Forward-Looking Solutions Enhancing Efficiency and Environmental Compatibility
At Fakuma 2023, which takes place from 17 to 21 October in Friedrichshafen/Germany, Oerlikon HRSflow will focus on the use of hot runner technology for more sustainability and efficiency in injection moulding in Hall A1 at Stand 1215. The focus will be on applications such as thin-walled packaging, caps and closures as well as medical technology products and will also include the processing of biopolymers and compostable compounds. Beyond, the company is focusing on future-oriented automotive applications and the innovative FLEXflow system, specially developed for demanding injection moulding tasks.
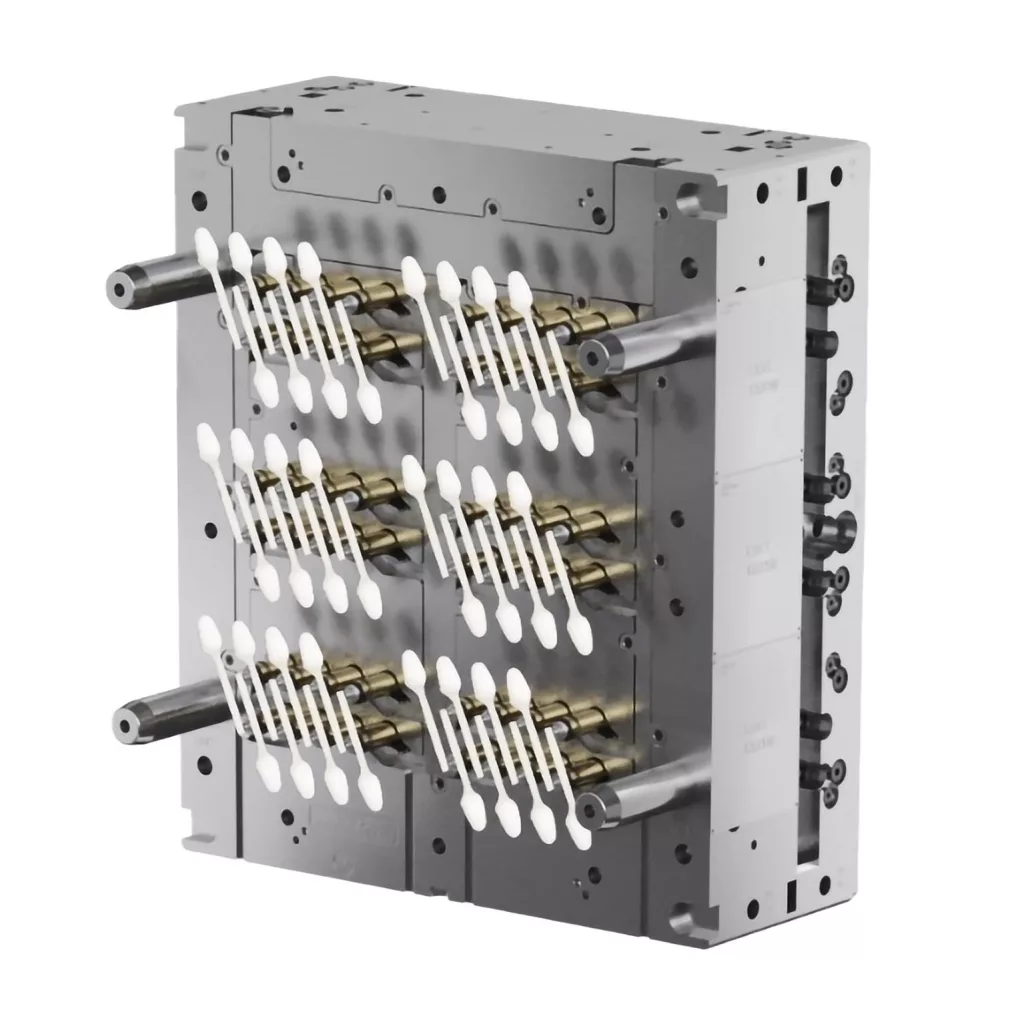
Stack mould for thin-walled packaging
Especially developed for time, material and energy saving injection moulding of thin-walled packaging, the Oerlikon HRSflow new stack mould system is dedicated to meet the latest requirements of the circular economy. Thanks to its innovative patent-pending design, thought to make the system extremely easy to assemble and maintain, it can be included in plug-and-play solutions that allow to avoid long and costly downtime. The stack principle also allows it to be installed in smaller injection moulding machines and enables flexible use for different applications.
The system, perfect for high filling pressures, is equipped with nozzles of the new Xd series, engineered for thin wall packaging applications and mounted on a 220 mm hot half plate. It is a prime solution for cost-efficient production, ensuring long term quality standards. A demo tool developed by Oerlikon HRSflow and equipped with this stack mould system offers customers the opportunity to test a wide range of polymers including bio-based and compostable materials.
To strengthen its expertise in thin-wall packaging, the company has also expanded its injection moulding machine park in its test lab with a new hybrid ENGEL e-Speed 280. With its high injection pressure (up to 2,600 bar) and high-speed injection screw (up to 1,400 mm/s), it is particularly suitable for processing R-PET, bio-based and compostable polymers, in compliance with the new EU Packaging and Packaging Waste Regulation (PPWR).
There it is also possible to define the optimal system configuration and to predict the part quality for special applications, using advanced hot runner systems mounted on dedicated prototype tools. Among the customer support services, plastic samples according to the weight, thickness and geometry of customer’s applications can be supplied for a preliminary analysis.
Multi-cavity systems for caps & closures
The multi-cavity line for low shot weights, recently named MULTIflow HRS, is suitable for packaging, caps and closure as well as medical applications, manufactured with engineering polymers for technical components. Some of the main benefits include fast cycle time, high production volume, processing of PCR compounds and biopolymers, quick colour change and an excellent finish of the molded parts.
At Fakuma, the expertise and knowhow of Oerlikon HRSflow will be highlighted through the display of the multi-cavity system designed for the production of 72 caps. Thanks to the new Vf nozzle series, it enables very short cycle times from 2.2 to 3.5 seconds while at the same time ensuring maximum process reliability thanks to excellent control and optimum balancing of the filling process. This technical solution, which is equally suitable for carbonated and non-carbonated beverages as well as for liquid and powdered concentrates, meets all the requirements of the new European single-use plastic directive, which makes tethered closures mandatory for all beverage containers up to three litres in capacity.
Specially developed for HDPE caps and closures, the Vf nozzles of the new multicavity line from Oerlikon HRSflow are suitable for part weights from 0.5 g to 8 g, and they stand for reliably consistent product quality, fast colour changes and system restarts. The special nozzle tip enables optimum control in the gate area and improves cycle time. Also, its separate replaceability makes maintenance particularly fast and cost-effective.
Rheologically optimized, hot runner geometries ensure significantly increased reactivity and thus effectiveness of the system. Special inserts minimize the time required for colour changes while keeping reject rates low, which contributes to the sustainability of production even with particularly critical colours.
A sustainable approach throughout the supply chain for eco-friendly applications
One of the primary goals of Oerlikon HRSflow is to develop hot runner systems that are specifically designed for sustainable applications and that contribute to greater efficiency in injection moulding. Here, the high temperature and shear sensitivity of bio-based and biodegradable polymers are the challenges when it comes to prevent material degradation while achieving short cycle times and good gate quality. In addition, hot runner systems for recycled compounds have to be designed to avoid any damage caused by possible impurities in the melt and to avoid any streaking or flow marks that could jeopardize the cosmetic and functional result of molding.
This is demonstrated by selected applications that Oerlikon HRSflow has realised in cooperation with customers.
Recycled plastic, new perspectives. The plastic pallet manufacturer, Ribawood, and Oerlikon HRSflow worked together to develop a hot runner solution that produces reusable and 100% recyclable pallets.
Transporting and storing products on modern plastic pallets is becoming popular in a sector traditionally dominated by wooden solutions. Plastic pallets are safer, very durable and recyclable. A quality in full compliance with future needs which are progressively connected to Circular Economy. As sustainability remains a priority, challenges for the injection molding industry are increasing.
Ribawood, the plastic pallet manufacturer, partnered with Oerlikon HRSflow to develop a hot runner solution able to produce lightweight pallets. The product is composed of fully recycled material. Quality issues swayed from surface defects to more serious issues that could affect the safety and function of the finished product, as well as the performance of the hot runner system. The main challenge was primarily connected with clog problems of the hot runner channels due to the foreign particles usually present in the recycled material.
- Application field: Logistics & Environmental
- Part name: Pallet
- Nominal weight: 6900 g
- Nominal thickness: 3 mm
- Molding material: HDPE regrinding
- Hot runner system: 8 drop system: Wa Series Oerlikon HRSflow
- Injection type: Conical Valve Gate
Rheological analysis
The first step was understanding the behaviour of the polymer within the mold cavity. The complexity of processing recycled material is usually related to foreign particles, leading to obstructions in the hot runner channels. The use of software to conduct a rheological analysis helped to define optimal injection pressure and speed based on the special material features.
Hot runner system
The technological solution was a hydraulic 8-drop hot runner system equipped with conical valve gate (Wa nozzle series) from Oerlikon HRSflow. Special attention was given to the gate configuration, due to a 14 mm diameter and a hot runner bore diameter of 32 mm. Any issues related to channel clogs would be avoided. In addition, the gentle injection pressure combined with low speed allowed for better control of the melt flow. This prevents any streaking or flow marks that could jeopardize the cosmetic and functional result. Continuing, the lower injection pressure allowed for the use of LPIM (low pressure injection molding) technology, maximizing production efficiency. With this design approach, system maintenance can be significantly reduced, avoiding long and costly downtime.
Oerlikon HRSflow: José Moreno, General Manager of Spain states, “developing and producing high-performance hot runner systems for plastic injection molding is a complex process. It requires high expertise and continuous desire to face new challenges. The project carried out together with Ribawood is a clear example of great collaboration. Both parties put into play their own knowledge to get the best result: a 100% reusable and recyclable pallet which combines a strong attention to sustainability with a high structural result”.
The Finished Product
Ribawood is an international company located in Zaragoza, that began operations in 1975. Business focuses on the transformation of plastics and extrusion of Woodstock® sheets, a plastic designed for the automotive sector that contains a derivative of wood. In the early 2000s, it became to diversify the production in the packaging sector by injecting pallets, boxes and containers of recycled plastic.
Pioneers in the recycling of their own waste products, with a production capacity of 2.5 million pallets per year, Ribawood can recycle their own pallets at end of their life. The growing demand for this product in the world of logistics is due to high durability and minimal impact to the environment, enabling companies to comply with their zero-waste commitments.
Ribawood needed a business partner that could operate within their versatile manufacturing process. Several tests revealed that the balanced hot runner solution from Oerlikon HRSflow would ensure the high structural result of the entire part. There would also be no internal stress, despite working with 100% recycled material.
Sustainable box : FLEXflow technology for R-PET materials
The system for injection molding a sustainable box, developed by Oerlikon HRSflow in collaboration with Pezzutti for the beverage and household sectors, features an end ring configuration optimised for processing R-PET material. The system is a FLEXflow stack family mold, with 8 drops Ga plus 4 drops Aa, where the 8-drop Ga-type cylindrical valve gate part is studied to ensure the aesthetic quality for lids and boxes, thanks to precise cooling and gate area design.
The wall thickness of the parts is 2.5 mm, the box weight is 870 gr. corresponding to a material input of 11 recycled PET disposable bottles. Highlights of this new sustainable application include optimal part balance and uniform cooling to minimise part warpage, resulting in a shorter cycle time.
Eco-friendly set for household use: tray, glass and lid
Also designed for processing R-PET are the hot runner systems developed for Guzzini to produce an environmentally friendly set, that includes a tray, a glass and a lid for household use. Oerlikon HRSflow’s hot runner systems selected for this purpose are equipped with Gs-My-Ms series nozzles and cylindrical valve gate, ensuring high aesthetic quality and low part distortion. With a wall thickness of 3 mm, the tray weighs 450 g, the glass weighs 108 g, the lid weighs 80g, corresponding respectively to a material input of 13.5, 3.3 and 2.4 recycled PET disposable bottles.
100% bio-sourced spoons
PLA is the material of choice for a fully bio-based spoon used in the food and beverage sector. It weighs 1.32 g with a part thickness of only 0.7 mm. The hot runner system for this application includes 48 drops with Tp series nozzles and cylindrical valve gate. Thanks to the use of a bio-based material, this application is perfectly adapted to the requirements of the circular economy. This was made possible by optimising the channel dimensions for shear rate control to avoid material degradation during high-speed injection in the multicavity system, which was designed for maximum production efficiency.
FLEXflow for demanding automotive injection moulding tasks
As a sought-after solution for demanding injection moulding tasks, Oerlikon HRSflow is presenting its FLEXflow technology, which combines a servo-driven valve gate system with a flexibly programmable control system. This configuration enables precise and independent adjustment of stroke and force in the positioning of each individual nozzle during the opening and closing phases of cascading injection processes. Potential applications include future trends such as back injection of films, smart automotive surfaces and lighting.
An example of this, presented at Fakuma, is a smart 2K rear panel consisting of a PC+ABS frame that is overmoulded with PMMA or alternatively PC. A hydraulic 2-drop system from Oerlikon HRSflow is used in the first injection phase, and a single nozzle from the Ga series in the second phase. Finally, the part is decorated with a capacitive and aesthetic film directly in the mould. The realisation of these complex requirements demanded exact rheological calculations. Oerlikon HRSflow’s project partners were Schöfer, LEONHARD KURZ and Röhm.
FLEXflow is also suitable for family moulds, which can offer significant cost savings compared to conventional sequential injection. A perfect example is the use of an 8-drop system for a car door panel. Equipped with a Ma series conical valve gate, three different cavities are filled simultaneously. Thanks to extensive flow simulations carried out at Oerlikon HRSflow, the system is perfectly balanced and enables high surface quality.
At Booth 7303, Hall A7, KraussMaffei will show the manufacturing of an automotive interior storage tray made of glass fibre-reinforced PP, realised together with Wirth. The mold is equipped with an Oerlikon HRSflow hot runner system especially developed to process reinforced materials.
About Oerlikon Polymer Processing Solutions Division
Oerlikon is a leading provider of comprehensive polymer processing plant solutions and high-precision flow control component equipment. The division provides polycondensation and extrusion lines, manmade fiber filament spinning solutions, texturing machines, BCF and staple fiber lines as well as nonwoven production systems. It also develops and produces advanced and innovative hot runner systems and multi-cavity solutions for the injection molding industry. Its hot runner solutions serve business sectors, including automotive, logistics, environmental, industrial applications, consumer goods, beauty and personal care and medical. Moreover, Oerlikon offers customized gear metering pumps for the textile, automotive, chemical, dyes and lacquers industries. Its engineering competence leads to sustainable and energy-efficient solutions for the entire polymer processing value chain with a circular economy approach.
Oerlikon Polymer Processing Solutions Division serves customers through its technology brands – Oerlikon Barmag, Oerlikon Neumag, Oerlikon Nonwoven and Oerlikon HRSflow – in around 120 countries with production, sales, distribution and service organizations.
The division is part of the publicly listed Oerlikon Group, headquartered in Switzerland, which has more than 12 100 employees and generated CHF 2.9 billion sales in 2022.
For further information: www.hrsflow.com
Manufacturing & Engineering Magazine | The Home of Manufacturing Industry News