At a tank farm in a Brazilian sea port, two centrifugal pumps were used for transferring heavy oil from storage tanks to road tankers or vessels until February 2020. This required the high viscosity of the medium to be reduced by means of diesel injection, costing the owner at least 2,000 US dollars each day. In addition, the centrifugal pumps regularly broke down due to cavitation damage. The owners decided to initially replace one of the two centrifugal pumps with a NOTOS® multi screw pump from NETZSCH. Due to its very good suction capabilities, the selected four-screw 4NS is also suitable for highly viscous media with up to 200,000 cSt, achieving a flow rate of up to 3000 m³/h. After commissioning, it became evident that – in contrast to the remaining centrifugal pump – the multi screw pump was running without cavitation even at significantly higher flow rates. Another benefit was that the extensive addition of diesel was no longer required. Based on this positive experience, the customer decided in February 2020 to also replace the second centrifugal pump with a NOTOS ®. Moreover, it became evident that the power consumption could be reduced significantly.
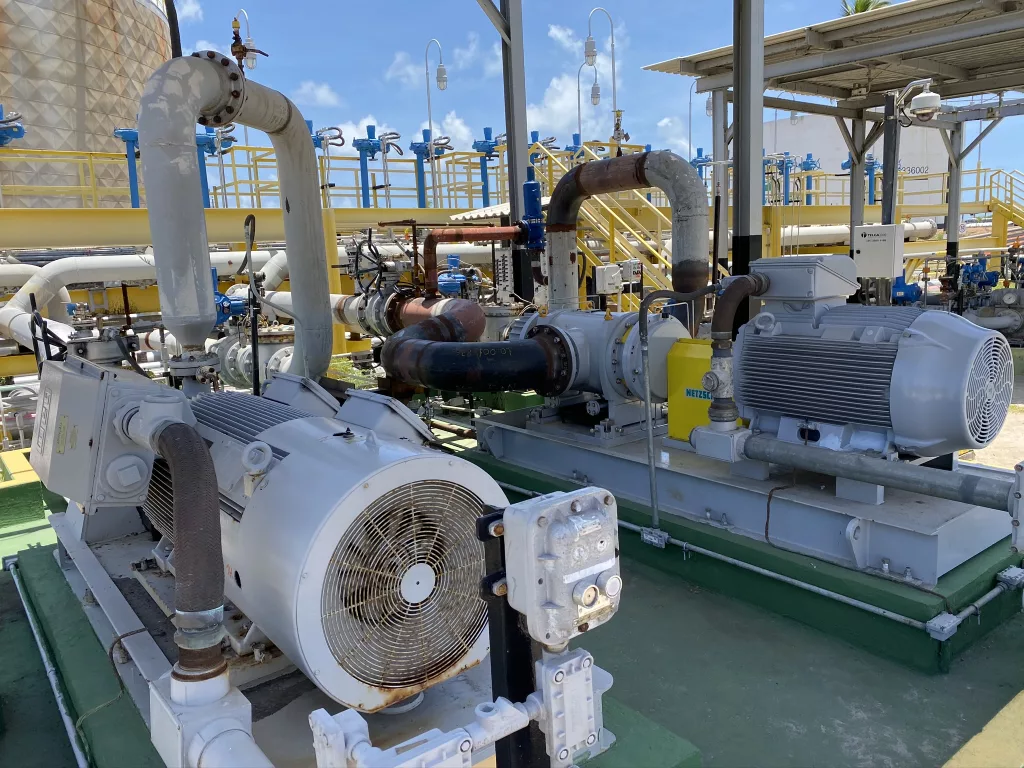
“The pumps, which are used for moving heavy oil from a tank farm to road tankers or vessels at a sea port in northeast Brazil, are primarily needed during dry periods,” explains Vitor Assmann, Senior Sales Manager at NETZSCH do Brasil. “That is because the hydropower plants in this country produce less energy during those periods, which increases the demand for heavy oil.” Until February 2020, this transfer had been implemented with two centrifugal pumps, which, however, had struggled with the high viscosity of the medium. “The poor suction capability of conventional centrifugal pumps means that some of the oil remains in the tank and cannot be used,” explains Vitor Assmann. “In addition to this, unsuitable technology can lead to cavitation, which will cause the pumps to fail in the long run.”
Cavitation was also an issue on the two centrifugal pumps at the Brazilian tank farm. Due to the high viscosity, the system had a lower NPSHa value, particularly at night, which made it necessary to add expensive diesel to the heavy oil in order to reduce the viscosity. “Around 3,000 liters had to be added each day, at a cost of at least 2,000 US dollars per day,” continues Assmann. To increase the reliability and efficiency of the process and to lower energy costs, the owners decided to replace one of the two centrifugal pumps with a NOTOS ® multi screw pump from NETZSCH and to compare the performance of the two units.
Robust pump for media with up to 200,000 cSt
The NOTOS ® series generally comprises multi screw pumps with two (2NS), three (3NS), or four (4NS) screws which can be used flexibly for different viscosities, even for large flow rates. The tank farm in Brazil required a pump that could transport up to 200 m³/h of heavy oil with a pressure of 18 bar, a temperature of 10 – 50 °C and a viscosity of up to 9,000 cSt. The owner of the tank farm selected a 4NS twin-screw pump, which is available for flow rates of up to 3,000 m³/h and is suitable for highly viscous media with up to 200,000 cSt.
The pump stands out on account of its high level of robustness, it is resistant to dry running and can be manufactured from materials that are specially selected for the application at hand. State-of-the-art production technologies enable narrow tolerances between the dynamic and static components, reducing the return flow. In combination with the flow optimized shape of the pump chamber, this results in a high level of efficiency.
Low NPSHr value prevents cavitation
Apart from efficiency, however, the flexibility of this pump in terms of the viscosity of the pumped medium was particularly crucial for the owner of the Brazilian tank farm: “While centrifugal pumps have a narrow operating range and their efficiency reduces drastically as the viscosity increases, NOTOS ® multi screw pumps work across the entire viscosity spectrum with very good efficiency,” explains the Senior Sales Manager. “This pumping concept is based on the interaction between the screws and the housing. It forms conveying chambers in which the medium is continuously moved from the intake side to the discharge side at stable pressure – almost independent of medium consistency or viscosity.” The flow rate is influenced by pump speed, screw diameter and screw pitch. It is consequently directly proportional to the speed and can be variably adjusted through it.
Saving energy costs with more efficient pump technology
The pumps are adapted to the application at hand in order to achieve the best possible performance. This mainly applies to the pump size and its tolerances, but also to the accessories. Overpressure valves, a variety of different sealing systems and bearing monitoring devices using temperature and vibration sensors are available, for example. “For the application in Brazil, the viscosity of the medium in combination with the pump speed required a double seal with an external sealing system, as Vitor Assmann explains. At the customer’s request, this was designed to be API compliant.
As the 4NS can run with highly viscous media, no diesel injection was required. This in turn resulted in a cost reduction of US$2,000 per day. In addition, this pump runs much more efficiently with such viscous media, which reduced the power consumption by over 40 % to 65 kW. This saved even more energy costs – in particular because the second existing centrifugal pump was also replaced with a 4NS after the successful test phase in February 2020.
For more than 70 years, NETZSCH Pumps & Systems has served markets worldwide with NEMO® progressing cavity pumps, TORNADO® rotary lobe pumps, NOTOS ® multi screw pumps, PERIPRO® peristaltic pumps, grinding machines, barrel emptying systems, dosing equipment and accessories, providing customized, sophisticated solutions for applications in every type of industry. With over 2,300 employees and a turnover of 352 million euros (financial year 2022), NETZSCH Pumps & Systems is the largest business unit with the highest turnover in the NETZSCH Group, alongside NETZSCH Analyzing & Testing and NETZSCH Grinding & Dispersing. Our standards are high. We promise our customers “Proven Excellence” – outstanding products and services in all areas. We have shown that we can keep this promise time and again since 1873.
NETZSCH Pumpen & Systeme GmbH Phone: +49 8638 63-0 pr.nps@netzsch.com
Manufacturing & Engineering Magazine | The Home of Manufacturing Industry News