German sawing machine and storage system manufacturer Kasto has introduced an automated magnetic handling system for long stock, enabling steel stockholders to speed and simplify order picking. KASTOpick bar is available in the UK and Ireland through the group’s subsidiary in Milton Keynes, Kasto Ltd, which will supply the equipment with newly purchased storage and retrieval systems or retrofit it within existing warehouse operations.
Automatically handling long stock that has been placed randomly in a cassette is challenging, as the position of each item is difficult to predict. KASTOpick bar incorporates a pair of robots that allows users to autonomously pick magnetic bright drawn or black steel material of flat, square or round cross section, both bar and tube, lying in any orientation.
There is no need for users to teach-in the robot movements. To start the process, the system deploys an optical sensor to scan the storage cassette, which can be up to six metres in length. An algorithm developed by Kasto processes the 3D point cloud generated by the scan.
Intelligent software analyses the data to identify the location of each stock item as well as potential gripping points for the robots. Points are only considered if they allow stock to be picked up and deposited without collision. The software then optimises movement to the target position, after which the process starts anew with the next scan.
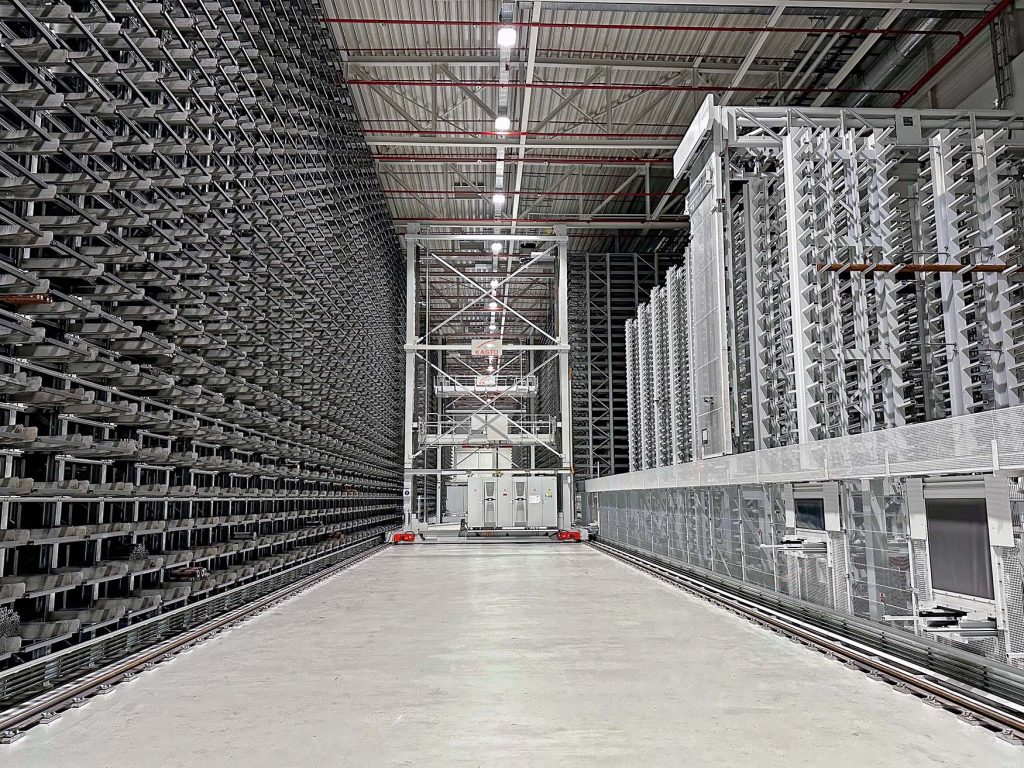
The handling system communicates with the stockholder’s enterprise resource planning system to provide the right material at the right time and location if on-site processing is required, such as cutting to length by a saw. The software also directs placement of material to ensure that it is stacked in an ideal pattern for bundling and strapping, based on material dimensions and order volume.
In its standard version, KASTOpick bar handles loads up to 500 kg, although systems capable of lifting heavier loads may be supplied on request. A range of grippers is available to provide customised solutions to suit the shape and size of the items to be moved. The system automatically selects the ideal magnetic gripper for each task to ensure material is transported carefully and safely, so high-mix, low-volume requirements are as easily addressed as those involving large volumes.
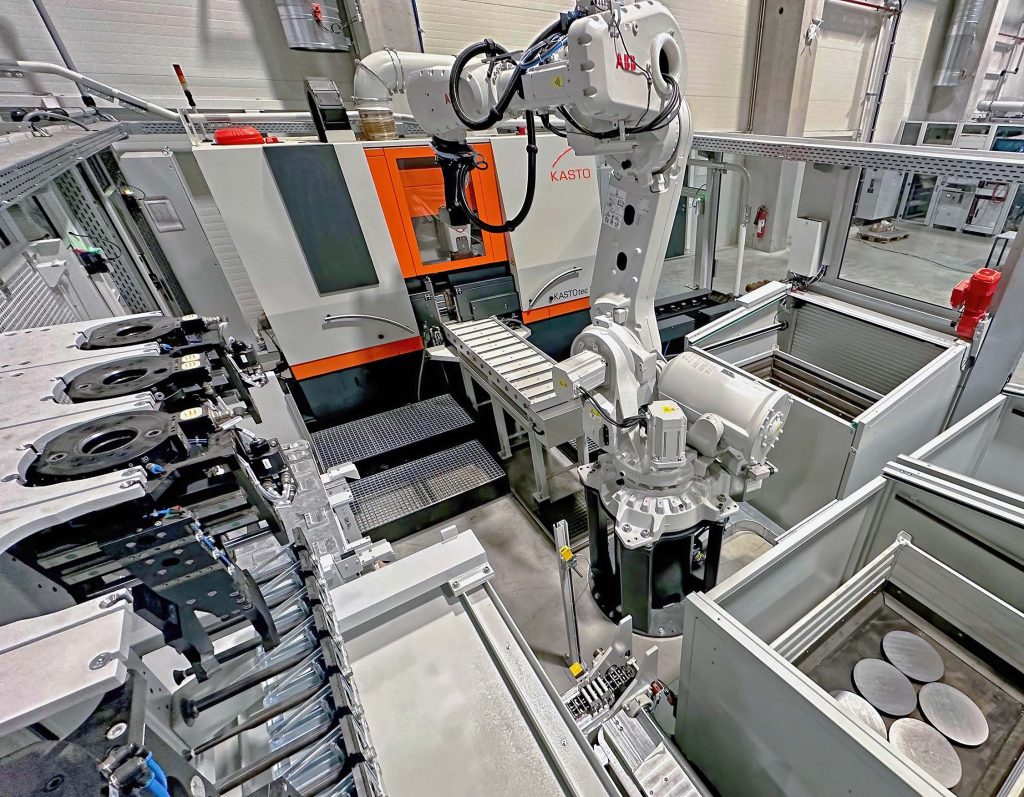
With its intuitive interface, KASTOpick bar is easy and efficient for operators to use without extensive training or specialised technical knowledge. The advantages of the automated solution are many. Warehouse staff no longer have to remove and transport heavy and cumbersome material by hand or crane. Companies therefore minimise physical demands on employees, preventing injuries and accidents. Labour can be used more efficiently in the workplace, lowering operating costs and speeding added-value processing and deliveries.
The compact system joins existing KASTOpick handling solutions. KASTOpick select supports manual picking by crane. KASTOpick sheet is able to separate sheet material that is accurately stacked on load carriers. KASTOpick split separates bars of larger cross section that have been placed neatly next to and on top of each other. This system is not suitable for dealing with random stock orientation, however, so KASTOpick bar has been introduced to fulfil this requirement.
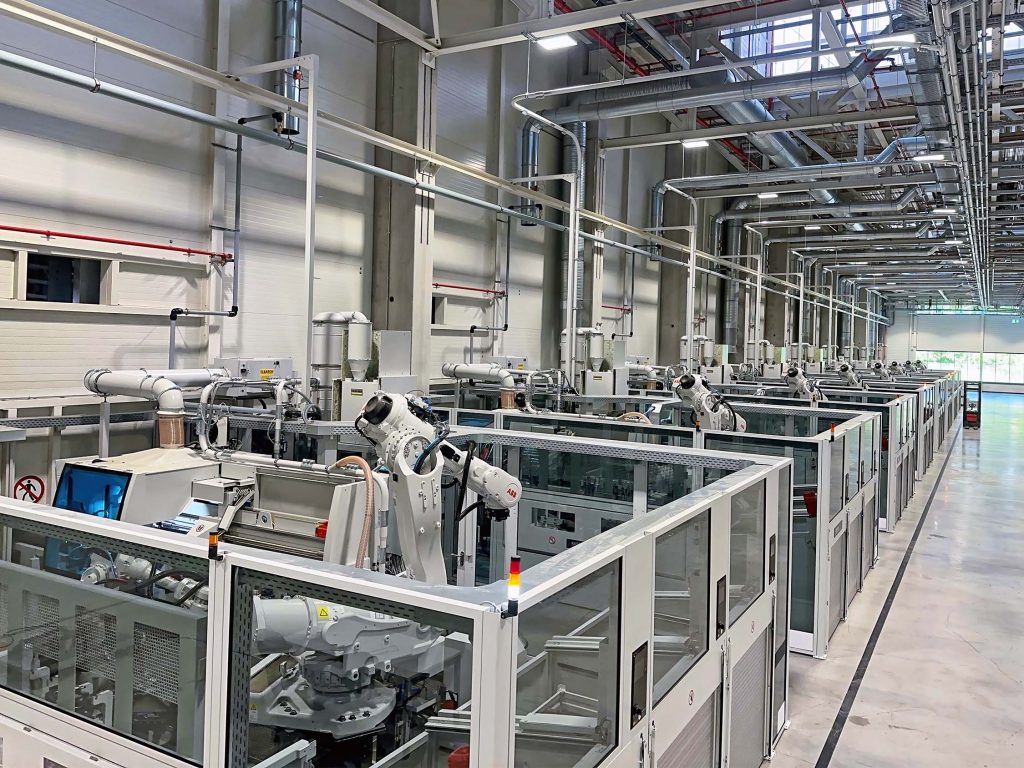
Manufacturing & Engineering Magazine | The Home of Manufacturing Industry News