~High process reliability with the OptiMill-Composite-Speed-Plus from MAPAL~
Improved clamping technology for large carbon-fibre parts enables the aerospace industry to machine more quickly. MAPAL supports this development with new tools. With its diamond coating and optimised geometry, the OptiMill-Composite-Speed-Plus guarantees process reliability.
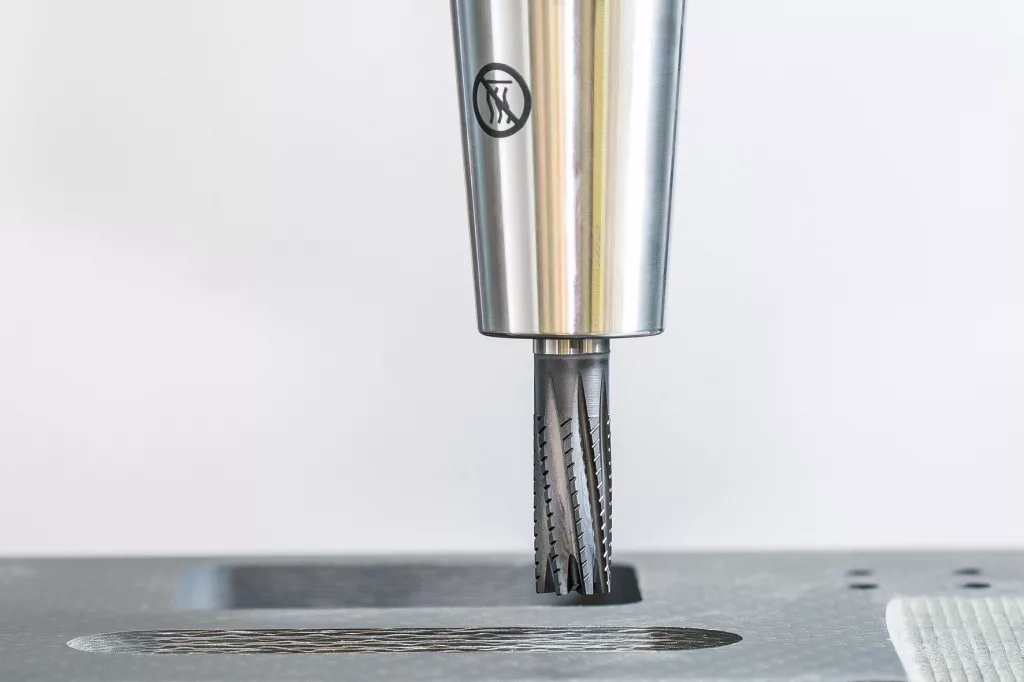
diamond coating and optimised geometry.
The aerospace industry is reluctant to change functioning processes that have already been audited due to the large effort involved. However, growing cost pressures are also forcing this sector to make its production as efficient as possible. Aircraft manufacturers have so far identified the clamping technology as an obstacle on the path to higher performance. Large carbon-fibre parts are usually fixed using vacuum clamping technology. The limited holding forces of the suction cups require relatively low cutting speeds in order to prevent rising vibration. This can lead to a loss of quality and deviations in shape and position tolerances.
New clamping technologies now enable manufacturers to increase the cutting values. But with this came a new problem: under the changed process conditions, there was an increased risk of breakage due to the increased load on milling cutters that had previously worked perfectly. “Even very large manufacturers were affected by tool breakages after using the tools to their limits”, explains Tim Rohmer, Product Manager for solid carbide milling tools at MAPAL. The tool manufacturer saw a need to act and developed the OptiMill-Composite-Speed-Plus as a response to market demands.
Large core, little chip space
In order to enhance the flexural strength, MAPAL increased the core diameter of its solid carbide shoulder milling cutter. Although this is at the expense of chip space, it does not have any negative effects because CFRP machining does not produce chips, but a fine dust. During tool tests with differently dimensioned diameters, no differences were found in terms of removing dust and process heat. MAPAL noticeably increases the flexural strength with the larger core diameter.
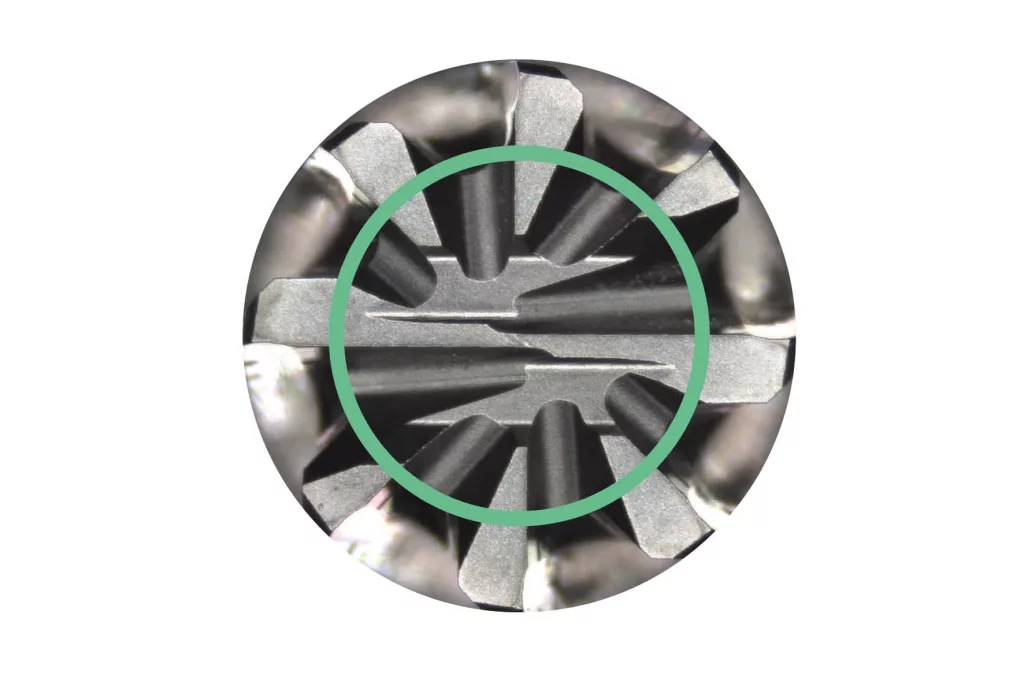
The requirements for the groove profile also differ from the machining of metal, where feed, infeed depth and cutting width influence the chip thickness. Since the rake angle for CFRP is only slightly engaged due to a low feed per tooth, MAPAL has designed the cutting wedge for maximum stability.
The new OptiMill-Composite-Speed-Plus also has an optimised envelope contour to reduce leverage forces and thus for increased fracture resistance. It works well in practice, as Rohmer explains: “Typical parts for aviation consist of stacks, i.e. composite panels, with five to 15 mm usually being machined. Shorter tools are perfectly adequate for this.” While the predecessor tools were still longer than specified in DIN6527, the new tool series largely complies with the standard. MAPAL provides the tools with diameters of 4 to 20 mm.
Even diamond layer
The OptiMill-Composite-Speed-Plus also ensures high tool lives for machining abrasive carbon fibres with an innovative diamond coating. The uniform layer thickness distribution and the high repeatability with which MAPAL applies the diamond in the CVD process are exceptional. Conventional coating technologies often produce irregular layers that are thicker at the tip than further down on the cutting edge. This process ensures different edge rounding and thus fluctuating cutting pressure and wear and tear.
The homogeneous layer thickness over the cutting edge length contributes to process reliability. This enables consistent performance regardless of which part of the cutting edge is involved. This means that the tools can also be used for circumferential machining of a stack, regardless of height: users sometimes use the milling cutter until the end of wear and tear, then readjust it and continue working with a fresh part of the cutting edge. The shoulder milling cutter is suitable for a wide range of applications. In addition to circumferential machining, it is also used to produce slots, edges and pockets.
Perfect cutting quality is very important in the aviation industry. Once the fibres are no longer neatly separated and the part thus no longer achieves the desired quality, the tools are replaced, even if they only appear slightly worn. The OptiMill-Composite-Speed-Plus achieves its excellent cutting quality thanks to its specially arranged “fibre catchers” on the cutting edges, which cause a double compression and thus separate the fibre protrusions on the workpieces extremely precisely. The double compression is additionally created by the spiralisation of the tool.
Pull or push: improvements of up to 30 percent
One aspect of CFRP machining is that the tools available today produce different machining qualities on the workpieces. The user must decide which quality requirements are placed on the part according to the existing material composite and therefore make the ideal tool selection. It is often connection points for which particularly neat edges are required. MAPAL provides two different variants of its milling cutters. The right-hand spiral model produces a pulling effect and thus axial tensile forces, while the left-hand spiral variant has a pushing effect and thus forms compressive forces in the axial direction. The fibre catchers counteract the force created by the respective spiralisation.
The previous model had a third, neutral variant. With further development, this variant is no longer required as the new tools reduce the axial forces by up to 40 percent. As such, the two versions of the new product also assume all tasks for which the neutral variant was previously used. In terms of tool life, quiet running, productivity and cutting quality, the new tools are up to 30 percent better than their predecessors.
Whilst the aviation industry is still recovering from the coronavirus slump, the use of CFRP is growing rapidly in other areas. In addition to automotive engineering and racing, the focus here is shifting to the consumer sector. Manufacturers of sports equipment such as bicycles, skis, snowboards or fishing rods increasingly use the modern material.
With its sharp cutting edges, the OptiMill-Composite-Speed-Plus can also be used to machine thermoplastics and thermosets. As these plastics are not abrasive, coating is not required here and sharp cutting edges are used. The uncoated milling tools replace the previous router tools as they are far superior, especially in terms of cutting quality. MAPAL also recommends the uncoated tools for machining fibreglass materials.
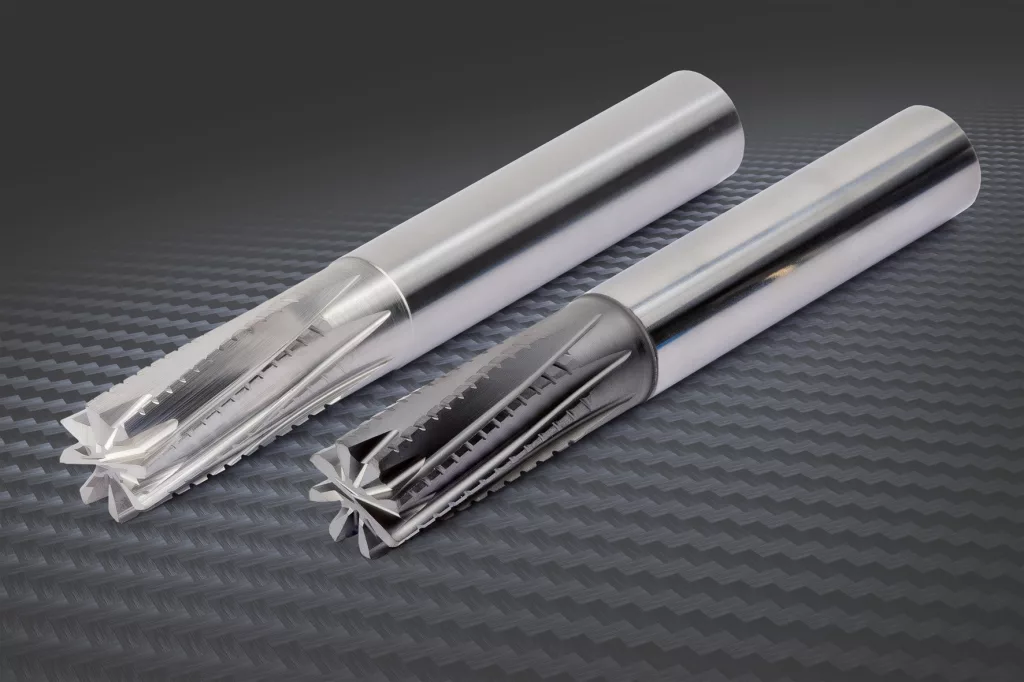
Manufacturing & Engineering Magazine | The Home of Manufacturing Industry News