Queen’s University Belfast Sees Installation of 3D Bioprinter
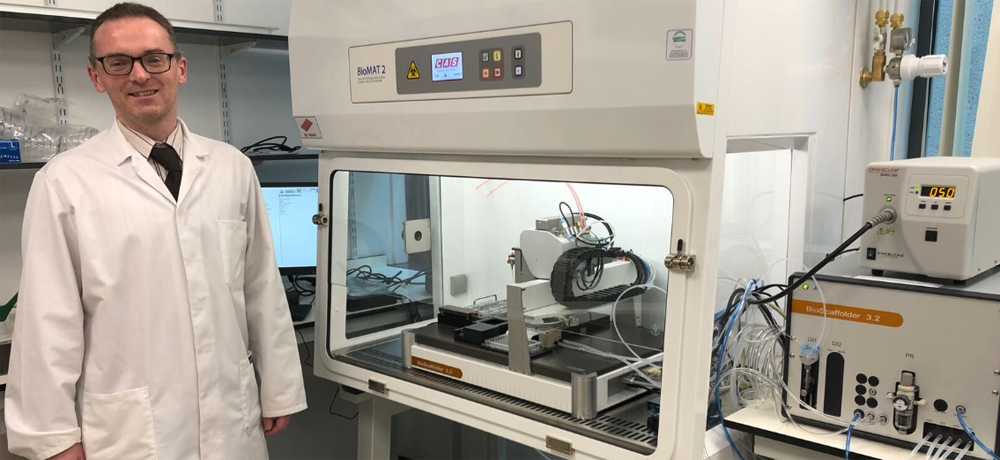
Analytik, a company that provides cutting-edge scientific instrumentation, has announced the recent installation of GeSiM 3D bioprinter at Queen’s University Belfast. It will be used in the development of new processes including the manufacture of medical and drug delivery devices. The company claim, ‘L3D printing could revolutionise personalised medicine’ by creating complex devices tailored to the individual patient through precise control of device geometry, materials and internal architecture. Instrumentation such as the family of modern 3D printers from GeSiM are being used to advance the development of new biodevices. The GeSiM BioScaffolder 3.2 is a flexible 3D bioprinter with a unique piezoelectric micro-pipetting system for pico- and nano-litre spotting of cells and biomolecules, as well as pneumatically-actuated cartridges for precise printing of highly viscous materials (e.g. molten thermoplastic polymers) on definable coordinates within a scaffold structure or on flat surfaces. This combination of both technologies is unique and not available on competitor 3D printers. The BioScaffolder can print polymers at temperatures up to 250 °C, while cells and biomolecules (e.g. enzymes, proteins) can be maintained at 37 °C or chilled to enhance stability. This innovative approach allows struts of mechanically-stiff materials to be combined with cell-friendly materials (e.g. hydrogels) containing suspended cells in novel regenerative medicine approaches. The instrument automatically aligns print tools of different dimensions by means of a 3-axis light barrier. Struts of up to three different materials can be combined, even in a single layer. Individual cells, cell suspensions and aqueous polymer solutions can be printed onto substrates for applications in single-cell analyses, biosensing and drug delivery. Importantly, the BioScaffolder can be interfaced with existing analytical equipment, with individual cells or minute-volume solutions accurately printed directly into multi-well plates, or onto microfluidic chips or biosensor substrates. GeSiM have recently added melt electrospinning for fibre production and UV-curing capabilities, while a new core-shell tool allows precise printing of tubes, with either a hollow bore or soft internal material, further extending utility. Professor Ryan Donnelly holds the Chair in Pharmaceutical Technology in the School of Pharmacy at Queen’s University Belfast. His research is focused on the design and physicochemical characterisation of advanced polymeric drug delivery systems for transdermal and topical applications. He describes the plans for his recently installed bioprinter which was funded by a Wellcome Trust Multi-use Equipment grant. “Our overall aim is to, for the first time, extend the utility of 3D bioprinting from applications in regenerative medicine into reproducible manufacture of micron-scale drug delivery devices, biosensor production, single cell analyses and enhanced understanding of tumour microenvironments. These novel uses of 3D bioprinting have the potential to make a significant and far-reaching impact, in improving health and therapeutic outcomes for patients. “This is the first 3D bioprinter in our university and, to our knowledge, is the first instrument with the unique capabilities of the BioScaffolder in Ireland. Together with my colleagues, we plan to follow the Wellcome Trust’s strategy on improving health for all, in that it will accelerate the application of research to improve health and drive forward development of new healthcare products, devices and technologies and promote clinical translation of research advances from bench to clinic.” Product Specialist, Hiran Vegad, says, “Working with Professor Donnelly and his group at Queen’s is already proving extremely exciting. Their broad focus will impact on the prevention of disease, antimicrobial resistance, improved diagnoses, better treatments and enhancing understanding of cancer and inflammatory diseases to the benefit of patients worldwide. As suppliers, we at Analytik look forward to playing an active role in this program over the coming years.” Manufacturing & Engineering Magazine | The Home of Manufacturing Industry News
Conference Programme for UKIVA Offers Rich and Varied Content
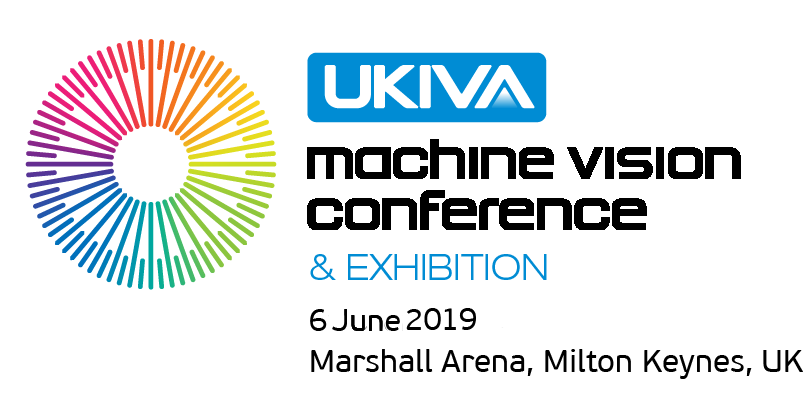
The Conference programme for the UKIVA Machine Vision Conference and Exhibition, which takes place on Thursday 6th June 2019 at the Marshall Arena, Milton Keynes, features 57 seminars across 8 different technology-themed presentation theatres. Dr Luca Benedetti from artificial perception technology specialists, Kudan, will deliver a Keynote entitled ‘Visual SLAM in the Wild’. SLAM refers to the process of determining the position and orientation (localisation) of a sensor with respect to its surroundings, as well as simultaneously building a map of the surrounding environment. New for 2019: Vision in Robotics The new ‘Vision in Robotics’ theatre has been introduced to reflect the growing importance of this topic and will include a contribution from BARA (British Automation and Robot Association). Presentations will include the application of 3D stereo vision in robot applications, in particular for bin picking and part handling. The increasing use of cobots will also be covered. There will also be opportunity to find out how deep learning methods are being integrated into vision and robot applications. The importance of HD digital transmission is discussed for robot applications where fast transmission and long cable distances are involved. High profile vision technologies The other presentation theatres cover a number of technology themes (full details at: www.machinevisionconference.co.uk/programme) with many of the underlying technologies appearing across several of these theatres. Deep learning and embedded vision continue to be hot topics in the industry. This year delegates can explore the crossover between deep learning and embedded vision with the emergence of ‘inference’ cameras, where deep learning capabilities are available within the camera itself. There are also sessions on deep neural network training, practical usage in the automotive food and packaging industries, deep learning vision solutions in the context of Industry 4.0 and AI-based vision systems in logistics applications. Contributions on embedded vision will focus on how they differ from PC-based systems and where they can and can’t be usefully deployed. With 3D Vision firmly established as a core vision technology, the Conference looks at how different types of 3D imaging suit different applications and how to specify and design a 3D system. There are special multi-view techniques that can be used for objects that are larger than the field of view, and at the other end of the spectrum there is 3D microscopy. The increasing cross-over between low cost consumer 3D sensors and machine vision will also be explored. Vision components, systems, applications and innovation Camera Technology covers the latest camera interfaces such as CoaXPress and 5GigE, ultra-high resolution cameras, multi-sensor prism cameras and cameras designed for use in extreme temperatures and harsh environments. Some recent developments in lens design to combat shock and vibration and correct distortion will also be discussed, while the importance of consistent lighting for reliable and repeatable results and the use of different illumination wavelengths to reveal hidden information are popular topics. Some very interesting innovations will also be highlighted including the use of polarisation technology for challenging inspection applications. For people interested in practical applications there are many examples of the use of systems in the pharmaceutical, food, automotive, packaging and logistics industries. Manufacturing & Engineering Magazine | The Home of Manufacturing Industry News
Europac3D Showcases at Manufacturing & Electronics Show
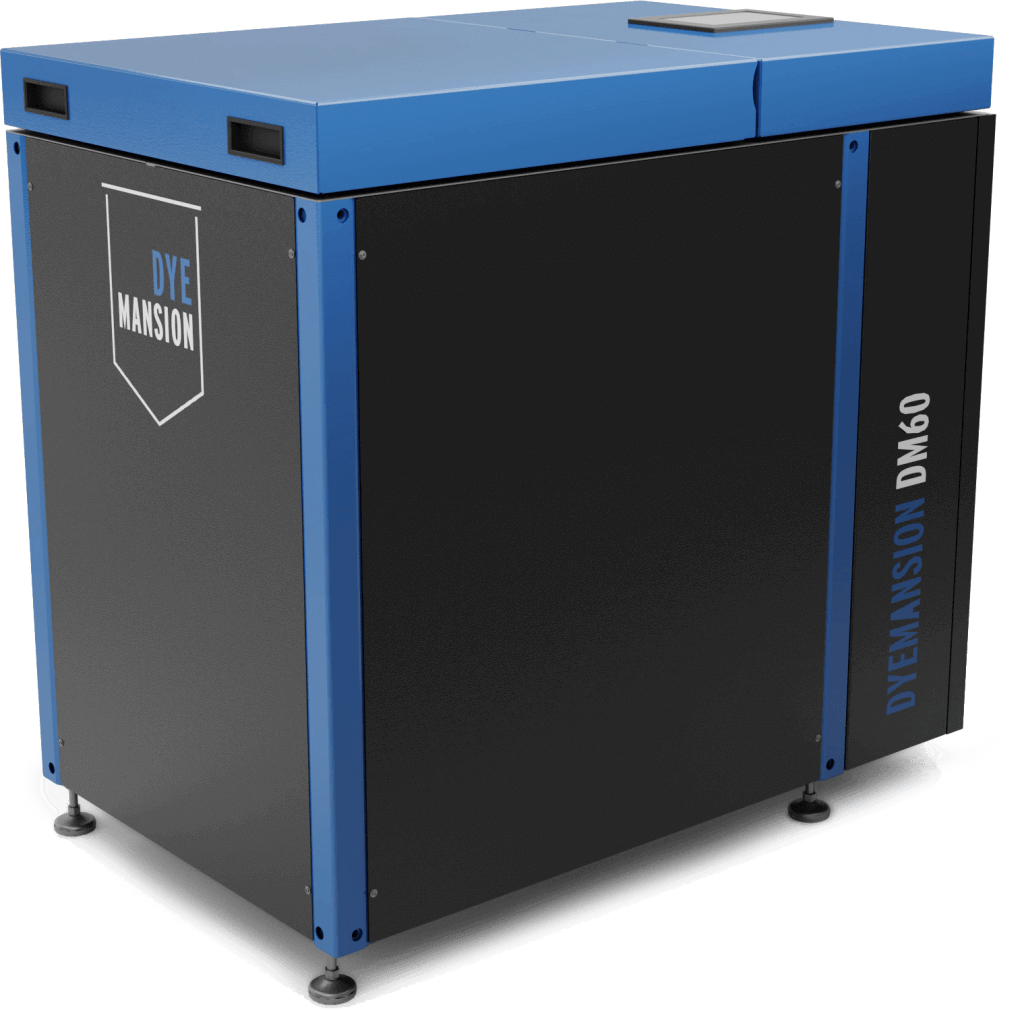
Europac3D, one of the UK’s leading 3D printing, scanning and inspection businesses, will be showcasing some of the latest innovations in 3D printing and scanning at this year’s Southern Manufacturing & Electronics Show at Farnborough International Exhibition and Conference Centre, 5th – 7th February, Stand G80. The company will be showcasing the following innovations at their stand: ROBOZE: Europac3D will be exhibiting Roboze 3D printers at this year’s show – the very first showing of these printers in the UK. Europac will be providing visitors with a unique opportunity to see one of the only FDM 3D printers capable of producing parts in engineering grade high performance thermoplastics, including the highly sought after PEEK and ULTEM. DWS: Also making their UK debut at this year’s show are DWS’ range of SLA 3D printers. Specialising in dental, jewellery and industrial applications, the DWS SLA printers have over 75 different materials options including direct casting, high temperature, ultra-high definition clear and flexible rubber parts. ARTEC LEO: Europac3D will be proudly showcasing live demonstrations of the much anticipated Artec Leo handheld 3D scanner. Leo is the first ever scanner to offer complete onboard automatic processing without the need to be tethered to a computer. “We are delighted to be offering visitors to this year’s show the opportunity to experience the first ever chance to see of a number of innovative 3D printing and scanning technologies first-hand. Our team will be on hand to answer any questions and to provide expert advice. We will also be providing live demonstrations to showcase the capabilities of our machineries and software, so we look forward to welcoming customers to our stand for what promises to be an action-packed experience,” commented John Beckett, Managing Director of Europac. Europac 3D, headquartered in state of the art facilities in Crewe, Cheshire, has more than 20 years of experience in the field of 3D scanning, printing and installation serving a range of sectors and more than 500 businesses across the UK. The company offers a full spectrum of services from the supply of cutting-edge scanners, printers and accessories to installation, maintenance and training of staff in the usage of 3D hardware and software.
Ultimaker Launches Industrial Material Solution for 3D Printing
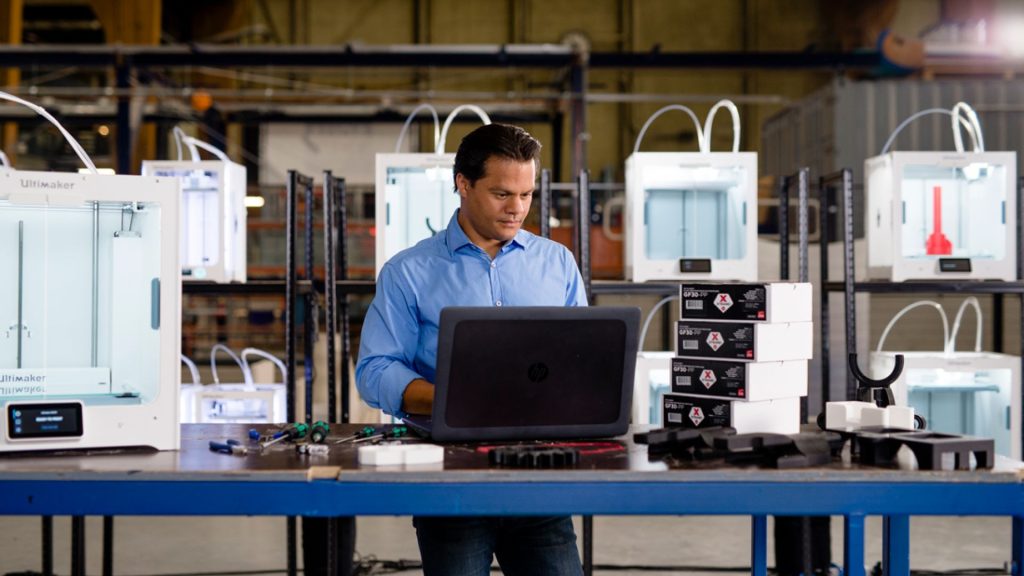
The leading 3D printer manufacturer Ultimaker had initiated a global material alliance that resulted in fully optimised industrial material profiles for professional FFF 3D printing. DSM, a global science-based company in nutrition, health and sustainable living, together with Owens Corning, global developer and producer of insulation, roofing, and fiberglass composites, introduce their optimised materials for the Ultimaker S5. Moreover, Ultimakes also introduces a new print core CC Red 0.6 at the TCT Show in Birmingham that allows reliable 3D printing on the Ultimaker S5 with composite materials. DSM Novamid® ID1030 CF10, a new carbon fiber filled grade PA6/66 filament, brings the properties of 3D printed parts close to what is usually achievable only by injection molding. With 10% carbon fiber reinforcement, it produces stronger, tougher, and stiffer 3D printed parts for functional prototyping and end-use applications, at the same speeds as unreinforced plastics. Meanwhile, Owens Corning has created its own high-end 3D printing material XSTRAND™. This specific material is designed for functional prototyping and industrial applications, and has strong mechanical and thermal properties enabled by glass-fiber reinforcement. The material is very durable, with stiff mechanical properties, a very low thermal expansion coefficient, and a high working temperature. “I am extremely proud to see that our global material alliance with leading material companies such as DSM and Owens Corning so quickly open up the possibility to use very sophisticated engineering plastics on the Ultimaker S5. We were recently listed as an IDC Innovator for creating important breakthroughs that address and solve some of the challenges that end users in a number of industries have identified with. This alliance will continue to give more professionals access to high-end materials for all kinds of use cases and industries, and will give each Ultimaker S5 in the field an extra upgrade,” commented Jos Burger, CEO at Ultimaker. The new print core CC Red 0.6 will be available in November 2018. Industrial material profiles will become available in Ultimaker Cura in November 2018.
How 3D Printing Development is Aiding Military Defence
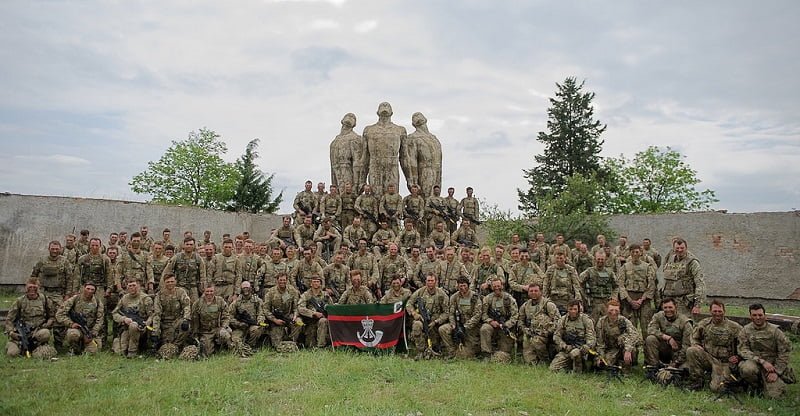
Customized equipment is vital in various sections of military defence. The development of 3D printing gives government, military and defence manufacturers the freedom to design essential products efficiently to ensure low volume tooling while building complex and precise prototypes to further design from. Using an object printer helps to cut the development cycle time by approximately 25-40% with the cost of such developments being reduced by as much as two thirds. 3D printing, particularly when done at home which is becoming increasingly accessible, enables a design to be produced in high quality with moving parts as a realistic prototype. This comes at a relatively low cost compared to other methods such as outsourcing or machining. This advancement means teams can use prototyping on projects where previously this wasnât feasible due to cost or time considerations. Essentially this means products such as weaponry can be created quickly as a prototype before final edits and advancements can be made. In relation to functional testing, more options for efficient prototypes means more opportunities for evaluating whether parts will or will not function as originally intended without losing essential time and money. Such prototypes allow for designers and manufacturers to be aware of potential flaws before incurring any exponentially high costs of re-tooling and re-working an idea. The reduce of risk and cost is allowing more products to be introduced into the military successfully. Having the ability to quickly produce real working prototypes which can be seen and touched by teams of creatorâs aid to bridge the gap between virtual CAD design and final production. Manufacturing and design engineers can use such prototypes as successful tools to better communicate how a design feels, looks and operates. Which allows the product to integrate with manufacturing with little if any problems at an earlier stage than previous development processes. By being able to create various products with such ease and at a lower cost is ultimately changing the way governments and the military behave with their manufacturers and design engineers. Ensuring they get crucial products on a quicker time scale and via a more efficient process.