After well over a decade of exhibiting at Advanced Engineering UK, PRF Composite Materials reflect on the vibrant and busy 2024 event, for which they were headline sponsors, participated in a number of presentations and attended the Composites UK Industry Awards 2024 dinner as a shortlisted company.
Showcasing a new stand for 2024, the PRF team were delighted to welcome a large number of visitors over the two-day event and were particularly pleased by the high quality of connections made. Over the course of the show, the team hosted composite constructors, continued to grow and develop already fantastic relationships with suppliers and recyclers, and to nurture newer connections with software companies looking to bring the composites industry to new and younger audiences through apps and websites such as Engineers Insight – for which PRF are leading the way as the first composite materials manufacturer on the app!
This year, PRF have introduced two new resin films: RF Primer and RFA570 eXpress cure adhesive film for core bonding applications. Formulated as an epoxy-based composite primer/surfacing film, PRF’s new RF Primer is fully compatible with their epoxy prepreg systems and provides a sacrificial surface that enables the constructor to eliminate paint priming, thereby reducing the time required for surface preparation. RFA570 eXpress cure is a unique product which has been principally designed for use with PRF’s RP570 and RP570 FR eXpress cure epoxy prepreg systems, as an adhesive film for core bonding applications. The distinctive characteristics of this product enable it to be cured in a press in 4 minutes at 140°C, thereby speeding up the processing of honeycomb sandwich panels – with either nomex or aluminium honeycomb. It is for this class-leading, unique product which PRF were shortlisted this year for a Composites UK Industry Award in the category of Innovation in Materials – making this a second year in a row for PRF to be shortlisted in this category.
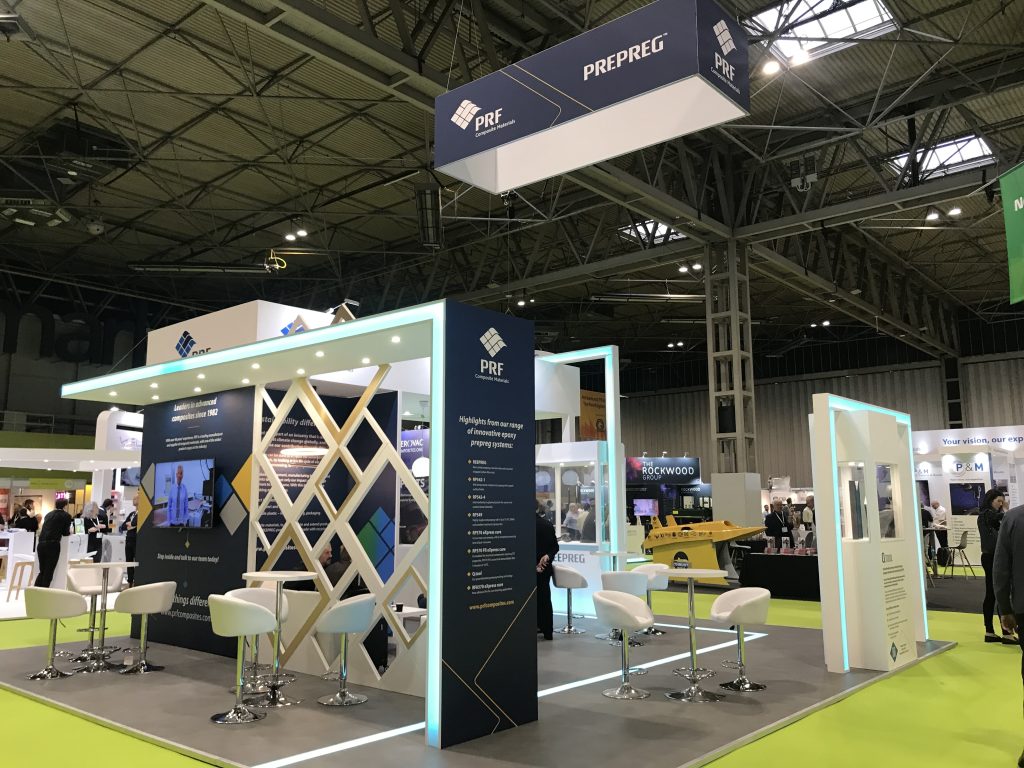
Product development at PRF is not only driven by customer and market need, the team also focusses on cost-efficiency and faster processing, high performance and superior quality, and improved sustainability and lowering energy-per-part. With this in mind, they showcased their innovative prepreg materials with a number of high performance components on display.
On the stand, PRF showed aircraft interior components constructed using their RP570 FR eXpress cure fire-retardant epoxy prepreg system and REEPREG prepreg material made with recycled carbon fibre nonwoven – reducing carbon fibre waste going in to landfill and also improving circularity by providing constructors with a practical and cost-effective way to incorporate recycled carbon fibre into component construction.
PRF have investing in development of a special methodology of impregnation to ensure that once prepregged, REEPREG material is easy to handle and press from a flat sheet into a 3D shape. Combining this with their class-leading RP570 and RP570 FR eXpress cure epoxy prepreg systems creates a product that offers not only increased cost-efficiency and productivity (with complete processing times of 4-6 minutes in heated press) but also offers improved circularity, end of life options and sustainability gains. This exciting material also has an out life of 60 days at 20°C.
Also showcased were exceptional carbon tools manufactured with their groundbreaking, patented prepreg tooling technology Q.tool. Q.tool (UK Patent GB2614600) significantly reduces the time and costs of carbon tool manufacture, with its uniquely designed surface and 1020g/m2 bulk plies. Using PRF’s class-leading RP800 epoxy tooling system, the combination of Q.tool’s new surface and 1020g/m2 bulk plies provides the same weight and thickness as the 1:8:1 system, and significantly reduces the number of debulks to as few as one. Q.tool offers the constructor: Up to 50% reduction in labour time/cost; Reduced number of debulks; Improved sustainability and cost savings with reduced use of plastic consumables; Exceptional drapeability and surface finish – as demonstrated with these beautiful carbon tools produced by Composite Products.
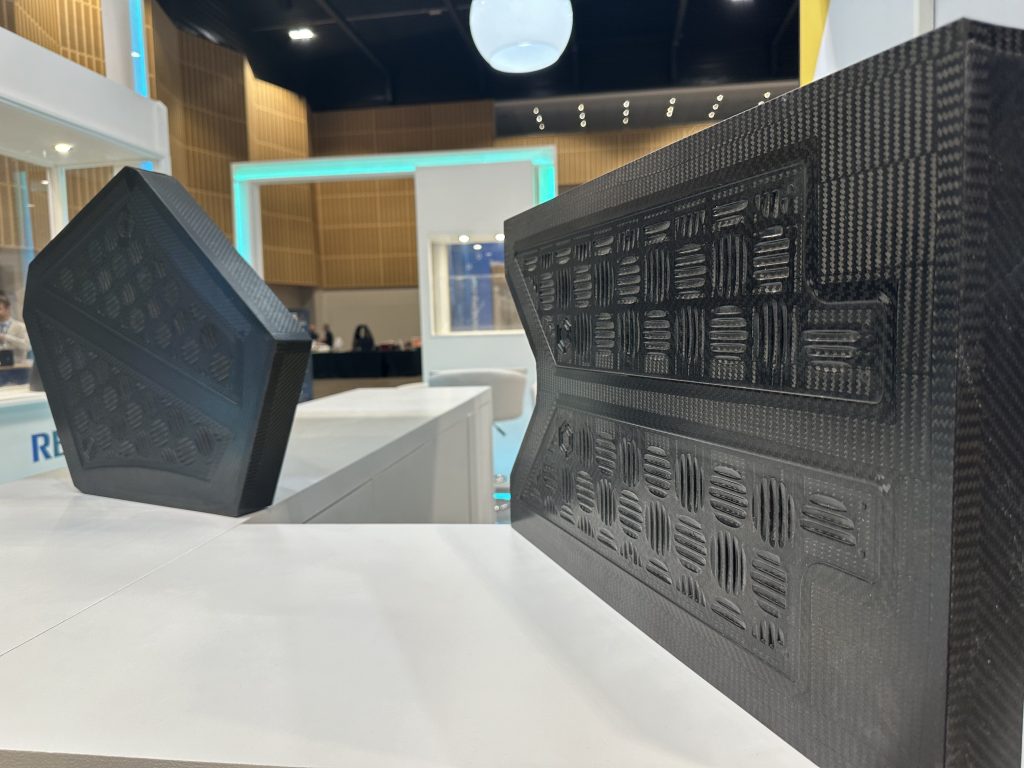
On the first day, Sales Director Vincent Fawcett alongside Dr Stu Morris (Director of Business Development at Pentaxia) presented how the combination of PRF’s eXpress cure prepreg materials alongside Pentaxia’s significant investment into high volume manufacturing (HVM) capabilities are key for driving forward the use of composite materials in industries requiring HVM of structural parts.
Vincent Fawcett also presented PRF’s RFA570 eXpress cure adhesive film for core bonding applications in the Innovation showcase as a shortlisted product in the Composites UK Industry awards. During this presentation, the PRF team were able to show the audience demonstration panels constructed from carbon fibre twill weave skins impregnated with RP570 eXpress cure epoxy resin. These were laid up either side of honeycomb, with a layer of RFA570 adhesive film between the skin and the honeycomb. The panel was then cured in heated press in just 6 minutes for the entire process.
As headline sponsors of the show, PRF Composite Materials sponsored the Composites zone, including special areas such as the Composites Forum and the Composite Networking Area. It was at the latter where the ThrustWSH quarter scale exhibition model boat was situated. ThrustWSH, led by Richard Noble OBE and Lorne Campbell, aims to set a new water speed record, using pioneering research and a truly innovative design to create a safe and fast hydroplane with a target to set an officially ratified two way average speed of 400mph over a measured mile or kilometre. The PRF team are proud material sponsors of this world-leading and innovative project, supplying their innovative prepreg materials to construct the craft. Hannah Khusainova, Marketing Director at PRF, introduced Richard to the Composites Networking Area – where he undertook an informal Q&A about the project, answering questions on how the team were reducing the risks of the project, connecting with the younger generations and also improving the sustainability of the jet fuel needed by working with teams looking at converting human waste.
When the UK composites industry comes together, it is impossible to escape the sincere feeling of being at a family reunion, and it is wonderful to have shows like Advanced Engineering to celebrate and showcase this world-leading industry!
Please visit www.prfcomposites.com to find out more!
Manufacturing & Engineering Magazine | The Home of Manufacturing Industry News