¬Why hydraulic chucks are more sustainable¬
If tools must be safely clamped while also providing good radial run-out, then there’s no getting around shrinking or hydraulic chucks for the clamping devices. When choosing between the methods, technical aspects and personal preferences most often play a role. However, sustainability considerations should also be taken into account.
As a manufacturer of both shrink and hydraulic chucks, MAPAL compared both methods with respect to sustainability. The comparison is principally based on the areas of technology, economics and social issues as the classic pillars of sustainability. There are always overlaps, as technological progress often goes hand in hand with more economic efficiency.
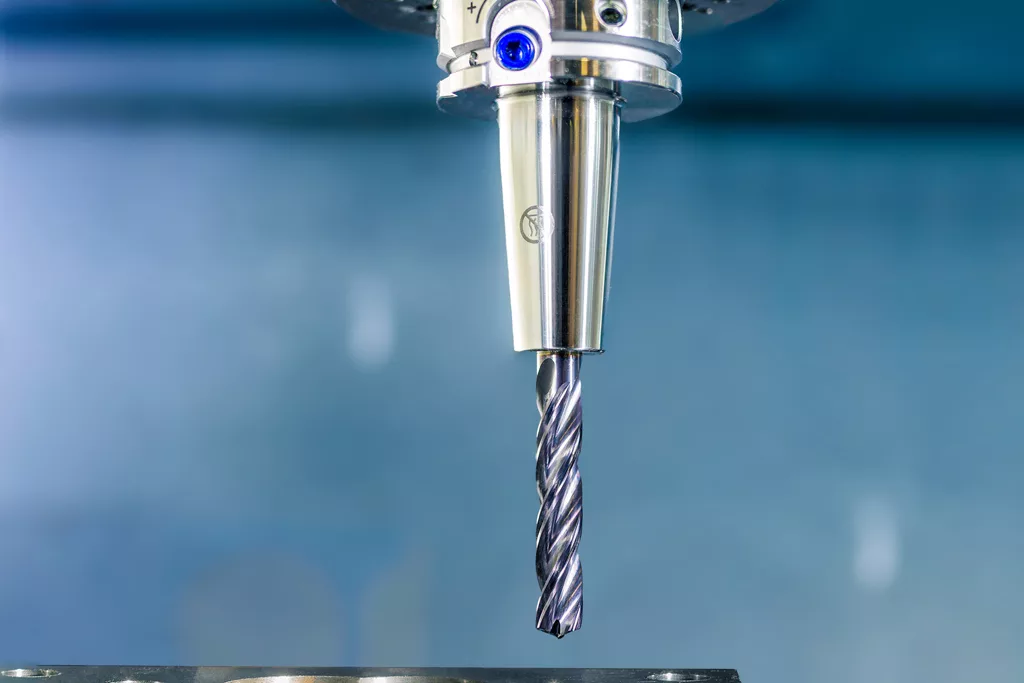
Sustainability can serve as a deciding factor because the various clamping devices are readily interchangeable for many machining tasks. Applications where only shrink chucks are viable due to their innately smaller tool restrictions are becoming rarer. The newest generation of MAPAL hydraulic clamping technology under the brand name UNIQ allows the technologies to substitute each other showing exactly the same tool restriction as defined by DIN.
The UNIQ hydraulic chuck from MAPAL has at least a ten-times longer tool life than a shrink chuck and promises reliable machining results. ©MAPAL
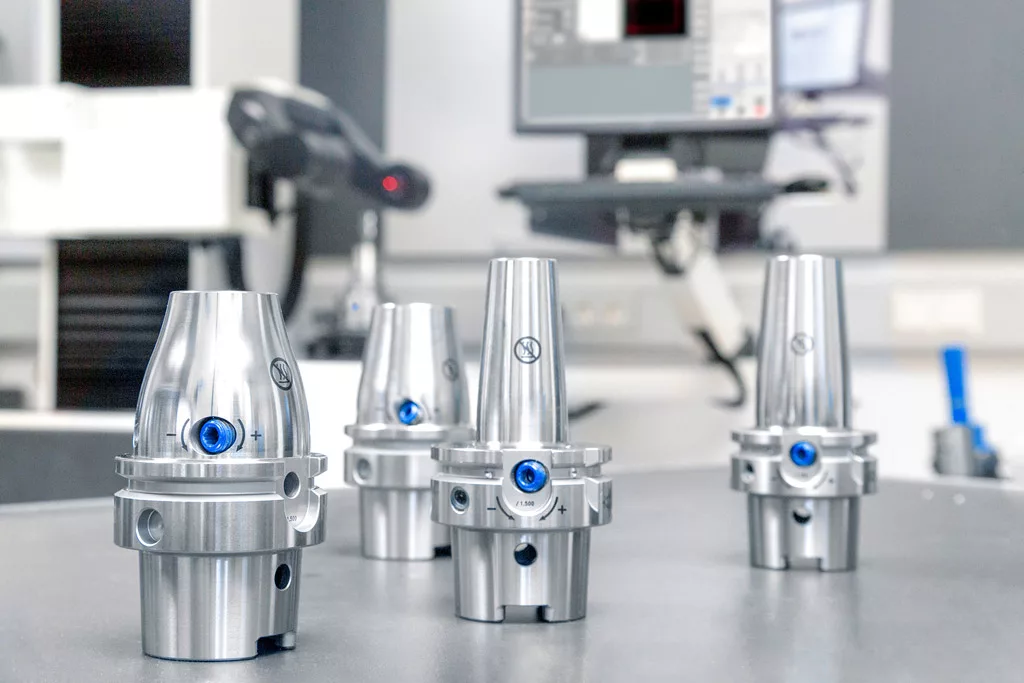
When it comes to sustainability, a big advantage of the hydraulic chucks is a much longer tool life. In the comparison, MAPAL investigated that they last at least ten times longer than a shrink chuck. What’s more, they can also be reconditioned. If installation parts are replaced during servicing and the hydraulic oil is refilled, the chucks run like new again and are ready for another full tool life. While a shrink chuck clamps approximately 500 cycles, the current UNIQ hydraulic chuck models from MAPAL can reach 10,000 to 15,000 cycles. In this way, a hydraulic chuck, which is twice as high in terms of pricing, actually pays for itself – in particular because shrinking technology involves additional costs for a device.
Tools are clamped in shrink chucks by heating and cooling the connection. In this regard, the structure of the material changes every time, which leads to fatigue. The quality of the clamp lessens with every shrink procedure; radial run-out and rigidity keep deteriorating from the first use onward. By contrast, clamping with oil reduces microvibration during machining. Tool life and surface quality are therefore improved: Hydraulic chucks reliably generate better surface finish over their entire tool life.
Shrink units are power guzzlers
A strong argument for switching to hydraulic clamping is the high energy requirements for shrinking. In its own factory, MAPAL ascertained that a shrink unit that is used in three shifts per day can consume between 10,000 and 12,000 kilowatt hours per year. This corresponds to the electricity consumption of five energy-conscious two-person households. This energy consumption not only entails high energy costs but also emits a large amount of CO₂.
According to the statistical analysts at Statista, the current energy mix in Germany results in approximately 366 grams of CO₂ being emitted for each kilowatt hour. Each shrink unit therefore emits 3.6 tons of CO₂ into the atmosphere every year.
Nowadays, this has an impact on the entire supply chain, where the sustainability of manufacturing is becoming increasingly important. Many first- and second-tier customers only want to source from suppliers that can prove that they are reducing their carbon footprint.
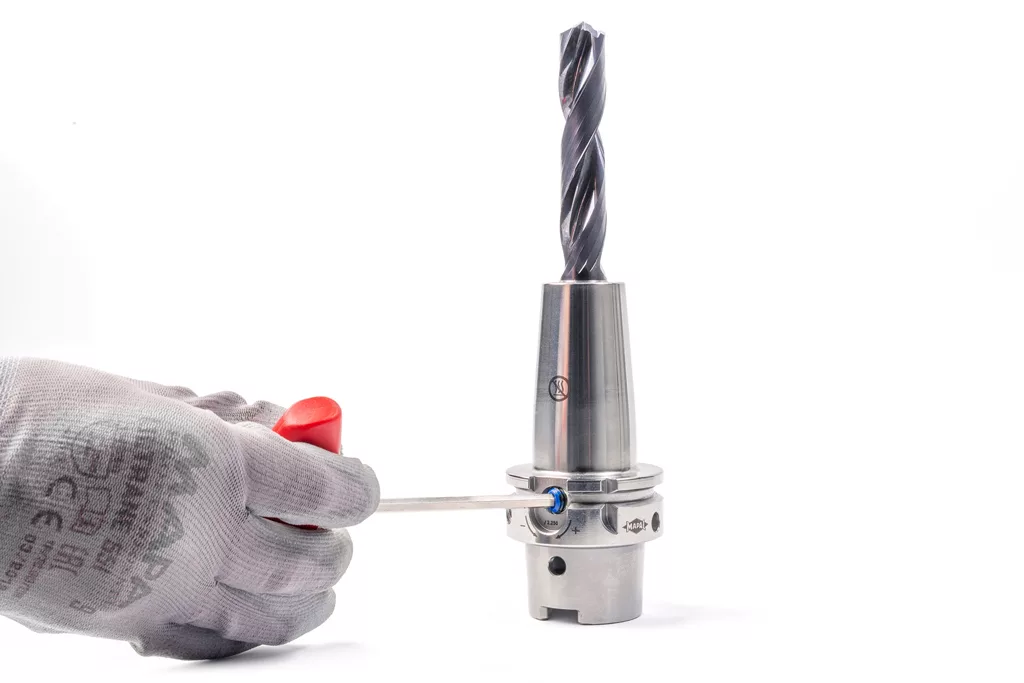
In addition to the tool life of a chuck and energy requirements of the device, time is also a factor when calculating return on investment. It takes at most two minutes to swap a hydraulic chuck, whereas six to eight minutes are needed for shrink chucks, depending on the size. If tools are changed often in manufacturing, this results in considerable labour costs. The space required in the tool-setting area for the shrink unit would also no longer be needed.
Simpler and safer
The social aspects of sustainability shed light on the topic from the user’s perspective most of all. A product where the performance is obvious to the naked eye is likely more agreeable to users than one with a rusted sleeve. When it comes to handling and safety, there are even more arguments for switching to the hydraulic clamping technology.
A shrink unit is not only cumbersome to handle but also a safety hazard. Almost every user has burned their finger once on a hot chuck during a busy workday. There is no such risk with hydraulic chucks. In general, they are very simple and straightforward to use – the tool only needs to be inserted and tightened. The workers benefit from processes that run more smoothly and require less reworking. The fact that a shrink chuck subject to material fatigue might be the cause for increasing tool wear or deteriorating surface quality is not always immediately obvious in practice.
The comparison result is clear: If you want to manufacture responsibly, then you should consider switching to hydraulic clamping technology. For new purchases, hydraulic chucks are the first choice from a sustainability perspective.
Manufacturing & Engineering Magazine | The Home of Manufacturing Industry News