Lightweighting foams are essential in advancing electric vehicle (EV) development, addressing challenges such as energy efficiency, safety, and design flexibility. These foams reduce the overall weight of EVs, enhancing energy efficiency and extending range by requiring less energy to propel the vehicle. They also allow for smaller, lighter batteries, reducing costs and improving performance.
Additionally, these foams enhance safety by improving crashworthiness without adding weight and offer designers flexibility to create aerodynamic and aesthetically pleasing vehicle designs.
TECHSiL’s foam technologies are playing an increasingly important role in the development of electric vehicles. They form part of the manufacturer’s solutions which also include silicones and adhesives. This is supported by the company’s deep technical knowledge and ability to produce customised products for production needs. Unlike a typical stockist, TECHSiL collaborates with clients to understand their applications and provide the right technical insight, becoming a trusted supply chain partner known for on-time performance and bespoke packaging.
The company is a “trusted material expert,” says Marketing Manager Kate Harris, adding that it is never simply referred to as a “stockist of adhesives.” Its core advantage is “our deep technical knowledge across silicone, adhesive and foam technologies. TECHSiL goes that extra mile to understand the application and offer the right technical solution that fits the production needs of the customer.”
Foam encapsulants and potting materials are revolutionary and TECHSiL is a frontrunner in their production for automotive uses. Their lightweight options are vital when a large area needs to be filled as their use could mean the difference between a few kilos and a few hundred grams. TECHSiL’s applications in automotive lead to dramatic reductions in weight, which in turn reduces fuel use. The rough rule of thumb is that reducing weight in a vehicle by 10% improves fuel economy by 8%.
This also means less emissions and helps meet global fuel economy standards. Christopher Dilley, Managing Director at TECHSiL, said, “The inclusion of both silicone and PU foams offers our customers limitless shape and size possibilities, fast filling of voids, lighter weights, strength, and stability. We can also go further with fire resistance, soundproofing and excellent production cycle times.”
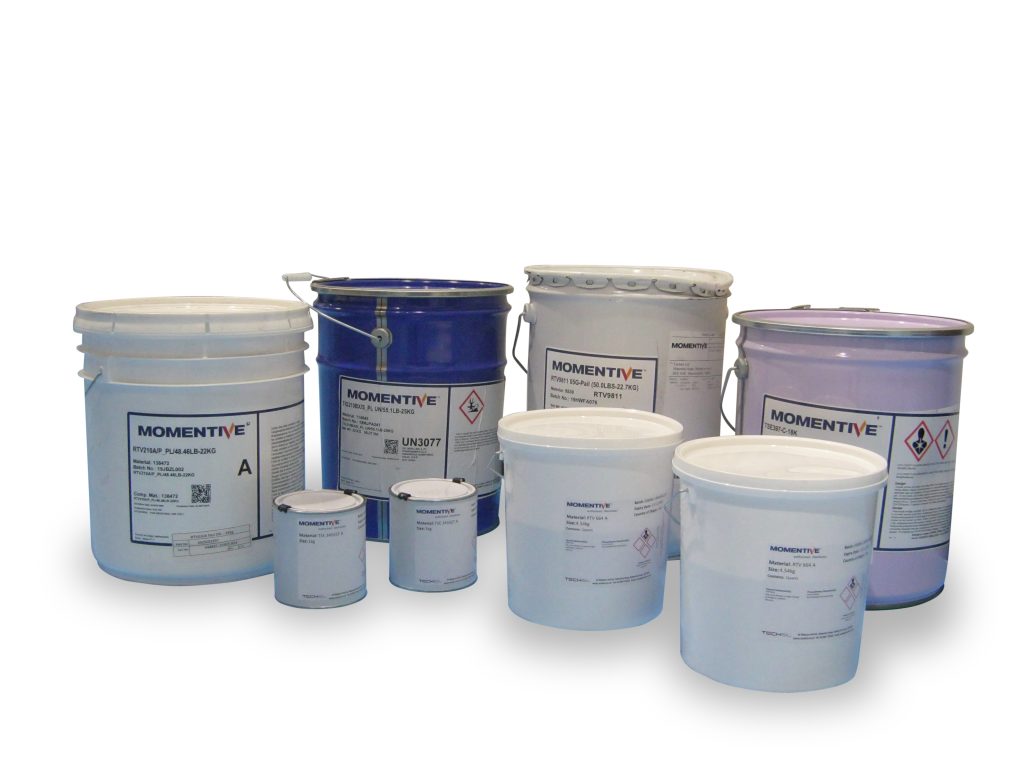
TECHSiL Partners with DOPAG
TECHSiL partnered with DOPAG UK recently to provide FIPFG (formed-in-place foam gasket) foam gaskets through a comprehensive contract manufacturing service. This collaboration brings together high flexibility, extensive expertise, and personalised consulting to benefit customers. The service encompasses all aspects of foam gasket production, from material testing and sampling to prototypes, small quantities, and large series production.
One of the significant strengths of this partnership is the individual consulting provided for prototype production and support for companies entering the seal foaming business. Initially, industry-experienced engineers conduct a feasibility study for the desired application and determine all production parameters. During the sampling phase, initial prototypes are produced, followed by complete series production based on customer requirements.
TECHSiL and DOPAG UK leverage their proprietary metering and mixing technology and together their systems process all common materials for gasket foaming, including low-to-high-viscosity polymeric gasket foams made of PU and silicone. This allows the use of foam gaskets from all material manufacturers, ensuring the optimal material is selected for each application. Customised adaptations or developments are also possible.
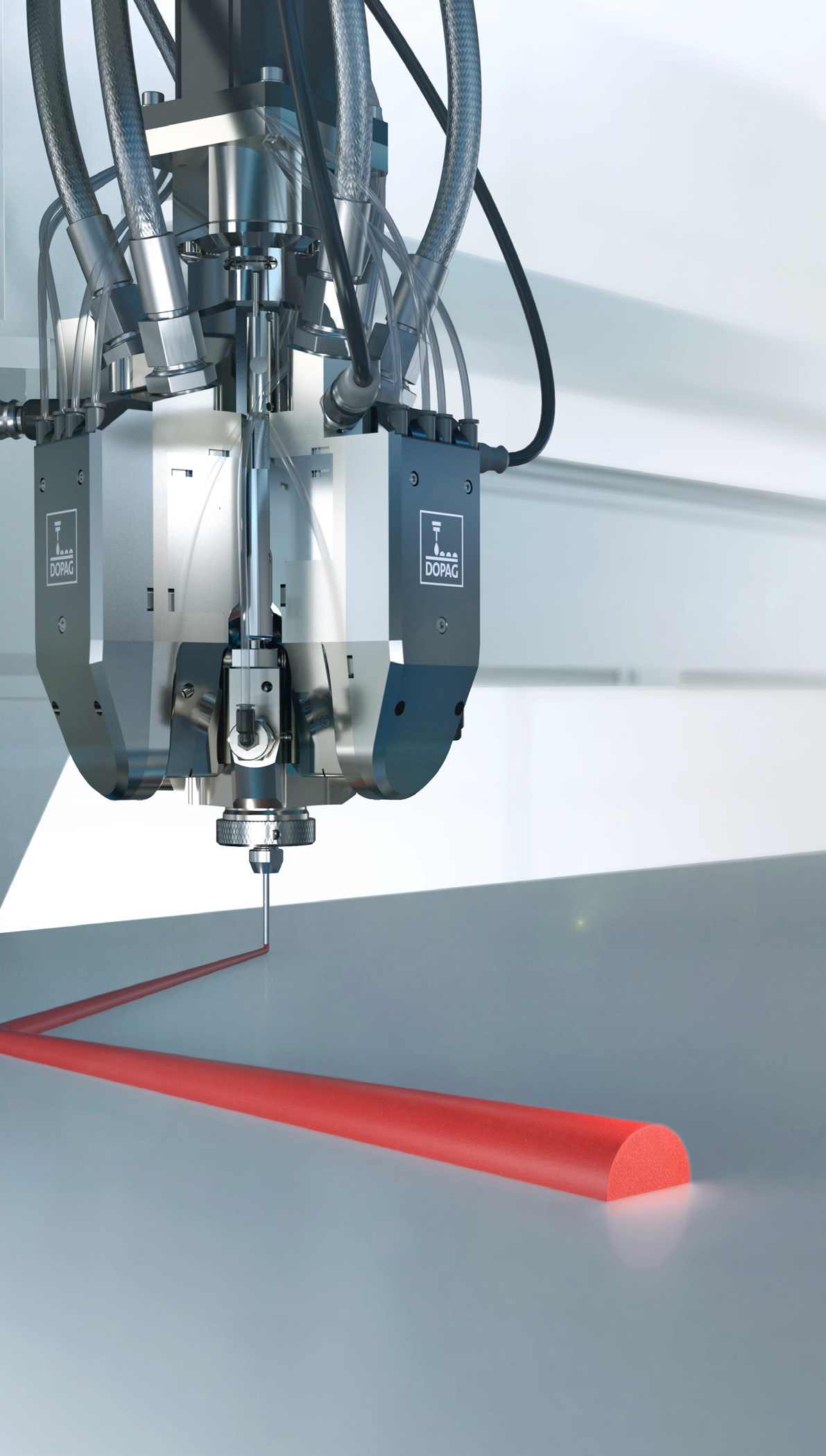
Automated applications for three-dimensional components, grooves, moulds, and flat surfaces can be implemented. Contract manufacturing for FIPFG foam gaskets offers an efficient and flexible solution for numerous industries, including the manufacture of control cabinets, automotive and lighting components, and applications in the household appliance, filter, and packaging industries.
Foam gaskets made of polyurethane protect components from dirt, dust, and moisture. They are used both in classic automotive construction and in the field of mobile energy, for example in electric vehicles, e-scooters or charging stations. They can also be applied to, for example, loudspeakers, lights, doors, and ventilation grilles of switch cabinets as well as housings for control units in cars or as clear encapsulation on LED lights. A fully automated system that meets all requirements in terms of process reliability and quality standards is suitable for series production with high quantities.
Exploring New Opportunities
TECHSiL is understandably ambitious as it looks to the future with a keen focus on growing its presence in the relatively new markets of PU and silicone foams. It helps that they possess a lot of in-house knowledge and experience which they are complementing through significant investment in training. TECHSiL is part of Diploma Plc and has a huge DVR programme in place. It also has many material scientists within the company who complement the drive to develop the next generation and promote continuous learning and technology innovation.
TECHSiL are constantly looking for the next big breakthrough. “Symptomatic of this is our thermal management adhesives and potting materials,” notesChris. “15 years ago no one was talking about these thermal transfer materials much but today they account for 25% of our product range.”
The trend for miniaturisation and high-density boards in electronics changed the market and TECHSiL adapted quickly and gained market share with great products and reacting early to customer needs. More recently the company has launched the FIPFG – Form In Place Foam Gasket – as developed by DOPAG in the UK for sealing housings in automotive, lighting, and electronic control boxes.
________________________________________________________________
How Lightweighting Foams are Aiding EV Development
By Kate Harris
Lightweighting foams play a crucial role in electric vehicle (EV) development, from improved energy efficiency to safety and design flexibility – foams are revolutionising EV development by addressing key challenges faced by an ever-changing market.
By reducing the overall weight of the vehicle the energy efficiency is dramatically improved. EVs with lighter bodies require less energy to propel, thus extending their range on a single charge. With less weight to carry, EV batteries can deliver better performance. Lighter vehicles also require smaller, lighter batteries to achieve the same range, reducing costs and increasing efficiency.
Lightweight foams can also contribute to the safety of EVs. By strategically placing these materials in the vehicle’s structure, manufacturers can improve crashworthiness without adding excessive weight, thus enhancing overall safety.
Foams can be moulded into various shapes and sizes, offering designers greater flexibility in creating aerodynamic and aesthetically pleasing vehicle designs. This flexibility allows for innovative approaches to EV design, optimizing both performance and visual appeal. While lightweighting foams may initially involve higher material costs, they often lead to long-term cost savings. The improved efficiency and performance of lightweight EVs can result in lower operational costs over the vehicle’s lifetime, making them more economically viable for consumers.
Why is EV Development Important?
EV development addresses environmental, economic, and social challenges, playing a crucial role in transitioning toward a more sustainable and resilient transportation system. EVs produce zero tailpipe emissions, reducing air pollution and greenhouse gas emissions. As the world strives to combat climate change and improve air quality, transitioning to electric transportation is crucial.
Electric vehicles typically have higher energy efficiency compared to internal combustion engine vehicles (ICEVs), meaning they can travel farther using the same amount of energy. This efficiency contributes to resource conservation and helps reduce the depletion of finite natural resources.
EV development drives innovation in battery technology, electric drivetrains, and charging infrastructure. These advancements not only benefit the automotive industry but also have broader applications in energy storage, renewable energy integration, and other sectors.
Challenges of Future EV Development
EVs are increasingly incorporating autonomous driving capabilities and connected features, such as advanced driver-assistance systems (ADAS), vehicle-to-everything (V2X) communication, and over-the-air updates. These technologies enhance safety, efficiency, and user experience in electric vehicles. The EV market is also diversifying beyond passenger cars to include a wider range of vehicle types, such as electric trucks, vans, buses, and even electric aircraft. This expansion of EV offerings reflects the growing demand for clean transportation solutions across various sectors.
Collaboration between automakers, technology companies, energy providers, and other stakeholders is essential for driving EV development forward. Strategic partnerships enable shared expertise, resources, and infrastructure to accelerate innovation and market penetration.
One of the most significant areas of focus for EV development is battery technology. Continued research and innovation aim to improve energy density, reduce costs, and enhance the longevity and safety of batteries. Solid-state batteries, for example, hold promise for higher energy density and faster charging times. As battery technology improves, EVs are expected to offer greater range and performance, making them more competitive with traditional internal combustion engine vehicles. Enhanced charging infrastructure, including fast-charging networks, will also contribute to the practicality and convenience of EV ownership.
Choosing the Right Manufacturing Supplier
Choosing the right manufacturing supplier plays a pivotal role in the development of EVs; by providing specialised components, innovative materials and manufacturing expertise they can assist automotive manufacturers with their cost optimisation, research and design collaboration whilst providing quality assurance and full supply chain management.
Suppliers can research and supply innovative materials suitable for EV construction, including lightweight metals, advanced composites, and high-strength alloys. These materials can help reduce the weight of EVs, improve energy efficiency, and enhance overall performance. They develop and provide specialised components specifically designed for electric vehicles, such as batteries, electric motors, power electronics, and charging systems. Components which are essential for the performance, efficiency, and safety of EVs.
EV manufacturers partner with key suppliers on research and development projects to innovate new technologies and solutions for electric vehicles. This collaboration can lead to the development of next-generation EV components with improved performance, safety, and sustainability.
Visit www.techsil.co.uk

Manufacturing & Engineering Magazine | The Home of Manufacturing Industry News