A leading Gloucester-based toolmaker and precision subcontract machinist is using its investment in two new Sodick EDM machines to optimise the machining of parts for use in automated vehicle battery manufacturing machinery. Supplied by Sodi-Tech EDM, the new high-performance CNC wire- and spark-erosion machines have almost doubled production throughput at this progressive and ambitious manufacturing business.
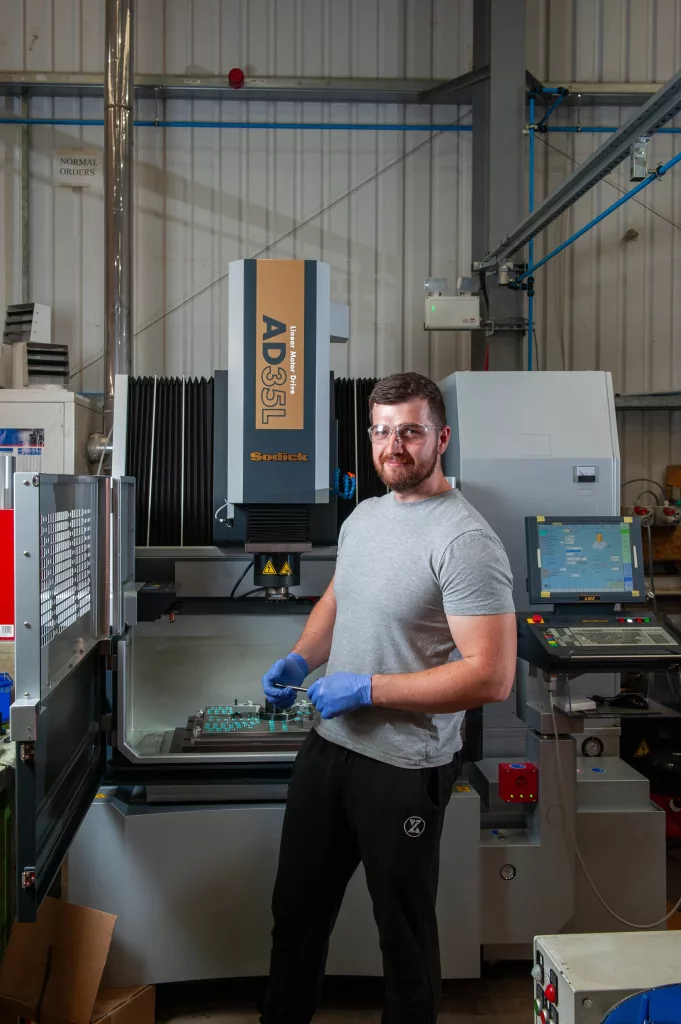
Trading since 2003, Richard Demczynski is the owner of L&R Precision Engineering, an eight-employee, ISO9001-accredited manufacturing business.
“L&R is about far more than simply making tools or parts, we undertake development work for customers to help resolve their problems and deliver the optimal solution,” says Mr Demczynski.
A case in point is a customer that makes automated machinery for vehicle battery manufacturers. These advanced machines are capable of producing thousands of SLI (starting, lighting and ignition) batteries for use in both petrol/diesel and electric vehicles. The machines require many complex parts, and the manufacture of some of the most challenging takes place at L&R Precision.
“One particular part was causing us real problems to machine using CNC milling,” states Mr Demczynski. “It was taking about three months to cut up the parts from black billet. We found that the material would distort after each cut, even after stress relieving.”
He knew EDM would provide the answer, but L&R Precision’s ageing manual wire eroder lacked speed and repeatability. The time had come to invest in a new wire EDM machine.
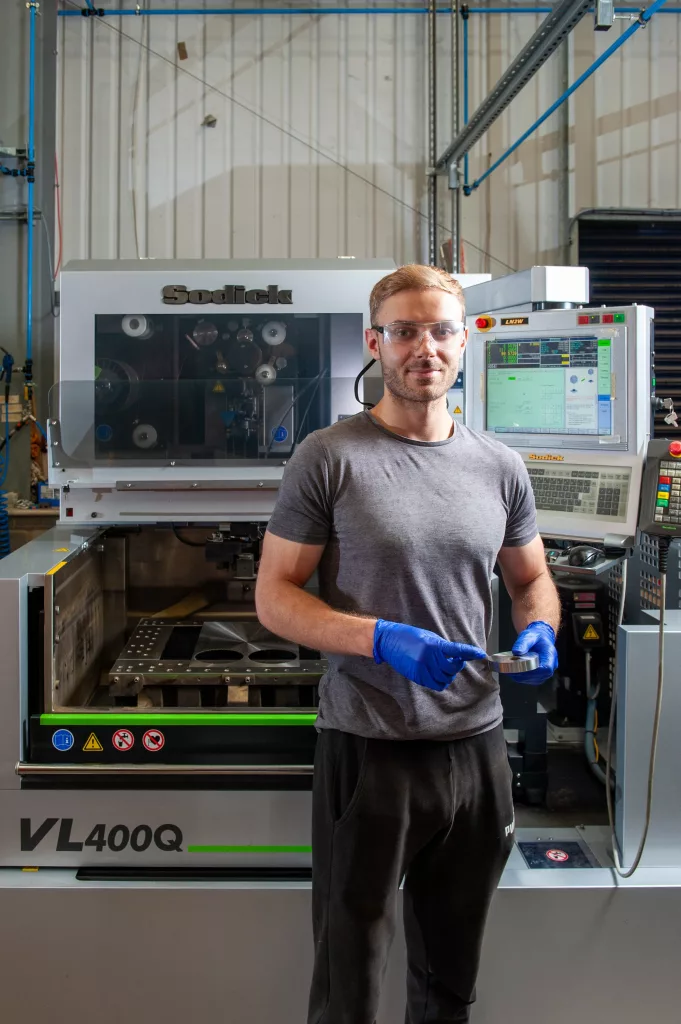
“I know a company that specialises in EDM and the owner told me I wouldn’t go far wrong with a Sodick,” explains Mr Demczynski. “When I approached Sodi-Tech and told them about my application they recommended the Sodick VL400Q, a compact, advanced-performance wire EDM machine. The up-front support was brilliant: Sodi-Tech explained everything to me in detail and I could see the advantages straight away. I scrapped my old machine with 100% confidence that the new Sodick would do the job. And so it proved. The new machine arrived in February 2023 and what previously took months now takes just hours. Installing the Sodick also freed-up capacity on three or four milling machines.”
Sodi-Tech EDM delivered a comprehensive suite of training sessions on the new VL400Q wire EDM at L&R Precision’s Gloucester facility. During this period, the company’s existing spark-erosion machine broke down. The ageing model was soon declared beyond repair, prompting investment in a new die-sink EDM. L&R Precision knew where to turn, duly taking delivery of a Sodick AD35L in July 2023.
“Like the VL400Q, the AD35L is producing parts for the battery manufacturing machines,” says Mr Demczynski. “Mould ejectors, for example, feature special forms in the end. We could do them on our old spark eroder, but the new Sodick is so much better. It has even helped win more parts from the same customer. These will again require development work, with production beginning in the New Year.”
He says that customers from all industries, not just automotive, return time and time again because L&R Precision invests in the latest technologies. Beyond EDM, the company offers a full range of machining services, including CNC milling and CNC turning supported by 3D CADCAM capabilities.
“There’s very little we can’t handle in-house. It helps to minimise lead times and keep customers happy. Customers do not tolerate lateness, so if we want full control over lead times we must undertake our own manufacturing. We’ve seen the benefits of this strategy with our new Sodick EDMs. The machines have been in place for a few months now and haven’t missed a beat. Furthermore, the aftersales support has been excellent. Sodi-Tech always comes straight back to us when we have a question. We’ve not had Sodick machines before so this proactive attitude was much appreciated in the early days when we were still learning.”
As a final note, Mr Demczynski points out that his operators are really enjoying the new Sodick wire and die-sink EDM machines, particularly as the company runs an incentive scheme based on output.
“Production throughput has nearly doubled since our investment in the two Sodick machines and our operators have seen the benefit in their wages. No wonder they are happy.”
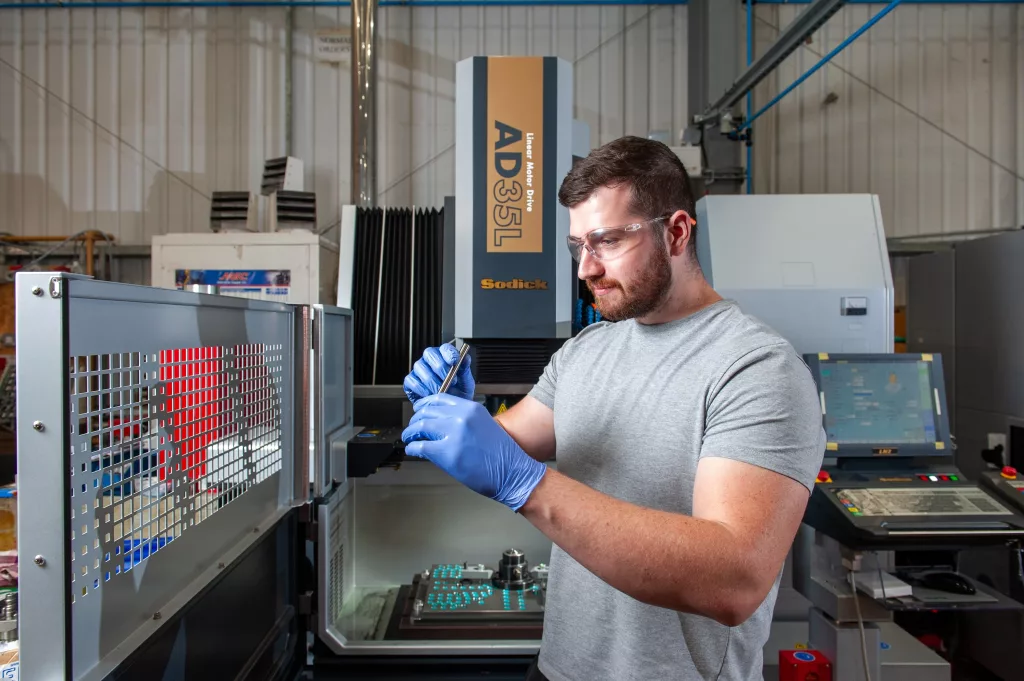
Manufacturing & Engineering Magazine | The Home of Manufacturing Industry News