In the precise worlds of science and engineering, the integrity of measurement is of utmost importance. Enter granite surface plate, the stalwarts of accuracy, providing a reliable reference plane for critical measurements in component assembly and inspection processes. As fixtures of exactitude, these granite surface plates underpin sectors where precision is non-negotiable, making their calibration—a process often overlooked—vital for ensuring continued measurement accuracy.
Granite surface plate calibration is an essential practice, not only preserving the robustness of measurements but ultimately safeguarding the quality and consistency of engineering outputs.
The necessity of maintaining the flatness and precision of your granite surface plate cannot be overstated. Regular wear and tear and minute alterations in its form can render a once-trusted surface inaccurate, and this is where the calibration process steps in.
Granite surface plate calibration ensures that the surface plate not only complies with meticulous industry standards but also conforms to the stringent organisational policies dictating measurement integrity. With considerations for use frequency and equipment specifications shaping calibration schedules, specialists proficient in granite surface plate care employ refined techniques to verify flatness, execute necessary adjustments and meticulously document the procedures.
This upkeep, essential for the longevity of granite surface plates, establishes a foundational assurance in the various applications where these precision tools are indispensable.
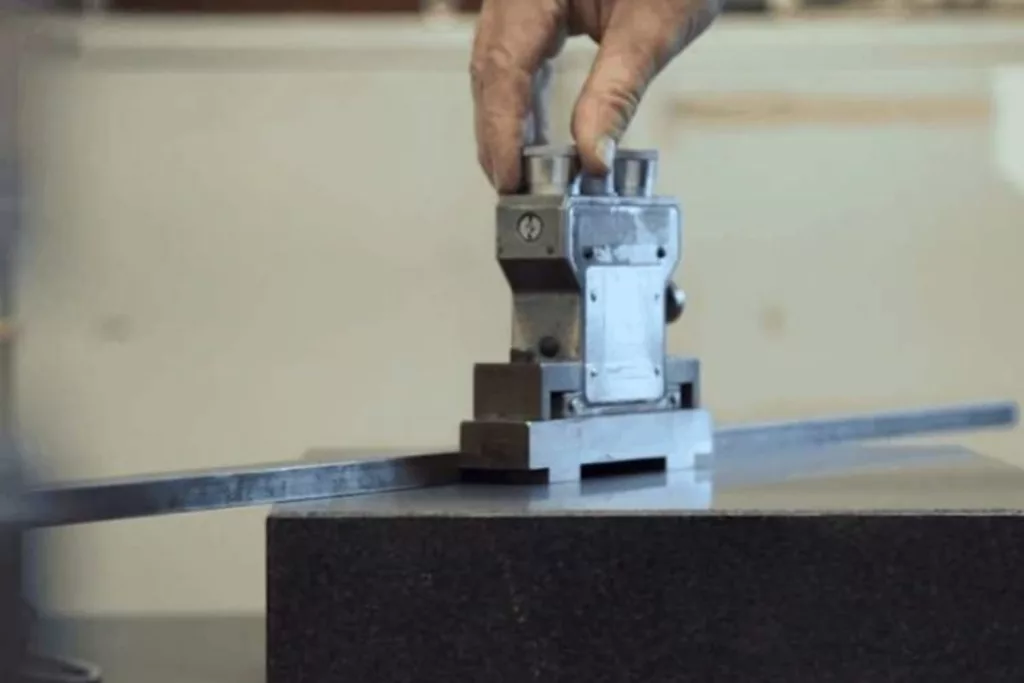
Maintaining Your Granite Surface Plate
Eley Metrology, through the Crown Windley brand, has over 100 years of experience in manufacturing and maintaining surface plates. Their highly skilled engineers provide calibration and resurfacing for all sizes and grades of granite surface plates and tables. Calibration can be conducted on-site or at the company’s centrally located UKAS Laboratory in Derby.
To maintain the precision of granite surface plates between calibrations, following a regime of regular care and maintenance is crucial. Below, Eley Metrology engineers share the essential practices to keep the surface plate in optimal condition:
- Rotation: Periodically rotate the plate to minimise the formation of wear spots, as consistent use in one area can lead to uneven wear over time.
- Protection: When not in use, cover the granite surface plate to prevent dust accumulation and other contaminants that could affect its flatness.
- Cleaning Routine: Clean the surface plate before and after each use to remove any particles that could impact measurement accuracy. Employ a specialist granite cleaning solution to achieve the best results. Avoid using water-based cleaners or volatile solvents, as they can damage the granite surface plate.
- Weight Distribution and Usage: Ensure even weight distribution across the surface plate to avoid localised stress and potential damage. Utilise the granite surface plate strictly for its designated purpose and avoid using it as a storage bench to prevent overloading. Do not over-tighten hold-down bolts; consult the manufacturer’s specifications for the correct torque limits to prevent undue stress on the surface.
- Surface Integrity: Regularly inspect the surface for scratches or nicks. If found, gently remove burrs with a silicon carbide stone to maintain a smooth surface.
Manufacturing & Engineering Magazine | The Home of Manufacturing Industry News