The Driving the Electric Revolution Industrialisation Centre (DER-IC) network provides open access to expertise and state-of-the-art manufacturing, test and validation equipment in Power Electronics, Machines and Drives (PEMD).
The North East of England is one of the few places in the world with the capability to create a complete electric drive system, consisting of a power electronic converter, electrical machine, controller, and battery. Collectively, these technologies are known as PEMD – Power Electronics, Machines and Drives. They are ubiquitous and found in a variety of domestic and industrial applications, including white goods, electric vehicles and transportation systems, renewable energy (wind turbines, solar arrays, wave and tidal generation systems), and industrial processes.
DER-IC North East can support the design, development and scale-up of the manufacturing process for power electronic switching devices and modules, electrical machines (motors and generators) and electric drives. The network uniquely provides open access to industry-representative, scalable manufacturing and assembly processes to support the development, prototyping, and testing of a complete electrical drive system in a single location.
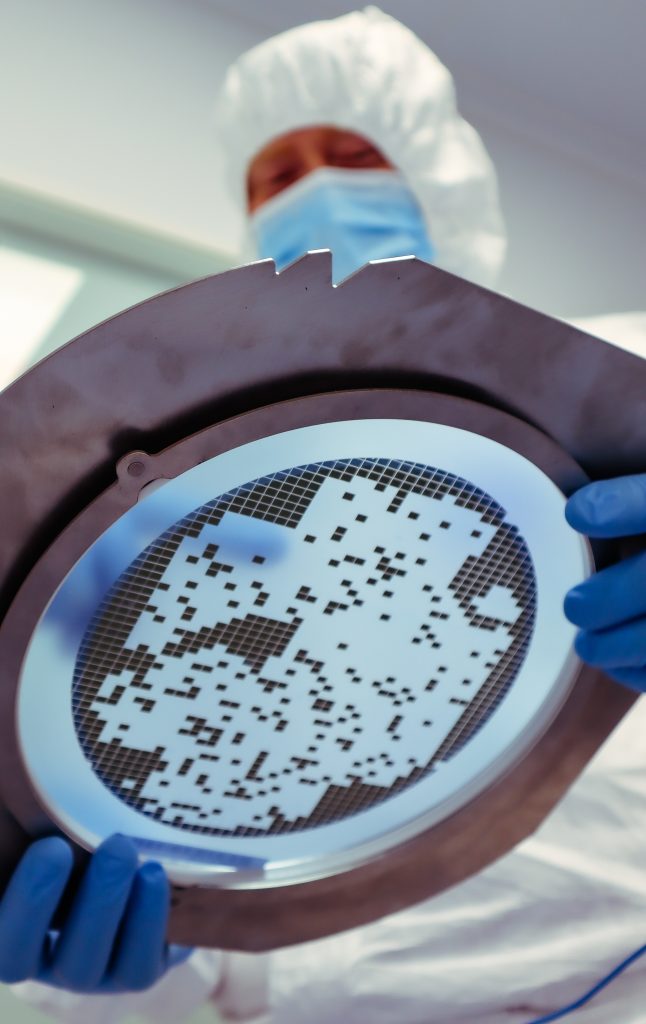
The network enables companies to get products to market faster and with much less capital expense in the early stages. Companies that are looking to produce new products can gain access to DER-IC North East’s equipment and capability to develop and manufacture prototypes, test their performance, and show that they can be produced with scalable manufacturing processes. By following this approach, products can be proved viable before companies need to commit to full-scale manufacturing, and the multi-million pound investments required to achieve that.
As part of Newcastle University, DER-IC North East offers extensive engineering expertise across multiple disciplines, including Electrical and Mechanical Engineering. This expertise is enhanced by the Design Unit, which operates the UK National Gear Metrology Laboratory, providing specialised knowledge in mechanical gear technologies, commonly integrated into electric drive systems.
The site is equipped with seven robot and collaborative robot (cobot) arms from various manufacturers, each offering distinct capabilities. Plans are in place to expand this robot and cobot capability further, particularly in the field of manufacturing and assembly process automation. This will enable companies to explore how cobots can work alongside human operators to complete complex tasks, lower manufacturing costs, and minimise potential injuries.
DER-IC North East also provides advanced environmental testing capabilities with a variety of specialist chambers. These chambers can simulate pressure, temperature, humidity, thermal shock, and vibration to accelerate the ageing process and test product durability in harsh conditions.
In terms of inspection and testing, the facility offers both visual and mechanical evaluation methods. Automated optical in-process inspection is available, alongside X-ray and CT scan inspection that allow for internal examination of electronic packages, modules, and other mechanical assemblies to identify manufacturing defects or service-induced weaknesses. The facility is equipped for pull and shear testing of electronic components and mechanical structures and will feature a scanning acoustic microscope for detecting defects or failures within solid materials.
Embracing Innovation
Ever-evolving, DER-IC North East is expanding its capabilities with several new advanced technologies and equipment. Among these additions will be laser cutting technology, which will be used for the precision cutting of lamination steel in the manufacture of electrical machine rotors and stators, as well as other materials.
Laser welding is also being introduced to support the assembly of lamination stacks and the creation of busbar connections in power electronics, machines and drives components and batteries. To facilitate rapid and accurate capture of complex geometries, laser scanning will be available, aiding in reverse engineering and the identification of packaging space.
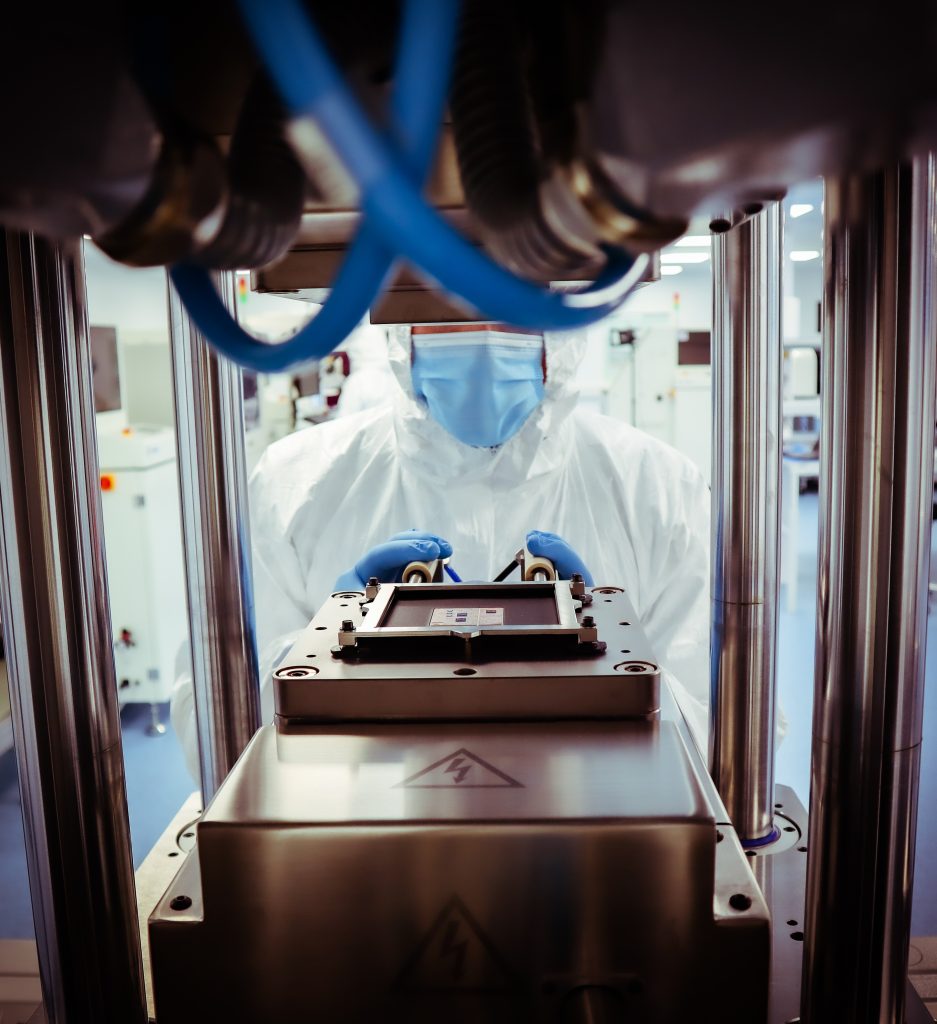
Further enhancing its testing capabilities, DER-IC North East is introducing a thermal testing suite, which will include a specialised safety chamber, datalogging capabilities, and controllable power supplies. This setup will be crucial for developing and testing new thermal management methods aimed at boosting the performance of PEMD components. Additionally, power cycling equipment will be introduced to assess the operation and performance of semiconductor devices and modules. A multidisciplinary team also provides expertise in thermal management.
The facility will also feature equipment for coil winding, essential for electrical machine manufacturing, and encapsulation technology to embed machine components and power modules in resin, thereby improving their mechanical and thermal properties. Finally, there will be an extension of instrumentation to support comprehensive development testing and fault diagnosis, ensuring that new systems can be rigorously evaluated and optimised.
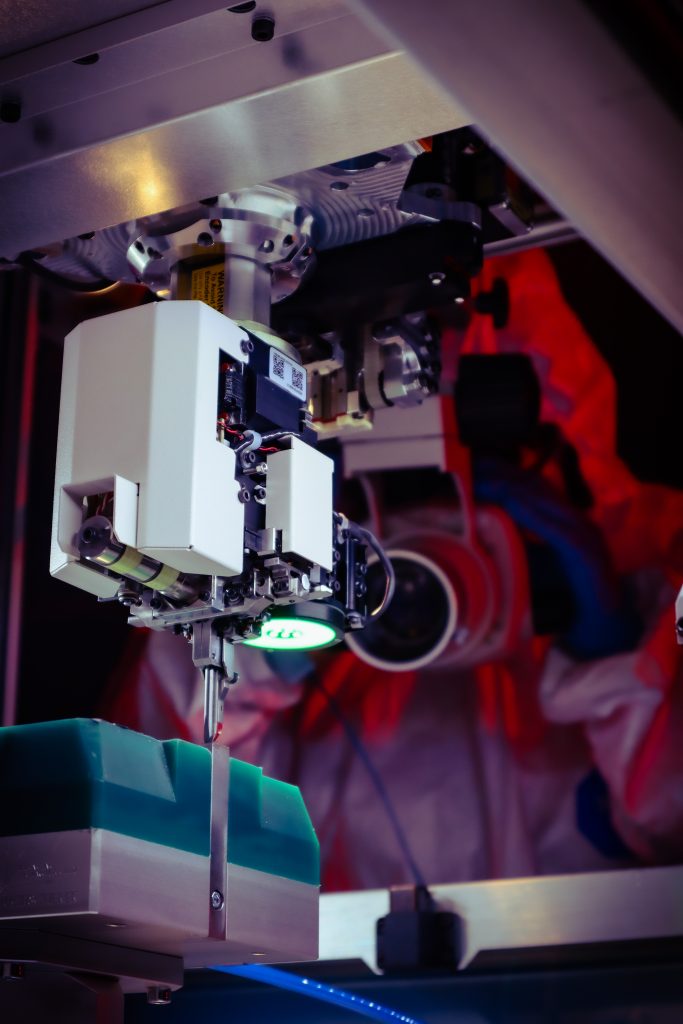
DER-IC North East is pioneering exciting new technologies, particularly in advanced manufacturing for power electronics. A standout feature of its facility is the AMX P101 sinter press, which uses high temperature and pressure to bond components together. Sintering can result in lower profile compact assemblies, by removing the need for wire bonding and, due to the bonding materials used, results in components that are able to withstand significantly higher temperatures than those manufactured using conventional soldering techniques, and which are suited to high-power applications. This advanced sintering equipment is revolutionising the way power electronic devices and modules are manufactured and assembled, enabling innovative design possibilities, and the development of more power-dense assemblies.
Looking to the Future
Looking forward, DER-IC North East maintains a vision to be a front door for industry customers to enable flexible engagement with Newcastle University. This will be achieved through a systems-oriented approach that addresses the full lifecycle of highly integrated electrified systems. From initial manufacturing to remanufacturing, reuse, recycling, and eventual disposal, DER-IC North East ensures that products are developed and optimised with sustainability and efficiency in mind.
What sets DER-IC North East apart is its interdisciplinary teams, which draw from both academic and industrial backgrounds. These teams provide expert support for product and process development across all Technology Readiness Levels (TRLs) and Manufacturing Readiness Levels (MRLs), making DER-IC North East a comprehensive resource for companies at any stage of their development journey.
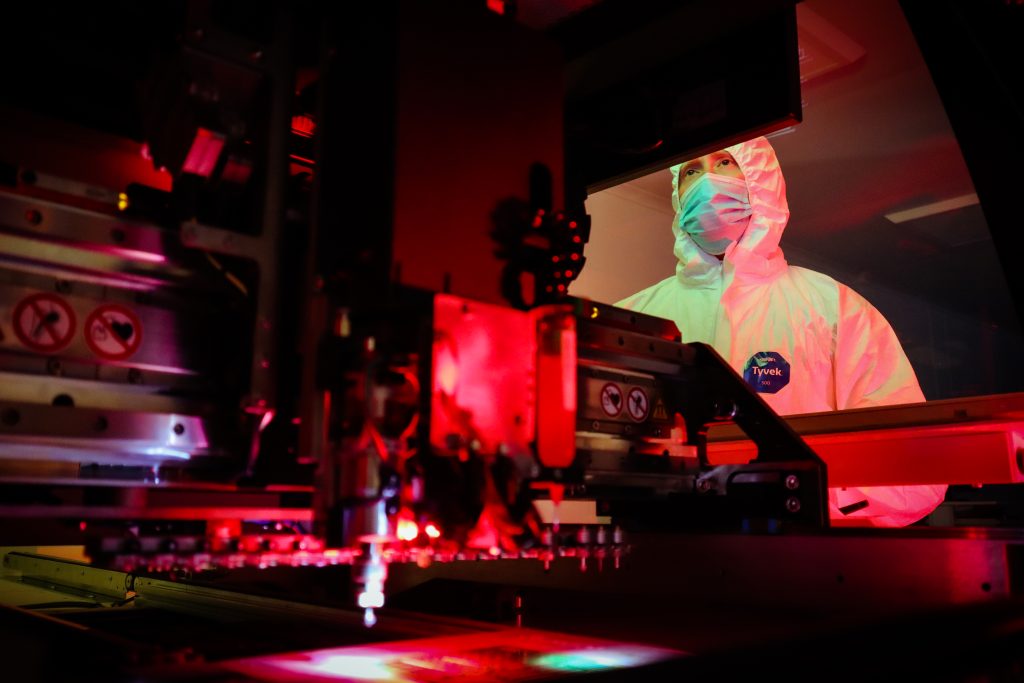
The Centre’s expertise spans a broad spectrum of electrification technologies, including semiconductor devices, power electronics, electrical machines, drives, batteries, renewable power sources, and energy storage. It also excels in mechanical systems, materials, modelling and simulation, prototyping, and advanced manufacturing processes, as well as end-of-line testing and lifecycle analysis.
This capability ensures that from concept to integrated systems, DER-IC North East provides a robust platform for innovation. Moreover, the Centre’s strategic partnerships across the region and nationally, alongside a network of accrediting institutions, collaborators, and supply chain partners, facilitate a coordinated and comprehensive approach to technology development and deployment. Through these initiatives, DER-IC North East not only fosters technological advancement but also propels the transition towards more sustainable and efficient electrification solutions for the future.
Manufacturing & Engineering Magazine | The Home of Manufacturing Industry News