The automotive industry is complex. Alongside pressures to improve the sustainability of production processes and the vehicles rolling off the line, carmakers are also looking to push the limits of performance and aesthetics. Innovative approaches, such as Physical Vapour Deposition (PVD) coatings, can make this possible, particularly when adopted by partners within the supply chain, as Dr Yuen-Ling Kong of Vestatec discusses.
Traditional methods of metal coating, such as painting and electroplating, have become less favourable in recent years due to potentially harmful waste products and questions around safety. Hexavalent chrome, for example, is banned under the EU’s 2017 REACH directive due to its high toxicity, which makes it harmful to human health as well as the process resulting in hazardous waste material.
To adapt and respond to a shifting industry landscape, while focussing on performance, innovation and sustainability, carmakers must look to new techniques, such as PVD coatings. This journey starts with suppliers within the existing chain, who can support the adoption of new technologies cost effectively, while further strengthening the supply chain and sharing of expertise.
How do PVD coatings work?
PVD is an advanced technique used in the process of metal finishing to achieve a durable, high-quality and aesthetically pleasing coating for decorative metal components. Presenting an alternative to traditional processes, PVD coating delivers a superior finish, which maintains the substrate surface finish – for example, polished, brushed grit and bead blast surface finishes.
At the heart of the process is a cathodic arc PVD machine which houses a vacuum chamber. It is here where an electrical arc is created which vaporises a conductive metal target source (known as a cathode target). This vaporised metal is combined with a unique combination of gases to create a compound, which is deposited atom by atom onto the substrate, forming a highly adhesive, strong and thin coating.
Once the coating is applied, testing is carried out on every batch to ensure consistency. An X-ray fluorescent (XRF) machine is used to determine the composition and thickness of the applied coating, while a spectrophotometer is used to measure its colour through lighting, chroma and hue.
The benefits of PVD coatings
At a production level, the process of PVD delivers a host of benefits. With a high deposition rate, manufacturers can benefit from more time-efficient production and improved cost efficiency. Alongside this, the specialist process results in a highly uniform coating, creating greater consistency across batches.
Once coated, components will begin to add value to the final vehicle. Despite measuring just one micron thick (25 times thinner than a human hair), the coating delivers high hardness and great scratch resistance. This improves long-term durability and enables PVD coated components to stand up to the demands of everyday use.
Additionally, the thin coating achieved with the PVD process heightens aesthetic appeal. By allowing the texture of the substrate metal to remain visible, the process enables carmakers to showcase the design detail of individual components. A range of colours – including black, graphite, blue, rose gold, gold, silver and nickel – can also be achieved consistently and repeatably, giving carmakers greater design freedom and the ability to appeal to a broader customer base.
Alongside strengthening product development and innovation with PVD coatings, the process can also enhance sustainability efforts. With increased pressures on manufacturers to reduce the environmental impact of their processes and those of the wider supply chain, this is a significant factor for carmakers. Unlike alternative methods, PVD coatings do not use substances which are hazardous to humans and there are no harmful waste products.
Investing in sustainable metal forming and finishing
To support carmakers in leveraging the full potential of PVD coatings, Vestatec has made a significant investment to bring PVD coatings in-house. In practice, this strengthens the supply chain while enabling manufacturers to accelerate innovation through supplier expertise.
With the full spectrum of expertise sitting with one supplier, from metal forming through to coating and component assembly, carmakers can push the boundaries of what is possible and make their design visions a reality. The specialist knowledge of PVD experts ensures a complete understanding of the tolerances of different metals, the properties of substrates and how everything works together. In practice, this means that manufacturer-specific requirements can be achieved, without the need for costly and time-consuming trial and error.
As a trusted supplier of formed metal components, Vestatec has been supporting customers every step of the way for more than 40 years, from concept design through to production. The addition of PVD coatings means that metal components can now be designed, formed, coated and assembled under one roof, streamlining production and reducing complexity for the world’s leading car brands.
To find out how Vestatec’s PVD coating capability could transform your metal forming and coating needs, visit www.vestatec.co.uk
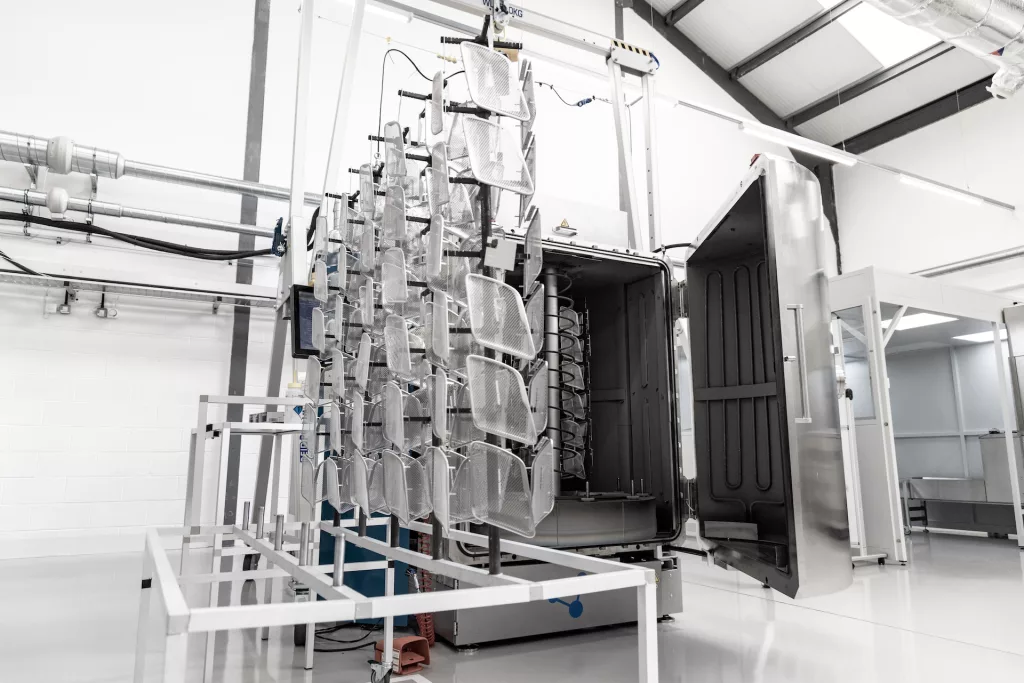
Manufacturing & Engineering Magazine | The Home of Manufacturing Industry News