In this article split over three parts, Dr Richard Brown of Finch Consulting looks at effective lighting at work and how it enables safe working. This third part discusses sockets for temporary lighting, how providing lighting can lead to accidents and ensuring the correct type and positioning of lighting.
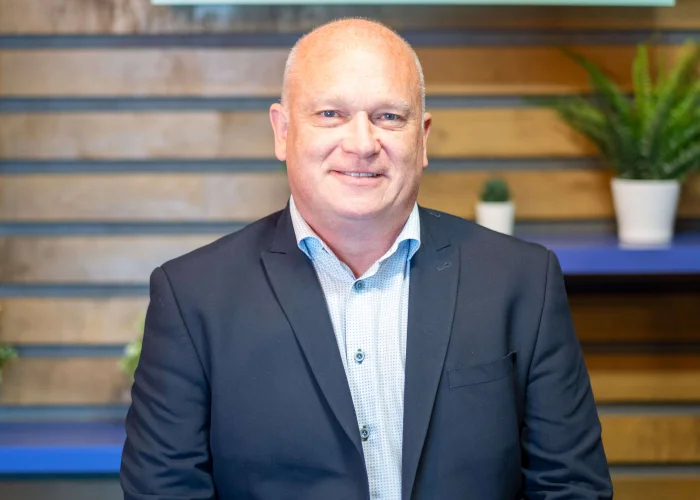
Have enough sockets for temporary lighting.
I have endured the unfortunate experience of being within a large coal boiler furnace on an outage (a maintenance shut down in the power industry) when without warning all the temporary furnace lighting failed. The furnace was decked out with scaffolding, and most workers held on to a handrail and waited for the lighting to be remedied. As is usual in these circumstances, the language was rather choice and voluminous! After the many shouts the lighting returned to its previous state after what was probably a minute or so (but perhaps in absolute darkness seemed more like hours).
After an investigation it was discovered that a welder needed to grind out a weld and couldn’t find a free power socket. Rather than spend time arranging for this to occur, he simply unplugged the nearest plug to him in a splitter box and carried on with his work. As part of the investigation, it was discovered that there were generally insufficient power sockets for the trades at each boiler level. Due to slow reactions to complaints, workers grew tired of constantly asking for further sockets and resorted to their own means of finding a power source.
In this circumstance, I was lucky to have a personal light on my hard hat, as did many of the contractors. Better provision of power sockets and mandatory personal lighting to enter the boiler were a result of the investigation.
Providing lighting can lead to other accident types
Temporary lighting is often strung at low level, across the floor, over motors, pumps etc. Consequently, poorly designed temporary lighting often leads to slip and trip type of accidents and incidents. Additionally, lighting can be placed on improper surfaces (e.g., hot) which can affect the lighting cabling. How often in industry do we see extension cables, lighting, sockets surrounded or in pools of water? In my experience quite often.
I have always found the best approach to temporary lighting to be to plan it in like any other task. On large power station outages for example consultation with the scaffolders has allowed the temporary lighting to be attached to set points above head level, to prevent trip hazards and the damage of cabling at low level. Furthermore, the minimisation of electrically related accidents can be achieved.
This approach in conjunction with the scaffolders also allows the proper derigging of scaffolding and lighting, without overly affecting the lighting provision. Often without planning high mounted lighting, once the scaffolding is dropped ends up on the floor because the scaffolders haven’t been consulted.
Ensure The Correct Type and positioning of Lighting
Some lighting systems will have a stroboscopic effect that may make rotating objects appear stationary (this happens with video cameras recording helicopters flying and the footage looks as though the rotors are stationary). Different lighting systems may need to be combined that operate at different frequencies to prevent this effect.
Ensure that lighting levels are assessed at the point of work. High level lighting may provide ample lighting however when work equipment is installed or used then lighting levels may be reduced at the point of work (think of working underneath vehicles).
To read parts one and two please go to finch-consulting.com/insights-and-articles/
Manufacturing & Engineering Magazine | The Home of Manufacturing Industry News