Xaar Hosts Businesses at Manufacturing Flexibility Workshop
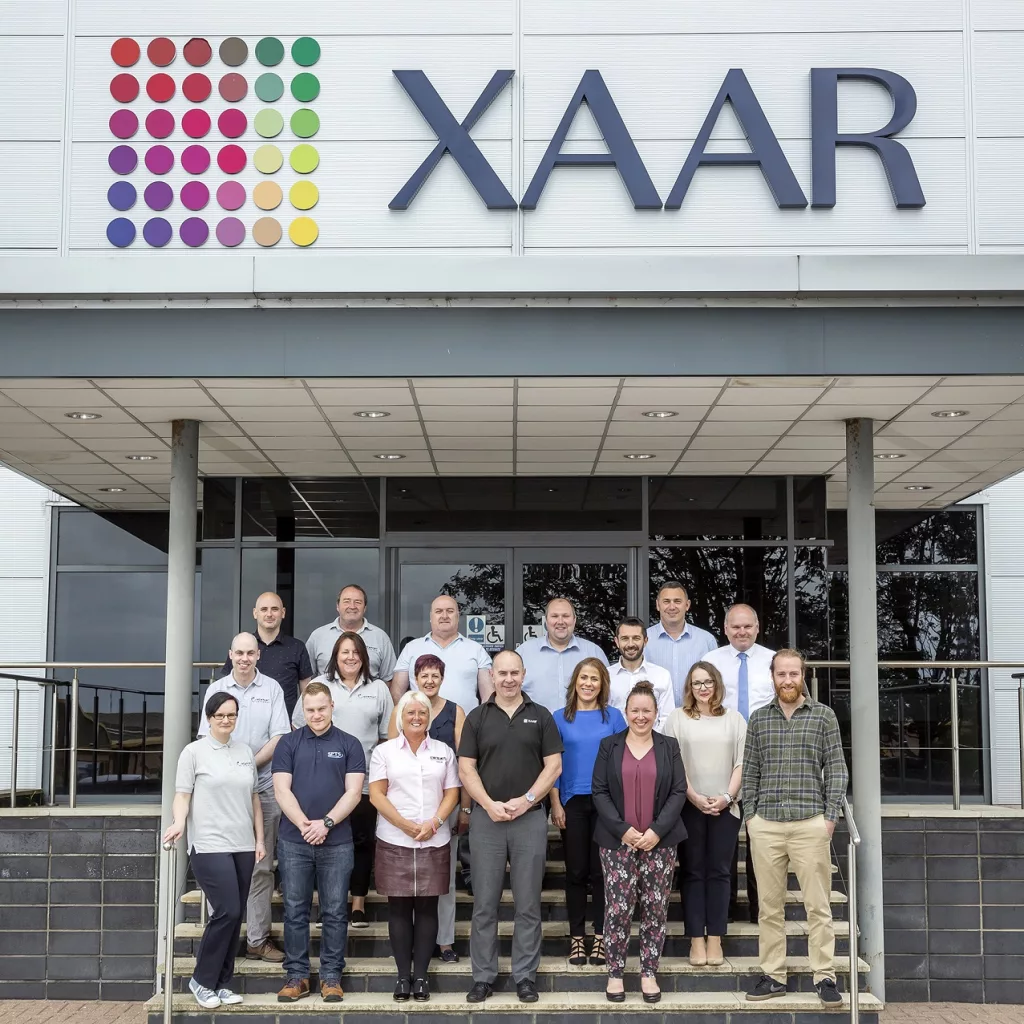
Xaar hosted members of the NMI including Diodes, Ultra CEMS, SPTS Technologies and Newport Wafer Fab at its workshop on ‘Learning and Development for Manufacturing Flexibility’ at Xaar’s Huntingdon site on 18th June. The interactive session highlighted the importance of focusing on people in the overall process, with discussion groups working to define key learning points for the implementation of Manufacturing Flexibility initiatives. NMI champions the role of its member companies in the UK electronics sector, facilitating knowledge exchange. Member workshops are key to the role and as part of this programme Xaar shared its experiences from the processes and changes made in its progression from a single product site to manufacturing a variety of different products. As a world-leader in industrial inkjet printing, Xaar recognised that in order to grow its business it needed to find ways to broaden its portfolio of products and as a result compete in previously untapped markets. The workshop reviewed the concepts traditionally discussed within Manufacturing Flexibility and asked attendees to work together on the challenge of ensuring people have the skills to adapt according to the constantly changing business needs. Leader of the workshop and Continuous Improvement Manager at Xaar, Mark Lamb said, “As a business, developing our Manufacturing Flexibility was fundamental to building our ability to deal with an increasing number of new product variants and enhancing the way people worked. Our workshop has hopefully helped participants define what Manufacturing Flexibility really means, and through our collaboration today, create a collection of ideas and strategies that each organisation can take back for potential progression.” Chris Bennett, NMI’s Director of Manufacturing Services added, “The strength of NMI is its membership and today’s workshop held by Xaar was truly indicative of this. Everyone attending was able to learn about a more holistic approach to Manufacturing Flexibility and share their ideas and strategies as part of a wider group. “I would like to thank Xaar for hosting this invaluable day of learning and look forward to hearing how our members take this information back to their organisations as part of their own development.” Manufacturing & Engineering Magazine | The Home of Manufacturing Industry News
New Engineering Practice Announces Its First Office
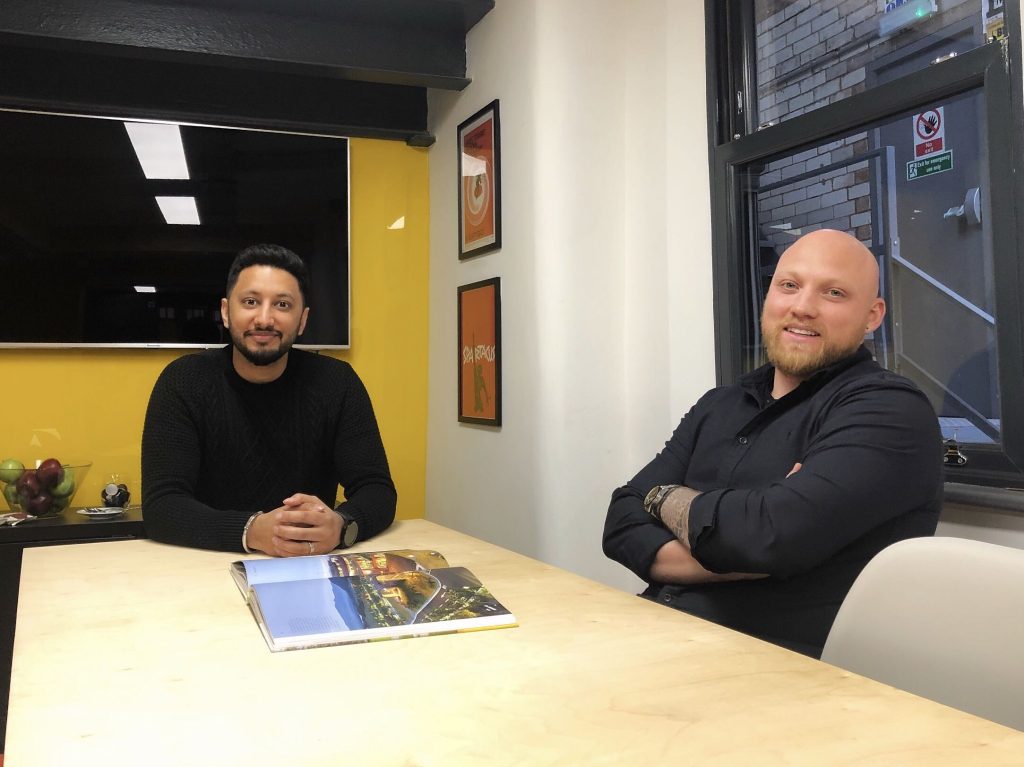
The current perception of engineering is that of a traditional industry; engineers with their heads buried in squared paper and visiting building sites in garish, yellow hard hats. But, in reality, it is a sector which is rapidly developing to meet the evolving requirements of clients, updates in technology, environmental changes and social factors; and a new, Nottingham practice plans on proving this. Dice, a new engineering practice, was set up less than 12 months ago and has recently moved into its first office. As the anchor tenant at Works Social – Nottingham’s newest co-working space – directors, Wayne Oakes and Raj Somal, now have big plans for the future of the business. “We’re delighted to now be in our first office in the Lace Market. We’ve always worked in Nottingham and Works Social is the perfect base for us – it’s a totally new concept for Nottingham; a dynamic, flexible space which suits us perfectly,” said Wayne. The East Midlands-based duo had always worked for large, established civil and structural engineering firms but had a firm belief that they could bring something different to the industry, which is why they’ve created a new concept for their engineering practice. Wayne added: “Raj and I have worked together for a number of years and, during this time, we’ve learnt a lot about what works and what doesn’t. “When we set up Dice, we knew we wanted to create a business that was honest and operated with integrity above all else – with customer service being at the heart of everything we do.” The duo have already developed an impressive portfolio, completing a range of services nationwide for PureGym, as well as working with Co-Op during its UK-wide store improvement programme and rationalisation of its existing stores. They are also involved in the new student residential development on Derby Road and a mixed use development on the Isle of Man. Wayne continued: “Sustainability is now more important than ever and goes beyond token gestures such as the installation of solar panels. There’s so much more potential with sustainable design now, which encompasses far more than just energy saving techniques. “We have a holistic approach to environmentally-sustainable designs, considering every facet of the environment, and actively look to incorporate at least one element of sustainability into every project we’re involved in. From Bee Bricks – designed to accommodate bees’ habitats inside bricks – to attenuation tanks made from soya beans, we want to push the boundaries of what has always been considered ‘the norm’. “As a business, we’re also aiming to be 95% paperless – incorporating sustainability into the fabric of the practice, not just in our work for clients.” A creative and agile approach to design and use of tech is what the industry needs in order to progress, the team at the new engineering practice believes. Raj added: “We need to inspire the next generation of engineers if we’re going to address the skills crisis we’re experiencing in the sector. Utilising technology to its full potential – promoting our industry as the modern, dynamic place to work it really is – is one way of doing this. “We use drone technology as well as design tools like Site 3D, Tekla Structures for completing designs, whilst drawing mark-ups are annotated on iPads. All of our technical drawings are produced in a traditional fashion but stored on cloud-based servers. “The business community in Nottingham has been really supportive and we’ve achieved a lot in less than a year. It’s a really exciting time for construction in the city – with the regeneration of the Southside of the city, all of the work happening within the vicinity of our Derby Road site, as well as the Boots Island site and Nottingham College work – so we look forward to seeing what the next 12 months brings.”
£1M Funding Announced for UK Pharma Sector
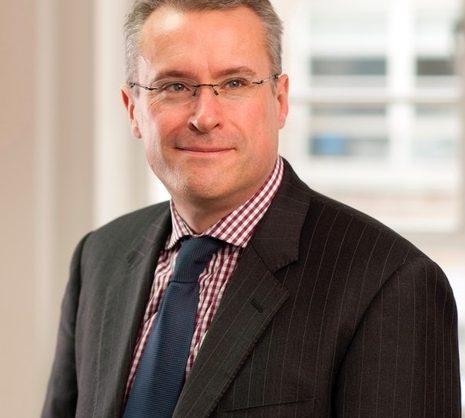
£1M Funding Announced for UK Pharma Sector : Bermele has been advised with a £1 million capital-raising move by lawyers at the Birmingham office of Shakespeare Martineau in order to target acquisitions in the pharma and biotech sectors. Bermele has become a cash shell on the Standard List and has begun trading on the London Stock Exchange. Bermele is a special purpose acquisition vehicle, formed to acquire commercial technologies in the life sciences, pharmaceutical and biotechnology sectors. It is hoped that the move will allow the business to invest in innovative companies focusing on medical and technological advancements in the areas of diabetes, cancer, mental health and personalised medicines. Bermele was advised on the finance raising process by Shakespeare Martineau’s corporate team, who provided guidance on all legal areas of the transaction, including technical contractual elements and corporate governance. Keith Spedding, corporate partner at Shakespeare Martineau, who acted as lead adviser, said: “Bermele has shown the faith it has in the UK and international life sciences and biotechnology sectors. As one of the fastest-developing fields of innovation, these areas are an extremely attractive proposition for forward-thinking investors, such as Bermele. “Against the uncertainty which pervades all areas of UK business, this finance raising operation is testament to the success of the both the UK and international markets. For smaller companies on the hunt for funding, seeing investors such as Bermele position itself as being open for business, should be a real vote of confidence.” Toby Hayward, chairman of Bermele, said: “We have recognised that the pharmaceutical and biotechnology sectors are driven by a need for more effective new products and technologies to help in the diagnosis, treatment and prevention of a multitude of illnesses and conditions. It’s a fast-paced section of the market, with ground-breaking new developments being made on almost a daily basis. “Undergoing this transaction will allow us to engage with, and support, a number of incredibly innovative businesses, aiding them on their growth trajectories.” Manufacturing & Engineering Magazine | The Home of Manufacturing Industry News
Preparing for an Ever-Evolving Digital Ecosystem
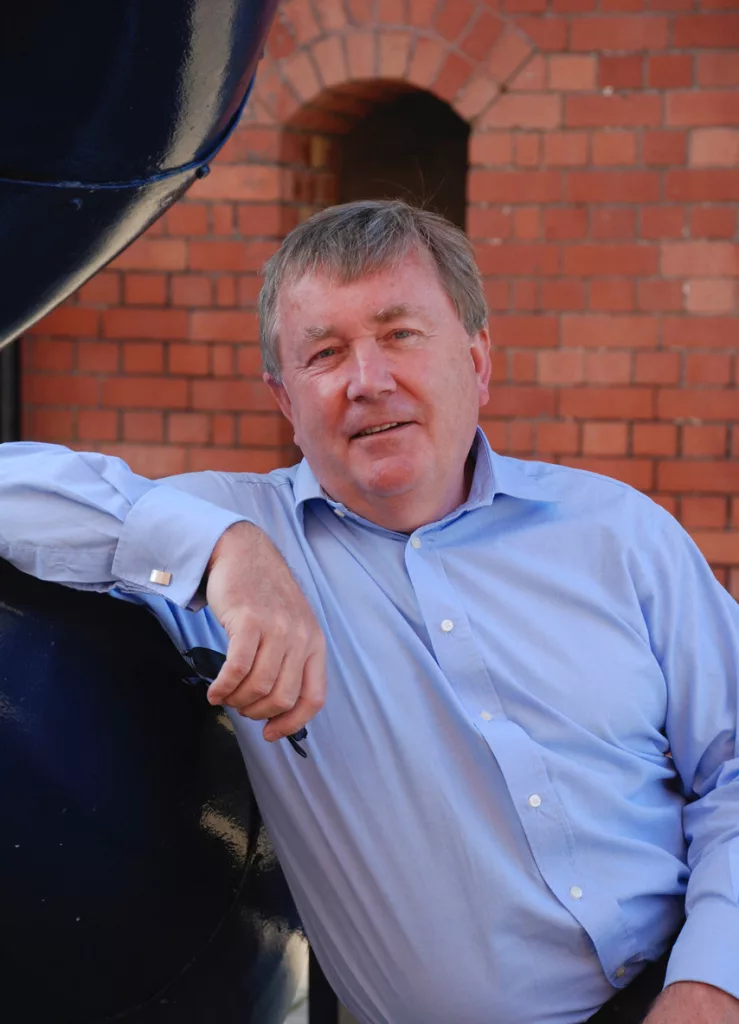
Advances in technology over the last decade has paved the way for digital evolution, with many organisations putting digital at the core of operations. In a world of ‘Big Data’, it has become more important than ever before for those operating within the manufacturing industry to utilise technology effectively, particularly where monitoring efficiencies and productivity has become crucial, with many looking to developments in Industry 4.0 as motivation for acceleration. As many organisations are taking steps towards digital transformation, John Roberts, director of Idhammar Systems, explains why businesses must streamline their approach to digital within their manufacturing practices in order to create an ecosystem which is sustainable but also beneficial for both businesses and customers alike. Invest in the right technology Not all technology will be the right fit for your business and as more emerging technologies are introduced, it’s crucial to separate the necessary from the so-called ‘next-big-thing’. It’s important to strengthen the basic elements of the whole organisation – remember the route to improvement cannot be a one-size fits all approach. As such, always do your research and pay due diligence to evolving technology and ensure it’s the right fit for your organisation. There’s a lot to digest and according to Forbes, cloud services, analytics, security and management tools are set to be the biggest planned investments in technology across the next several years. By modernising these essential technology tools, it can help to future-proof your business, protecting it (and you) from any cybersecurity issues and also reduce any potential system downtime, minimising threat to profitability and overall efficiency levels. Consider the whole picture It’s unlikely that any business will be able to establish a comprehensive digital ecosystem in one fell swoop – it’ll require a range of elements in order to do so effectively and this cannot be expected to happen overnight. Plus, your team will need effective systems training in order to fully integrate any new processes into day-to-day operations. However, in the manufacturing sphere, you can look to implement digital measurement to understand data around profitability and efficiency levels – after all, every second counts on the production line. For example, data can help to better forecast product demand by 46% and can provide support to customers more quickly. Increasingly so, data is also available through mobile devices or remote access, meaning that data can be accessed anytime, anywhere, making any improvements or issues handling more streamlined and accessible. This will become increasingly important as 5G becomes more prominent, with 32% of users stating that they would look to adopt this technology. Add value As digital ecosystems continue to build momentum and change the business landscape, demonstrable value is ever-more important, especially when justifying cost within any organisation. Accenture recently highlighted that by transforming and flourishing with digital in mind, it can help to create benefits for customers and partners alike. Increasingly so, ecosystems are driven by evolving customer demands, particularly for those searching for more intuitive, real-time, integrated solutions. By addressing these needs, not only will it result in added value, but it can help companies expand their market share by introducing solutions tailored to customer pain points. The way that we do business as a whole is changing and particularly in the business of manufacturing, Industry 4.0 is becoming increasingly common and necessary in order to meet high production volume demands. Although still relatively in its infancy in the sector, those who invest in digital ecosystems and overall digital transformation are likely to be better prepared for the ever-evolving business landscape that we are operating in. This is particularly true in the manufacturing sector where change has been relatively slow for the most part, regardless of the need for increased efficiencies as competition levels are continuing to rise. However, transformation will not happen overnight, and an ecosystem needs to be nurtured and developed in a way that is tailored to the needs of your business, with the right training in place to ensure your team know how to implement it effectively for maximum return on investment. Manufacturing & Engineering Magazine | The Home of Manufacturing Industry News
How Your Business Can Benefit From Using A Data Centre
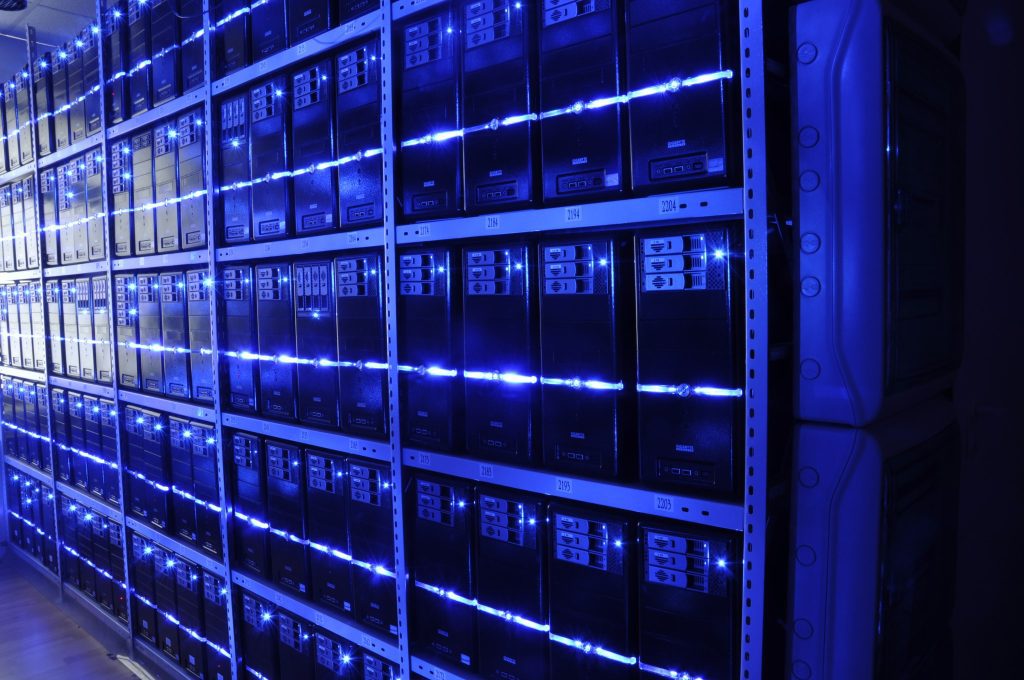
Data centres are the hub of almost all enterprise businesses in this day and age. At the rate that technology is increasing, the way that organisations do business also changes dramatically year on year. The need for data and technological power increases so significantly that it is too much for most companies to handle without serious support. That’s where the Data Centre comes in. Employing a data centre allows a business to effectively outsource its data and power needs. One of the biggest benefits of this is that it allows a business to move away from technological maintenance, and the long hours and large personnel needs to handle the technological needs. Instead, it allows a business to refocus on its customer objectives. But what other benefits of a data centre are there? The economy of a data centre Back in the days when companies were processing and storing a lot of data on-site, they had all the headaches that came with it – a lot more staff on the books, more space required, and hardware maintenance costs. Outsourcing these issues to a data centre significantly reduces your costs and can really help to fix your budget. By using a data centre, you will have a fixed monthly cost that you can depend on, no more juggling of budgets to get bills paid. Growth It would be remiss of us not to mention that outsourcing your requirements to a data centre can also induce huge growth into your business. This is particularly important to small-medium size businesses who can utilise their data centre, and gain access to hardware and software that may otherwise be cost prohibitive. Data centres will allow you to chop and change the space and software you rent as your requirements grow in some areas and shrink in others. So there is no more worrying about not having the ability to afford a piece of software or more server space. This allows small businesses to be very agile in their business offerings. It gives you peace of mind that you will get performance, no matter the scale of your business. Security and Compliance Protecting your data is critical to your business operations, and one the major benefits of a data centre is that you know your data will be more secure than you can keep it. Through use of both physical and cloud securities, data centres keep access to stored data to the absolute minimum. This can also help when it comes to data compliance. In the UK, for example, there are a number of laws and policies that companies must adhere with to become fully compliant. Data centres such as Telehouse have the ability to ensure that your company is fully compliant, while also protecting your data. Disaster recovery When you employ a data centre, planning, implementing and executing a disaster recovery plan becomes so easy that you won’t have to worry about it at all. If the worst happens and your business becomes victim to a disaster, having a data centre allows you to get up and running again as quick as possible. Not only is your data backed up and ready to be redeployed, but the vast majority of your technology infrastructure can be up and running again in no time. It becomes as easy as grabbing a laptop, accessing your data centre, and getting your business back up and running – or at least, informing your customers what happened while your IT team gets on the job. Think of a data centre as recovery at the flick of a switch. What next? So there you have it, some of the major benefits of moving to a data centre. Unless you have a particularly niche business case, it makes sense for almost all organisations to be utilising data centres in some form. Do your research and make sure you find the right one to suit your companies needs.
Higgidy Pie Brand Records Period of Growth
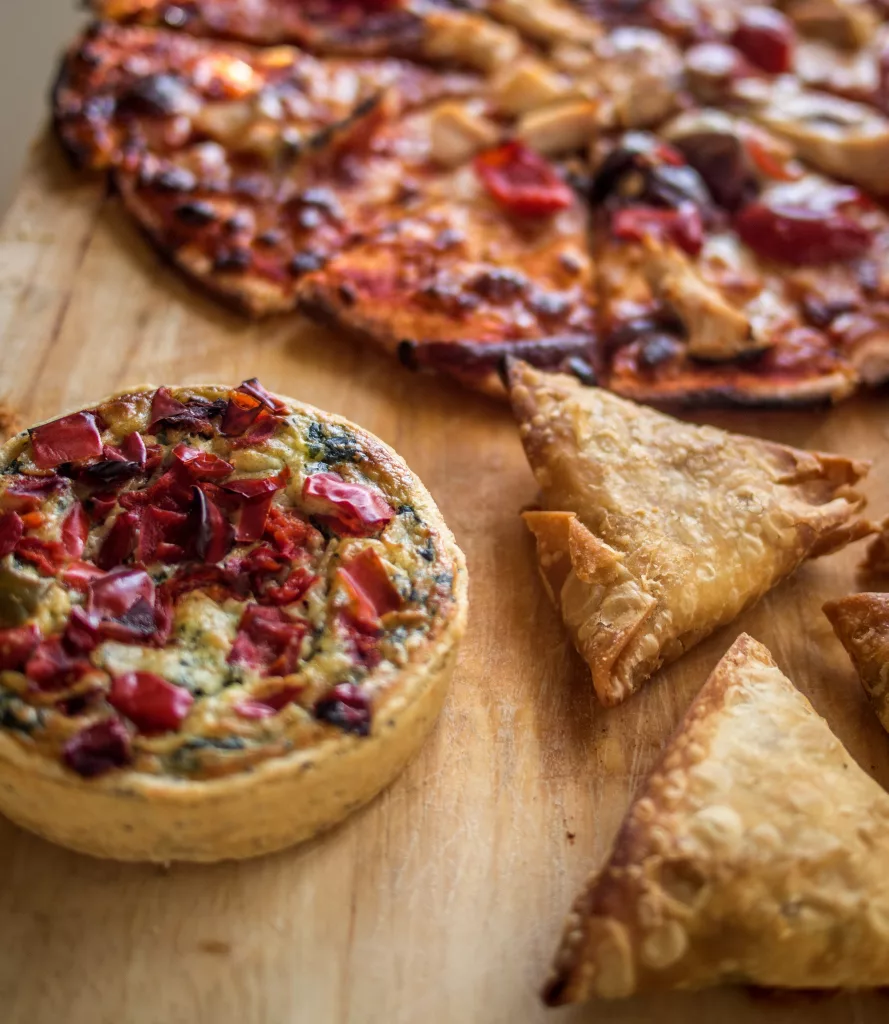
Increased revenues have been recorded at handmade pie and quiche brand Higgidy. The company described its latest financial year as a “period of growth” following consolidation and brand investment. However, the capital expenditure as well as one-off costs pushed the business to a pre-tax loss. In the year to 30 September 2018, newly filed accounts revealed a turnover of £25.5 million, up from 12 months earlier when it recorded £23.8 million. The hike, according to the company, was driven by innovation and new product development. In the 2017/2018 period, Higgidy invested in its Shoreham-by-Sea base, spending more than £386,000 on plant, machinery and leasehold improvements. During that period, the accounts revealed the business made an operating loss of £90,000 compared to a profit of £888,000 in 2017. It is also worth mentioning that 2017’s figures were bolstered by a £1.5 million depreciation charge reduction. Higgidy said the operating loss was down to “heavy investment in product innovation” and a “further significant one-off expenditure” of £177,000. Moreover, the price of ingredients also increased and the business refused to pass that on to customers. In a statement filed with the results, Higgidy said: “We anticipate to continue to improve our profitability into the next year with continued investment in operational efficiencies.” In total, the pre-tax losses for the year were £180,320 compared to a profit of £816,698 in the previous period. Higgidy was founded in 2003 and is headquartered in Shoreham-by-Sea, West Sussex. Manufacturing & Engineering Magazine | The Home of Manufacturing Industry News
Fear of Disruptive Technologies Could Lead to Declining Revenues
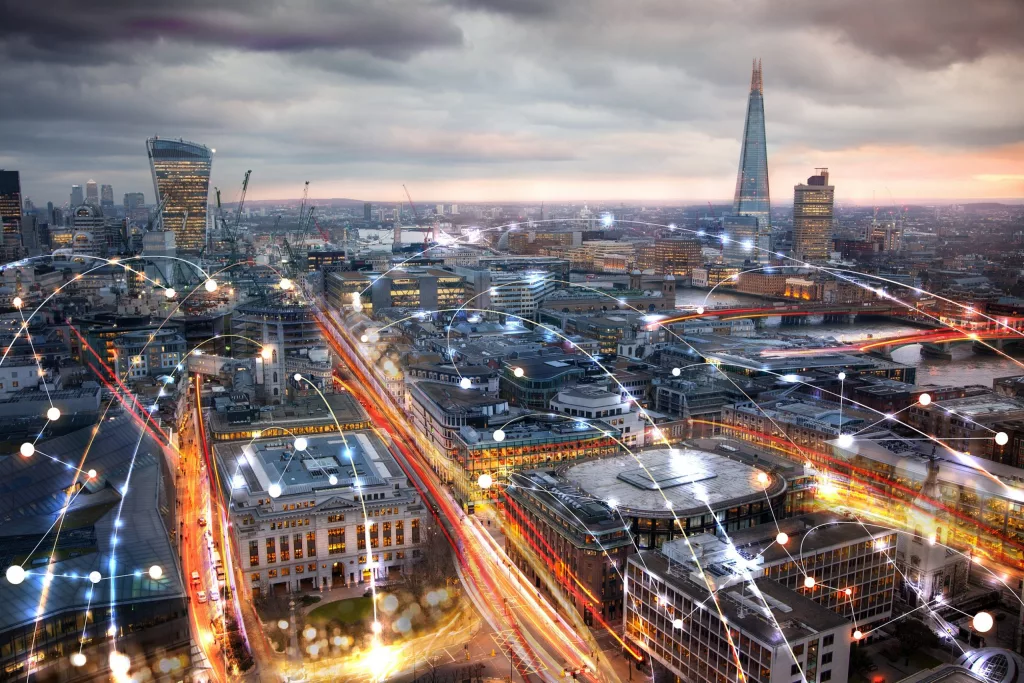
A new research revealing that although the fate of many organisations depends on their ability to implement strategic change and to adopt disruptive technologies, a reported lack of business and IT alignment, coupled with a corporate fear of risk, means they risk losing out on crucial revenues and market share, announced Coeus Consulting. Just 21% of those surveyed stated they seek to implement new technology as soon as possible, with some of the main barriers to adoption being: fear of disruption to core business (30%), lack of budget to adopt new technology (21%), and poorly planned adoption strategies (19%). “While it is reassuring that organisations are at least attempting to keep up with disruptive technologies, it is somewhat concerning that they are not doing more. Monitoring advancements is the first step on the road, but only three in ten organisations make technology decisions in the boardroom. With technology now playing a vital role in every industry, organisations need to increase their understanding of technology and be prepared to take more calculated risks in order to reap the benefits and execute successful strategic change,” commented Keith Thomas, Head of IT Strategy Practice, Coeus Consulting. Successful implementation rates are low among respondents which could explain these fears, with only 7% noting that all of their organisation’s strategic IT change projects have met initial objectives over the past two years. The good news is that, of those from organisations that have a test and learn culture, and also set objective success or failure criteria for initiatives in advance, almost 60% report that their organisation investigates or adopts a different approach when initiatives don’t meet objective success criteria. Aligned and informed organisational leadership is clearly an issue within organisations where at least some strategic IT change projects have not met initial objectives, with just over 70% admitting one of: business plans changing, senior management not buying into the change, or not taking enough risks as a reason for failure. Seeking to discover how organisations view the next wave of disruptive technology, almost a third (29%) of respondents believe artificial intelligence represents the most significant innovation set to impact their industry in the next two years, with data and analytics (18%) next in line. Despite their predictions on the next generation of technology, only 38% of respondents say they operate with dedicated teams monitoring the latest advancements. This suggests 60% of organisations could be operating with little knowledge of innovations taking place outside their four walls. Despite the current economic climate, funding seems to be a secondary issue. Last years’ research found that just over six in ten (62%) of respondents predicted an increase in the size of their budget for the coming year. In actual fact, only 50% of respondents from the survey this year reported an increase. However, just over 50% of respondents reported that digital services are being funded from the IT budget in their company, and additional funding is also allocated from elsewhere. Indeed, approaching six in ten (57%) are anticipating an increase in their budget for the financial year 2019 to 2020. This indicates that business leaders appreciate the need for IT in their current and future operations to the point of allocating funding, but not always to the point of consistently aligning with their IT counterparts. Increasing operational efficiency (49%), customer satisfaction (32%) and increasing revenues/sales (31%) top the list of drivers of strategic IT change projects, demonstrating the expectations around the business value of IT change are not being effectively driven. Businesses need to recognise the consequences that slowing IT spend, and ultimately, stagnating progress, could have on their business prospects. Taking unnecessary risks could lead to the downfall of an organisation, but in reality, spending on technology and taking a fail-fast, calculated approach to IT risk is now a necessity. Manufacturing & Engineering Magazine | The Home of Manufacturing Indu
The Future of Transportation
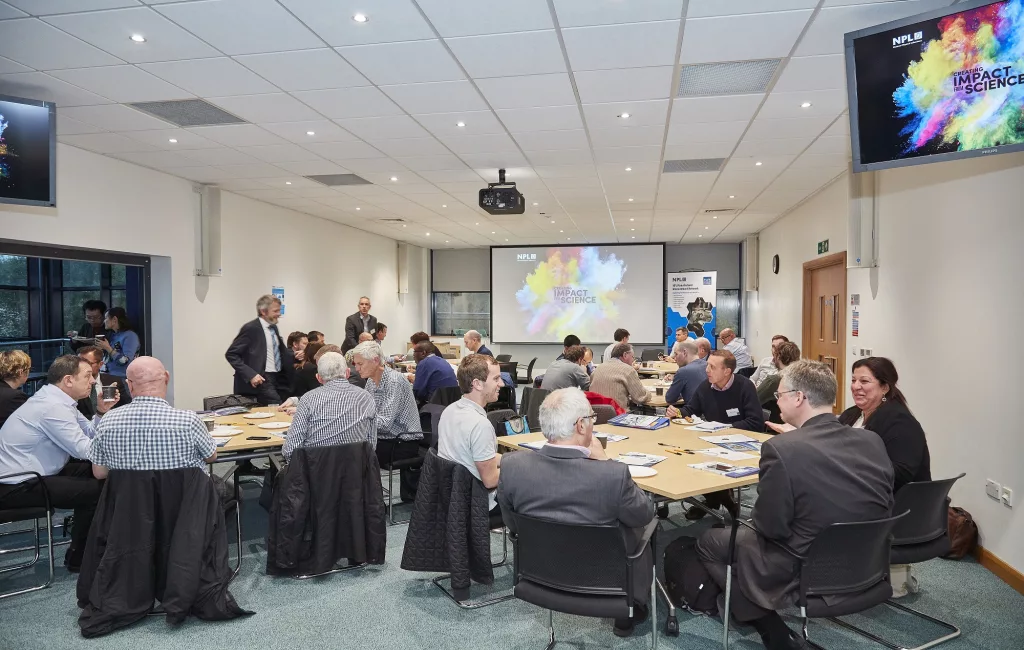
The Future of Transportation : The first event of 2019 for Measurement Manufacturing Network (MMN) led by the National Physical Laboratory (NPL) North of England in conjunction with the University of Huddersfield took place on 15th January at the 3M Buckley Innovation Centre in Huddersfield. The Future of Transportation event was organised by NPL which is the UK’s National Measurement Institute, and a world-leading centre of excellence in developing and applying the most accurate measurement standards, science and technology available, attracted an audience of over 70 people from different business backgrounds including both large organisations and small and medium-sized business (SMEs) as well as representatives of academia, and technology providers. The talks focused on light weighting and composites; electric and hybrid propulsion; and connected and autonomous vehicles. The speakers included Rowan Eagen from Northern Automotive Alliance, Nigel Schofield from University of Huddersfield, Martin Sharp from Liverpool John Moores University, Gareth Hind and Andre Burgess from the National Physical Laboratory. Their presentations helped attendees to develop a better understanding of the complex topics from different perspectives. In addition, the representatives from Leeds City Region based business support programme gave the audience an update about available funding options. The audience was entertained by a usual measurement competition which involved estimating the distance from Huddersfield to Dominican Republic in kilometres. The winner was a representative of Lancereal Limited located in Huddersfield and received a prize of NPL mug and socks! The event received very positive feedback, and many positive comments: “Great event to gain awareness and network with others, gaining different perspectives”. “Good mix of presentations at different levels”. “It was a fascinating insight into future developments”. The opportunity to network with likeminded people is key to the success of events like The Future of Transportation and delegates often find potential customers and answers to issues they face in their day to day business. NPL established a North of England Regional Centre with the aim of supporting regional manufacturing, in particular SMEs, to help them achieve their full potential to become competitive within a challenging worldwide market. NPL has a range of ways to support business such as measurement and product verification related services to help SME Manufacturers identify appropriate validation methods within their business with the aim of increasing efficiency, reducing waste and improving product quality. The NPL MMN has been created to make this process as simple and seamless as possible with free membership to all manufactures. The aim of the Network is to enable the members to benefit from NPL’s expertise with the view of optimising productivity and increasing confidence in their products, keeping their businesses at the forefront of measurement and validation technology. Following the feedback received during previous events from the MMN members, the next event will take place on 16th April at the 3M Buckley Innovation Centre in Huddersfield and will cover the topic of Succession Planning and the Skills Mix for Manufacturers. To book your place at the event, visit https://www.eventbrite.co.uk/e/npl-mmn-event-succession-planning-the-skills-mix-for-manufacturers-tickets-54279467348 or call NPL North of England 01484 505713. Manufacturing & Engineering Magazine | The Home of Manufacturing Industry News
How the Robot Revolution Affects Manufacturing
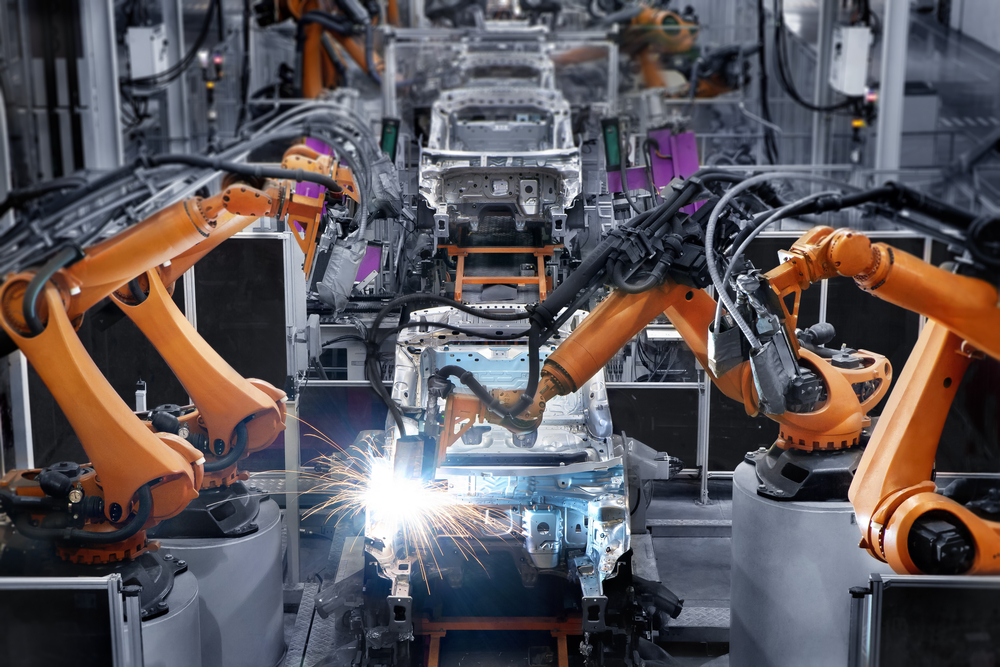
Since the inception of the assembly line, manufacturers have continually searched for ways to improve their efficiency. In the past few decades, robots have taken over some of the functions of human workers, mostly in repetitive, routine tasks. This has caused alarm for some who are worried about robots taking their jobs. So how exactly is the robot revolution changing the manufacturing business? Here’s what you need to know. The State of the Robot Revolution Last year, an 11-inch armless robot named Jibo — a so-called “social robot” — became the latest example of a clear phenomenon: more capable robots are coming soon. In truth, they’re already everywhere: in planes, in cars, in operating rooms, on assembly lines, in the military, and on the last mile. As more robots appear, a new product architecture and more computing power become essential. In 2015, Gill Pratt, who oversaw robotics technology at the Defense Advanced Research Projects Agency (DARPA), said “Improvements in electric energy storage and the exponential growth of computation power and data storage had enabled robots to learn and make decisions informed by the experiences of other robots.” Does that sound frightening? Robots learning from other robots? In a sense, it leads to a larger consumer interest because the smarter robots are, the more helpful they are to humans. The consumer market will approach $100 billion in the coming years. Today, most of the world’s robots are used in factories. What’s different is that those robots are smaller, more observant and more cooperative than their predecessors. Venture capitalists are flooding the robot market, which means we will be seeing more of them in our distribution centers and warehouses soon. And it’s not just manufacturers who are utilising robots. Companies from retailers to hotels are implementing the use of smarter machines. So, not only will more robots become available, the manufacture of the units, all of their parts, and their internal chips and other technology will greatly affect the robotics industry. The Changes Wrought By Bots The upcoming “robot revolution” will change the global economy over the next two decades, cutting the costs of doing business, as machines take over jobs like caring for the elderly or flipping burgers. Robots can already perform manual jobs, such as vacuuming the living room or assembling machines. The development of artificial intelligence (AI) means computers and robots are improving their ability to “think”. They are on the verge of being able to perform analytical tasks once seen as requiring human cognition. This begs the question: what jobs could eventually be taken over by machines? Bank of America Merrill Lynch’s analysts predict the following jobs to be at risk: Burger Flippers, Manufacturing Workers, Financial Advisers, Doctors, and Care Workers. Manufacturing Robots Running off Humans? Should workers be concerned about the infiltration of robotic workers? While the US and Canada have lost more than 6 million jobs to overseas outsourcing, the majority of job losses in both countries was due to machines replacing humans. The facts, however, tell us that over the past two decades, inflation-adjusted U.S. manufacturing production has grown nearly 40%. While there may be fewer jobs, more is getting done. Manufacturing employees have better education, are better paid and produce more valuable products — including technology that allows them to be more productive. In the past few years, there have been millions of jobs remaining unfilled in the manufacturing sector. The aging workforce is not being replaced by younger workers. Youth are more interested in other work. There are other issues to consider as well: Robots are safer. They are reliable. They are more ethical than using exploited labor overseas. They’re incredibly cost-effective, with manufacturers seeing return on investment in 12 months or less. Robots allow manufacturers to focus on innovation. This creates new jobs that require and build a more educated, highly skilled workforce. So, will a robot take your job? Possibly. But, in return, workers of the future will likely find more meaningful work, for better pay. But there is also a distinct possibility that more white-collar jobs will be taken by robots with AI. Conclusion While many will continue to fear robots and AI for the damage they can do to the job market, when businesses are able to save money with cost effective machinery, they have more resources to higher more skilled workers. The robot revolution is inevitable. Humans in manual labor jobs need to prepare for adding new skills or starting a whole new career. Full article: https://www.iqsdirectory.com/resources/how-the-robot-revolution-affects-the-manufacturing-business/
BakerHicks Appoints Business Development Director
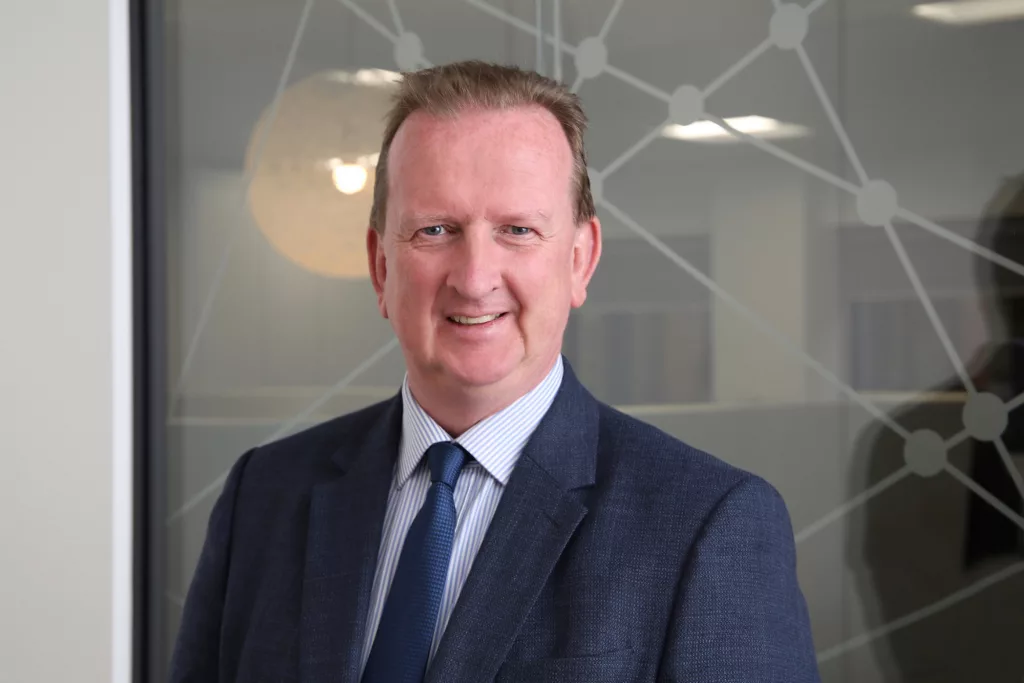
John Lawton has been appointed by BakerHicks, the multidisciplinary design and engineering company, as Business Development Director to support the continued success and growth of the business across its key sectors. John will specifically support the company’s business development and management teams in implementing their respective sales and marketing strategies within the Aviation, Defence, Life Sciences & Manufacturing, Nuclear, Power, Public Sector and Rail industries across the UK and the D-A-CH (Germany, Austria and Switzerland) region. The role reflects John’s own experience in successfully running operational and sales teams in Europe, Ireland and Asia Pacific, most recently for Jacobs, where he spent more than 20 years of his 30 year career in a number of roles, latterly as Vice President of Strategy. “John’s expertise is closely aligned with our sector-led approach. He brings a depth of knowledge and experience that will be crucial as a client advocate, challenging our teams to deliver the best outcomes for our customers,” said Martin Lubieniecki, managing director of BakerHicks. “He has already been supporting our Life Sciences & Manufacturing team in developing its growth strategy since the start of the year. In his new role, he will extend this to the company as a whole, working closely with our leadership team to identify further opportunities for growth and evolving the services we provide,” Martin added. John, a Chartered Electrical Engineer by profession, is a member of the Institution of Engineering Technology (IET). Manufacturing & Engineering Magazine | The Home of Manufacturing Industry News