How Real-Time Visibility of the Supply Chain Can Help Mitigate Food Waste
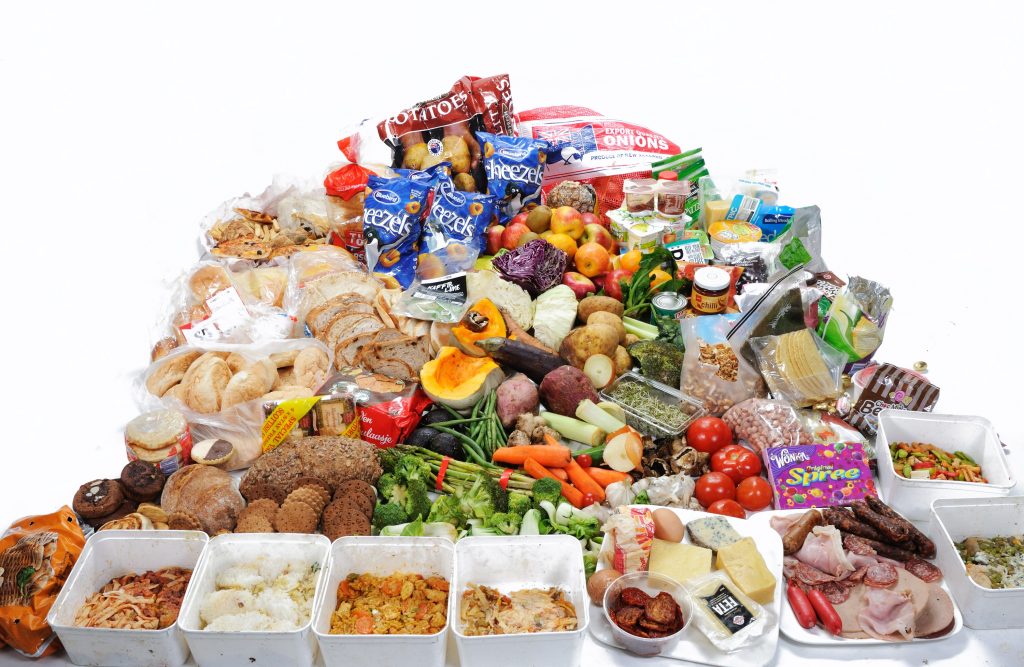
How Real-Time Visibility of the Supply Chain Can Help Mitigate Food Waste : In today’s market, consumer demands have not only driven supply chain efficiencies for greater speed and convenience but are increasingly now forcing retailers to address expectations of improved sustainability. The consequences of keeping up with customers’ wishes aren’t always easy and may have an adverse effect on short term business plans and processes, especially if your supply chain isn’t as seamless and transparent as it should be. Even the smallest of inefficiencies can add up and lead to all manner of waste during production, transport and even disposal. Over recent years, the grocery market has come under scrutiny and intense pressure to re-evaluate its approach to tackling food waste, with around 88 million tonnes worth being generated yearly across the EU, a staggering 40% of food doesn’t even make it to the market. The problem is, without real-time insight into the exact status and condition of product and inventory within the end-to-end supply chain, what options do companies have to address waste and improve customer engagement? Amir Harel, General Manager of Visibility Solutions at Zetes, explores how complete real-time, intelligence-driven visibility of the supply chain can help mitigate food waste. The Lack of Supply Chain Visibility The world is ready for change. According to REFRESH, an EU research project acting against food waste, resources being lost and wasted in Europe would be enough to feed all the hungry people in the world twice over. It’s a message that consumers around the world are taking to heart. From reusable bags to paper straws, and bottle-free toiletries to meat-free diets, people are taking real steps to reduce waste, and they expect the businesses they buy from to do the same. In the UK, for instance, grocers have encouragingly pledged to halve their food waste from ‘farm to fork’ by 2030. Whilst we commend large retailers for deploying innovative ideas such as the introduction of ‘wonky veg’ – vegetables that do not meet the aesthetic requirements of supermarkets due to shape or appearance – are now being sold in supermarkets to help combat waste, it is analysing the production of waste on a more granular level that will achieve a positive environmental impact at a far greater scale and have more effect. Yet, recent research from Sapio, on behalf of Zetes, reveals that the current levels of supply chain visibility are far from perfect, with a staggering 94% of organisations surveyed saying they lack transparency throughout their supply chain. Unlock Capability To implement an appropriate resolution, it is imperative that the cause of waste is understood. There are so many contributors – from the excess inventory that arises from poor and/or delayed forecasting and orders, to time lost during the distribution process coupled with inefficient transportation models can be devastating for any short shelf-life products. Just 30% of organisations have full visibility of goods in transit. As a result, addressing the food waste that occurs at every stage of the supply chain is a complex task. Research highlights that 79% believe that improved visibility would have a material effect on cutting wastage. As a taste of the potential savings, it’s estimated that supply chains could reduce food waste alone by €240bn. For example, reducing empty miles, improving first time in full delivery, minimising unnecessary stock movement between stores, avoiding forecasting or ordering disputes and achieving far more intelligent routing, are all critical components for an efficient supply chain that minimises waste. Real-time efficiency Having complete visibility and traceability of products is also key to a resilient supply chain, which is especially important when recalls and faults in production can cause crisis situations and disruptions. When retailers are able to share data throughout their supplier ecosystem in real time, they can create the foundations for better collaboration based on stronger connections and highly effective dynamic forecasting. It is also essential that companies understand how technology can be deployed and utilised to address each challenge – whether that is waste reduction through improved transportation or more accurate and dynamic levels of stock availability. So, where to start? Environmental consciousness in the digital age will continue to have a huge impact on retailers. The vision to transform ‘farm to fork’ and remove food waste from the supply chain is big. To succeed, retailers need to start small, identifying priority areas first, where quick and impactful wins can be realised. As they start to see results, they will be able to scale fast and ultimately achieve full end-to-end intelligence-driven visibility. Manufacturing & Engineering Magazine | The Home of Manufacturing Industry News
Zetes Supports the Fightback of the Illicit Supply of Tobacco
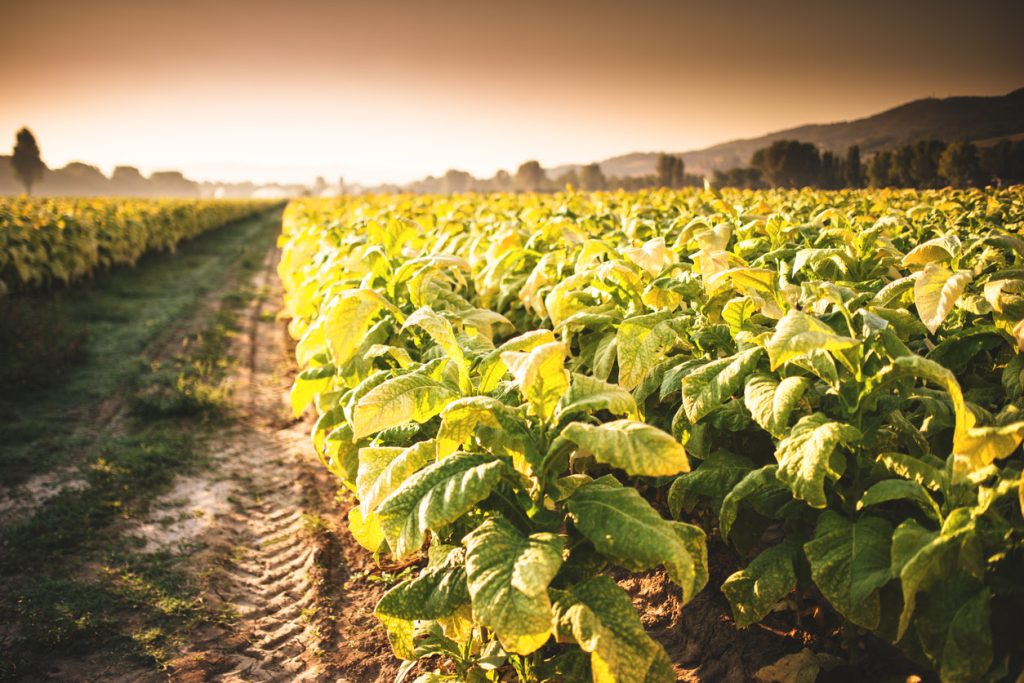
Six major Belgian tobacco manufacturers are working with Zetes to make their supply chain compliant with the revised Tobacco Products Directive (TPD) and fight illicit trade. “We are proud to be at the forefront of driving security and integrity in the European supply chains across industry. Supporting tobacco manufacturers, wholesalers and retailers to eliminate the illicit supply of tobacco is the next chapter for us,” said Olivier Frère, Traceability Expert at Zetes. The revised TPD (2014/40/EU), which will come into force on 20 May 2019, concerns the manufacturing, packaging, and sale of tobacco-related products. The aim is to fight illicit trade to protect public health and ensure taxes are collected properly by making the complete traceability of tobacco products mandatory. To comply with the new legislation, six Belgian tobacco producers – CTS, Flandria, Nollet, Notebaert, Stubbe, and Twist Tobacco – selected Zetes to ensure the traceability of their products across their supply chain. The TPD makes it mandatory for producers of tobacco products to mark each product with a unique identification code (serialisation) and store these identifiers in a private repository connected to a European repository. Other economic operators (wholesalers, distributors, third party logistics service providers and retailers) must capture and register the movements of these packages along the supply chain and send the relevant information to a European Router. The data will then be available to the public authorities of the EU countries and the European Commission in the European repository, making it easier to check the legitimacy of a product. “Zetes’ expertise in the field of serialisation and traceability is a plus when it comes to implementing compliance projects such as this one. We are now confident that our business will conform to the new aspects of the legislation,” added Cédric Santelé, CEO at CTS Tobacco. To support this process, economic operators will need to review their processes and implement a compliant technology solution. For manufacturers, Zetes TPD compliant solutions provide packaging and product identification, required for the serialisation and aggregation process, and traceability (data processing in a central repository). For wholesalers, distributors and retailers there is a need for a TPD compliant solution to capture and share the unique identification codes together with the specific sales data to identify the transaction and who it was for.
Granot Avocado Achieves 100% Shipping Accuracy with Zetes
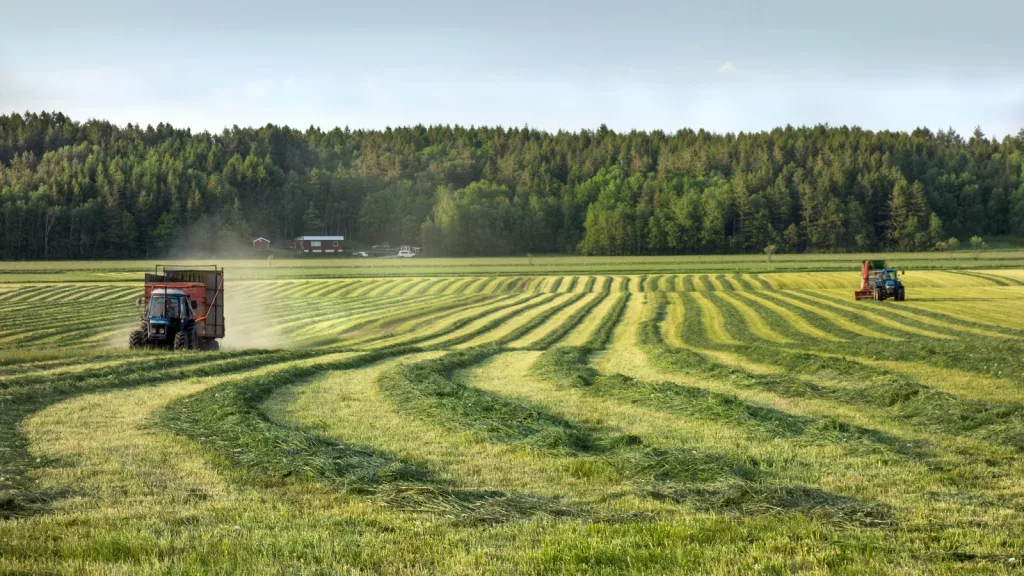
Granot Avocado, an Israeli cooperative of agricultural farms, selected the ZetesMedea shipping verification solution, to maximise efficiency and eradicate errors from its loading verification operations. The new system enables the cooperative to achieve 100% accuracy and traceability of outbound pallets combined with dramatic improvements in processing and loading onto vehicles. Time-consuming manual process Granot Avocado is a cooperative of 43 agricultural farms growing about 30% of the total production of avocados in Israel. The fruit harvested by the different farms are gathered in the Granot’s packaging house, where 75% of them are shipped to be sold on the European market. An average of 200 pallets leave the packaging house every day. In the past, warehouse operators manually checked the labels on boxes and pallets to confirm the origin of the products and their shipping destination. This time-consuming manual process broke the flow of outgoing pallets and led to more than 50% error rate. Granot Avocado needed a solution that would allow them to provide traceability on the pallets and their content, improve data accuracy, and streamline their outbound logistics processes. Machine Vision to streamline outbound logistics Part of the ZetesMedea warehouse execution portfolio, the ImageID technology, based on Machine Vision, is positioned at each loading dock capturing images of the pallets to be shipped as they flow through. The system instantaneously reads the carton and pallet labels in real-time to check for any mistakes, such as a missing box or a box on the wrong pallet. The system triggers a go/no go signal, ensuring the right pallet is loaded onto the right truck. If items are incorrect or mis-labelled, visual identification is shown on screen so that remedial action can be taken. Main benefits “Since the implementation of ZetesMedea, we’ve seen a significant increase in our data accuracy, reaching 100%. We are now able to scan all pallets without human intervention, considerably reducing our error rate and making us save valuable time. Zetes’ palletisation software also drastically limited customer disputes as we can now provide our customers a visual proof of the condition of the pallets when they leave our warehouse,” said Eran Rotem, COO at Granot Avocado. Eli Harel, Country Manager of Zetes in Israel also commented, saying: “We are happy to be helping out Granot Avocado with their outbound logistics operations. We trust that our proven experience in implementing similar projects for other companies will continue to bring them significant benefits and will bring them quick return on investment.” Manufacturing & Engineering Magazine | The Home of Manufacturing Industry News
SodaStream Chooses ZetesMedea for Its Production Line
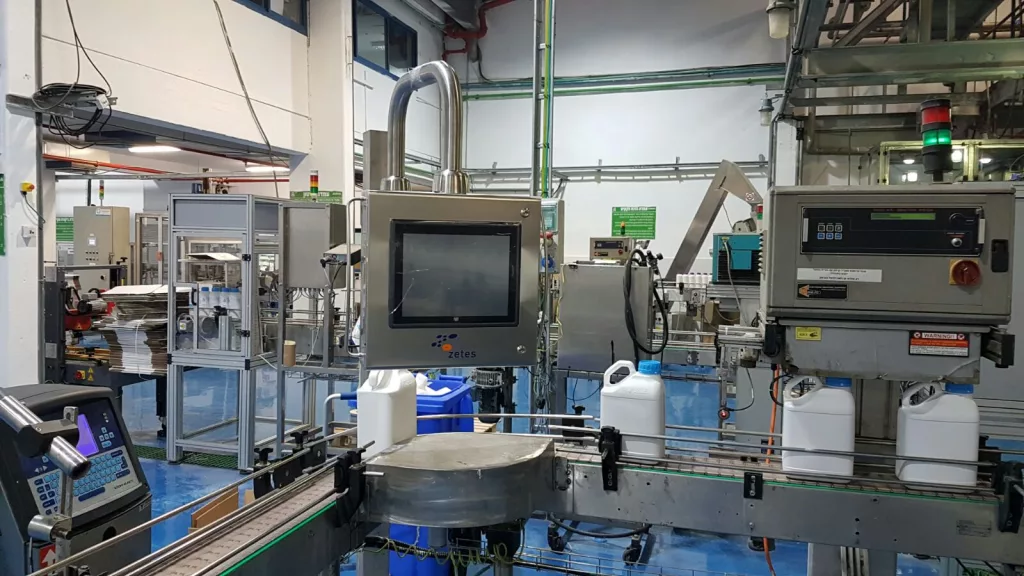
The largest manufacturer and supplier of home carbonation systems, SodaStream, has decided to implement Zetes’ ZetesMedea solution in its Israeli production campus, ensuring the precise identification of stock and full visibility of its production line. SodaStream’s production site in Israel contains conveyor belts, which transport cases from six lines out to their logistics centre. Previously, staff manually counted the cases as they moved from the conveyors prior to being loaded for delivery. This process was error-prone and left an information gap when staff were unable to effectively analyse the exact numbers at the end of each shift. As such, the organisation sought a solution that could monitor and accurately calculate stock as it moves through the production line. Zetes’ palletisation software, ZetesMedea, uses high-quality camera identification to scan the barcodes on each case, providing SodaStream with a reliable and accurate inventory count. The solution also reads and decodes 100% of the cases as they travel on the conveyors. The data, which includes product information, is automatically captured in real-time, allowing managers to monitor and proactively optimise performance processes. “After examining a number of systems that failed to meet our needs, we were pleased to see that Zetes’ technology surpassed our original requirements. Since implementing ZetesMedea we have been impressed with the results and delighted with the consultancy and professionalism displayed by the team at Zetes. From start to finish, it’s been a partnership. Zetes have listened to all of our requirements, advising and implementing the solution best suited to our business,” said Tomer Ariel, Project Manager, SodaStream. In addition, ZetesMedea integrates seamlessly with the existing legacy software providing a broad and accurate picture of item movements. The solution has also extended capability by monitoring the output volume of cases on the lines and calculating the production rate during a shift, informing staff in real-time of KPI performance. Manufacturing & Engineering Magazine | The Home of Manufacturing Industry News