Qashqai Production in Sunderland Remains Unchanged
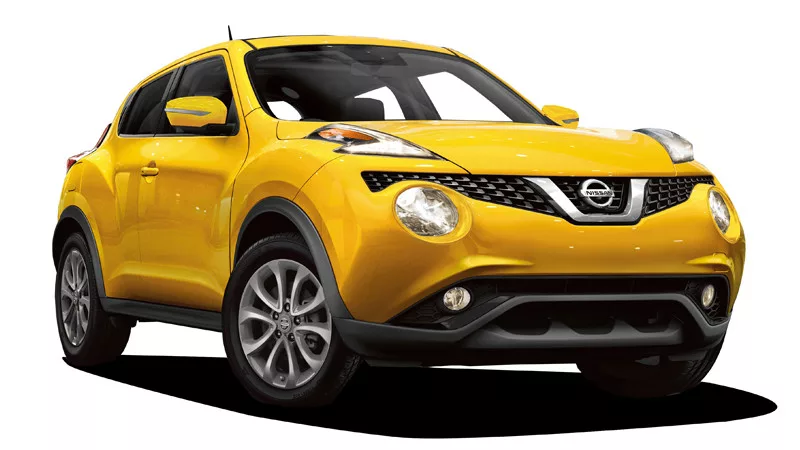
Qashqai Production in Sunderland Remains Unchanged : The plans for Qashqai production in Sunderland have not changed, according to Nissan, although reports stated that the company would review its decision to build the vehicle at the location. But the vehicle maker urged the UK and EU to work together to ensure that an orderly Brexit is achieved. The UK has been a production base for Nissan since 1986, with the Sunderland plant exporting more than half of its production to the EU. The first Qashqai was produced at the plant in 2006 and helped the base build its ten millionth vehicle earlier this year. A statement released by the company said: “Today we are among those companies with major investments in the UK who are still waiting for clarity on what the future trading relationship between the UK and the EU will look like. “As a sudden change from those rules to the rules of the WTO will have serious implications for British industry, we urge UK and EU negotiators to work collaboratively towards an orderly balanced Brexit that will continue to encourage mutually beneficial trade. “While we don’t comment on speculative scenarios, our plans for Qashqai production in Sunderland have not changed.” The SUV accounts for more than two-thirds of the vehicles built at the plant, which employs 7,000 people. Manufacturing & Engineering Magazine | The Home of Manufacturing Industry News
Auto Trader Expands with Software Acquisition
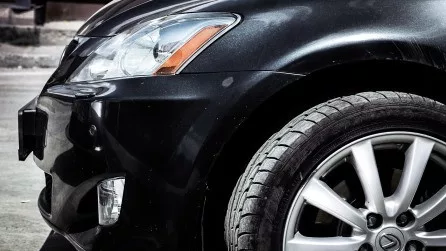
Auto Trader Group, an automotive classified advertising business, has purchased a software specialist for an undisclosed sum. The specialist in cause is KeeResources, a company that provides its services to the automotive industry, including a detailed vehicle taxonomy dataset for new and used cars which Auto uses to power its platform. Funded in 2000, the software company operates out of offices in High Wycombe and Eastleigh. Its reported annual revenue and operating profit for the financial year to 31 December 2018 was reported to be of £5.5 million and £800,000 respectively. “KeeResources has been an integral supplier to Auto Trader, as their unique vehicle taxonomy data underpins much of our core platform. Strategically, we believe it’s important to own and develop such a valuable data source,” commented Nathan Coe, chief executive-designate of Manchester-headquartered Auto Trader. Manufacturing & Engineering Magazine | The Home of Manufacturing Industry News Manufacturing & Engineering Magazine (MEM), is a the leading UK based monthly print & digital publication focused on promoting innovation in manufacturing and engineering available here in the UK. We cover : SUSTAINABILITY (Waste & Water Management, Recycling, Energy); INMOTION (Rail, Marine, Aerospace, Automotive, Defence); INFRASTRUCTURE (Oil & Gas, Nuclear, Construction); Healthcare (Medical), TECHNOLOGY(Printed, Connected, Software, Composite); MANUFACTURING (Chemical, Metals, Plastics, Electronics, Electrical); CONSUMER GOODS(Furniture, Electrical, Electronics, Food) to name but a few. We have over 50,000 views of each issue of MEM on average in 2022 and go to print monthly and also publish in our newsletter, (each issue is available free for 12 months digitally). Our focus is aligned across the next 12 months with our global media partnerships around Trade Events and also contains original content.
Foundrax Delivers Quality Components for Automotive Manufacturer
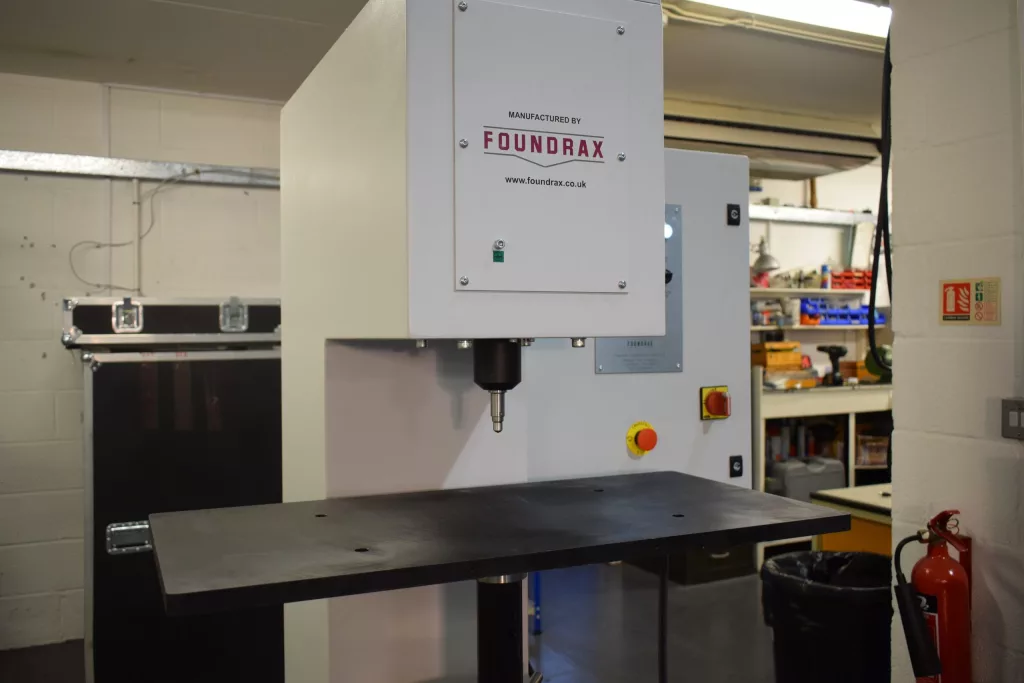
Foundrax, the world’s leading specialists in Brinell hardness testing, has just shipped a second bespoke system for the intricate inspection of automotive suspension components to a full-service supplier of aluminium and plastic automotive solutions in Mexico. The leading supplier of high-quality automotive parts that include aluminium powertrain, structural and transmission components have international automotive manufacturers across the world. Last year, they commissioned Foundrax to address a complex requirement to test suspension parts being produced for a prestigious German car manufacturer. Pioneers in Brinell hardness testing equipment, Foundrax design and manufacture all their own equipment to deliver the highest standards of reliability and repeatability. They are also one of the only companies in the world to offer custom built solutions. This made them the perfect partner for the automotive supplier’s intricate component testing requirement, one that other standard hardness testers on the market simply couldn’t match. The challenge was that the hardness test location as specified by the car manufacturer was in an extremely tight space, hemmed in on three sides by vertical sections and almost no test area to work with. As many of these parts are hollow, there is no other position which would be strong enough to allow for a reliable test. After discussing the options both remotely and on site with the customer, Foundrax solved this challenge by developing a uniquely customised BRIN400B; a rugged, shop floor Brinell hardness tester with customised automatic Brinell microscope to carry out fully automatic indentation and hardness measurement without operator influence on the test or the results. This robust and reliable machine was designed with custom features in the form of an extended indenter in order to access the restricted space and an external BRINtronic microscope with a special narrow nose to enable the customer to measure their indentations. This meant the customer could test exactly where the automotive manufacturer required rather than having to ask for a dispensation to test elsewhere and Foundrax’s solution proved to be a great success. Ultimately, the part design specification effects optimum performance of the vehicle’s suspension. If the material is too hard, the part cracks, too soft and the material bends; so, in either scenario, this is a safety critical test of the component material. Following the successful application of the first machine, the automotive parts supplier went back to Foundrax with an even more complex shaped part to measure. Foundrax commissioned a second system with a bespoke configuration to enable the customer to test in very awkward locations that ensured the highest quality and structural integrity of the suspension component. Alex Austin, Foundrax MD said; “We’re delighted we could fulfil the customer’s requirements. We are always open to making changes to equipment or to making special purpose machines. Our job is to solve the problem and, if required, to give our customers a bespoke product that addresses their need, not simply give them an off the shelf, one-size-fits all, solution.” Offering custom solution components is one of Foundrax’s core USPs and they have done it all over the world, including customers in China, Russia, India, USA and throughout Europe. A modular product design means they can design and build to a customer’s exact requirements. The machines are now being used at this Mexican site as an integral part of the production process in two areas of the factory for quality testing prior to shipping. Foundrax was founded in 1948 with over 70 years of foundry, forge and steelworks experience. They provide hardness testing solutions to customers in 46 countries worldwide and also serve the aerospace, power generation, leisure and construction industries. Manufacturing & Engineering Magazine | The Home of Manufacturing Industry News
Green Light to New Automotive Initiative
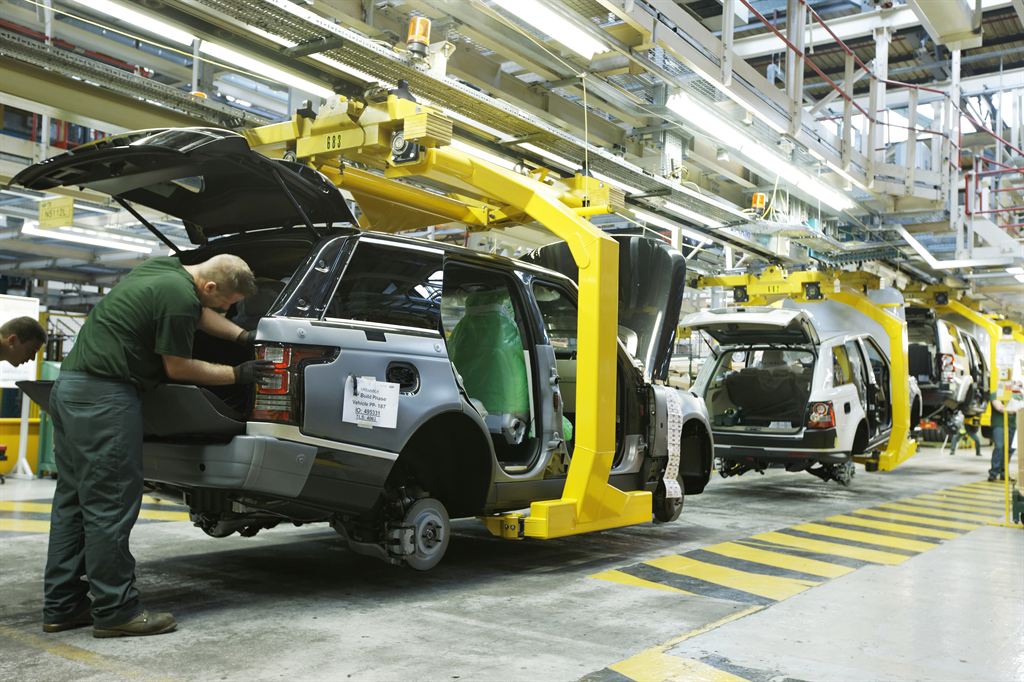
The selection of the National Manufacturing Competitiveness Levels (NMCL) programme, which will deliver the government’s national supplier competitiveness and productivity improvement initiative, has been announced by the Department for Business, Energy and Industrial Strategy (BEIS). Designed to improve competitiveness, raise workforce capacity and increase productivity of UK manufacturers, NMCL will be boosting the nation’s exports and economic growth. Led and match-funded by industry, and with the backing of 25 of the UK’s largest manufacturers, NMCL has been jointly developed by the automotive and aerospace sectors for application across all areas of manufacturing. Delivered by SMMT, NMCL Automotive is designed for the automotive sector and will make use of the £16 million of government funding to develop sustainable and internationally competitive UK supply chains. The new NMCL approach has already been successfully piloted by companies in the North West of England. NMCL is designed to help manufacturers of all sizes and stages of development understand how competitive they currently are and develop the specific business capabilities they need to boost their performance. The programme includes an in-depth competitiveness assessment based on company capabilities and the views of key customers. This data is then applied to investment decisions across six areas of competitiveness; quality, cost, delivery, flexibility, products/technology and customer experience. Projects are tailor-made for each manufacturer and focus on boosting competitiveness, increasing ‘value-add’ and winning more orders. “This announcement is a shot in the arm for the UK’s automotive industry in general and the supply chain in particular. NMCL is a central part of the Government’s Industrial Strategy and the sector deal for the industry, offering a proven way for business to achieve competitiveness. Coming at a time of considerable upheaval, it is important that all manufacturers are alert to the technological, market and trading changes that are occurring and take the right steps to ensure they are not just viable but globally successful in the future,” said Mike Hawes, SMMT Chief Executive. NMCL projects will typically last from six months for smaller initiatives to up to three years for entire business transformations. NMCL’s approach is also ideally suited to other manufacturing sectors such as rail and defence. Companies are invited to declare an initial expression of interest in participating in NMCL by completing a short form on the NMCL website.
Register for this Year’s Automechanika Birmingham
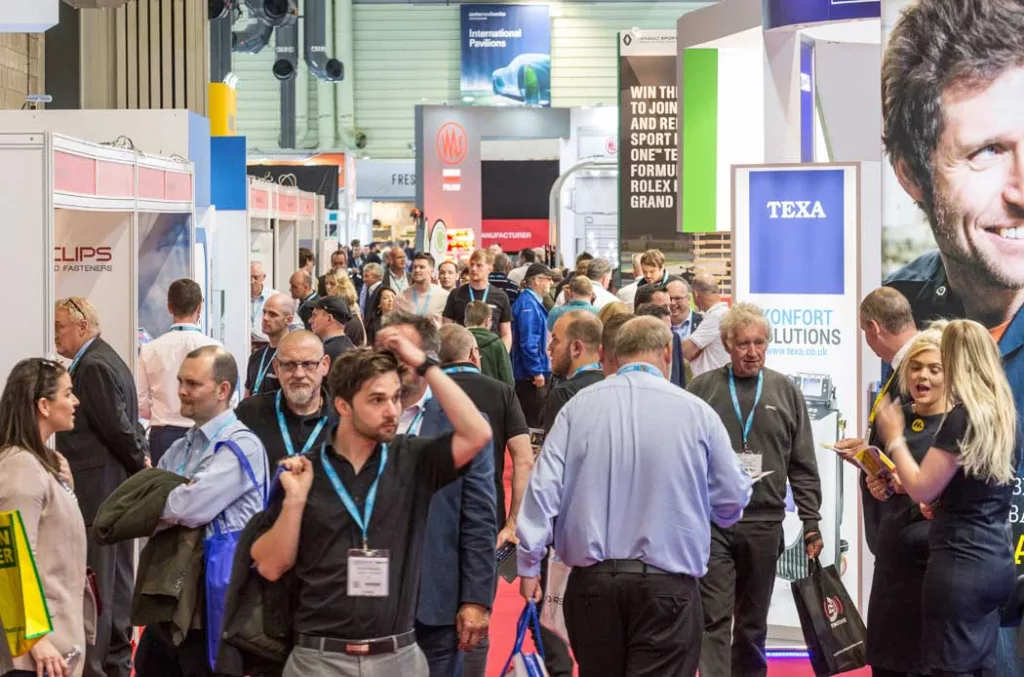
The UK’s must-attend automotive exhibition returns with a larger presence in 2019 before going biennial Automechanika Birmingham is set to return to the NEC from 4 to 6 June 2019, with many major industry players signed up to exhibit. Following hot on the heels of the 2018 event, which saw 86 percent of visitors having purchasing authority, next year’s event has attracted widespread support from across the UK automotive industry. It will be the last time the event runs before going biennial, alternating years with Automechanika Frankfurt. Major suppliers committed to the 2019 event include: Schaeffler, ZF, DENSO, Delphi Technologies, Valeo, Bosch, Hella, Bilstein Group, MANN + HUMMEL, NGK and Yuasa. “The automotive industry deserves its own event and Schaeffler is proud to partner with Automechanika Birmingham 2019. Having successfully established itself as the industry’s exhibition, the event has positively changed the way we as a trade think about and approach exhibitions. We fully support the event’s decision to move to a biennial frequency and encourage others to get behind the event in 2019,” said Nigel Morgan, Managing Director, Schaeffler Automotive Aftermarket. In 2019, Automechanika Birmingham will return for a fourth time and expects to house 600+ exhibitors with more than 12,000 visitors attending. While a new layout is being planned for 2019, visitors to the event will continue to benefit from the hugely successful Garage Quarter, the facilitated meetings programme and SMMT events. This, alongside industry focussed seminars, networking opportunities and the opportunity to launch new products, makes Automechanika Birmingham a must for automotive companies. “The event will go biennial from 2019 – we’re already experiencing a high demand from companies wanting to exhibit to ensure they see the market before 2021,” said Jack Halliday, Automechanika Birmingham’s Head of Sales. Register today and secure your spot at Automechanika Birmingham: https://automechanika-birmingham-2019.reg.buzz/?tts=. Manufacturing & Engineering Magazine | The Home of Manufacturing Industry News
Record Year for Car Sales at Rolls-Royce
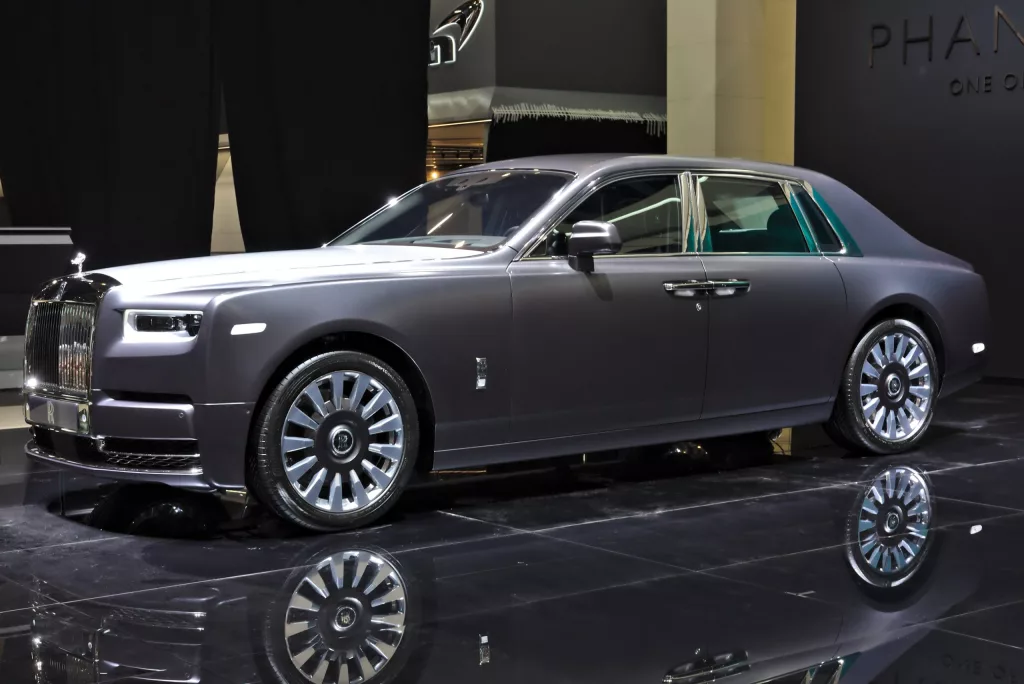
Record Year for Car Sales at Rolls-Royce : Rolls-Royce Motor Cars has announced its highest number of sold vehicles in its 115-year history in 2018. 4,107 cars were delivered by the luxury brand to more than 50 countries across the world, with its Phantom model hailed as a “major growth driver”. The Cullinan, which are the first cars under its SUV model, were delivered to customers in time for Christmas, with advance orders running into the second half of 2019. Torsten Müller-Ötvös, chief executive of Rolls-Royce Motor Cars, described the year as “a most successful, record-breaking” 12 months. “We have seen growth in all our regions around the world. At Rolls-Royce we are deeply focused on each and every one of our customers and are delivering on their demanding expectations. The home of Rolls-Royce at Goodwood is acknowledged and celebrated as a global centre of luxury manufacturing excellence, where our skilled, dedicated team create the world’s finest, most sought-after luxury products. We set a formidable mark in 2018: I am confident it will prove the spur to even greater success in 2019,” he added. Roll-Royce’s largest market in 2018 remained the Americas. Manufacturing & Engineering Magazine | The Home of Manufacturing Industry News
Brexit and the UK Automotive Industry
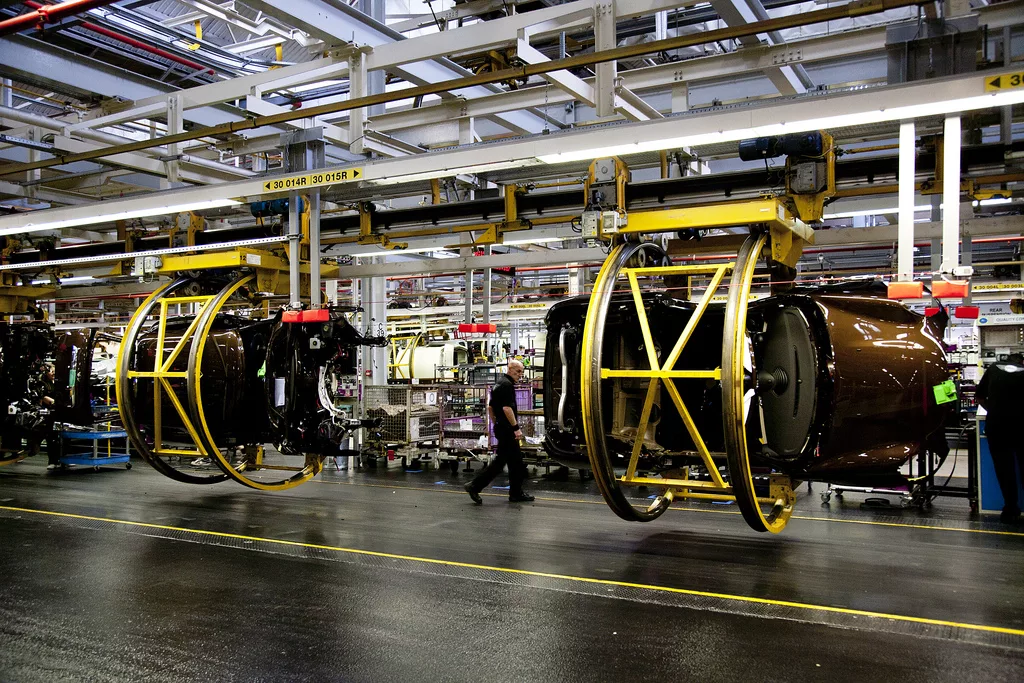
Brexit and the UK Automotive Industry : Uncertainty around the final Brexit deal between the UK and the EU still remains. This is particularly true for the automotive industry where OEMs such as Ford, Honda and Renault-Nissan have all publicly raised their concerns. To find out what was happening within the industry, OpenText and the Centre of Brexit Studies conducted a comprehensive study focusing on this sector. The research study set out to identify the likely implications that different Brexit options could have on the industry and how prepared organisations were across five key business areas: supply chain management, operations and logistics, human resource management, regulations and compliance, and customer communications. The research drew on many different information resources and included in-depth interviews with senior executives in the UK automotive industry. The research findings suggest that all current available trade scenarios put up different types of trade barriers for the sector, and makes a series of recommendations for risk management and scenario planning strategies that can help companies adapt, whatever the final outcome of Brexit negotiations. Key recommendations include: Automotive companies need to have good enterprise information management (EIM) policies in place for managing and reporting on contracts to implement changes and mitigate risks. OEMs and suppliers need to have a strong information governance strategy in place to ensure compliance with any new regulatory requirements or checks. More emphasis on workforce planning and skills development is needed for the UK automotive industry to mitigate restrictions or changes to the free movement of people. Closer communication and collaboration between automotive manufacturers, partners and customers is needed to ensure a free flow of information. Automotive manufacturers need to have an improved understanding of their supply chain, particularly with respect to any new documentation and compliance requirements that might be put in place. Manufacturing & Engineering Magazine | The Home of Manufacturing Industry News
Work on New R&D Facility Begins
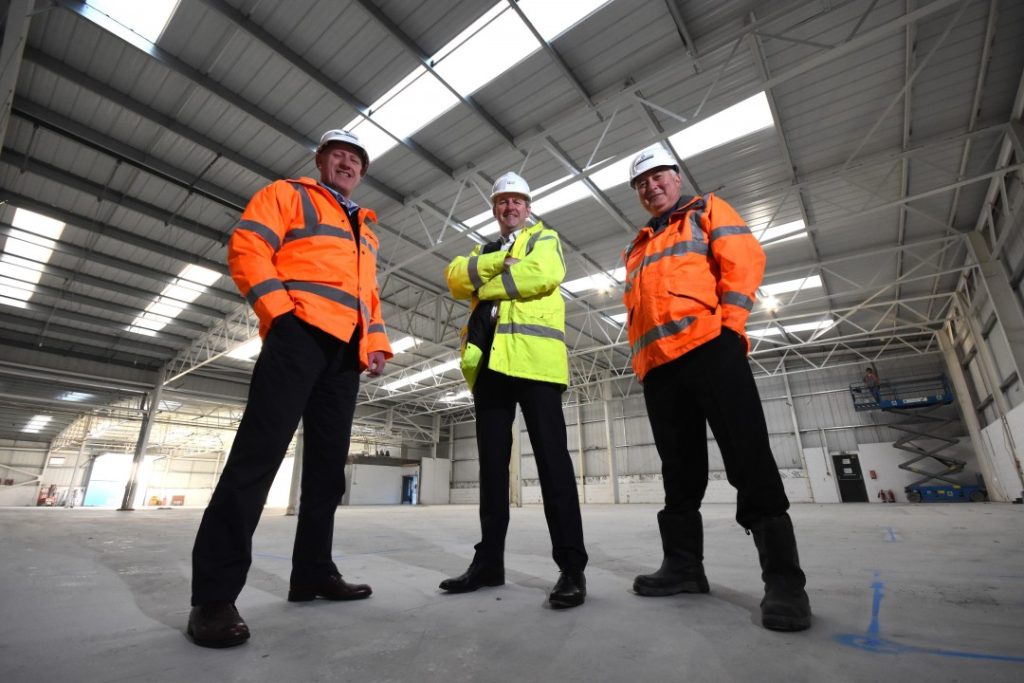
Work on a £2 million research and development facility in Gateshead has been started by BorgWarner, the electric vehicle component maker. After acquiring Gateshead’s Sevcon last year, the US-headquartered company will safeguard 200 jobs by building the new laboratory, which will be used by engineers to develop clean technology prototypes for testing. “The new premises will provide us with the facilities and space to achieve the next stage of our growth strategy. We are investing heavily in the new offices and testing facilities and hope to be up-and-running by the summer next year,” said David Sidlow, general manager at Borg Warner. In March 2017 BorgWarner moved into 55,000 sq ft of premises at the rear of Gateshead College’s Skills Academy for Construction. Two existing properties are being remodelled to facilitate the company’s expansion. The project manager of the development of the laboratory is Knight Frank’s building consultancy team. Meanwhile, Blake Hopkinson Architecture designed the scheme and Robertson North East is the general contractor, supported by Portland Engineers and Wilson Grey. “We have actually been working on this project for over a year as we were originally appointed by Sevcon prior to the company being taken over by Borg Warner, so it’s a relief to finally get on site and get started,” said Knight Frank managing partner, Ian Tew. “It’s a very exciting, futuristic development to be involved with and because the project is securing a significant amount of local jobs, it’s even more of a pleasure to be steering it,” he concluded.
Automotive Industry a Pioneer for Most Technologies
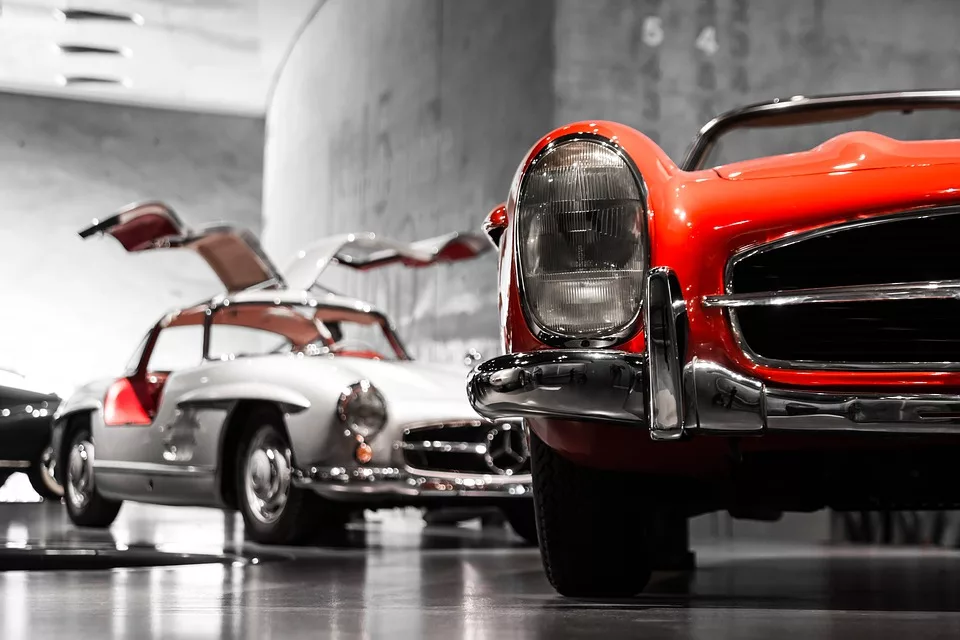
Automotive Industry a Pioneer for Most Technologies : The adoption of smart manufacturing technologies is growing in almost all industries within the leading manufacturing countries such as the United States, Japan, and Germany, and the automotive industry has been a pioneer for most technologies in each of them, finds ABI Research, a market-foresight advisory firm providing strategic guidance on the most compelling transformative technologies. “The automotive industry has been a pioneer in adopting many transformative technologies because it has more of a need and a demand to increase flexibility and agility,” explained Pierce Owen, Principal Analyst at ABI Research. These technologies include Additive Manufacturing (AM), Artificial Intelligence (AI) and Machine Learning (ML), Augmented Reality (AR), and Collaborative Robotics (cobots), as well as Industrial Internet of Things (IIoT) platforms. Some of the leading automotive Original Equipment Manufacturers (OEMs) including Audi, Volkswagen (VW), Ford, Honda, Daimler, and BMW have at least piloted and, in some cases, have scaled these technologies. In terms of overall automation, while most industries have automated 20% to 30% of their operations, the automotive industry has automated closer to 50% of operations. This has resulted in more real-time operational data made available to automotive OEMs and their suppliers. Some of the OEMs use the 3D printers for customized or low-volume production parts, a trend in-line with demand for more customized, low-volume batches. Smart manufacturing vendors targeting automotive have already seen a surprising amount of progress. Dassault Systèmes has Honda North America using DELMIA to design and simulate its plant floors before building them and works with Cummins on the execution side. Telit also works with Honda North America, connecting its equipment. In addition, Telit works with BMW as a client in its factories in Africa and the United States and has Ford as a client with factories spread around the globe. EOS sells 3D printers to BMW, Audi, and Daimler, and Universal Robots sells cobots to 90% of all the OEMs, and even more to suppliers. But, to meet and exceed the complex demands of the automotive industry and scale adoption, smart manufacturing technology vendors need to understand the unique automotive industry challenges, offer solutions with obvious business cases, and have a stakeholder management strategy for all involved parties. “As in many other industries, automotive manufacturing faces the challenges of bridging the gap between IT and OT and providing low-code or no-code tools for content creation, app development, and logic configuration,” Owen explained. “Technology vendors targeting the automotive manufacturing industry need to understand that while automotive shares many challenges with other industries, it often takes them to extremes. For example, while all industries struggle right now to deploy new technologies and integrate them with current processes, the magnitude and complexity in automotive manufacturing present greater risks. One minute of downtime in automotive can cost tens of thousands of U.S. dollars.” If smart manufacturing vendors hope to scale their solutions and platforms in automotive, they must guarantee and prove that they can provide value. “Automotive manufacturing deals with relatively high-value, high-volume and high-complexity products. Neither automotive OEMs nor their suppliers will take gambles on unproven technologies when it comes to their production lines. Vendors must define, prioritize, prove and present their business case before approaching this sector. If they can do so and show potential automotive clients exactly how to implement and integrate their technology without disrupting production, this market will adopt and scale the solution,” Owen concluded. Manufacturing & Engineering Magazine | The Home of Manufacturing Industry News
Torqeedo Launches Lithium-Ion Battery for the Marine Market
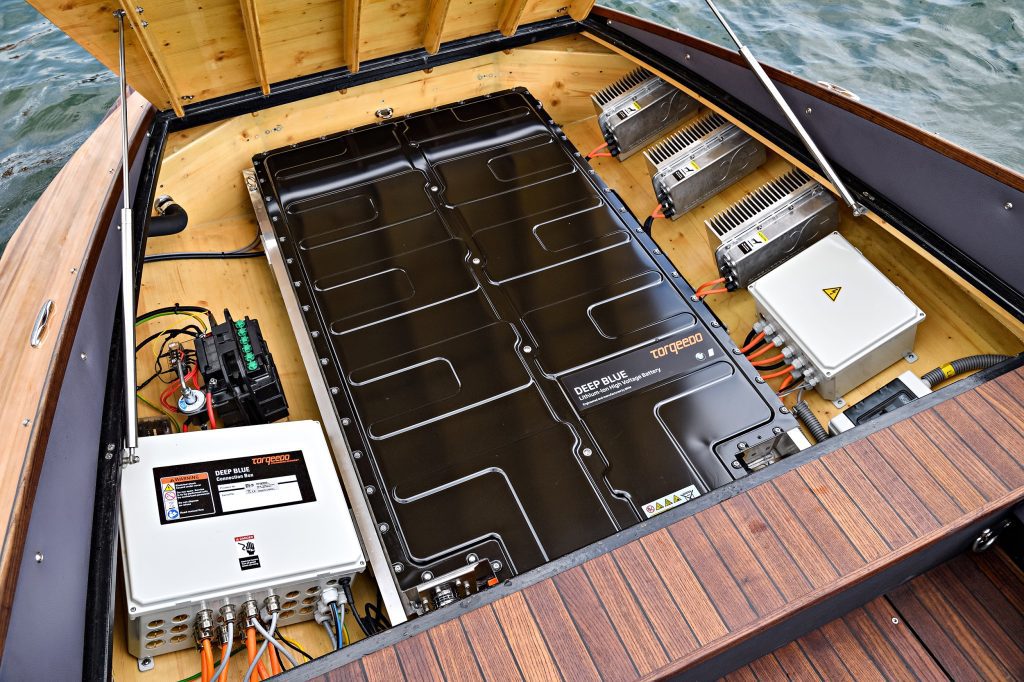
Torqeedo continues to bring the best of automotive technology to the marine market with a more than 30% capacity increase for its Deep Blue lithium-ion battery with technology by BMW i. The new 40 kWh Deep Blue battery (i3-type) brings the latest in automotive-grade lithium-ion technology to the marine industry, offering an increase in energy storage capacity with no increase in footprint. “The Deep Blue series of high-power electric motors are now available in 25 kW, 50 kW or 100 kW power ratings and in outboard, inboard or saildrive configurations. This means larger, faster and more types of boats can now experience the convenience and luxury of clean electric propulsion,” said Torqeedo CEO, Christoph Ballin. “The 40 kWh Deep Blue battery not only extends the range of Deep Blue-powered vessels by more than 30%, it also provides plenty of storage capacity for all onboard needs,” he continued. Produced at the BMW plant in Dingolfing, Germany, the high-capacity battery consists of eight modules, each with 12 storage cells. It has been tailored by Torqeedo so that it is suitable for the marine environment, modifying characteristics such as external shock protection and cooling. Torqeedo also continues its offer of a nine-year limited battery capacity warranty. The new Deep Blue battery features an industry leading energy density of 144 Wh/kg and a comprehensive safety system. It can be charged up to 75% capacity in as little as 1.5 hours when properly equipped and with adequate shore power. Torqeedo is the market leader for electric mobility on the water. Founded in 2005 in Starnberg, Germany, the company develops and manufactures electric and hybrid drives from 0.5 to 100 kW for commercial applications and recreational use. Its products are characterized by an uncompromising high-tech focus, maximum efficiency and complete systemintegration. Torqeedo is part of the DEUTZ Group, one of the world’s leading independent suppliers of diesel and natural gas engines