PervasID Launches the First 99%+ Accurate Multifunctional RFID
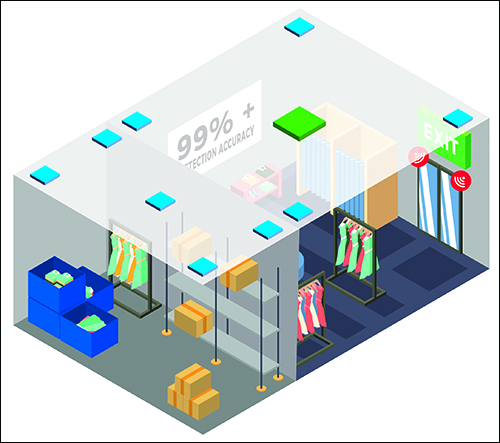
An award-winning RFID (Radio Frequency Identification) technology provider has announced the launch of its new product, Multi-Ranger. PervasID secured £1.6 million in Series A funding earlier this year to create the first 99%+ accurate multifunctional RFID reader to address retailers’ challenges concerning inventory. The technology, which was pioneered at the University of Cambridge and achieves more than 99% tag detection, will combine a wide-area passive RFID system (Space Ranger), an anti-theft RFID system (Security Ranger) and a portal system (Portal Ranger) in order to create the multifunctional reader solution that is the first of its kind. The new solution allows retailers to use a single RFID reader to cover back storage area, sales area inventory and exit/entrance anti-theft solution, as well as any transition portals that may be required, at a 50% of the cost of using independent disparate systems. This cost saving element to the reader, along with its impressive accuracy, makes the reader revolutionary in the market. “RFID technology is not new to the retail market, it has long promised but not delivered benefits. The business case for widespread use of the technology beyond security has been insufficient for many companies to make the investment. With a reader of this nature, retailers can embrace the benefits of RFID technology with a relatively low cost investment and a quick implementation time, revolutionising the way they manage their inventory,” said Dr Sabesan Sithamparanathan, co-founder and CEO of PervasID. “For RFID technology to bring real benefit to retailers, it must drive sales, deliver improved operational efficiency and increase revenue while requiring modest investment. At PervasID we are really proud to be working on technology that does just that,” he continued. PervasID is a leading RFID technology company based in Cambridge, UK. Over the last ten years it has pioneered the development of ground breaking patented RFID innovations based on original research undertaken by the University of Cambridge.
Cambridge Technology Expert Provides 3D Printing Insight
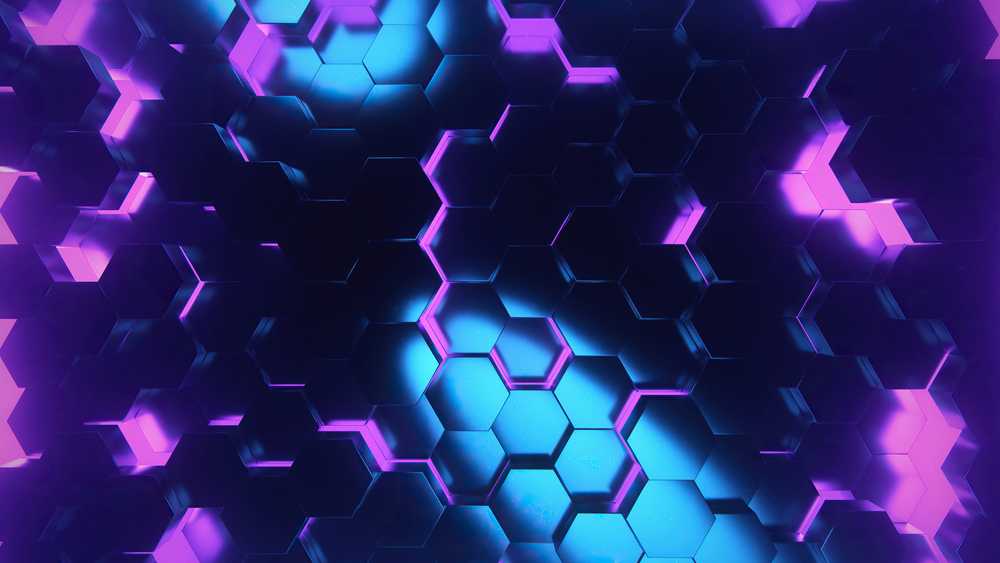
A Cambridge University technology expert says the best way to manufacturing success is to improve our knowledge of technical and commercial 3D printing. Dr Tim Minshall, Reader in Innovation and Technology Management at the University of Cambridge, is head of the Institute for Manufacturingâs Technology Enterprise Research Group. The organisation is undertaking a research project supported and funded by the EPSRC and ESRC and studies both the reality and possible role that 3D printing could play in the UK economy. The group also conducts a UK research and industry network focussed on 3D printing-enabled redistributed manufacturing. Dr Minshall, who is also part of the steering group that develops the UK National Strategy for 3D printing, gave an in-depth explanation of how he sees the best future for 3D printing. He began by stating that going back three years, there was much hype surrounding 3D printing technology and that they would be the hub of a modern industrial revolution. Since then, he believes the clamour has died down somewhat as we begin to set more realistic expectations of the reality of the technology. Dr Minshall believes that in order for UK manufacturers to benefit from the technologyâs opportunities, there must be a coherent approach to dealing with its obstacles. He continued that companies with a good understanding of how the process works will have a commercial inters to prevent it from becoming freely accessible. He stated that this, combined with the media hype surrounding the technology, has resulted in a complicated state of affairs that makes it difficult for manufacturing firms to properly gauge the potential of the technologies. He said that one thing that is evident is that the technologies are increasingly used in various sectors and that UK manufacturing companies must make sure that they fully understand both the positive and negative aspects of the technology. In terms of the UK adopting the technology, he added that recently there has been a keen drive to analyse and acknowledge the primary limitations of adopting 3D printing in a wider sense. Agents across the manufacturing industry, government and universities are cooperating to establish a national approach for UK 3D printing to be showcased later in 2016. Dr Minshall concluded by saying that there is a pressing need to advance our technical and commercial understanding of the 3D printing technology processes to make sure that UK manufacturing firms are able to fully benefit from them.