Airbus Trials Robots as Vehicles
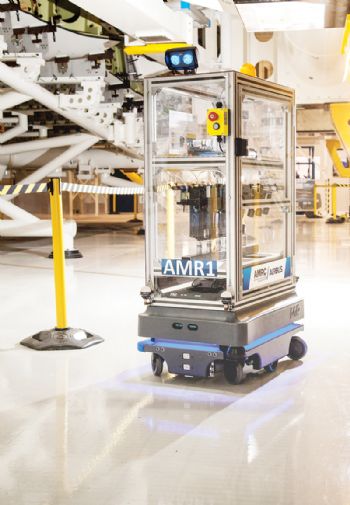
A collaborative research project involving engineers at the University of Sheffield Advanced Manufacturing Research Centre’s Integrated Manufacturing Group could lead to an entire aircraft wing assemblies being transported by autonomous robots at the Broughton Airbus factory in North Wales. “Supervised trials of the robots have already taken place, and it has been estimated that using them could save the whole-time equivalent of one operator per shift at Airbus, freeing them to work on other tasks and ultimately improving shopfloor productivity,” said AMRC senior project engineer Lloyd Tinkler. “This outcome has led to Airbus exploring opportunities where such robots could be used to optimise processes, including specially adapted versions to pull trolleys with aircraft parts and tooling already in use at the Airbus site.” Started with the developing of a safe automated system for delivering tooling within the facility, the ambitious project could be expanded to further benefit from using small autonomous robotic vehicles on the shopfloor. “This project has been our first trial of autonomous mobile robots (AMRs). We enhanced the standard off-the-shelf technology to make it safe and suitable for our factory environment, and we are now working towards its roll-out to other Airbus sites world-wide,” said Amer Liaqat, technology manager at Airbus UK. “We can see the potential to go even further and work with the AMRC to develop autonomous mobile robots for precision assembly tasks such as component positioning and certification. Developing it further, we could see this technology being used to transport an entire aircraft wing between factories at Broughton,” Mr Liaqat added.
TWI Based in Port Talbot is Expanding
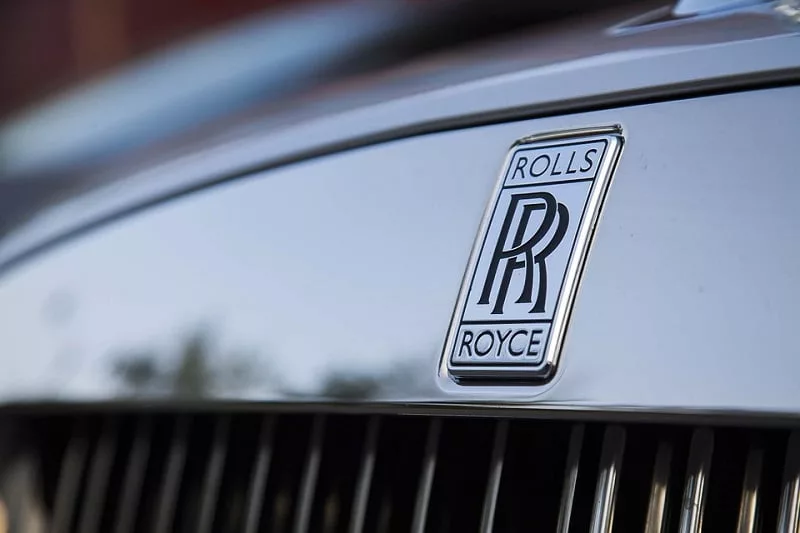
TWI, based in Port Talbot is expanding. With the help of global brands such as Boeing, Rolls-Royce, Airbus, EDF Energy and BAE Systems are all contributing to the expansion of the research and technology firm TWI. A success story of the Waterfront Enterprise in Port Talbot in Wales, TWI has been based in the area for fourteen years. The company has announced a plan to build a top specification engineering and validation facility. TWI focuses on structural integrity engineering, with Headquarters in Cambridge since the 1940s, TWI also has bases in India, Malaysia, the Middle East, China and Texas. The Welsh testing center focuses on non-destructive testing. This process requires a specialized team to use technology such as ultrasonic, radiographs, and electromagnetics to inspect the critical structures of various vehicles like aircrafts, submarines and nuclear power plants. TWI also finds ways of saving time and money by testing advanced materials and evaluating their risk of failure. The plans to develop the Port Talbot arm of the company will create facilities to allow the division to employ more team members, as well as expand their available working space. The Advanced Engineering and Materials Research Institute is expected to increase resources as well as create unique structural testing and evaluation facilities to meet all of TWIâs client needs. The development is being funded by the European Regional Development Fund as well as the Welsh Government, with contributions from industry partners. The ERDF has granted £8 million of funding for the project, as well as a further £8 million combined from their industry partners. The Welsh division of TWI started fourteen years ago, and began with only four team members. Progress made since then shows a successful expansion over the course of that time for the company and promises similar success for this and future expansion. Manufacturing & Engineering Magazine | The Home of Manufacturing Industry News
Airbus Makes Headway on 3D Printing Solutions for Aircraft
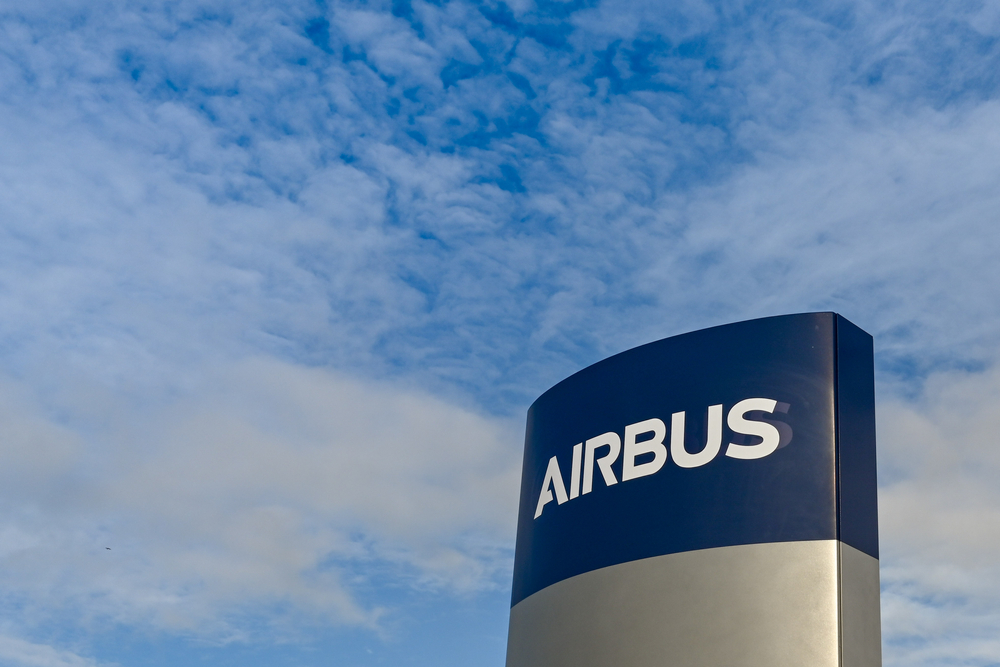
Global aircraft manufacturing specialist, Airbus has revealed it is ever-closer to realising the ultimate ambition of aerospace business: the ability to produce highly complex and highly competent planes with additive manufacturing. The leading manufacturer continues to invest heavily in pioneering additive manufacturing technologies with a view to revolutionising the aerospace industryâs production line and has, most recently, inaugurated a new AM initiative. Itâs through Airbusâ express commitment to creating innovative, and ultimately better, ways to fly that the firm continues to be ahead of the game when it comes to additive manufacturing. At the start of the month, the company launched a new additive manufacturing initiative which pools the skills, expertise and experience of Airbusâ engineering, manufacturing and procurement divisions with the hope of developing 3D printing technologies that are both capable and exceptional. And having long held a leading position in the aerospace industry, this coming-together of the best minds under the companyâs header will doubtless place Airbus is a strong position to lead in a new era of AM. Jerome Rascal, the elected head of Airbusâ additive layer manufacturing initiative, was enthusiastic about the potential of the AM drive. He insisted that the scheme of investment would significantly enhance the companyâs technical and commercial competencies as well as fostering greater closeness between Airbusâ distinct divisions. Through the lucrative partnerships which Rascal highlights, it is thought the multinational manufacturer could develop 3D printing solutions for aircraft in the very near future. In terms of what this might mean for Airbus and the aerospace industry more broadly, additive manufacturing would inevitably speed up production considerably â replacing the need for complex, multi-machine operations with just one and, of course, final assembly. More than that, with fewer operations, fewer materials and significantly less downtime and wastage, AM also has the potential to usher in a new environmental age in the industry. Of course, Airbus has already dabbled in additive manufacturing; 3D-printed parts are currently used across the firmâs commercial range of aircraft, including the popular A350 widebody and A320neo. Indeed, for the firmâs newest aircraft, the A350 XWB, the company has produced over 2,700 additive manufactured, plastic parts. Beyond plastics, Airbus is also working with the European Aviation Safety Agency (EASA) in order to develop additive manufacturing technologies capable of produce titanium parts to an aerospace qualification standard. Whilst AM arguably represents the greatest changes to the production process, itself, Airbus hasnât ruled out exploring the uses of 3D printing for cabin renovation. Indeed, Rascal readily admits, There are surely applications and paradigm changes we have not thought of yet. With that in mind then, Airbus is set to explore and develop 3D printing technologies in both a concentrated and outward-looking way. And following its previous successes and the launch of an AM initiative, the firm will likely do so with great reward.
Airbus Secures Over £8bn of New Deals In Just 48 Hours
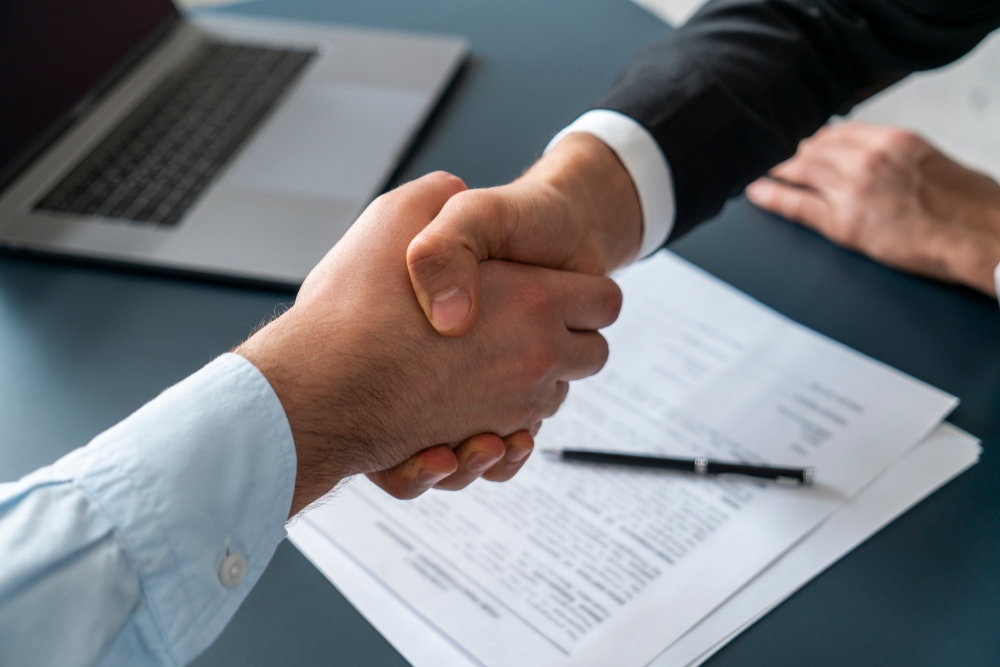
Despite what was described by early reports as a sluggish start to 2016 by Airbus, the aerospace giant has secured over £8bn of new deals â in just two days of trading. As a result of increased demand overseas, the market leader will commence the manufacture of 74 new aircraft for four major clients based in Asia, Africa and the US. And whilst the new planes wonât be housed in any UK airports, thatâs not the orders arenât good news for the UK. In fact, all of the wings for the new passenger planes will be manufacturing right here at Airbusâ manufacturing plant in Broughton. The plant has quite the illustrious history; it marks the birthplace of the iconic aerospace feats, the De Havillandâs Comet and the Mosquito. Broughton currently employs over 6,000 people across sectors of manufacturing, engineers, procurement and finance. The plant is responsible for the wing assembly of all Airbusâ civil aircraft â including even the newest addition, the A350 XWB. Indeed, the greatest boost in sales for Airbus came as a result of its newest plane. China Eastern Airlines placed an order for 20 new A350 XWBs (worth approx. £4.2bn) whilst Philippine Airlines signed on the dotted line for 12 (worth approx. £1.25bn). Air Côte DâIvoire, meanwhile, opted for aircraft from the leading aircraft manufacturersâ long-established range, ordering two A320neos and two A320s at a cost of around £275m. US-based Delta invested in what looks to be a fleet overhaul, placing orders for 37 new A321s (at a value of £2.92bn) John Leahy, Chief Operating Officer at Airbus was unsurprised by the popularity of the new A350 XWB, drawing attention to its outstanding long haul performance amongst its excellent fuel efficiency and comfortable cabin. As well as representing an extension of China Eastern Airlinesâ global identity and air network, the aircraft model will be the flagship of Philippine Airlinesâ long haul provision â adapted to provide a three-class layout of premium seating. It will be utilised for all non-stop flights between China and the US, as well as several new services between Europe and the country. Air Côte DâIvoireâs deal marks a similar spate of firsts and makes them the first African airline operator to order the A320neo aircraft. Delta has specified that each of its new, A321s be fitted with lightweight composite-manufactured wingtip devices called Sharklets so as to maximise fuel efficiency. Sharklets have be known to present firms with up to a 4% saving of fuel-burn â representing both huge financial and environmental advantages. Indeed, Delta became the first to receive its goods last week with an A321ceo delivered on Tuesday 25th April 2016.
Philippine Airlines Becomes The Latest Operator To Purchase The A350
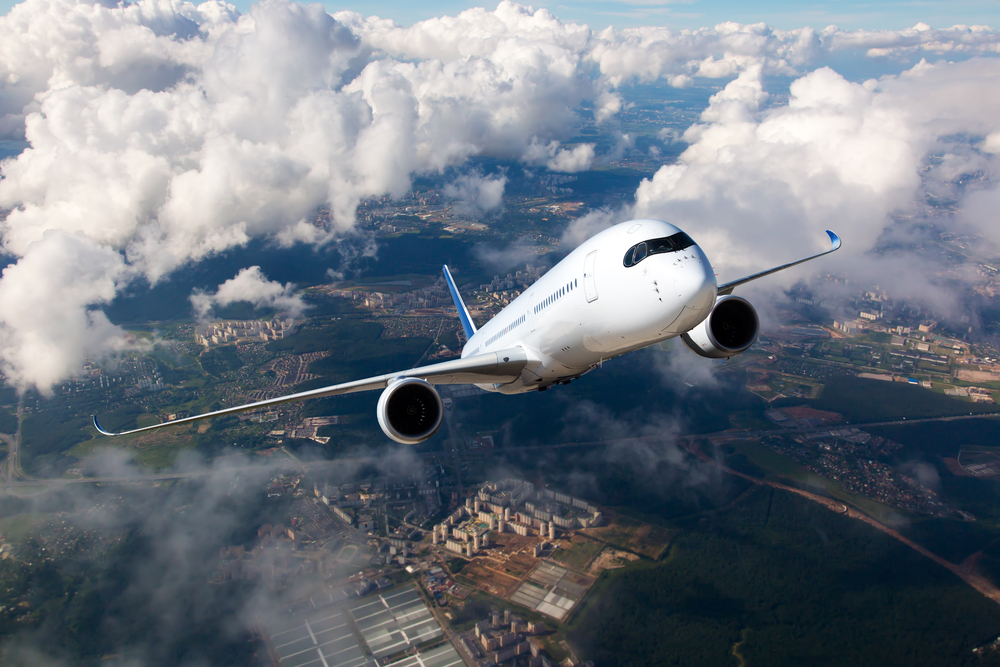
Philippine Airlines has agreed a deal with Airbus for six A350-900s, with a possible six in future. The news came as Philippine Airlines’ President & COO Jaime J. Bautista spoke at the Singapore Airshow where he revealed the airline will configure its new purchases with a three-class premium layout. The A350-900s will operate on Philippine Airlines’ non-stop routes from Manila to New York City and various other destinations on the USA’s west coast. Philippine Airlines is also beginning new routes to Europe and envisages the planes forming a key part of its plans to develop these routes. The airline operator is aided in its ambition thanks to Airbus’ aircraft being able to travel the 8,000 nautical miles to New York from Manila non-stop. Bautista acknowledged that the aircraft had come out on top after a series of rigorous tests and trials. He also said the A350 provides Philippine Airlines with a modern, technologically advanced aircraft that meets the demanding needs of today’s passengers while tackling the challenges faced by airline operators. The aircraft gives operators “greatly enhanced” efficiency while providing passengers unrivalled “comfort”. He also noted the A350’s range saying it was key to the operator’s decision. Airbus President & CEO Fabrice Brégier said the aircraft would offer great advantages to Philippine Airlines, setting “new standards” with extra long “range capability” and highly fuel-efficient new engines from Rolls-Royce. In fact the aircraft achieves 25% less “fuel burn” and “emissions” than previous models while significantly reducing maintenance costs. The new planes are ideal for operators who need to save costs in order to offer a more competitive offer to customers but passengers will see the benefit. The extra-wide cabin is one thing, offering passengers more personal space with seats in economy class measuring an industry-leading 18-inches. It’s unsurprising that Airbus continues to witness plenty of orders for the aircraft with 777 to date from 41 different customers across the globe.
Airbus Increases Production As Commercial Success Continues To Rise
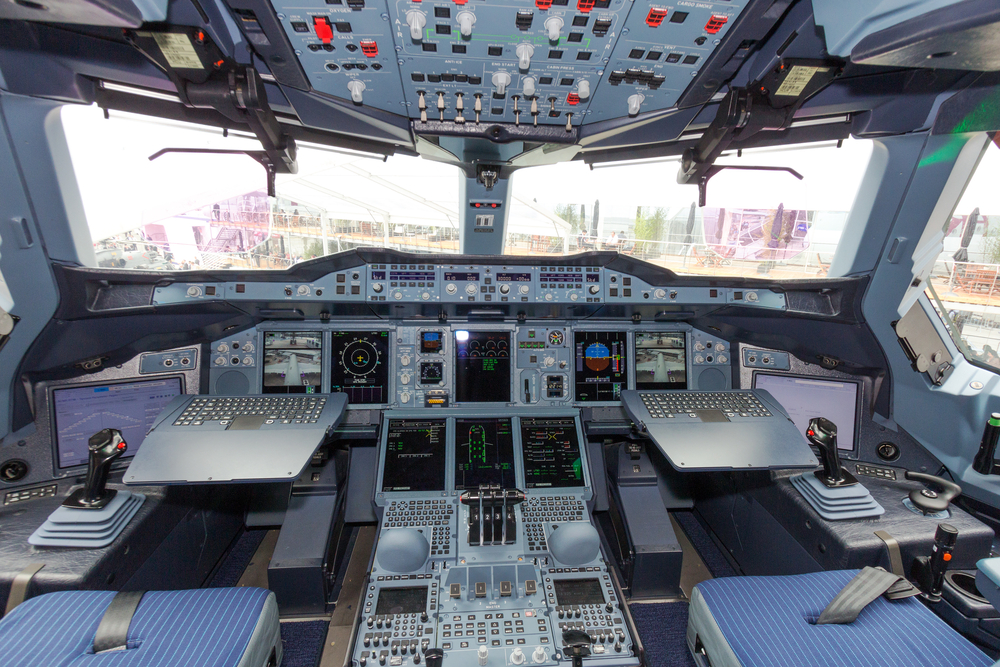
Airbus, the internationally renowned aircraft manufacturer, is pleased to announce the successful increase in production rate for its versatile wide-body aircraft A330. The A330 has enjoyed plenty of commercial success, highlighting Airbus’ ability to produce wide-body aircraft that fit today’s operator needs across the entire world. The A330-200 and its sister – the longer A330-300 – commercial jetliner versions, are the two common A330 aircraft types in operation. Elsewhere, the family includes the A330-200F freighter, the A330 multi-role tanker aircraft, the ACJ330 corporate derivative, and two planes currently in production that have been optimised for fuel efficiency – the A330neo’s 800 and 900 variants. Taking effect at the beginning of next year, production will rise from six aircraft every month to seven. It’s a case of the order book being full and Airbus, which employs more than 60,000 people across France, Spain, Germany and the UK, wanting to meet the needs of its customers sooner rather than later. As of January this year, the company had 1,610 A330s on order, 1,261 of which have already been delivered. The A330 Family Programme’s head honcho Eric Zanin said the A330 had enjoyed particular success in recent months across China, South Africa and Saudi Arabia. This increase in commercial success was added to by the aircraft’s military derivative which meant an increase to seven planes instead of six per month was needed. The latest innovation in the family – the A330neo – will see its first public flights in late 2017. Airbus envisages its newest aircraft will help it confidently tackle an emerging market. Indeed, the A330neo offers a number of benefits over rival aircraft with its increased range of 400 nautical miles, better economics and greater passenger comfort with wider seats in economy class. Component production is expected to reach new levels in the summer of 2016 when Zanin said Airbus’ increased production capacity would become “real”.
Airbus opens new A330 Completion Centre in Tianjin, China
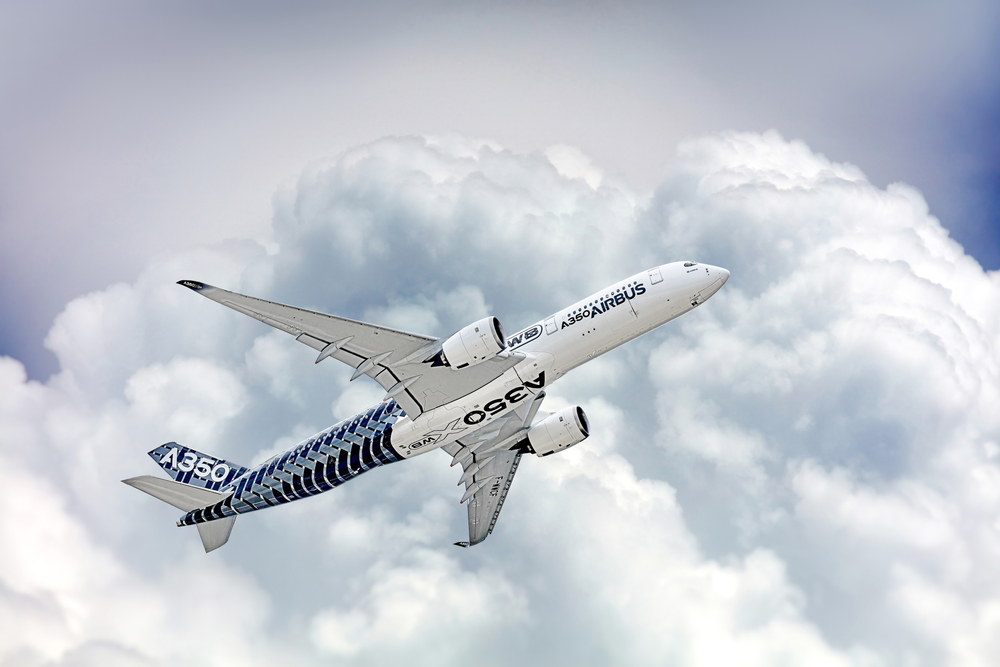
Airbus have begun construction on a brand new Completion and Delivery Centre in Tianjin China. This new facility will be the final stop for the widebody A330 aircraft. The location was chosen due to its close proximity to the final assembly line for the Airbus A320 family. The existing facility has been based in Tianjin since 2009 and has been responsible for the building of more than 250 of the single-aisle aircraft to date. Once the Completion and Delivery Centre opens the facility will employ around three hundred personnel with fifty bringing their experience over from the existing Tianjin A320 assembly line and a further seventy will be moving from Airbus’ various European final assembly lines. The A330 Completion and Delivery Centre will be responsible for a series tasks including installation of the passenger cabin, fuselage paint jobs, engine running, production flights, and final delivery to customers. The Airbus A330 aircraft scheduled to be processed at the new Completion and Delivery Centre will first be assembled at the existing final assembly line in Toulouse, France before being flow to Tianjin. The first aircraft off the production line will be delivered to their customers in September 2017. Also moving over to the new facility is Julien Montcru who has served a series of roles at Airbus and brings with him vast experience. He started his Airbus career in the Toulouse design office before taking on his first management role dealing with A330 cabin furnishings. Montcru then moved onto Hamburg where he worked at the Airbus A380 site when the giant airliners had their cabin interiors fitted before their final paint job and delivery. From 2012 he spent three years back in Toulouse where headed up the paint centre for the A320, A330 and A350. The move makes sense for Airbus with China set to become one of the leading countries for air traffic and the company already having a roughly 50% share of the current market having seen a massive growth over there over the past 20 years.
Singapore Airshow Lets Airbus Spread Its Wings
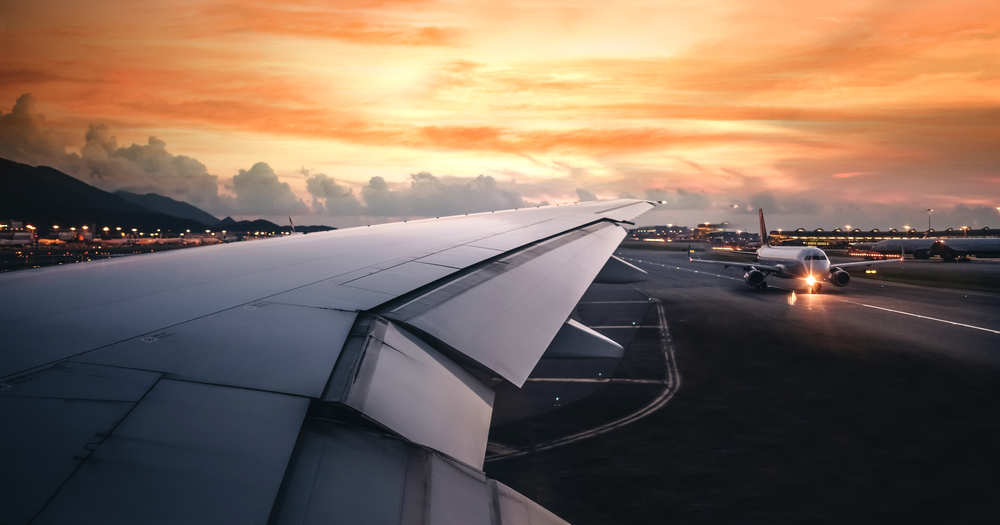
Airbus’ global presence shows no signs of abating after it revealed its latest aircraft at the Singapore Airshow. Its significant presence in the Asia-Pacific region was highlighted by its high-profile presentation at the airshow where potential customers could see first hand its new A350 XWB. Indeed, its appearance has won Airbus one new customer already with others expressing interest. The company also took enquiries which will expand its work in other fields with the Asia-Pacific region. It’s a prime area for expansion as the Asia-Pacific region is the world’s real growth market for civil aircraft. The market has therefore been targeted by Airbus as a new base for key customers where it already provides 31% of Airbus’ orders internationally. The Singapore Airshow gave Airbus another chance to show off its latest aircraft innovation – the impressive A350 XWB. The aircraft is proving very popular with customers in the region and enjoyed a successful presentation at the show where event-goers were wowed by its flying capability. Significantly, the A350 XWB enjoys much of its popularity in the region with Philippine Airlines being the latest carrier to order the aircraft. It will order six initially with another six potentially. The carrier’s specification calls for a three-class layout which will provide passengers with non-stop flights to the New York and the USA’s West Coast from Manila. Airbus’ presence in the region is not simply to provide the market with commercial aircraft. It also provides maintenance and offers training centres as well as other support services. The Singapore Airshow enabled Airbus to extend its presence beyond providing planes for passenger routes with an agreement with the Singapore-based SIA Engineering to provide cabin upgrades, general maintenance and modification capabilities to various aircraft including the the super-sized A380 as well as the A350 and other models.
Airbus On Top As It Moves Towards Zero Carbon
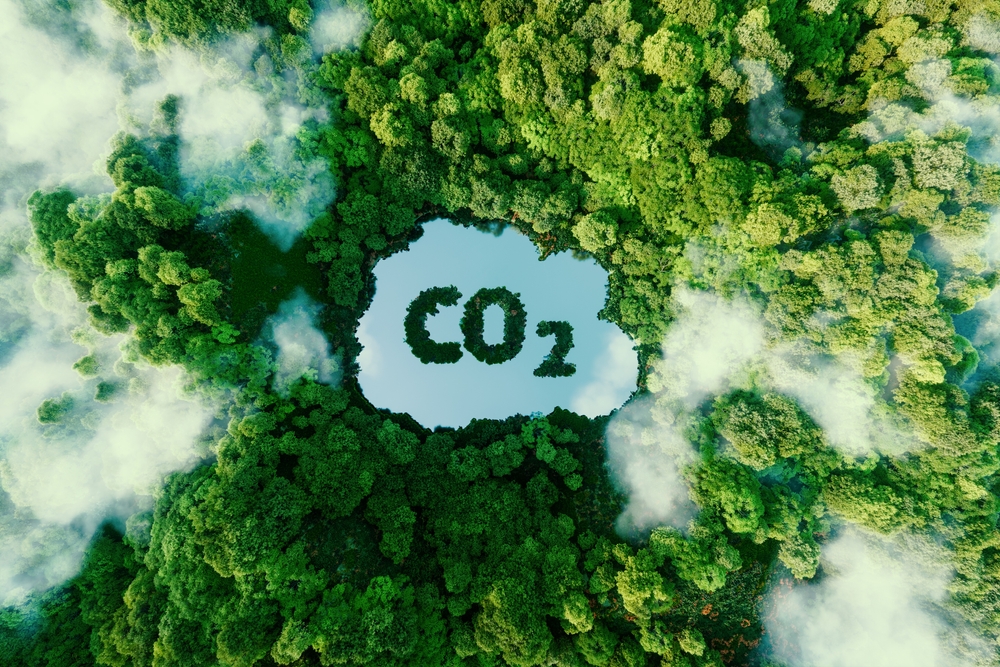
Airbus continues its efforts to reduce the carbon emissions of its operations. While a number of initiatives are ongoing to develop aircraft, systems and operational processes that run more efficiently, its latest innovation is in the use of paint. The Toulouse-based company has designed and built a new paint booth to enable it latest aircraft – the A350 jetliner – to be painted without as much energy demand when compared to typical facilities. The innovative booth in which the planes will be painted will also minimise carbon emissions. Usually, Airbus’ fleet will be decked out in relevant livery through a process which requires 21 to 26 degrees Celsius as a constant temperature and 45% to 70% humidity rate. This has proven challenging as the seasons change with more energy needed to either heat or cool the facility to create the optimum conditions for painting. The new paint booth which has gone into service at the company’s Saint-Nazaire plant will recover heat from the surrounding environment using what is known as the Enthalpic wheel which is essentially a rotary heat exchanger. The system is complemented by a CO2 heat pump (which replaces gas-powered boilers) which brings water up to a temperature of 85 degrees Celsius to furnish the booth with 21 degrees of heat. This eliminates the CO2 emissions generated from gas combustion. Pascal Danthony, project leader, exampled some of the many advantages of the system, not least its capacity to save up to 67% of energy use while drastically cutting carbon emissions. An 86% reduction in CO2 has been achieved. The leftover 14% comes from the electrics in the fans and heat pump. The biggest advantage, however, is the process can be put in place across Airbus’ many paint shops elsewhere. This would make an even greater gain in manufacturer’s green agenda while it has reported payback on investment of four years.
Airbus Global Footprint to Grow with New C&DC in China
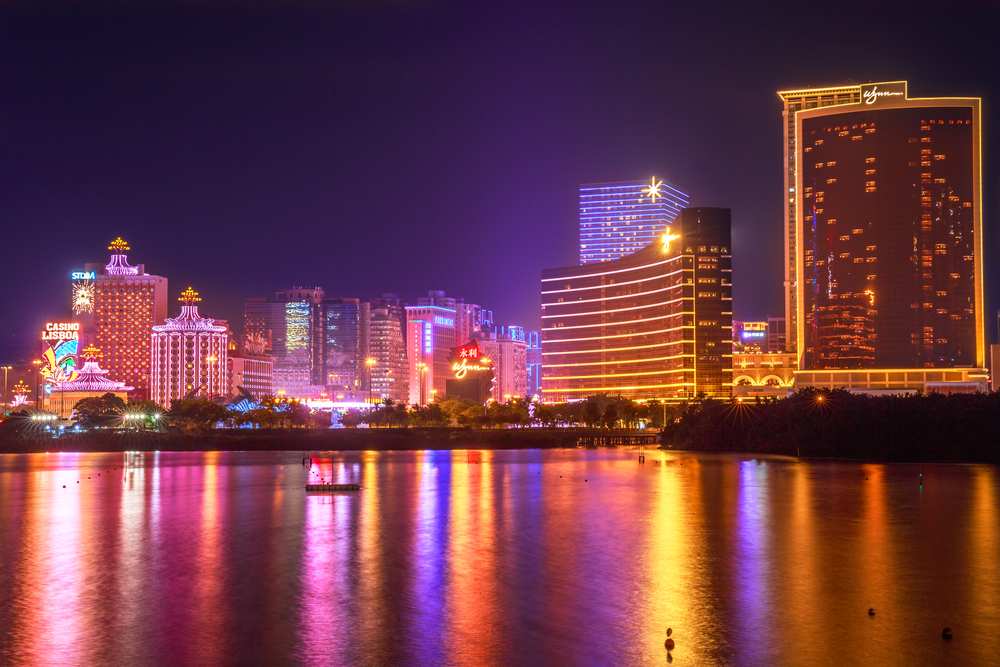
Following recent investment and a new partnership with China, Airbus is to grow increasingly international. The aerospace giant is set to enlarge its global footprint significantly as China welcomes a new Completion and Delivery Centre (C&DC) in Tianjin, expected to house the Airbus A330. The new facilities will add to Airbus’ existing presence in the country, and will occupy the same site as the Family Final Assembly Line and Delivery Centre for the Airbus Tiajin A320. Plans were approved by the Tiajin Free Trade Zone (TJFTZ) and the Aviation Industry Corporation of China (AVIC) back in 2014. President and CEO of Airbus, Fabrice Brégier is confident the development will allow Airbus to widen its customer base, commenting that the A330 C&DC was “a new milestone for Airbus’ international footprint”. At the project’s sign off, it will be the company’s first C&DC for widebody aircraft beyond the borders of Europe. Airbus had previous only served China’s single aisle market. The A330 C&DC Tianjin is is expected to provide a number of key maintanence and manufacturing services. It will incorporate facilities including: cabin installation, aircraft painting and flight test, as well as aircraft delivery and customer flight acceptance. The new A330 Family aircraft is to be the first test for the Tiajin-based facilties. While the new aircraft is to be assembled in Toulouse, final touches like painting and cabin fitting will be conducted at the new C&DC in Tianjin. The Airbus A330 has been a consistent hit with Chinese operators. Despite not being the most prevalent of any Airbus model in the country, it is regularly billed as the most popular with operators and passengers alike. There are current over 170 Airbus A330 Family aircrafts in use by Chinese operators compared with some 1,000 A320s. Airbus has long been a leader in the passenger airline market and the new C&DC is the latest in a string of recent investments for the company. The new facilities are hoped to support the firm’s increasing passenger numbers. Demand for air travel in China is, too, expected to grow well beyond the global rate predicted – at a rate of nearly seven percent compared with an international average of just 4.6%. As demand for both domestic and international travel is on the up, China’s economy looks set to continue to to grow. And as the country gets ever more connected with the wider world, exports are set to sky rocket.