Laura Hedley, Senior Occupational Psychologist at the OPC, explores why some employees struggle with fundamental safety practices.
In many organisations, safety performance fluctuates, with periods of high accident frequency which can prompt renewed vigour or new safety initiatives. These efforts often lead to temporary improvements, but long-term safety gains can sometimes remain elusive.
Laura Hedley from OPC said, “While equipment or insufficient training can contribute to poor safety performance, human factors are often the primary cause. Even though most employees adhere to safety protocols, everyone makes mistakes. Incidents often occur because we fail to get the basics right.”
Laura’s discussion highlights some of the key safety basics that can include: Ensuring the availability and proper condition of PPE; Conducting thorough equipment checks and maintenance; Holding safety briefings before work, and more.
Laura also points out “The Non-Technical Skills (NTS) of vigilance and conscientiousness also play a crucial role in the basics of safety, e.g., tools left on site or untidiness could lead to an incident. Risk and situational awareness are also vital in identifying and mitigating potential hazards.”
So, what prevents employees from mastering the basics of safety?
Through research and having undertaken hundreds of Post-Incident Assessments (PIA), OPC psychologists have found several common obstacles to mastering the basics of safety:
- Effort vs. Payback: Skipping the safety basics, preferring convenience over compliance.
- Task vs. the Basics: Prioritising job completion over safety.
- Over-Reliance on Experience: Ignoring safety basics in the absence of an incident or near miss
- Why Bother! A lack of positive senior response to safety concerns can lead to employee disengagement.
- False Security: Overconfidence and a failure to recognise potential risks.
- Not my responsibility! A pervasive attitude that can mean a culture of disengagement and neglect.
Laura emphasised, “Recognising human fallibility and promoting a culture where safety is everyone’s responsibility is essential. Employees must also feel empowered to report unsafe behaviours without fear. Regardless of role or seniority.”
The OPC identified some key factors why employees often struggle to challenge unsafe behaviour in others:
- Fear of reprisal or ridicule.
- Lack of confidence in their own safety knowledge.
- Social dynamics, such as not wanting to upset colleagues.
- An organisational culture prioritizing productivity over safety.
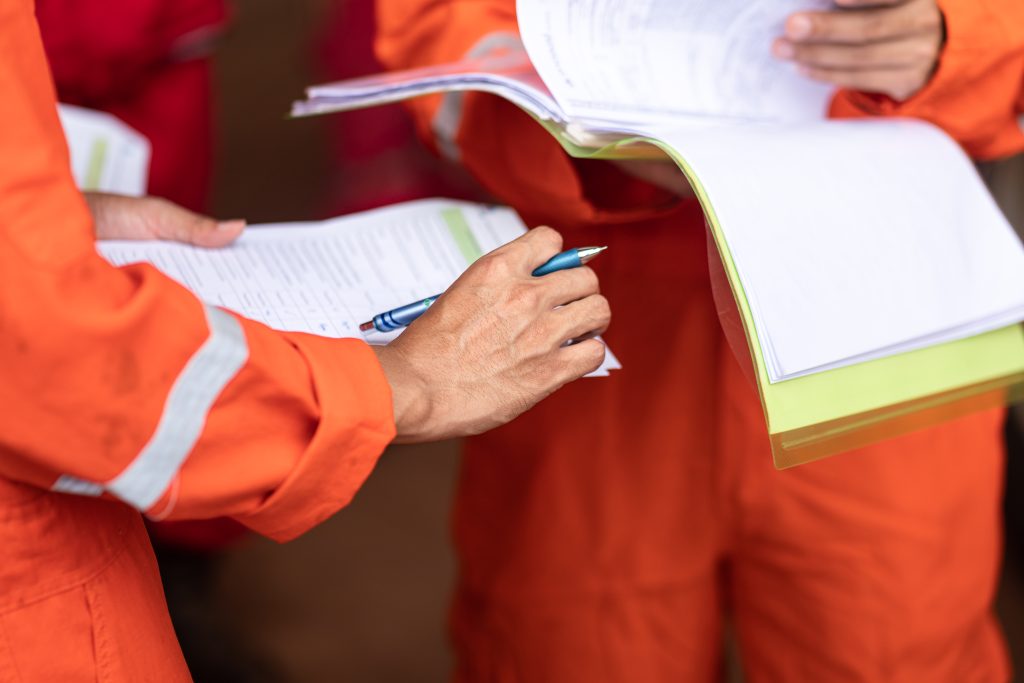
Creating a supportive environment where safety issues can be openly discussed is crucial. A recent OPC client survey of over 600 workers revealed that more than 90% prefer having their safety mistakes pointed out.
“Making the workplace safe isn’t just down to one person—it’s about all of us looking out for each other,” said a Maintenance Delivery Manager. “We need to speak up and hold each other accountable, even if it means having difficult conversations.”
How the OPC Can Help
The OPC offers various training initiatives to improve safety performance, including:
- Non-Technical Skills Training
- Back-to-Basics Workshop
- Accelerate Your Safety Leadership (AYSL) Workshop
You can read the article in full here.
Contact the friendly OPC team if you think your employees need some help getting back to the basics of safety.
E: admin@theopc.co.uk T: +44 (0)1923 234646 W: www.theopc.co.uk
Manufacturing & Engineering Magazine | The Home of Manufacturing Industry News