Porvair Filtration Group, a wholly owned subsidiary of leading filtration and environmental technology specialist Porvair Plc, is using its investment in a new TRUMPF TruLaser 1030 Fiber laser cutter to eliminate outsourcing and improve its in-house sheet metal profiling operations. Such is the speed of the new machine that estimates by Porvair Filtration Group suggest it will pay for itself inside the time originally expected.
The company’s New Milton facility in Hampshire is one of two UK operating divisions of Porvair Filtration Group. Established in 1963, the ISO9001-accredited plant with cleanroom facilities specialises in the design and manufacture of high-technology filters for customers in the printing, mining, satellite, petrochemical, polymer and general process industries (including food and beverage), to list but a few. Around 60 people work at the site, with the management team recently deciding to add a laser cutter to its production upgrade programme.
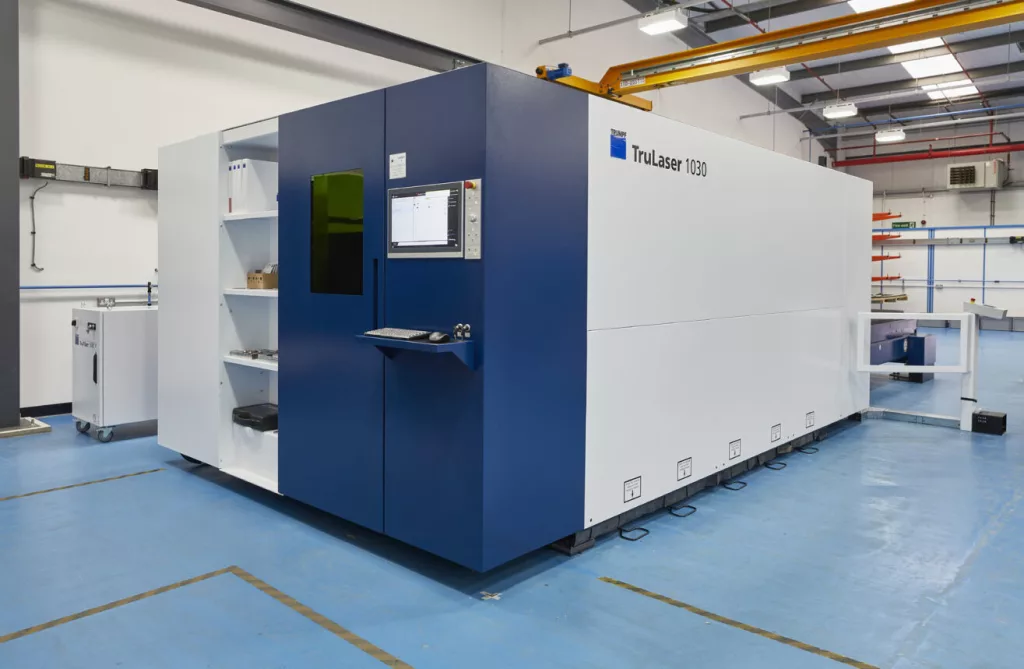
“Until recently, Porvair purchased sub-contract profiled sheet metal parts, performing secondary operations to make them fit for purpose, which was inefficient,” reports Production Engineer Karl Goodman, who Porvair Filtration Group recruited around 18 months ago to oversee the upgrade.
Mr Goodman commenced a review of laser cutters available in the UK, visiting no less than seven potential suppliers. TRUMPF stood out from the pack.
“First and foremost, TRUMPF manufactures its laser unit based on the company’s own design, which we found very reassuring,” he says. “Our confidence levels in TRUMPF technology, along with the service and support available in the UK, far outweighed the other options. The cutting trials were also highly successful.”
TRUMPF recommended the TruLaser 1030 Fiber. Arriving in the third week of August 2023, installation, commissiong and training were complete by the first week of September, with Porvair Filtration Group reporting a “fantastic experience”.
Today, the TRUMPF TruLaser 1030 Fiber is in daily use producing filter components from exotic stainless steel materials that act as filter media. In some applications, Porvair Filtration Group uses filter media down to 1 micron rating.
“The stainless steel sheets are very expensive: a 1.5 x 1.2 m panel costs around £600 on average, so we want to avoid any scrap,” reports Mr Goodman. “We’ve had no problems with the TRUMPF laser, which has an associated app if we need to log any issues. We are still learning how to get the best from the machine; TRUMPF are very quick to support by dialling into the machine remotely to keep us on the right track.”
Porvair Filtration Group uses the TRUMPF TruLaser 1030 Fiber to process sheet from 0.5 to 2.0mm thick. At present, the machine is set-up exclusively for stainless steel to avoid any potential for material cross-contamination. Many parts repeat on a monthly basis, typically in batch sizes of 100 to 5000, eliminating the need to outsource and taking a lot of work from in-house fly presses.
“The difference is like night and day,” states Mr Goodman. “From drawing, to having a cut part in my hand can be as quick as 15 minutes with the TruLaser machine and TRUMPF Boost software. We’re currently running a spreadsheet so we can record what we’re saving. As things stand, we’re on track to outperform our financial justification. It’s pretty impressive considering the TruLaser is brand new to the business. No one here had used a machine like that before.”
He adds: “The financial justification showed the TRUMPF laser cutter would fulfil our current annual demand in a couple of months. This additional capacity will enable us to support other group businesses in the UK and US. There’s little doubt that the TRUMPF TruLaser will have a highly positive impact on the whole group.”
Manufacturing & Engineering Magazine | The Home of Manufacturing Industry News