As we advance towards electrification, particularly in sectors like automotive and aerospace, the need for rigorous standards to ensure safety and reliability has never been more critical. Yet in striving to meet these all-important standards, are we inadvertently stunting the ability of SMEs to rise to the challenge? These standards, defined by precise tolerances, exacting quality control, and complex regulatory requirements, create unique challenges for manufacturers looking to scale. Moving from prototype to mass production demands consistent performance across units, scalability, and speed to market, all without sacrificing quality.
Achieving these rigorous benchmarks is particularly challenging due to limited access to the advanced skills, facilities, and testing capabilities required, which are resources that are often challenging for SMEs. Representing 99% of the UK’s manufacturing sector, SMEs drive agility and specialisation across industries, and pricing them out of scale-up would be to our collective detriment. Ensuring that SMEs can access the expertise and facilities needed to navigate these regulatory spaces will be essential for scaling production. In industries driven by emerging technologies in Power Electronics, Machines, and Drives (PEMD), equipping SMEs with these resources would create a more inclusive, resilient manufacturing landscape, where innovation and compliance go hand in hand.
Understanding why certain standards are difficult to achieve at scale
In the journey from prototype to production, manufacturers face significant barriers. Key among them is the scarcity of skilled labour, the costs, uncertainty and risks associated with capital-intensive equipment, and the complexity of configuring and programming new manufacturing systems for repeatable results. In addition, in sectors like aerospace, where timelines are dictated by milestones tied to rounds of investment, scaling production is often pressured by both time and financial constraints.
The challenge is not only about getting technology on the production floor but ensuring that it’s operable by a workforce that may not yet possess the highly specialised skills needed. Equipment needs to be user-friendly for semi-skilled workers, yet robust and flexible enough to handle the complex specifications required by PEMD applications.
Bridging the gap between innovation and industrialisation
Driving the Electric Revolution Industrialisation Centres (DER-IC) Midlands, located at the University of Nottingham, is a leader in this critical phase of PEMD development. Through its Nottingham Drives Specialist Services (NDSS), the centre provides companies with access to flexible, high-end equipment that can perform a variety of manufacturing tasks. For example, NDSS’s advanced winding technologies enable the production of motors across a spectrum of sizes and specifications, from compact aerospace motors to high-speed powertrains for ground vehicles.
Our flexible equipment carries the risk for companies by eliminating the need for early, costly investments in specialised machinery. This flexibility is essential; the same DER-IC equipment can produce components for a range of applications, from a motor for a mobility scooter to a high-power density engine suitable for aerospace. By creating an environment that supports iteration and experimentation, DER-IC allows companies to prove their concepts affordably and then decide on investments in bespoke equipment optimised for volume production.
Proven success in scaling
The success of NDSS and DER-IC’s mission is evident in numerous collaborative projects. For instance, with Cummins, we developed a prototype for a traction e-drive motor, guiding the company through the entire design and testing process. The result was a scalable, validated design ready for production; a project that was underpinned by UKRI funding and exemplifies the DER-IC model of industry collaboration and academia to accelerate scale-up.
In another case, we worked alongside a start-up in aerospace electrification, where timing and performance were mission-critical due to the company’s reliance on investor milestones. By leveraging DER-IC’s high-fidelity testing capabilities, the start-up was able to prototype and validate its designs swiftly, meeting critical deadlines without the burden of investing in its testing infrastructure.
The role of rigorous testing in achieving manufacturability at scale
Rigorous testing is a cornerstone of the DER-IC methodology, with each component and system undergoing a sequence of tests to ensure real-world resilience. From individual wires and magnets to full motor assemblies, our testing processes reduce risk by ensuring that every system element behaves as expected in complex configurations. This approach allows clients to refine their designs and ultimately bring robust, reliable products to market faster and with fewer iterations.
At every stage, testing mitigates the risks involved in scaling up production. It guarantees that manufacturers achieve the level of repeatability needed for large-scale production. Our advanced testing equipment is also accessible to businesses across a range of industries, making high-level PEMD expertise widely available.
Industry collaboration will facilitate innovation
As DER-IC and NDSS continue to support UK manufacturing towards ambitious growth, it cannot be overstated how important industry collaboration is to bringing everyone on this journey. Our open-access model offers a valuable opportunity for manufacturers to take advantage of cutting-edge PEMD technologies, high-quality equipment, and expert guidance, helping the UK lead in the race toward a sustainable industrial future.
Collaboration between academia, science and industry needs to work hard to showcase the exciting opportunities and careers within the electrification industry to ensure we have the skills we need for the future. It’s an incredible time to explore this industry, where we’ll see some of the biggest advancements in our lifetime over the next few years.
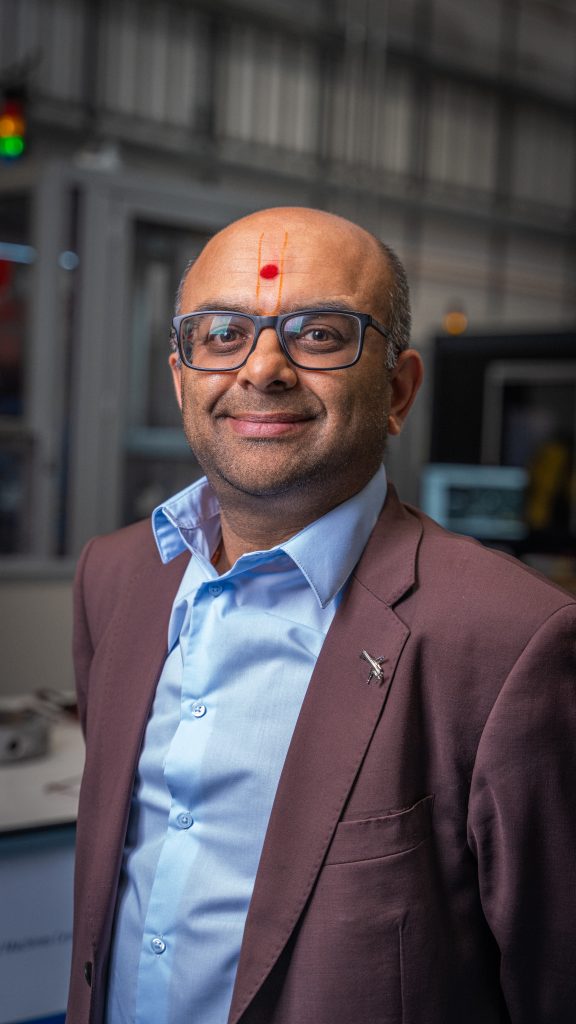
The path from prototype to production is complex, and something the DER-IC network is working hard to address the stringent standards needed for scale-up are not only accessible but practical, attainable, and positioned to the demands of an ambitious UK PEMD manufacturing sector.
Dr Hitendra Hirani, Sales Director and General Manager – Driving the Electric Revolution Industrialisation Centre – Midlands
Manufacturing & Engineering Magazine | The Home of Manufacturing Industry News