Testing and de-risking investments in new technology for transport : Jon King, DER-IC Midlands Centre Lead
The UK transport sector is in the middle of a revolution. At the start of this year, the UK government made its zero emission vehicle (ZEV) targets law, meaning that 80% of new cars and 70% of new vans sold in Great Britain need to be zero emission by 2030, increasing to 100% by 2035. A goal described by Ministers as ‘the most ambitious regulatory framework for the switch to electric vehicles of any country in the world’.
There has been a positive response to this shift away from Internal Combustion Engines (ICE) from industry and consumers, with data showing the market share of electric vehicles in the UK was an impressive 44.5% at the end of December 2023.
The government’s bold targets go far beyond a focus on cars and vans, however. In its Net Zero Strategy, Whitehall outlines its ambitions to deliver a net zero rail network by 2050, develop a net zero domestic marine sector, deploy zero emission buses and the corresponding infrastructure, and lead the way when it comes to developing sustainable aviation fuels (SAF). No matter what happens in politics in the coming year, there’s a strong appetite for change across parties and the public alike.
But one of the questions manufacturers working in the transport sector are grappling with is, without significantly large sums of upfront investment, how do they make this transition a reality?
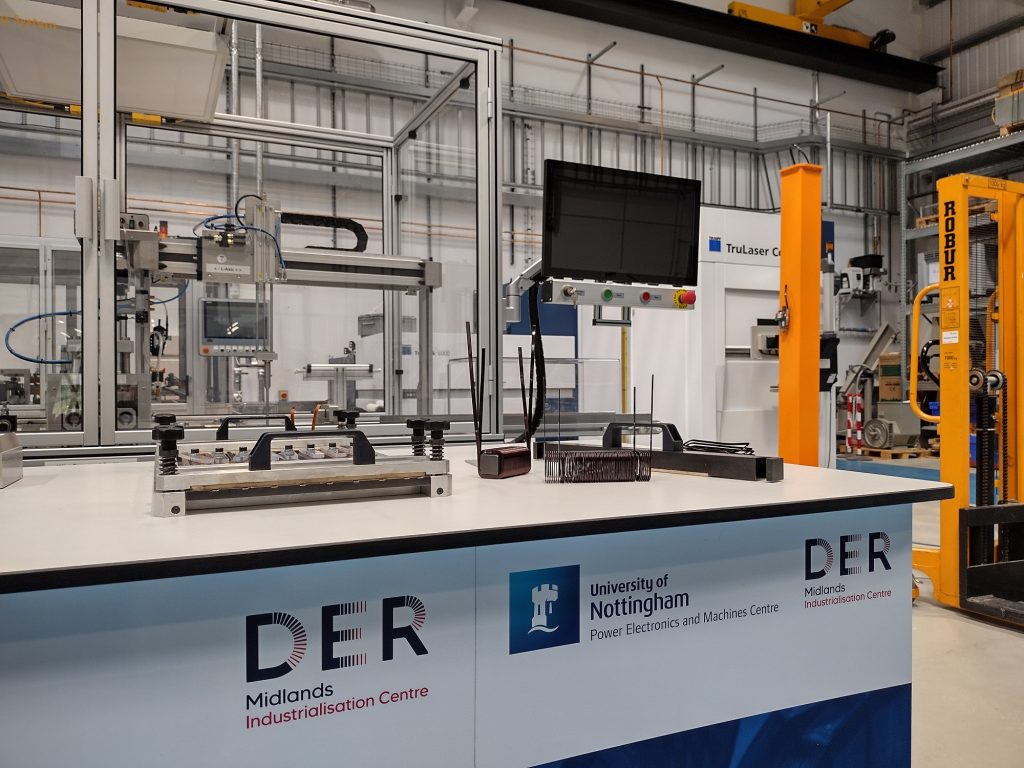
Power Electronics, Machines and Drives (PEMD): A key part of the puzzle
One supply chain that is essential to the electrification of our transport systems is Power Electronics, Machines and Drives (PEMD). PEMD technology enables the control and delivery of electrical power across a range of applications but crucially in transport electric motors.
The UK PEMD sector and its outputs will be relied upon heavily to bring about this change. However, to fulfil the ambitions for low carbon transport and be internationally competitive, the sector needs to evolve and innovate; something with associated cost and risk implications, as well as a scarcity of skilled engineers and technicians. In addition, many companies are looking to pivot towards electrification technologies to sustain their business and take advantage of these emerging opportunities. There is a need for many manufacturers to access expertise, facilities or equipment to create the space for innovation. Many manufacturers also face the challenge of securing external investment to develop, scale and commercialise new technologies; to do this, they need to test and validate their product and process capabilities first.
Fortunately, the UK enjoys a robust research and development (R&D) landscape through its world-leading universities and Research and Technology Organisations (RTOs) such as the Catapults. This excellence in academic research holds real potential for manufacturers and SMEs seeking to innovate and develop new technology and the Catapults can support development and scale-up into production. The Driving the Electric Revolution Industrialisation Centres (DER-IC) network, of which both universities and Catapults are part, occupies a central position in this university and RTO ecosystem for the PEMD sector. The DER-IC network has been funded by Innovate UK through the £80m Driving the Electric Revolution programme, showing the government’s long-term support for the PEMD sector. Power electronics, in particular, are an important component for the delivery of the UK’s National Semiconductor Strategy which aims to improve supply chain resilience.
Combine subject matter expertise with the correct equipment and facilities and you have a winning recipe for the PEMD manufacturing supply chain to innovate, commercialise and scale-up operations, which will ultimately lead to market transformation and growth. This is the premise of DER-IC which offers access to national centres with Innovate UK-funded equipment, and the opportunity to collaborate with its partner network made up of over 30 PEMD focused universities and RTOs. DER-IC can support manufacturers to develop and test prototypes, at a lower risk and cost than the more challenging self-funded route. This can happen through commercial projects, where IP is fully protected, or through collaborative R&D projects, which usually have several industry partners working together to develop and establish full supply chain capability.
Testing and de-risking investments: A collaborative effort
One of the reasons collaborations are crucial in this exercise is because bringing together the collective expertise of partners accelerates the process of de-risking and validating innovations. There are exciting new partnerships emerging across the UK PEMD ecosystem where breakthroughs in technology development are creating new commercial opportunities.
One such project saw six stakeholders including WMG, Ricardo, Aspire Engineering, Brandauer, Phoenix Scientific Industries and Global Technologies Racing come together for the UK-Alumotor project. UK-Alumotor sought to develop preferred manufacturing processes which are suitable for volume production of a patented motor design from the UK supply chain, with the overarching aim of developing the next generation of sustainable electric motors. The project also refined the design to meet the future requirements of its UK and international stakeholders. Meeting the requirements of international suppliers frequently leads to further testing and validation due to the many standards and certifications different markets mandate.
The UK-Alumotor project outcomes aim to include a more affordable, environmentally sustainable design which displaces the need for scarce material resources, resulting in a greener and more economical solution to support the mass adoption of electrification.
The right tools for the job
A crucial part of the testing and de-risking stage of developing new technology for transport is having the right equipment and facilities, as well as the skills and ability to operate them. With transport being such a broad sector, this means manufacturers need different equipment sets to suit the different topologies and requirements.
For example, the Winding Centre of Excellence at WMG at the University of Warwick is focused on high-volume winding technologies aimed at the automotive sector, whereas the seemingly similar facility at the University of Nottingham is focused on high-frequency applications for high-end automotive and aerospace applications. The testing of complete drive systems is demonstrated at DER-IC Scotland which has specialist equipment designed to test powertrains for aviation, maritime, rail and HGV applications. Hosted at the University of Strathclyde’s Power Networks Demonstration Centre (PNDC), these facilities provide first-of-their-kind, platform-level, route-to-market Power Train Test Bed (PTTB) for hydrogen fuel cell and battery electric drive trains.
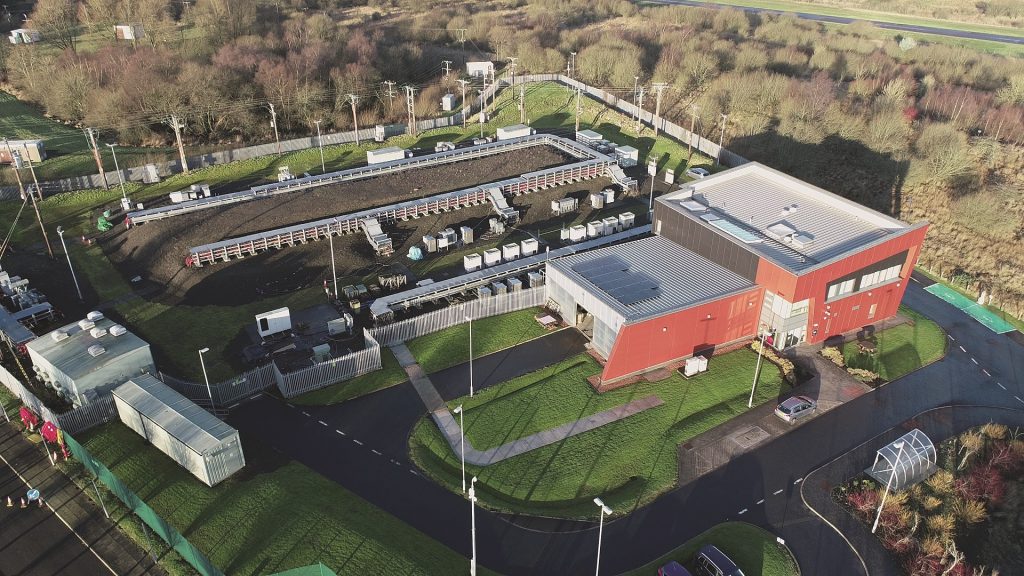
From product to assembly line
Beyond testing and de-risking the products themselves, manufacturers also need to test and de-risk the manufacturing processes they will use to create products, a journey that most manufacturers are now looking to automate. DER-IC North East, part of Newcastle University and located near the International Advanced Manufacturing Park in Sunderland, is equipped for manufacturers to trial different manufacturing processes with Power Electronics Packaging, and Electric Drives and Electrical Machines assembly lines.
Similarly, the University of Warwick hosts a power electronics module assembly, reliability and failure analysis facility for high power Wide-bandgap semiconductor (WBG) devices.
Partnership working opens doors to new opportunities
When a collaborative project engages with our facilities at DER-IC we frequently find it opens doors to other opportunities. This was the result of the APC funded @FutureBev project, which partnered with us at the University of Warwick to test a new power inverter in the power electronics module assembly, reliability and failure analysis facility. This equipment was commissioned just in time to support the @FutureBev project, which was completed this April, and involved six partners including the DER-IC teams at the University of Warwick and CSA Catapult.
The inverter testing project marked a new chapter for this supply chain. Car manufacturers have previously been testing inverters with motors in high-cost dynamometer facilities that needed to contain high-speed equipment failures. The DER-IC facility, created with input from academic specialists and using a Hardware in Loop approach, is smaller, less costly, easier to access, and can be applied in other sectors. The @FutureBev project used this new equipment to test components in isolation, i.e. the inverter, without the motor itself.
All the partners have benefitted from this project, and one has been able to enter the automotive supply chain as a result, gaining new customers and investing in new manufacturing capacity.
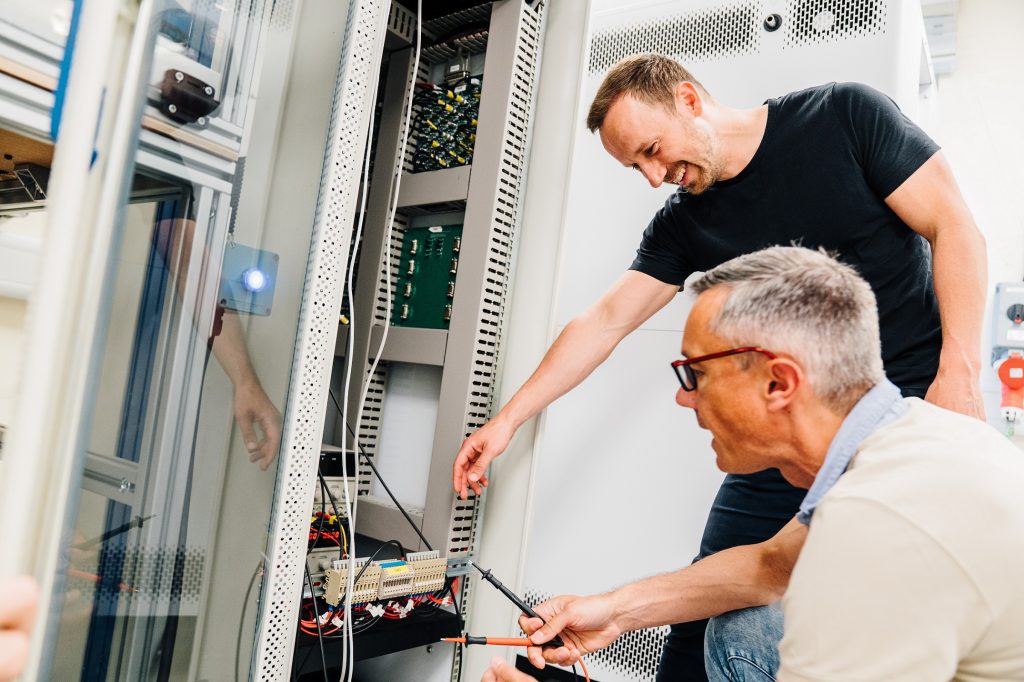
Materials and components: The missing parts of the puzzle
The final parts of this package of solutions focus on the materials and components end of the value chain. On the power electronics side, the Compound Semiconductor Applications Catapult (CSAC) has installed ceramic 3D printing for device packaging, backed up by 3D metal printing facilities and metrology and processing tools. Meanwhile at Swansea University there is a £5m wide band gap power electronics component industrial-scale pilot line. At the University of Birmingham there is a large scale recycling and production facility for rare earth permanent magnets to support the recovery and recycling of sintered magnets; critical rare earth elements which are essential for the electrification journey.
The facilities DER-IC provides in its open-access centres mean stakeholders from across the PEMD supply chain developing components for future transport systems can test, validate and de-risk together.
DER-IC can support manufacturers to de-risk new product development and introduction with:
- Prototype manufacture and scale-up support
- Manufacturing process development and optimisation
- Product and manufacturing process equipment design
DER-IC can support manufacturers to prove production readiness with:
- In-process and end-of-line test and validation
- Material and component characterisation
If you’re interested in working together, please contact Jon King, DER-IC Midlands Centre Lead at midlands@der-ic.org.uk or call 07802 476479 or find out more at the DER-IC website here.
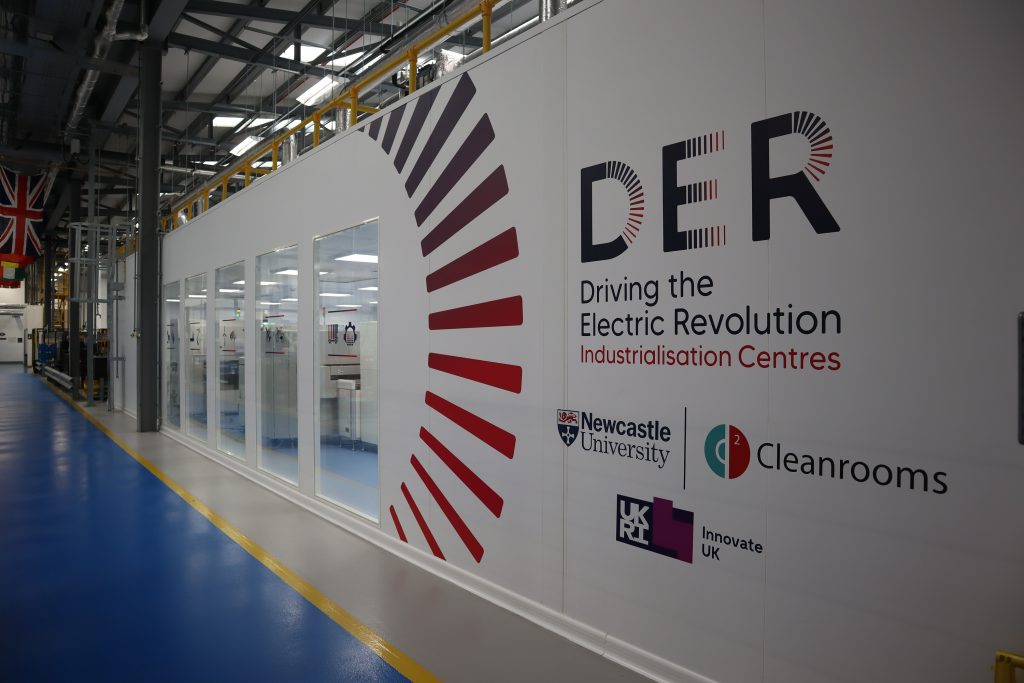
Manufacturing & Engineering Magazine | The Home of Manufacturing Industry News