Toolscope : Myth, Revolution or Solution?
The Myth
Machining consumable spend must be reduced!
Whilst it’s understandable that consumable cost is often a target for cost reduction, endeavouring to reduce consumable spend, in a world clamouring for best practice are we ignoring the obvious, does the result justify the effort?
With modern grinding machines costing anything up to a million pounds, productivity or O.E.E. (Overall Effective Equipment) of machinery and manpower can deliver multiple times the total consumable cost. Assuming the cost for a machine, labour and overhead is £150 an hour, how does this compare to the consumable cost per hour? In recent tests using the latest generation of Viper wheels, Tyrolit were able to decrease cycle time by as much as 30%.
Considering consumable unit costs at approximately £25 each (Viper wheel) and machine platform at £150* per hour, a 30% time saving reduction = £45; outweighing the cost of the consumable in one hour!
Tyrolits Machine Tool Revolution
Modular Assistance System
Toolscope** – Tyrolit’s Modular Assistance System; a revolutionary retrofit for any machine tool digitalisation of grinding technology. The system creates measurable added value for customers through increased process transparency featuring numerous process options, such as: O.E.E, collision detection, condition monitoring and much more. This provides an window into machining practice and process. Each machine can be set up with minimum effort, within a very short time and subsequently allows customers to save costs and time, as well as to ensure constant process quality reducing scrap, downtime and ultimately cost.
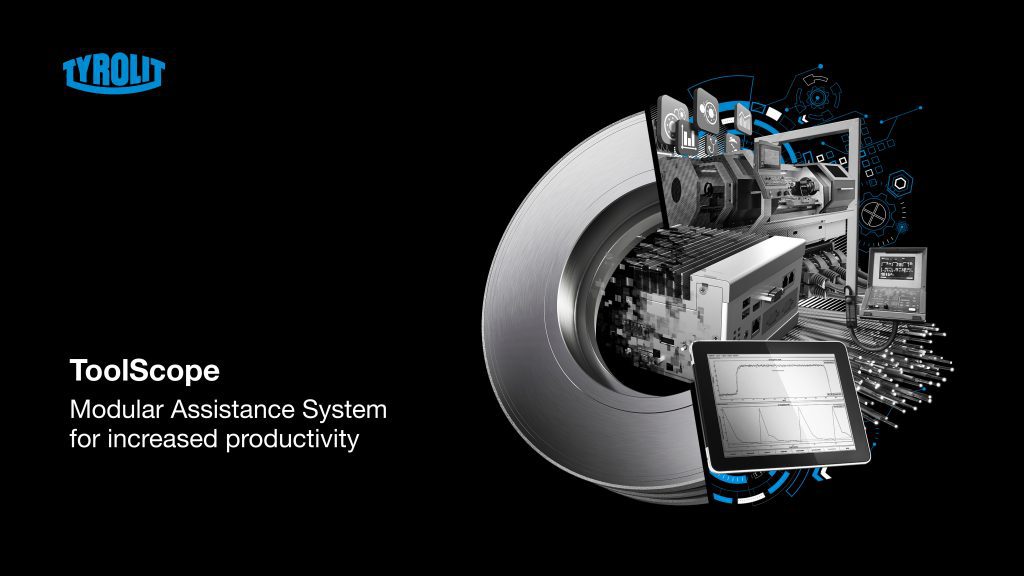
The Solution!
Viper Ultra Ultras Ceramic Hybrid Wheel – The Solution
As we celebrate 25 years of partnership in the development of the Viper Grinding Wheel, the development and introduction of a third generation of grinding wheels is a complete game changer. The original orange Viper wheel, lovingly referred to as “The House Brick” was superseded in 2007 by Viper Ultra; Utilising Tyrolit’s Bond Technology with a super tough but cool cutting abrasive, a new revision of the Viper Ultra was produced, now clearly identified by its blue colouring. A malleable product which adapts well to most Aerospace applications and can be found in most of the world’s machining facilities.
Tyrolit UK’s latest offering, a Viper Ultra Ceramic Hybrid wheel, uses our own manufactured ceramic blend but retains Tyrolit’s Bond Technology from its predecessors. Having only been on the market for 18 months, the results, its performance and the feedback from customers have been outstanding.
Customer Feedback
- “Whilst the consumable unit cost is higher, the parts per wheel is considerably higher, and more than compensates the increase in the wheel price!”
- “Regardless this is the future product for our facility.”
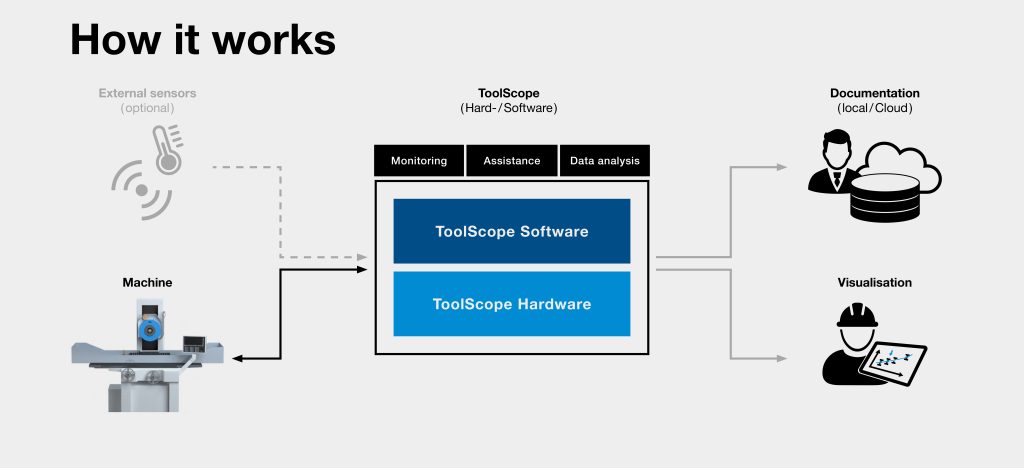
The Added Bonus ?
Environmentally Friendly
Tyrolit’s Ultra Hybrid wheel is manufactured at lower kiln temperatures than previous products, contains no naphthalene and with less dressing and more parts per wheel, reduces landfill, freight (Co2) as well as reducing demand for virgin material, safeguarding supply and reducing environmental impact.
Machine tools are precious to the manufacturing industry, protect your investment with Toolscope and invest in it with the latest in consumable technology!
Contact Tyrolit for a no obligation trial and let Tyrolit be part of your solution!
Pete Dufty – Sales Director at Tyrolit
*Prices based on estimates supplied by aerospace manufacturer.
**Toolscope features include :
- Process Monitoring Calibrated Bands; in which if the process alters from the set parameters the machine alarms (unsanctioned program modifications, incorrect feed rates etc.)
- Automatic Shift Log registering; Overall Effective Equipment (O.E.E)
- Wear Monitoring Measure; force on the axis, ensuring the grinding wheel is cutting freely reducing the chance of burning
- Adaptive Federate Control; lessen or maximise infeed depending on spindle load (assuming not a fixed process)
- Collision Detection; stopping the machine tool much quicker than the OEMs system; reducing damage risk and maintenance downtime
- Condition Monitoring; state of machine tool wear shown as a trend, providing potential risk analysis before failure of the machine tool
- Tool Change Log; recording accurate wheel change against pieces produced for cost analysis
- Machine Data Analysis; capturing the machine data for runtime analysis
- Documentation and Control; quality documentation generated for each process.
Toolscope : Myth, Revolution or Solution?
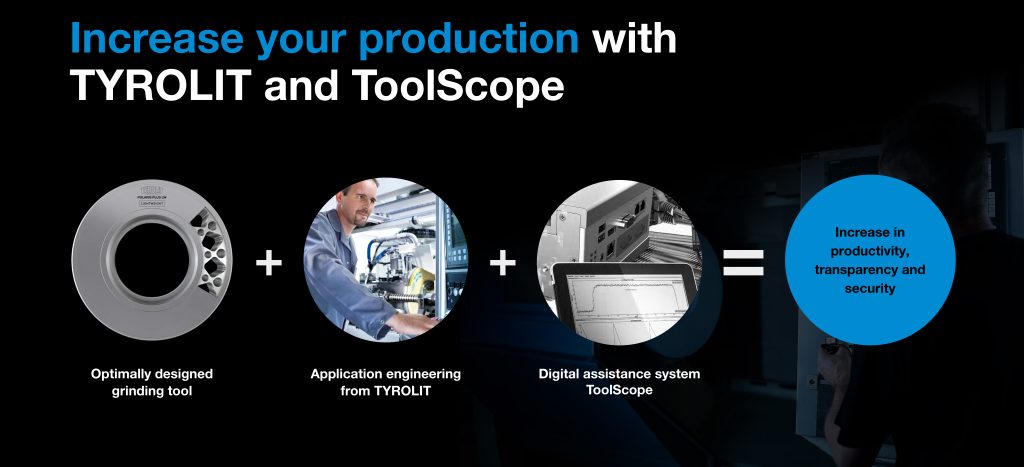
Manufacturing & Engineering Magazine | The Home of Manufacturing Industry News