Sheffield Opens Three Advanced Engineering Centres
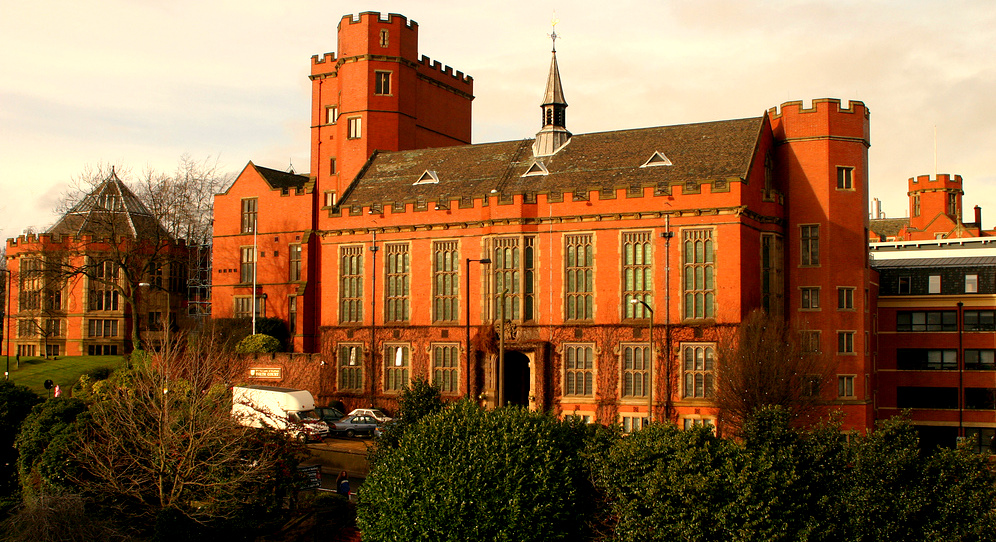
Three new multi-million pound research centres have been opened by the University of Sheffield in the region, aiming to further boost the city’s reputation as a hub for advanced engineering. The new centres could also boost the reputation of the Northern Powerhouse as a leader in advanced research, innovation and engineering. The Royce Translational Centre (RTC), the Laboratory for Verification and Validation (LVV), and the Integrated Civil and Infrastructure Research Centre (ICAIR) are all located within the Sheffield City Region’s Advanced Manufacturing Innovation District. RTC has been set up to evolve novel materials and processing techniques developed by research teams and make them accessible for trial by industry. It is home to Royce@Sheffield and the metals research group of AMRC, the National Metals Technology Centre (NAMTEC). LVV will enable research into the design and operation of advanced engineering structures when exposed to real-world vibration and environmental conditions, allowing testing of both full structures and substantial components. Experimental data, computer modelling and machine learning will allow industry to produce lighter, safer designs for a range of industrial sectors. ICAIR will enable experimental tests for investigating both underground and above ground constructed infrastructure. It can integrate data, AI, robotics and advanced manufacturing techniques to the field of infrastructure. The centres are working with companies to help develop new technologies, using research to cut costs and lead times, which could potentially transform industrial processes and businesses. They form part of a £47 million investment, part funded by the European Regional Development Fund (ERDF), UK research and Innovation (UKRI) and the University of Sheffield. The site is already home to the University of Sheffield’s Advanced Manufacturing Research Centre (AMRC) Factory 2050 – the UK’s first advanced factory, dedicated to conducting collaborative research, component manufacturing and developing machining technologies.
University of Sheffield Confirms £10m Investment from Science Research Council
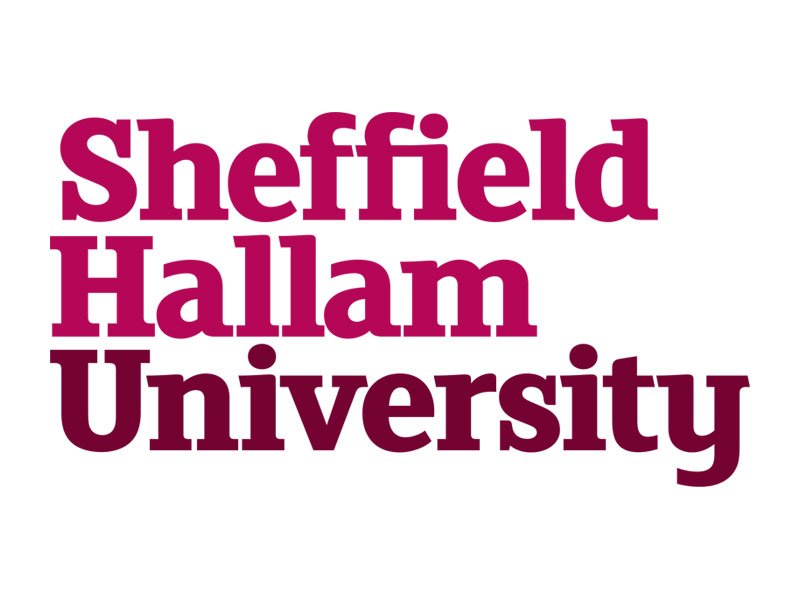
The University of Sheffield has confirmed a £10 million investment from Engineering and Physical Sciences Research Council (EPSRC) to lead The Manufacture using Advanced Powder Processes (MAPP) Hub. MAPP will focus on developing new powder-based manufacturing processes that provide low energy, low cost and low waste manufacturing routes and products for UK industry. MAPP, which will be part of the Sir Henry Royce Institute for Materials Research, will play a crucial role in unlocking the potential to use advanced powders in manufacturing processes. It will be led by Professor Iain Todd from the University of Sheffieldâs Department of Materials Science and Engineering. Speaking about the announcement, he said: There is a huge potential for manufacturing using advanced powders, however the industrial application of many processes is being held back by some fundamental science and engineering challenges, and they are not realising their potential. Our vision is to ensure that these game changing technologies deliver on their promise for UK industry. Todayâs announcement also named the University of Sheffield as a key partner in three additional Future Manufacturing Hubs – Advanced Metrology, Continuous Manufacturing and Crystallisation and Compound Semiconductors. It cements Sheffieldâs role in leading advanced manufacturing research in the UK – from developments in fundamental and underpinning science, through to translational research with industry partners. Vice-Chancellor of the University of Sheffield, Sir Keith Burnett, said: This investment recognises the vital role new technologies play in the security and growth of our high-value manufacturing sector – which must be a key component in the UKâs industrial strategy. Around the world, nations are determined to invest in next generation manufacturing and innovation. In the UK, Government is focusing on Industrial Strategy. This announcement is important because it shows how companies can become more productive and globally competitive by integrating the latest research into manufacturing processes. MAPP will focus on developing new powder-based manufacturing processes that provide low energy, low cost and low waste manufacturing routes and products for UK industry. MAPP, which will be part of the Sir Henry Royce Institute for Materials Research, will play a crucial role in unlocking the potential to use advanced powders in manufacturing processes. It will be led by Professor Iain Todd from the University of Sheffieldâs Department of Materials Science and Engineering. Speaking about the announcement, he said: There is a huge potential for manufacturing using advanced powders, however the industrial application of many processes is being held back by some fundamental science and engineering challenges, and they are not realising their potential. Our vision is to ensure that these game changing technologies deliver on their promise for UK industry. Todayâs announcement also named the University of Sheffield as a key partner in three additional Future Manufacturing Hubs – Advanced Metrology, Continuous Manufacturing and Crystallisation and Compound Semiconductors. It cements Sheffieldâs role in leading advanced manufacturing research in the UK – from developments in fundamental and underpinning science, through to translational research with industry partners. Vice-Chancellor of the University of Sheffield, Sir Keith Burnett, said: This investment recognises the vital role new technologies play in the security and growth of our high-value manufacturing sector – which must be a key component in the UKâs industrial strategy. Around the world, nations are determined to invest in next generation manufacturing and innovation. In the UK, Government is focusing on Industrial Strategy. This announcement is important because it shows how companies can become more productive and globally competitive by integrating the latest research into manufacturing processes.
Welsh Government to Invest £20m in Advanced Manufacturing & Research Institute
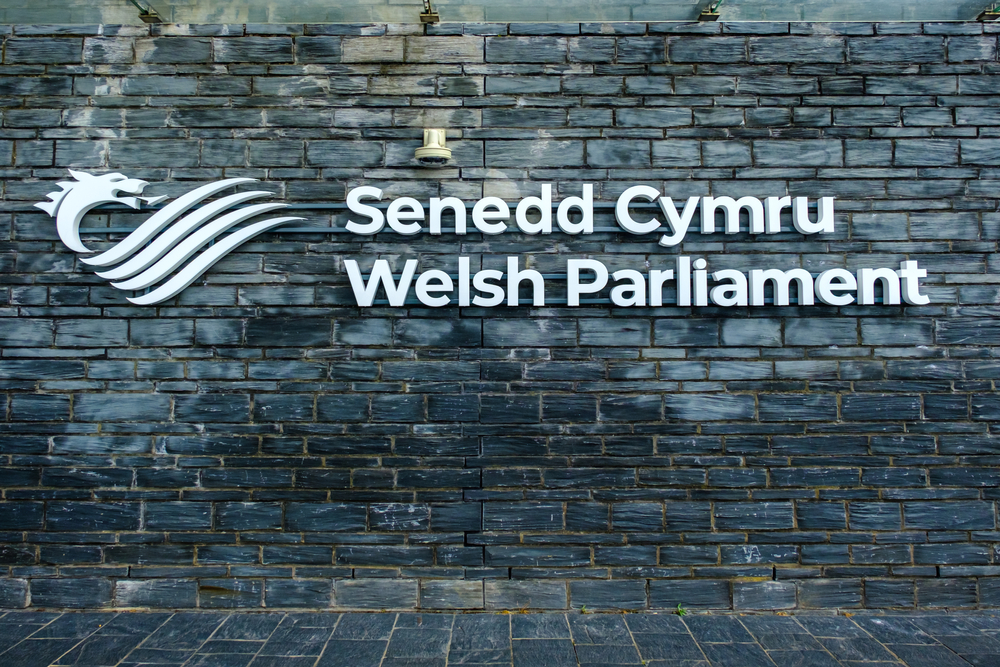
The Welsh Government is planning to invest £20 million in a new Advanced Manufacturing & Research Institute have been welcomed by Colin Sirett, chief executive officer of the University of Sheffield Advanced Manufacturing Research Centre (AMRC). The AMRC has worked with Deeside Enterprise Zone Advisory Board, Swansea University, and Coleg Cambria to develop the new Institute in conjunction with SMEs and large companies. The Institute will focus on research into and development of advanced manufacturing techniques and production processes for advanced manufacturing sectors including aerospace, automotive, nuclear and food. It will also address training and skills needs across industry. Announcing the investment, during a visit to the Airbus plant at Broughton, North Wales, Welsh Economy Secretary Ken Skates said: The Institute will deliver game-changing support to key manufacturing companies as well as multi-sector supply chain companies and the broader SMEs economy. It is geared to increase productivity, commercialisation, innovation and skills development to ensure a thriving competitive industry base that will be a catalyst for growth and jobs across the supply chain in Deeside, North Wales, the Northern Powerhouse and further afield. Airbus will be the anchor tenant for the new Institute, which will incorporate a state-of-the-art research and development facility at the European aircraft manufacturerâs Broughton plant, where it is working with the AMRC to develop new wing production technology as part of the Wing of the Future programme. AMRC CEO Colin Sirett said: The £20 million investment by the Welsh Government, combined with the £10 million from the project partners, will give an important boost to the competitiveness of the advanced manufacturing supply chain in Wales. The new instituteâs impact will go far beyond aerospace, supporting both the automotive and nuclear industries in Wales. It also encompasses sectors which have not traditionally been thought of as part of advanced manufacturing, which can, nevertheless, reap major benefits from the new techniques and technologies we will be developing. The Institute will operate as a single entity, split between a proposed 4,500 sq m state of the art hub R&D facility in Broughton and a 1000 â 1,500 sq m networking, training, business development and advice facility in close proximity to the Deeside Industrial Park. The Advanced Manufacturing & Research Institute is the latest in a number of collaborations the University’s AMRC is involved in around the world, including in Korea, China and the USA.
AMRC Launches AMOS Project to Develop Pioneering Additive Manufacturing Repair Technique for Aerospace Industry
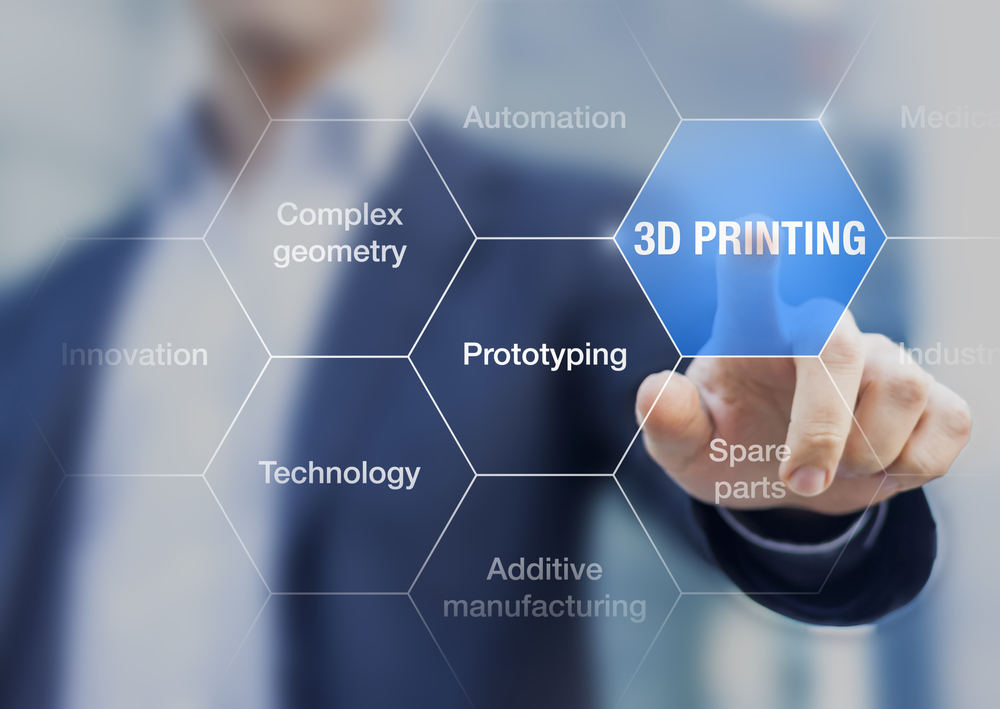
Experts in additive manufacturing at the Nuclear Advanced Manufacturing Research Centre (AMRC) are leading the way on a global scale in respect of developing pioneering repair and maintenance technologies for the aerospace industry. The research has been dubbed the AMOS project, a somewhat smaller a mouthful than Additive Manufacturing Optimisation Simulation platform for repairing and remanufacturing of aerospace components. It combines the intelligence, experience and resources of key manufacturers and researchers in Europe and Canada, and is led by University of Sheffield AMRC. The project is primarily geared toward exploring the potential of different direct energy deposition methods. The techniques entail combining conventional welding tools with automated control technologies with a view to increasing the accuracy with which metal powder or wire can be both deposited and melted. Since all manner of direct energy deposition techniques are evident across businesses within the aerospace sector â favoured for their ability to precision-manufacture parts to a degree elsewhere unseen â such research could provide the opportunity for further sector development and even open up AM technology to neighbouring sectors. The AMOS project will look specifically at those technologies already in use by partner or available on the market. Processes up for investigation and potential improvement include the wire-feed gas tungsten arc process, currently utilised for manufacturing the Nuclear AMRCâs bulk additive cell. Indeed, the Nuclear AMRC forms a key driver for the research and experts may well look into further technologies made use of by the research hub, including other AM techniques such as powder diode laser. From their investigations and research, industry professional and scientists alike are hoping to identify a way in which AM technology can be used to repair key aerospace components like landing gear and turbine blades. If found successful, such innovation could reduce both the time and cost associated with repair and maintenance works considerably. The initiative would could also improve the environmental identity of the sector as a whole, minimising material wastage during the process and, furthermore, prolonging the life of components which are both expensive to manufacture and properly dispose of. Dr Rosemary Gault, European Project Coordinator at the University of Sheffield AMRC was keen to stress the importance of the research, highlighting that while the sector is wholly dedicated to innovation, particularly in additive manufacturing, there is little focus on developing technologies specifically for repair and maintenance. Hoping to fill the gap, the AMOS project will inspect closely the various stages and aspects involved within the additive manufacturing process. Of significant interest will be how to maintain the integrity of the metal deposited as well as how to improve the precision of the deposition process, itself. With the help of technology specialists, researchers will also be looking to identify the advantages that automated control technologies represent to additive manufacturing technology in addition to fine-tuning the assembly of the net to produce a final, seamless â and therefore more durable â shape. As a final aside, and perhaps as a result of those findings, the AMOS project is expected to draw conclusions as to how strategies of additive manufacturing repair can be incorporated within the design of components in order to further improve efficiencies and lengthen the life cycle of parts. As such, it may well mark the creation of industry-complaint, best practice method with which to repair and maintain aerospace parts. The AMOS project consortium comprises a total of nine partners, spanning the globe from Canadian universities â McGill and Ottawa, and three further aerospace manufacturers, to Franceâs Central de Nantes and DPS. Also in the line-up are Swedenâs GKN Aerospace Engine Systems and, of course, the UKâs AMRC. It is thus made up of some of the biggest names in the sector and brings together the knowledge and specialisms of top research organisation, tier one manufacturers, and additive manufacturing and technology professionals. With such a broad range of high level expertise, it is unlikely the project will prove without positive conclusion.