Aylesbury-based R&A Engineering won a contract in early 2023 to produce several hundred aluminium parts per month across six variants for assembly into sensors that optimise the orientation of wind turbines to maximise the power they generate. The job was tying up a pair of BT 40-taper VMCs (vertical machining centres) on the shop floor and impacting the subcontractor’s ability to take on other work. So the decision was taken to transfer production to a 30-taper, high-speed VMC, prompting an order to be placed for a Brother M200X3 with a 16,000 rpm spindle.
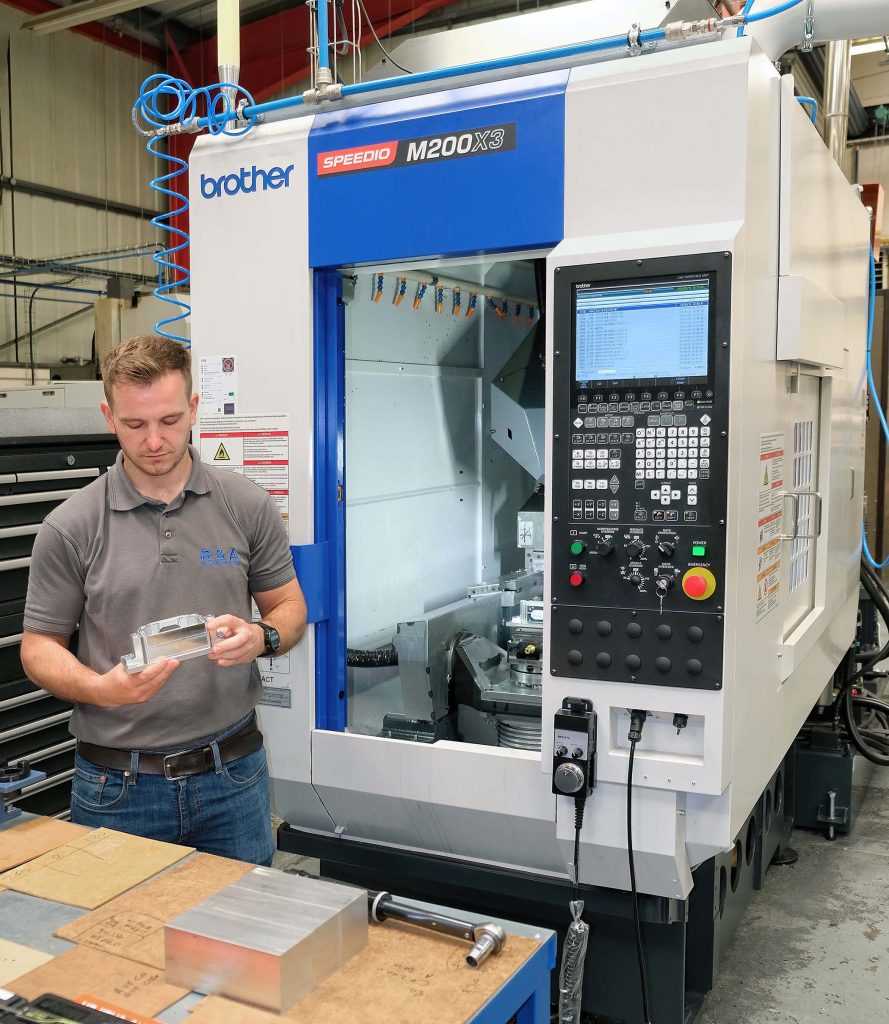
Delivered in August 2023 by the Japanese manufacturer’s sole agent in the UK and Ireland, Whitehouse Machine Tools, the Speedio M200X3 5-axis VMC has on average halved the time it takes to complete post-anodising milling, drilling and tapping operations on the six components. The machine is therefore able to perform the same work as the two VMCs used previously, which are now free to carry out other work.
Ed Piotrowski, operations manager at R&A said, “We approached a couple of 30-taper VMC suppliers but Whitehouse was the obvious choice, even though we have never bought a machine from them before.
“It is a family-run firm like ours and has a similar ethos as regards providing a high quality service, which was obvious when we visited their showroom in Kenilworth a couple of times for demonstrations.
“The Brother performs very well. Cycle times are now between one-and-a-half and four minutes, half of what they were before, and the ± 0.05 mm tolerance is held all day long without any problem. It is a really accurate machine.”
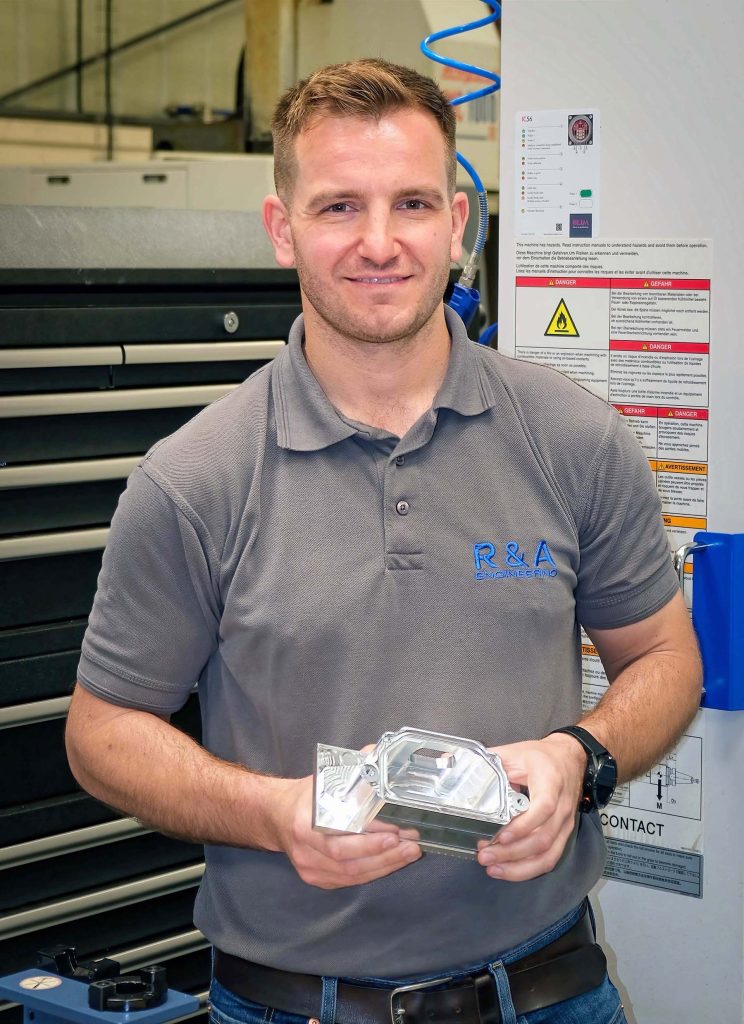
Established in 1985 by Ed’s parents, Richard and Alison, and currently employing 18 staff, R&A has grown by 50% since 2021. It has invested £800,000 in machine tools during the past couple of years and is looking to automate production wherever possible in both the turning and milling sections. The rationale is twofold: to be able to take on extra work without compromising existing, long-running contracts; and to be more cost-competitive on the world stage to accelerate the flow of work that is already being reshored from Asia and elsewhere in increasing quantities.
Ed has some interesting insights into why a subcontractor should invest in a 30-taper VMC, bearing in mind that an adage in contract manufacturing is that one never knows what work will come through the door next. The wider applicability of a 40-taper machine due to its size and power would therefore seem to make more sense.
The first advantage of a nimble milling machine with the smaller diameter tool interface is high speed production, which translates into greater profitability. Not only does the elevated spindle speed combined with up to 30 m/min cutting feed rate provide generous metal removal rates, but idle times are lower due to 50 m/min rapids in X, Y and Z and tool change in under one second.
A less well known benefit is the vastly lower power consumption of 30-taper machines. Ed advised that the M200X3 draws less than 10 kVA, versus typically 50 kVA for a 40-taper VMC or perhaps even more if it is an old machine. Energy bills are therefore lower and, as is the case at the Aylesbury facility, if a factory is close to its power supply limit the lower kVA rating is a godsend.
Reviewing the characteristics of the respective BT spindle machines, Ed observes that while power and rigidity are higher in a 40-taper VMC, modern, smaller-taper counterparts such as the Brother have a reasonably well specified spindle motor with good torque, even in the medium- to high-speed range. The drive motors are also consistent with robust machining and face-and-taper-contact tool retention assists further, as in R&A’s case.
He added, “Although machining of light alloys is really the province of this type of machine, using modern CAM software to create intelligent cycles involving light depths of cut and high-speed contouring means that tough and difficult-to-machine metals can also be tackled.”
The M200X3 has a further advantage for OEMs and subcontractors alike. It is equipped with a torque motor to drive the rotary table, allowing a component not only to be indexed, but also to be rotated at up to 2,000 rpm so it can be machined with a static turning tool in the spindle. Completing this second operation in-cycle without the need to re-fixture the part in a lathe simultaneously raises accuracy and productivity.
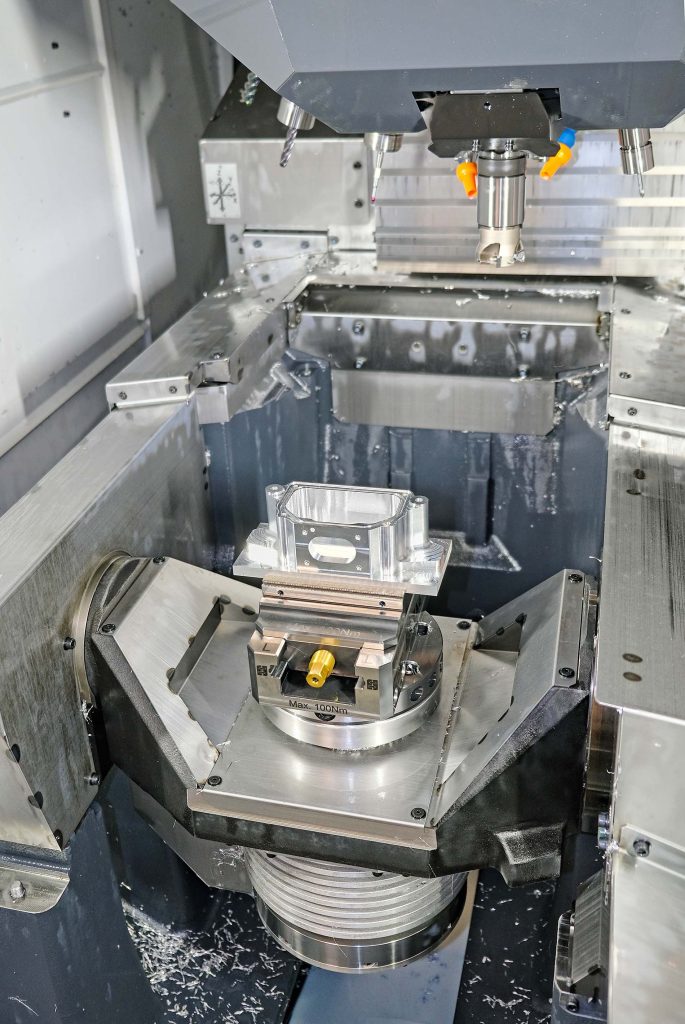
The mill-turn capacity in an impressively small footprint holds a lot of potential on the shop floor at R&A. Take, for example, the wind turbine sensor job for which the machine was purchased. Currently all six parts undergo turn-milling on a lathe before being sent out for anodising. The Brother is only required to remove the insulative anodic layer in certain areas to provide electrical conductivity. With the latter machine’s turning capability, all of the parts could be completely machined. Richard and Ed are actively considering this possibility, which would require automated component handling to be retrofitted.
In addition to seizing opportunities in the renewable energy sector, R&A is also taking advantage of growth in vehicle electrification. Two aluminium parts have already been produced on the Brother VMC for the latter sector. One is an EV (electric vehicle) engine terminal block, which is milled, drilled and tapped in a 20-minute cycle. Another engine part has been transferred to the M200X3 from a 40-taper machine, with the result that it is now machined in eight minutes rather than 12, again leading to more competitiveness, shorter lead times that impress customers and more overall capacity on the shop floor.
Ed is already planning the next job for the Brother. Water purification work accounts for about one-third of the subcontractor’s turnover and one of the parts machined from Ertacetal, an electrically conductive plastic, is currently turned and milled in four set-ups on three other machine tools. On the Brother it will come off complete after two set-ups.
Manufacturing & Engineering Magazine | The Home of Manufacturing Industry News