Embracing Innovation: Tennent’s Brewery Partners with SEEPEX
Tennent’s Wellpark Brewery is Scotland’s oldest brewery, tracing its roots back to the 1500s. Since its establishment in 1885, it has consistently produced award-winning brews. The brewery’s fascinating story revolves around Hugh Tennent, who defied skeptics in 1885 to create Tennent’s Lager, initially dubbed a ‘madman’s dream’ by newspapers. Today, Tennent’s Lager dominates the Scottish market, accounting for every second pint of lager consumed in the country.
Upgrading Brewery Operations for Enhanced Efficiency
As part of their process, spent grain is transferred from two mash filters that drain the spent grain to 24%DS. Originally, the spent grain fell from the mash filters into an expeller unit from where it was conveyed over 64m with a 20m elevation to the silo. With the expeller, the grain transfer took ~90 minutes after each brew and used 1,125Nm³ of air.
Tennent’s Lager, part of leading drinks manufacturer and distributor C&C Group, is committed to a robust sustainability strategy, exemplified by ambitious carbon reduction targets. These targets aim to achieve a 35% reduction in scope 1 & 2 emissions by 2030 and have been validated by the Science Based Target initiative.
In recent years Tennent’s has made significant investments in various carbon reduction projects, including carbon capture and anaerobic digestion plants. Additionally, Tennent’s has partnered with SEEPEX to improve energy efficiency in its spent grain transfer process, which is the most air intensive process on site.
Improved Efficiency, Productivity, and Energy Savings
Together with SEEPEX, Tennent’s explored the benefits of SEEPEX’s cutting-edge Smart Air Injection (SAI) technology. This ground-breaking solution combines an open hopper progressive cavity pump and pneumatic dense-phase conveying to efficiently transfer 15-40%DS spent grains, draff, and hops in plugs. Controlled air pulses enable seamless conveying over long distances.
SEEPEX established the optimum operation point with minimum air consumption to reduce the original air consumption and carbon footprint, and also assessed the energy efficiency in comparison with the initial system. SEEPEX was able to calculate all the consumptions eliminating the need to carry out a trial.
A Path to Sustainability: Scottish Industrial Energy Transformation Fund
The demonstrated energy efficiency from SEEPEX Smart Air Injection (SAI) enabled Tennent’s to access the Scottish Industrial Energy Transformation Fund (SIETF), designed to support the development and deployment of technologies that enable businesses with high energy use to transition to a low carbon future. Through this, the government funded 30% of the project.
Decreased Air Use and Transfer Times
Air consumption has decreased by an impressive 56%, dropping from ~1,125Nm³ to 500-700Nm³ per brew. Furthermore, there is a decrease in spent grain transfer time associated with the SAI system. The reduction in air use contributes to Tennent’s carbon reduction plan by reducing electricity use within the site.
Seamless Maintenance and Uninterrupted Operation
As Tennent’s embraces the future of brewing, it benefits from SEEPEX’s plannedCARE package. This comprehensive service ensures proactive, on-time planned pump maintenance, guaranteeing uninterrupted operation. This includes diagnostics to identify potential issues, enabling planned proactive maintenance for increased uptime and lower total cost of ownership.
Tennent’s commitment to innovation, efficiency, and sustainability shines through its partnership with SEEPEX. With enhanced efficiency, substantial energy savings, and a focus on seamless maintenance, Tennent’s continues to set the benchmark for excellence in the brewing industry.
Join Tennent’s in improving your efficiency and success story. Contact SEEPEX today to explore our innovative pump solutions for the brewing industry and distilleries, addressing your unique pumping challenges.
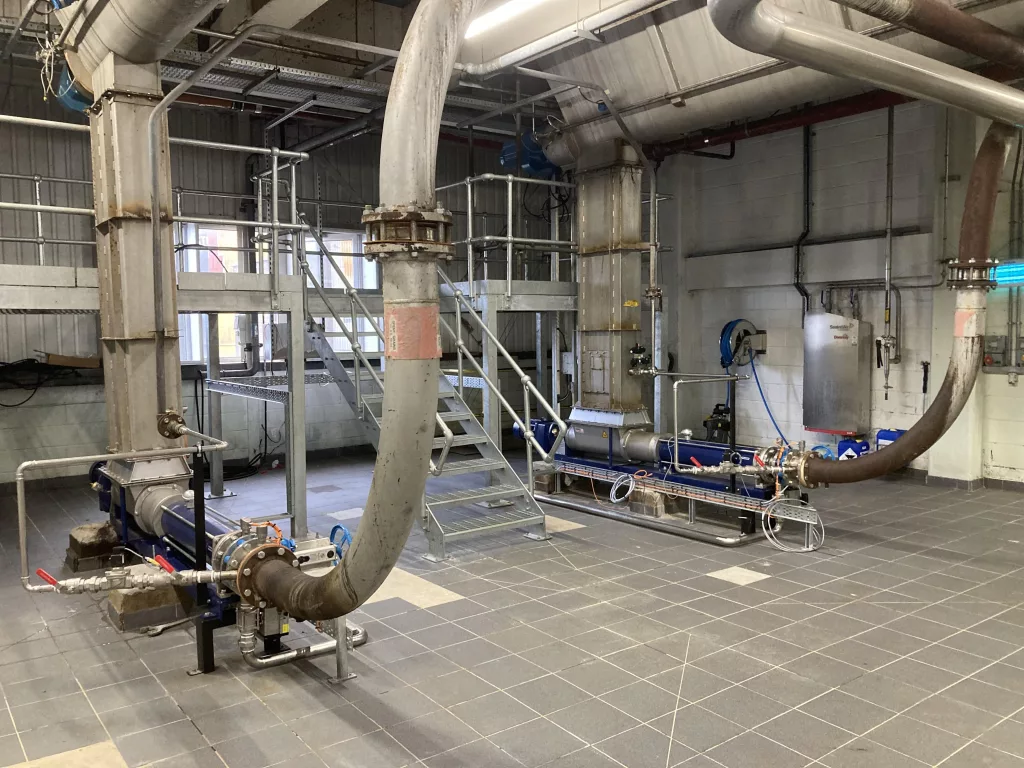
Manufacturing & Engineering Magazine | The Home of Manufacturing Industry News