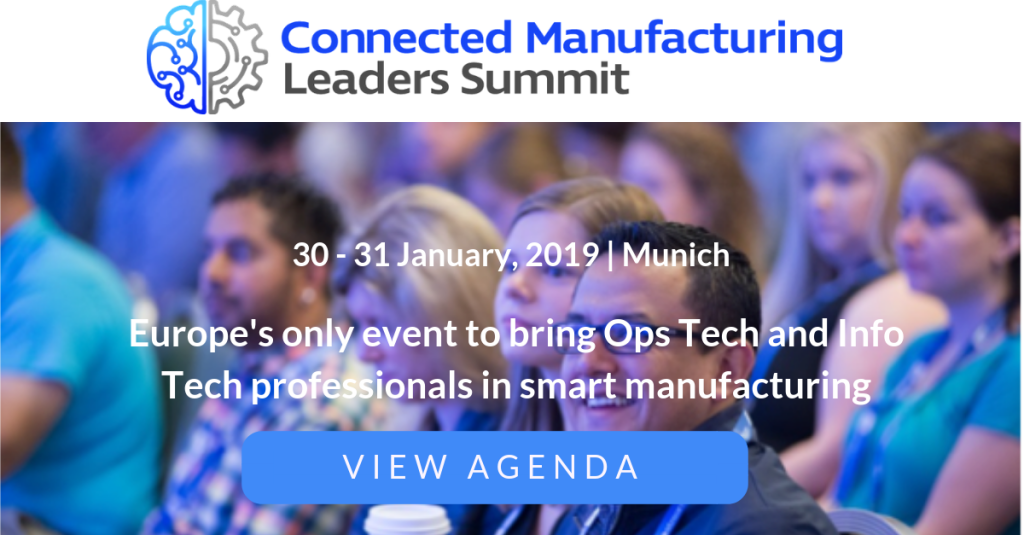
Connected Manufacturing Leaders Summit 2019 : Taking place on 30-31 January 2019, Connected Manufacturing Leaders Summit is Europe’s only event to bring Ops Tech and Info Tech professionals together in smart manufacturing. Senior decision-makers from the leading European manufacturing companies attend Connected Manufacturing Leaders Summit to engage in detailed discussions with their peers, to source solutions and to benchmark their digitalization journeys against competitors. For further information visit our website. With Heads of Manufacturing, Operations and IT attending join 120+ delegates and 40+ speakers from global European companies across several manufacturing industries including Automotive, Aerospace and Defense, FMCG, chemicals and more. With companies under increasing pressure to become more efficient in production, cost-competitive and flexible in their manufacturing processes, it is vital to stay ahead of the competition by driving technology innovation within the business. This is your chance to learn and gain insight, with 15 hours of networking in small interactive sessions. To find out more, download the final agenda here. Get 15% off the current ticket price with code CM19MEM– Book your tickets here. We hope to see you in Munich! Manufacturing & Engineering Magazine | The Home of Manufacturing Industry News Manufacturing & Engineering Magazine (MEM), is a the leading UK based monthly print & digital publication focused on promoting innovation in manufacturing and engineering available here in the UK. We cover : SUSTAINABILITY (Waste & Water Management, Recycling, Energy); INMOTION (Rail, Marine, Aerospace, Automotive, Defence); INFRASTRUCTURE (Oil & Gas, Nuclear, Construction); Healthcare (Medical), TECHNOLOGY(Printed, Connected, Software, Composite); MANUFACTURING (Chemical, Metals, Plastics, Electronics, Electrical); CONSUMER GOODS(Furniture, Electrical, Electronics, Food) to name but a few. We have over 50,000 views of each issue of MEM on average in 2022 and go to print monthly and also publish in our newsletter, (each issue is available free for 12 months digitally). Our focus is aligned across the next 12 months with our global media partnerships around Trade Events and also contains original content.
FBX Solutions Helps LoneStar Group with Massive Move
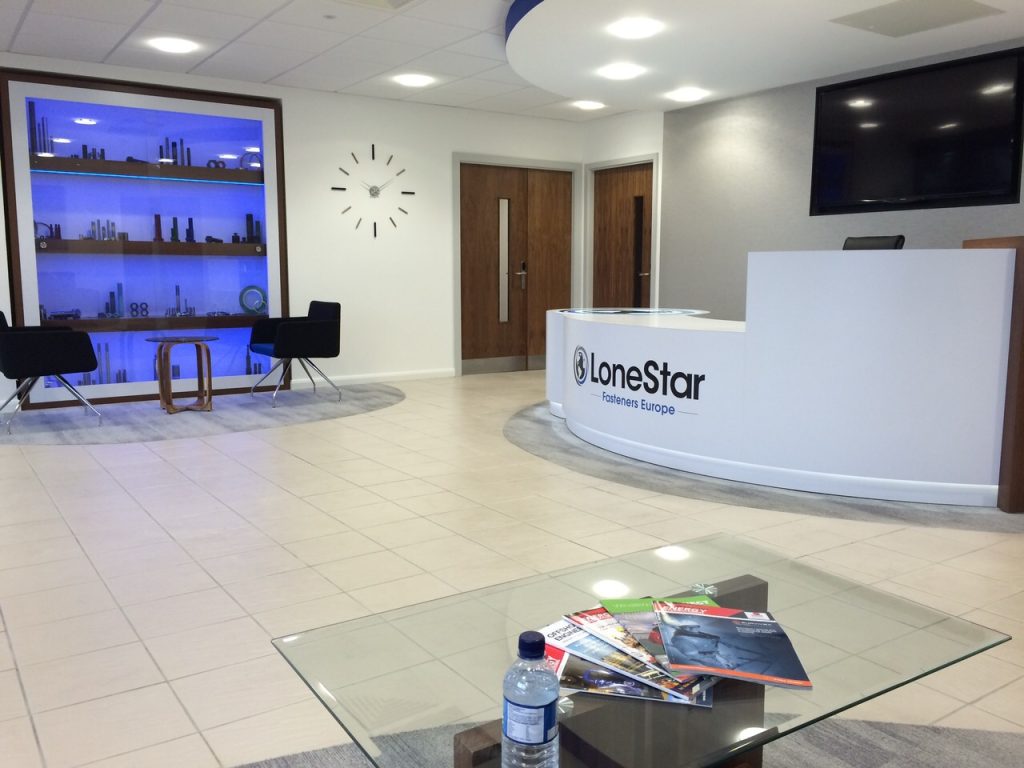
When multi-national engineering group LoneStar needed someone to manage a huge consolidation and relocation project in the West Midlands they knew exactly who to turn to for help – FBX Solutions. LoneStar manufactures and supplies high-performance fasteners, sealing and precision-engineered components for the global energy markets and the company wanted to combine three sites and a head office into one. And the brains behind the move were FBX, who project managed the whole process from start to finish. The result was a new £7.5million, 115,000 sq ft manufacturing and distribution centre of excellence at Universal Point in Steelmans Road, Wednesbury, near junction 9 of the M6 which saw PRD Fasteners, Eurofast Petrochemical Supplies and Triplefast International form LoneStar Fasteners Europe. Set up in 2012 by Managing Director Frank Blahuta, FBX provides a unique service to help small-medium sized businesses in the manufacturing and logistics industries get the maximum value out of their facilities, whether through relocation or optimizing their current one. They were approached by VABS (Value Added Business Solutions) to project manage integrating the company’s three existing sites in the West Midlands – two at Willenhall and one at Bilston – plus a head office in Wednesfield, all operating under one roof. Frank explained: “It was quite a significant process taking three limited companies on four different sites and bringing them under one company’s management on a single site. “We had to look at the size of each space, how they utilised that space and how efficient the companies ran to what they needed. The work included the consolidation of repeated functions across the three limited companies, including HR departments and finance departments, so there was a lot of work to do. “Then running parallel with that, we were asked to look at the prospect of relocating LoneStar to a new site, so we looked at brand new builds and existing builds and how much space they would need. We needed a 115,000 sq ft facility and there was one that had just come onto the market – the old Dreams For Beds distribution centre just off the M6. “So, we put a plan in place with architects, designers and a construction company, leased the building and managed the whole design and redevelopment of the new site.” FBX then picked up and managed the whole move into the new premises, which saw 268 staff move in over two floors. A spokesperson for the LoneStar Group, said: “Appointing FBX Solutions to programme manage our business relocation and consolidation project was the best decision we made. Their industry knowledge and expertise, combined with their professional and reliable attitude throughout, made them an invaluable resource to our company. “Having them onboard meant the whole process ran as seamless as possible and I would recommend the team at FBX Solutions to any business who want to grow, become more efficient or relocate.”
FBX – the Perfect Partner for Managing Your Business Facilities Change
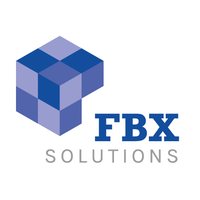
Frank Blahuta, Managing Director of FBX Solutions, explains to Manufacturing & Engineering Magazine how the company is providing a unique service to help small-medium sized businesses in the manufacturing and logistics industries get the maximum value out of their facilities, whether through relocation or optimizing their current one. Modern manufacturing and logistics companies are subject to continual change through expansion, restructuring, downsizing and relocation. Executing such fundamental changes, however, can prove to be a huge headache for small-medium sized companies who may not have the manpower or expertise to put an experienced in-house team in place to manage the complex process of changing facilities. But thanks to FBX Solutions, companies thinking of growing or relocating their business either now or in the longer term can have the expert support they need from the very start right through to completion. Set up by Frank in 2012, the Blackburn-based company has helped several businesses to successfully manage new facility projects and subsequent relocations thanks to their dedicated facilities change management service. And, as Frank explains, having FBX onboard will make the whole process run as seamless as possible to ensure minimal disruption to production. Frank explained: “The engagement from FBX starts at the outset with a consultation with senior management to understand their strategic objectives and how the current facilities will need to change over time. We can then contribute to a feasibility study and assist management to build and present a business case for Board approval. “Thereafter we have the expertise to manage the entire facilities change process to a successful conclusion. We work best in situations where we can become an integral part of the company’s management team for the duration of the project. “We look at everything from the size of the space and how the business utilises that space, to the number of staff they have and how efficient the company runs and identify what they need for the future. “If it’s a complete relocation, then FBX do everything from the assessment of available properties and applying for planning permission to sourcing architects, construction companies and, ultimately, the management of the dilapidation process for your old premises. Then once finished, we accept the building on behalf of the client and can hand the keys over to them when they are ready to move in, or plan and execute the physical relocation on their behalf. “We also assist with the design of lean manufacturing and process flows for the new location which informs the overall design and layout of a facility.” With the areas mentioned above making up only a small part of what the company has to offer, FBX Solutions tailors its service to clients to provide relevant expertise and support as a project progresses through its different phases. So, if you are thinking of growing or relocating your business now or in the future, contact FBX on 01254 832582 or visit https://www.fbxsolutions.co.uk/ to find out what support FBX can provide for you.
What Is Facilities Change Management?
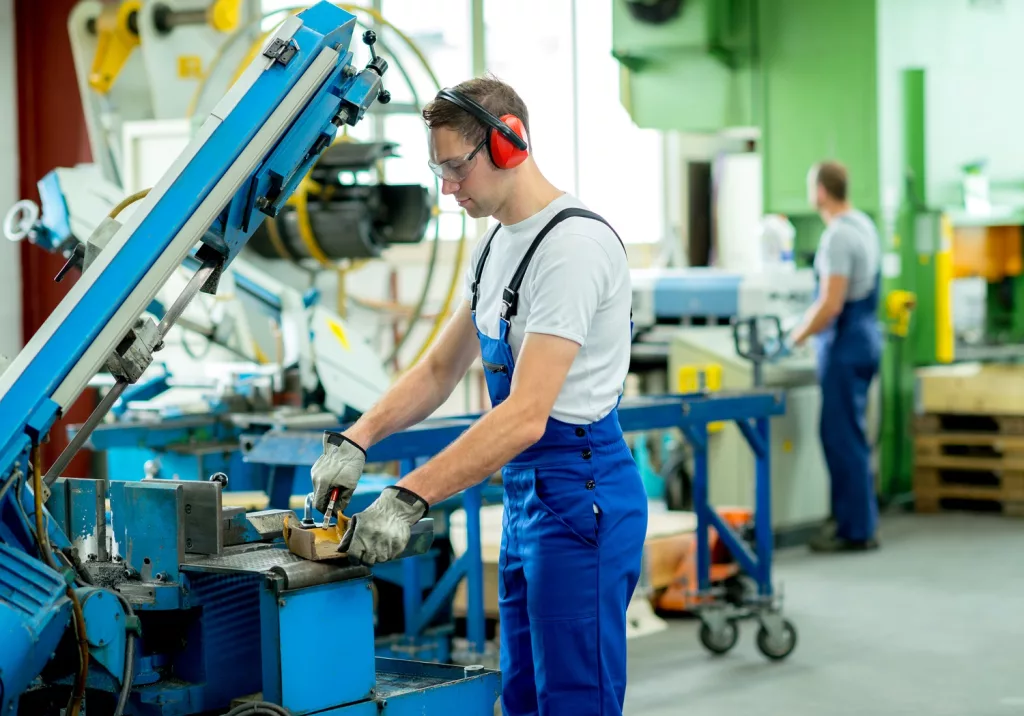
Businesses are set to come across the term ‘facilities change management’ more and more thanks to a Blackburn-based management consultancy company. FBX Solutions help small-medium sized businesses in the manufacturing and logistics industries get the maximum value out of their facilities through facilities change management. But what does the term mean? In a nutshell, facilities change management is the management of the processes a company goes through when changing facilities. This could mean anything from restructuring and downsizing to expansion and relocation. But executing such changes can be a tough task, with the stress involved enormous. It can involve a huge amount of planning and logistics and can cost a lot of money too, plus companies may not have the manpower or expertise to put an experienced in-house team in place to manage the whole process. And this is where FBX come in. They can manage the whole complex process for whatever changes a company need to make from start to finish, meaning the whole process will run as seamless as possible to ensure minimal disruption to production. The engagement from FBX starts at the outset with a consultation with senior management to understand their strategic objectives and how the current facilities will need to change over time. They look at everything from the size of the space and how the business utilises that space, to the number of staff they have, and how efficient the company runs to identify what they need for the future to get the maximum value out of their facilities. Once a feasibility study has had board approval, FBX manages the entire facilities change process to a successful conclusion. Frank Blahuta, Managing Director of FBX, said: “We are seeing more and more companies interested in our relocation service due to its uniqueness. A complete relocation is a massive project and we do everything from the assessment of available properties and applying for planning permission to sourcing architects, construction companies and, ultimately, the management of the dilapidation process for your old premises. “Then once finished, we accept the building on behalf of the client and can hand the keys over to them when they are ready to move in, or plan and execute the physical relocation on their behalf.” The company is currently working on a relocation for a South East based client. FBX were asked to project manage the construction of a 45 sq ft manufacturing facility and, after reviewing several existing locations, they recommended to the client that they design and build a brand-new purpose-built facility. The project is on target to be ready next February. If you are thinking of growing or relocating your business either now or in the longer term, contact 01254 832582 or visit https://www.fbxsolutions.co.uk/ to see what support FBX Solutions can provide for you. Manufacturing & Engineering Magazine | The Home of Manufacturing Industry News
How Will Brexit Affect British Engineering and Manufacturing?
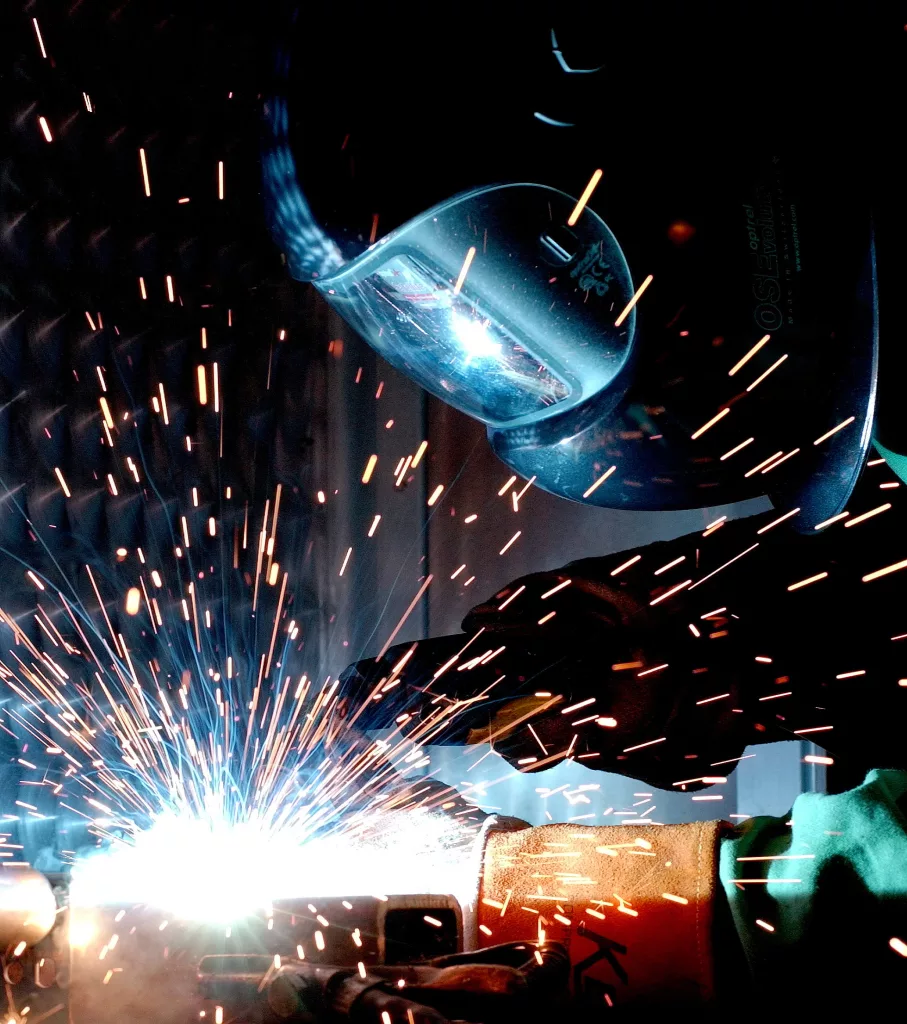
Post Brexit Britain is a place that is scary for many, people are in fear of what will affect them and to what extent, or if it will affect them at all. In terms of manufacturing and engineering, there are the positives, the negatives and still the unknown… An obvious impact of the referendum is the sterlings rapid depreciation against other currencies. This in fact makes exports cheaper, so buying British goods becomes more attractive to foreign purchases who suddenly realise their currency will go a lot further than in previous years. Essentially this might mean we are giving other countries a bargain when we can’t really afford too, but this will give Britain a short term boost for the internal market. Manufacturers are becoming more likely to source components for products domestically, as buying from abroad becomes a little more expensive. Sourcing components from local manufacturers means cars can claim back the old-Made in Britain statement which could lead to interest from companies abroad in the long run. Since the financial crisis and dark days of 2008, production seems to have declined slowly since the all time record set in 1972. Now, new technology, models and investments, even new company owners are aiming to put this depressing trend in reverse! There have been predictions that the UK could speed past the previous record and hit 2m for the first time in the next three years. That’s exciting news for all, with approximately 160,000 people employed in the vehicle manufacturing business and a total of 800,000 across the wider industry it certainly seems that Britain’s car industry is in high gear, although this was also the case before brexit, with most manufacturers voting remain, so there is some obvious remaining concern. Brexit present unprecedented opportunities that will increase trade deals that are of benefit to both the UK and foreign partners. There are already steady reports in gains of revenue and profit as we approach mid 2017. The result was unexpected for the business and people are still trying to get their head around the change, the main disadvantage to the industry being the time it takes to negotiate new sales strategies to the rest of the world outside of the brexit drama. The Royal Academy of Engineering has revealed a heavyweight analysis of both the threats and opportunities the referendum has brought with it, which include the need to maintain a supply of skilled labourers. Those in the industry are aware this is a critical time for Britain’s engineering sector with plans for a new industrial strategy being announced after the referendum took place, people are in high indications that the government realises how important engineering and manufacturing are to the overall economy. Making up approximately 10% of the UK’s economy and contributing approximately 280bn gross added value (which leads to about 20% in total) means these two industries must not be overlooked for Brexit to be a success. The Academy has warned a lack of skilled staff in the UK is trumping their other concerns and are determined more time and money should go into the encouragement of young people to follow in the field. Hiring people from all over the world, not just Europe needs to be made easier to fill the void of skills that Britain seem to suffering from. This is putting politicians in a difficult spot of trying to satisfy voters desires to control immigration but simultaneously support the crucial engineering sector who need more variety of staff, skills and knowledge. It appears that Brexit can have many positive advancements for both the manufacturing and engineering trades, but in order for those benefits to become clear the industries need to work on the issues that remained before the referendum. The new wave of manufacturing and engineering will be able to come forward and be bigger and better than ever, predictions for the next half decade are very exciting and the industries need to remain positive in times of uncertainty and continue doing what they do best. Manufacturing & Engineering Magazine | The Home of Manufacturing Industry News
Despite Rising Costs UK Manufacturing Remains Bouyant
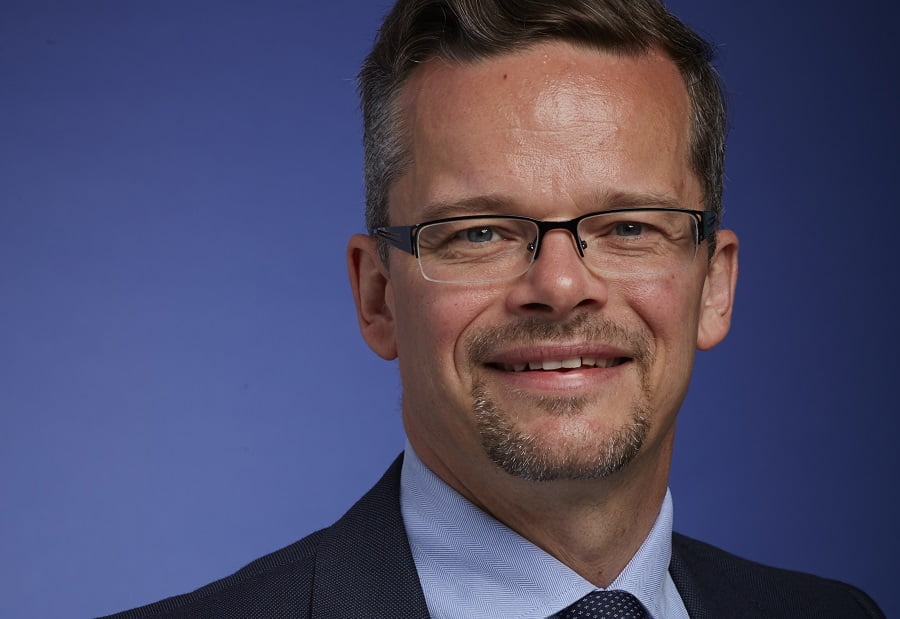
Despite Rising Costs UK Manufacturing Remains Bouyant : “With another month of PMI data above the long-run average, and solidly in expansion territory, manufacturers must surely have a spring in their step this month,” said Justin Benson, a Director at KPMG Commenting on the recently revealed Markit/CIPS UK Manufacturing PMI figures, Justin Benson, a director in KPMGâs manufacturing practice, said UK manufacturers had every reason to have a spring in their step. He said, Albeit at a slower pace, another increase in new order volumes, driven mainly by overseas orders, has meant that almost 50% of UK manufacturers expect production to be higher in 12 monthsâ time. Despite the increase in input costs, business confidence is on the rise, leading to further job creation across the spectrum of manufacturers, from small to large. KPMGâs Rethink Manufacturing survey has shown that two thirds of UK manufacturers expect to offset rising costs by either achieving saving elsewhere, or absorbing them. Pressures on margins will increase, leading to potential price rises and increased risk in the supply chain. Therefore, manufacturers need greater transparency in order to spot potential risks to future supply of key components early, keep a close eye on cash/working capital and ensure contingency plans are in place. Manufacturing & Engineering Magazine | The Home of Manufacturing Industry News Manufacturing & Engineering Magazine (MEM), is a the leading UK based monthly print & digital publication focused on promoting innovation in manufacturing and engineering available here in the UK. We cover : SUSTAINABILITY (Waste & Water Management, Recycling, Energy); INMOTION (Rail, Marine, Aerospace, Automotive, Defence); INFRASTRUCTURE (Oil & Gas, Nuclear, Construction); Healthcare (Medical), TECHNOLOGY(Printed, Connected, Software, Composite); MANUFACTURING (Chemical, Metals, Plastics, Electronics, Electrical); CONSUMER GOODS(Furniture, Electrical, Electronics, Food) to name but a few. We have over 50,000 views of each issue of MEM on average in 2022 and go to print monthly and also publish in our newsletter, (each issue is available free for 12 months digitally). Our focus is aligned across the next 12 months with our global media partnerships around Trade Events and also contains original content.
Why British Manufacturing Is Booming (And Why It’s Getting Even Better)
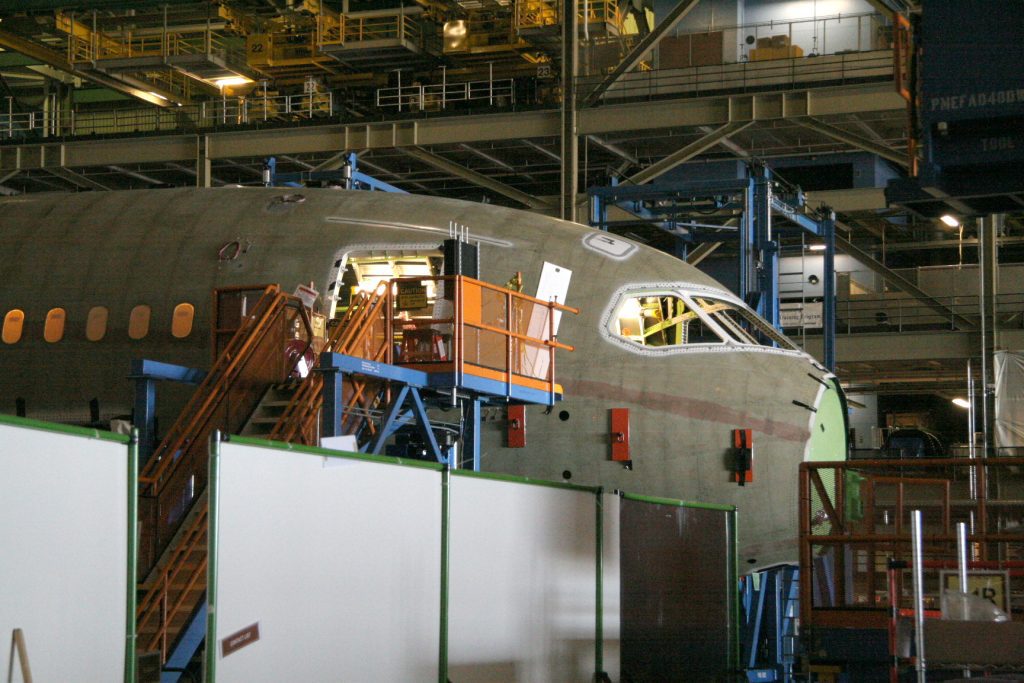
British manufacturing is booming. There’s a hundred reasons to be optimistic. Productivity Growing Currently the ninth largest manufacturer in the world, Britain’s annual output of £190bn has seen our output per hour improve within the sector three times faster than it has in the economy as a whole. Growth Witnessed by Most UK Manufacturers It might be as small as 1% but British manufacturers are growing. In a survey carried out by the BPMA of manufacturing businesses within the Briman Group membership, every single company said it had experienced growth with some revealing 40% growth. The average was 11%. Going Up Market is Helping Small British Manufacturers Compete Globally In the highly competitive clothes manufacturing market, British manufacturers are not trying to be the cheapest but be the best by using the finest quality materials, production standards and techniques. Exports Rise Ending last year on a high, British manufacturers played their part in the economy’s growth, enjoying rising export sales. Innovation is In-Built in the British Manufacturing Mentality – and it Makes Us a Global Leader R&D receives huge investment every year and it’s making the difference. Manufacturing, accounting for 68% of research and development, makes up 10% of our exports. Manufacturing Success Reflected in Higher-Than-Average Wages The average wage in the manufacturing sector is £31,000 compared to the national average of just under £28,000. The latest figures show 2.7 million people are employed within UK manufacturing. Britain’s Thriving Manufacturing Sector is Employing More People than Almost All Developed Countries Only the USA has created more jobs in manufacturing than the UK. British Manufacturing is Truly Global 45% of UK manufacturing output is exported abroad. This figure is expected to grow. “Made In The UK” is Highly Sought Around the World That is especially true of the UK’s most productive manufacturing sectors Pharmaceuticals, Food and Drink and Transport. Collaboration between UK Manufacturers and Academia has put Britain in the Box Seat Acknowledging the fact British universities lead the world, manufacturers have worked closely with academia to further enhance R&D. Adversity has made British Manufacturers Stronger It hasn’t been an easy few years for British manufacturing but adversity has made UK businesses stronger, better equipped for growth and more resilient. Key to this is adaptability, a willingness to invest in innovation, and understanding the market.
Experts By Design: Carrs Welding’s Phil Carr Talks To MEM About Reputation, Ambition & Expansion
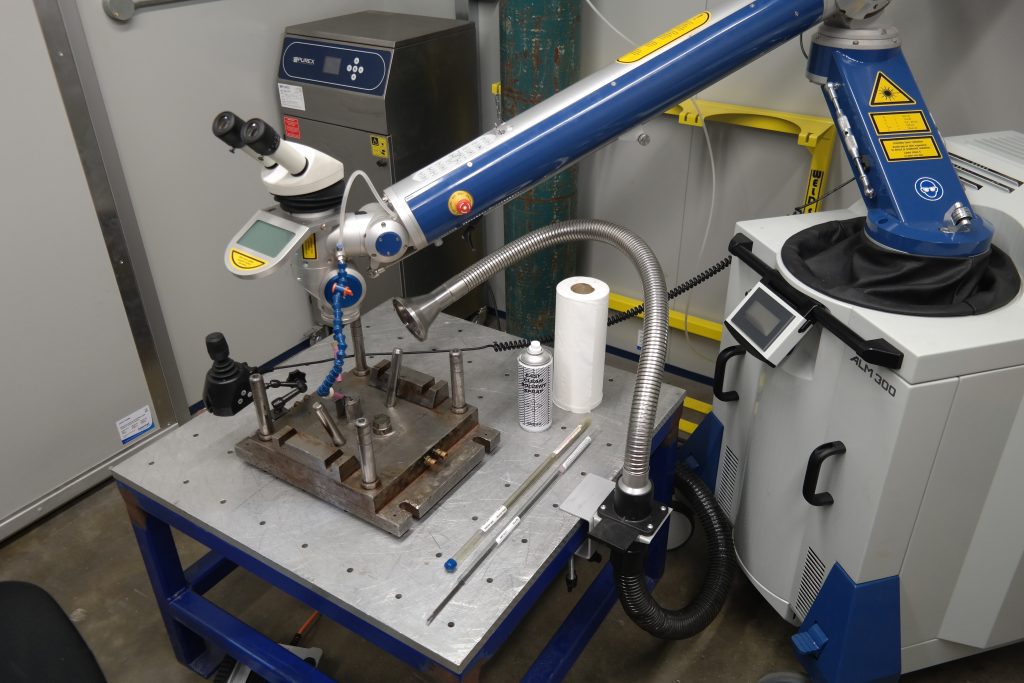
It is all a constant evolution, but Carrs will as ever, buy the latest kit and in using these lasers all the time, we shall become the industry experts and then like other centres of excellence, Carrs will be the proving house for many welding operations. – Phil Carrs, Sales Director at Carrs Welding. Carrs Welding boasts an enviable reputation as one of the most efficient and technologically advanced laser welding and mould repairing companies in its highly competitive industry. The business was established in 1992 and started out solely focusing on mould repairing, but in the late nineties it developed its service portfolio through investment in the latest, top of the range laser welding equipment. Typically known for its extremely quick turnover for repairs and enduring standards, the organisation has cemented itself as a market leader by virtue of utilising the highest quality equipment from the best suppliers in the industry. Complementing this is a desire to work closely with clients, providing customer service that values an open platform to deliver added value solutions and meet expectations and requirements. With laser welding system providers such as Alpha, Trumpf, and Rofin on board as Carrsâ main suppliers, the business is able to offer its customers a quality of service they would struggle to find elsewhere. High End Equipment Phil Carr, Sales Director at Carrs Welding, noted the businessâs use of high end equipment, as well as its willingness to invest, as a defining quality of Carrs. It is all a constant evolution, but Carrs will as ever, buy the latest kit and in using these lasers all the time, we shall become the industry experts and then like other centres of excellence, Carrs will be the proving house for many welding operations. This has resulted in an ambitious approach to growth. Indeed, Carrs has never stood still, seeking ways to enhance its capabilities in order to offer more for its current crop of customers and generate new ones. Examples of this development include the company passing its first assessment to AS9100 Aerospace Certification in August 2013, and also the reassessment in November 2016. The positive results in these assessments mean that Carrs has been able to become a regular supplier for Airbus, for example. The Ambitious Approach More recently, Carrs has seen the expansion of the business reach the South of France. Starting out with just a local repair service the business now aims to have a full laser repair centre established by the end of the year. The expansion is expected to be the start of further development for Carrs as it aims to bolster the businessâs reputation. Of course, objectives for the coming year and beyond will be influenced by the evolving repercussions of Brexit. Carrs has already witnessed fluctuations in the rate of the Euro and Dollar against the pound have an impact on its operation. All its lasers are built in Germany or USA, for example. Yet, as Phil explains, Carrs is preparing itself for a number of eventualities and is confident it can make further progress in the aftermath of Britainâs break from the European Union. We cannot dodge the issue on currency exchange rates, but being so small (about 12 people), we can re-invent ourselves around a client to help support the welding operation. He added; Like when we assembled battery terminals for McLaren, it was a tricky job as they easily shorted out the cells if badly placed across the wrong terminals, but we made tools and put safety procedures in place and we managed the whole build programme of nearly 400 cars with no disasters. Attentive To Customer Needs Many businesses have clear and intricate unique selling points, but Carrs has kept its USP simple and very customer centric. Carrs will always endeavour to have the latest laser welders and be the best at delivering a good welding procedure, said Phil. We have 12 lasers and although there are many more now on the market we can weld most jobs, large or small. In addition, Carrs has been able to boast some high end clients and contracts. For McLaren, for example, Carrs supported the programme for the three years that it took to build the car manufacturerâs P1 supercar. Now in the spares phase of the project, the company previously laser welded the busbar assemblies during the production of the boost batteries for the car via its collaboration with Johnson Matthey Battery Systems. Carrs is an extremely well-organised and resourceful laser welding company; small enough to offer open, honest and value-adding customer service and skilled enough to take on the biggest businesses in the market. Concluded Phil, We are a small family owned business and we are small and efficient in what we do, but we also happened to be really good at welding. That is good enough.