The Wallwork Cast Alloys foundry was set-up in 1986 to supply parent company Wallwork Group with heat resistant furnace jigs, fixtures and spares to meet their aerospace quality needs for heat treatment furnaces.
Across four sites in Manchester, Newcastle, Birmingham and Cambridge, Wallwork Group operates many furnace types and sizes including sealed quench and vacuum furnaces.
Meeting this constant need for bespoke jigs and furnace furniture means the foundry team has amassed a wealth of experience that they bring to customers. The team at Wallwork Cast Alloys understands the properties that are essential to make reliable high quality heat resistant castings.
Lesser known, is that the foundry apply this expertise to castings for other companies in wind turbines, offshore, chemical, aerospace, glass melting, decorative castings, plaques, and metal printing build plates. Being able to cast economically in low volumes is attractive to many potential users.
There are three predominant groups of alloys used in heat treating or high-temperature applications. These are chromium and iron based; chromium, nickel, and iron based; and nickel, chromium, and iron alloys.
Casting capacity ranges from 0.5kg up to 500kg including running systems and feeders. These can be produced as one-off or in multiple batches. Short delivery times at competitive pricing are supported by prompt reliable delivery and collection via the Wallwork Group nationwide commercial pick-up/delivery fleet. There is even provision for emergency delivery of castings on request.
Wallwork Cast Alloys holds extensive stocks of industry standard patterns for most major furnace manufacturers and bespoke ones for customers. They can manufacture castings from customer patterns and drawings, and also offer in-house CAD / Solidworks design and bespoke pattern making services.
Wallwork Cast Alloys, recently invested £120K in new sand recycling plant from FMS Ltd. Foundry manager Alex Beck explained, “Sand casting allows for smaller batches than permanent mould-casting and at a very reasonable cost. Sand may not seem the most important of materials, but even in a niche foundry like Wallwork Cast Alloys, there can be high costs around sand use, handling and disposal. We have calculated the £120K investment in the recycling plant will pay back in just 2.5 years. FMS have done a great job in tailoring the system to our needs.”
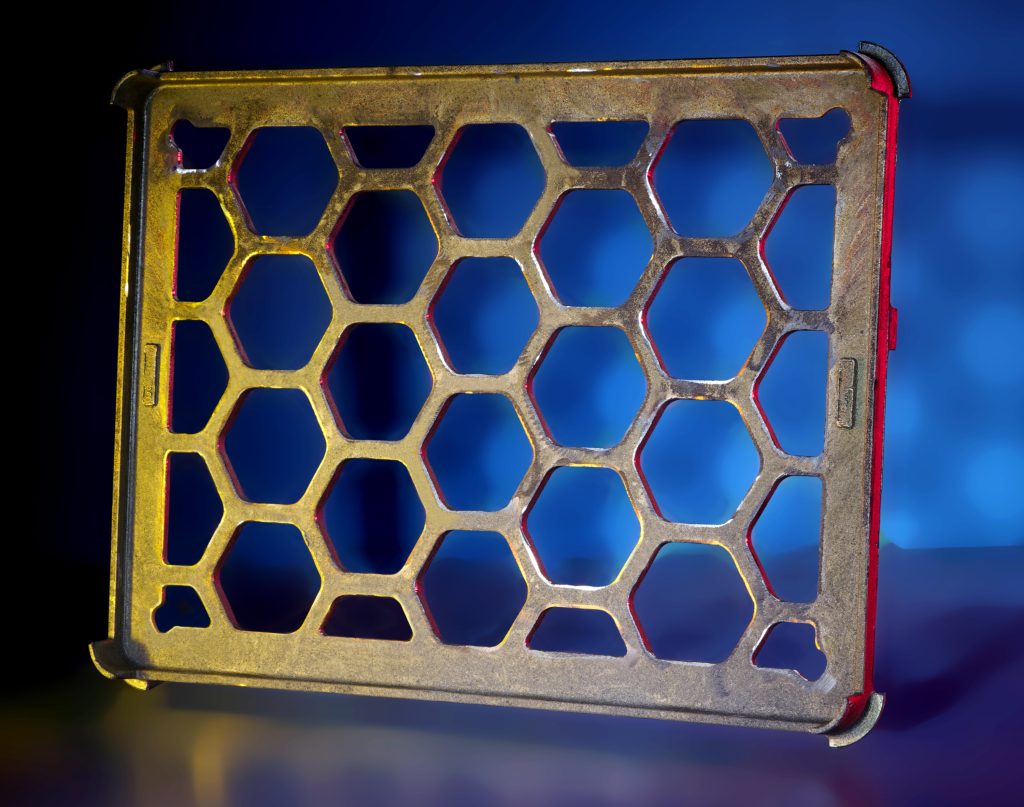
Recycling sand also gives greater flexibility in costing jobs for customers. Depending on the nature of the casting required, sometimes 100% new sand is essential. For other castings, reclaimed sand will work well. Blends of new and reclaimed sand can also be created that better suit the intricacy of the casting mould.
“While not a huge sand user, recycling helps to conserve its availability and reduces the environmental impact of sand mining and transportation. Reducing waste also reduces landfill use and associated costs. The energy required to recycle sand is generally lower than that needed to process and transport new sand and contributes to a smaller carbon footprint for the Wallwork Cast Alloys foundry operations,” said Alex.
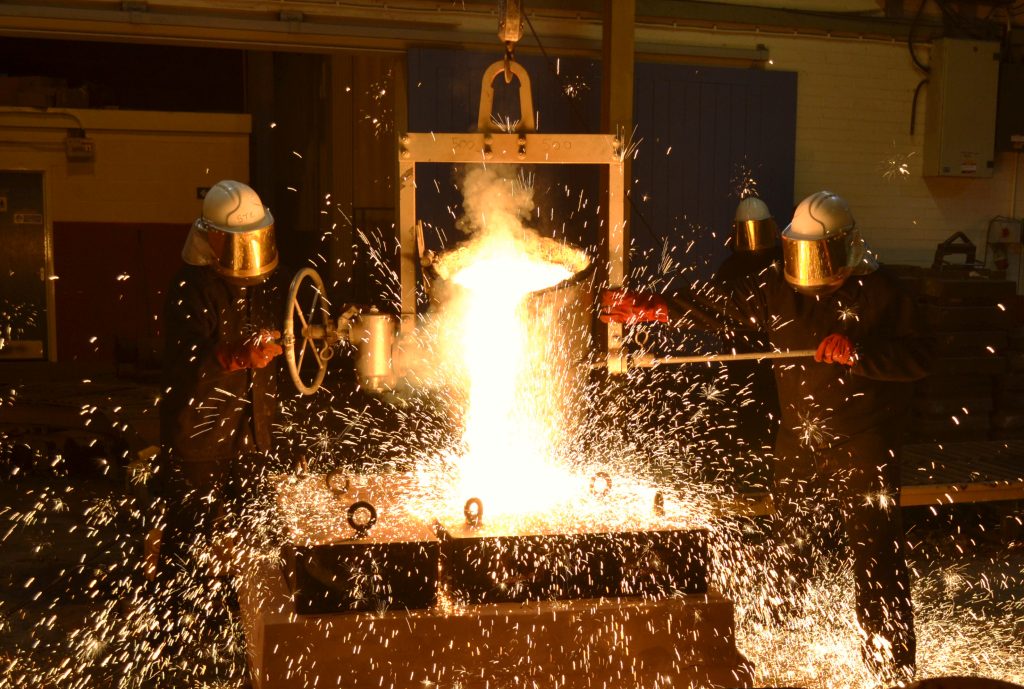
Alex concluded, “Quality is ingrained in everything we do, Wallwork Cast Alloys conform to ISO9001 accredited processes. Wallwork Group operates to the exacting standards of aerospace primes and component manufacturers, Nadcap and AS/EN9100. The foundry also shares the same high service ethic as the Group.”
Have a heat resistant casting project? Call Alex on 0161 763 7494.
More Information
Alex Beck, Foundry Manager, Tel. +44 (0)161 762 7494
E-mail: alex.beck@wallworkht.com Web: www.wallworkcastalloys.com
Manufacturing & Engineering Magazine | The Home of Manufacturing Industry News