Showcase Innovation at the UK’s Largest Annual Engineering Event

Advanced Engineering is on the lookout for start-ups to showcase their inventions as part of its innovation zone. As the UK’s largest annual exhibition for manufacturers and supply chain professionals, the Enabling Innovation Zone will support smaller enterprises that are eager to accelerate their innovations into the advanced manufacturing and technology industries. Supported by Innovate UK/KTN, Advanced Engineering is searching for growing businesses to exhibit their disruptive technologies and inventions on the show floor. Start-ups across all engineering sectors, whether that be aerospace, automotive, marine, medical, automation or any other industry, are encouraged to apply. We expect to see some of the most exciting technologies including novel materials, automotive and autonomous technologies. The opportunity, which is free of charge for successful applicants, will give innovators a platform to showcase their inventions to thousands of key industry players from a range of notable companies. From senior directors and engineers to research and development specialists, chief technology officers and investors, a wealth of influential people spanning across the world’s most renowned manufacturing businesses will be visiting the zone. Successful applicants will receive a branded plinth in the Enabling Innovation Zone to display their technologies, along with full marketing support in the show’s catalogue, on its website and across its PR campaigns. During the show, exhibitors have the chance to gain further recognition as visitors will be able to vote for their favourite innovation, with the winner announced ahead of the show’s closure. “Following the success of the Enabling Innovation showcases, this dedicated zone will act as a springboard for new and exciting technologies,” explains Jeremy Whittingham, Head of Marketing at Advanced Engineering. “As we are establishing an entire area of the show for such innovative businesses, the impact the zone will have is bound to surpass that of previous years and encourage the growth of even more innovations”. Previous showcases have been instrumental in accelerating business growth. Listed in Forbes 30 Under 30 Class of 2017, previous winner Aceleron has revealed that the showcases played a key role in the company’s business development. “It played a crucial part in establishing our credibility and had a direct impact on at least five business relationships we have today”, said the advanced lithium battery developer. Is your business ready to showcase its innovation? To submit an application, please complete this short form or email Jeremy.whittingham@easyfairs.com. For more information visit www.advancedengineeringuk.com Manufacturing & Engineering Magazine | The Home of Manufacturing Industry News
XYZ Machine Tools Posts Another Record Year
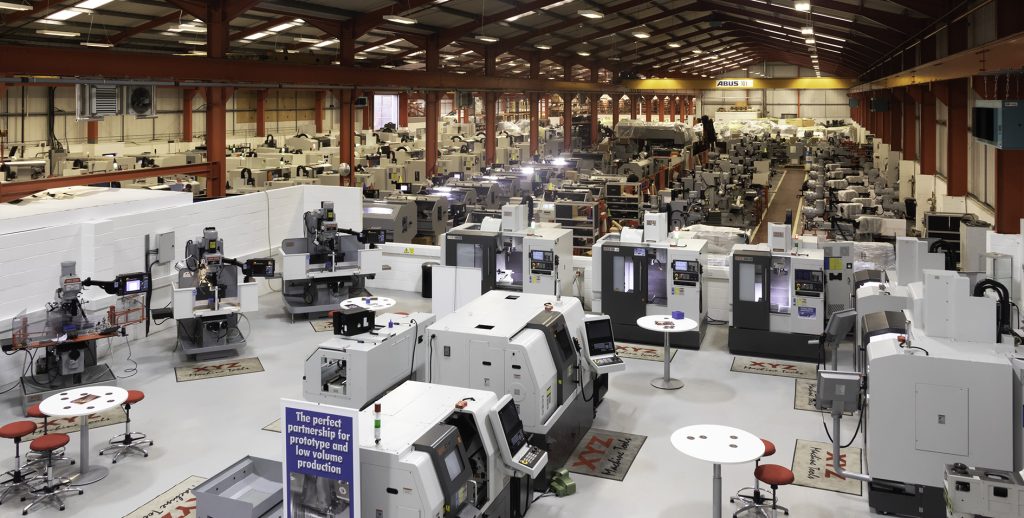
XYZ Machine Tools has continued its record breaking run of year-end results posting an 11 per cent increase in turnover for 2018/2019, taking it to a significant £33.9 million. This growth reflects what is continuing optimism within the UK manufacturing sector, along with increased sales within the education sector and mainland Europe. This optimism is reflected by 33 months of sustained growth in the sector highlighted by the Purchasing Managers’ Index (PMI) which remains resolutely above 53 and the Bank of England has upgraded its growth forecast. On top of this inward investment also remains robust and with that comes greater demand for machine tools. A recent survey by the organisers of the SUBCON show suggests that some 65 per cent of manufacturing businesses are positive about investment. “There is some amazing positivity in the manufacturing sector at the moment, despite the uncertainty that our politicians are generating around Brexit,” says Nigel Atherton, Managing Director XYZ Machine Tools. “Our sales have been bolstered by a mix of the optimism in the sector along with the introduction of new products to our portfolio such as the LR series of vertical machining centres, our two UMC five-axis machining centres and the latest generation of ProtoTRAK RMX and RLX controls for our mills and lathes. Put simply we are meeting the needs of our customers with machines that are both price competitive and highly productive.” The coming year is also one of optimism for the Burlescombe, Devon-based machine tool company with order books remaining encouragingly strong and plans in the pipeline for more new product developments, along with the opening of a new showroom in the north of England. Manufacturing & Engineering Magazine | The Home of Manufacturing Industry News
Manufacturers’ Sales Performance Needs Rapid Transformation
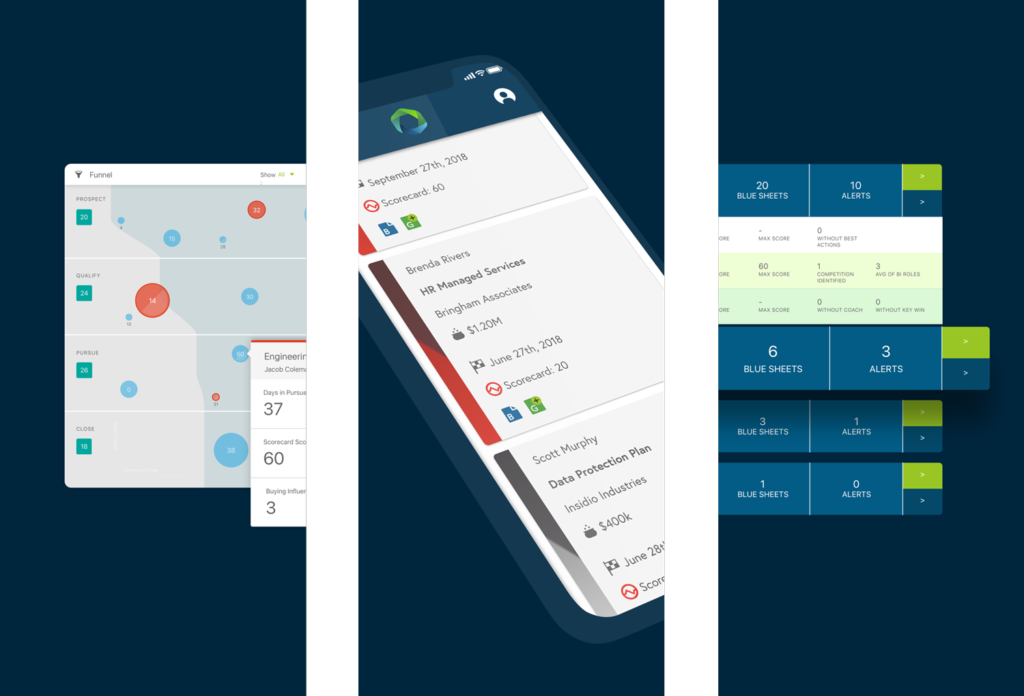
Miller Heiman Group, the world leader in improving sales performance through training, consulting, technology and research, reveals in a report that manufacturing organisations must re-train sales teams to provide perspective and value, in addition to technical expertise, if they’re to survive the changing and volatile European landscape. The report includes a survey of 103 manufacturing sales leaders worldwide. Manufacturing currently accounts for 15 percent of European GDP, but with €17 billion in funding earmarked for industrial leadership by the European Union’s Horizon 2020 programme, that number will likely jump as more companies incorporate advanced robotics, sensors and other advanced technologies. Given the investments that many countries plan to make, understanding the unique challenges that European manufacturers face will be key to supporting its current and future salesforce. Top Challenges in Manufacturing Sales Performance In the 2018-2019 Sales Performance Report, CSO Insights, a division of Miller Heiman Group, surveyed manufacturing sales leaders globally on what they viewed as the factors that needed major redesign or improvement for closing new business and managing existing accounts. It identified the following: Top 5 Challenges for Closing Business Identify and gain access to all decision makers (72.2%) Conduct thorough needs analysis (71.2%) Build solid business case/ROI for solutions (68.0%) Develop and execute opportunity plan (68.0%) Provide perspective which helps customers advance thinking (62.0%) Top 5 Challenges for Managing Existing Accounts Penetrate other business units within existing customers (72.2%) Generate referrals from existing customers (67.0%) Develop and execute account plans (65.7%) Create and maintain case studies and references (65.7%) Effectively cross-sell and upsell (56%) The report also identified three main external challenges that are affecting European manufacturers’ ability to sell: Firstly, a globalised manufacturing market means greater sensitivity to geopolitical factors, causing even the most informed seller to be overwhelmed by issues such as Brexit. Secondly, while not a new problem, without a thorough understanding of a customer’s end goals and priorities, sellers will find it nearly impossible to overcome price competition from lower-cost Asian manufacturers that they’ve battled for decades. Thirdly, the high-quality standards required for the aerospace and defence sectors make them a natural fit for European manufacturers, however stakeholders are conservative and prioritise safety, meaning contracts take longer to negotiate and finalise.
Business Support Boost to Unlock SME Manufacturing Potential
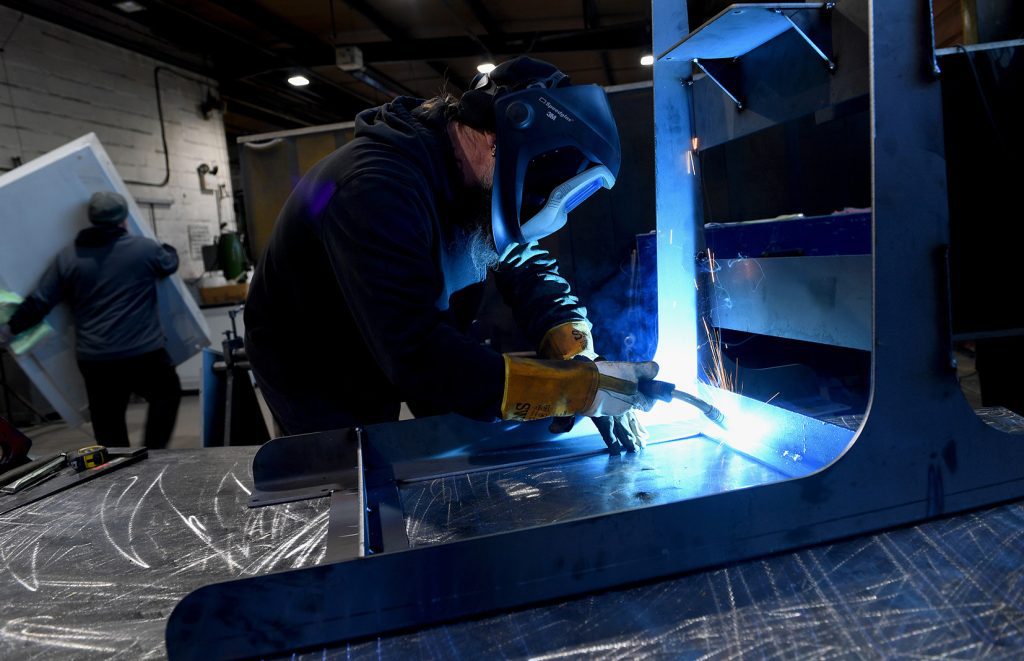
Small to medium-sized (SME) manufacturers across England have been awarded an £11.8 million business support boost, dedicated to helping them grow and address key skills issues. The Manufacturing Growth Programme, which is funded by ERDF and delivered by Economic Growth Solutions (part of Oxford Innovation), has been extended until September 2021 and will help a further 2400 companies to tackle barriers to growth, with the potential of creating 2500 new jobs. Going forward, support can be used for an array of improvement projects, such as continuous improvements, change, environmental and sustainability, leadership and management, marketing, people and skills, productivity and capacity, quality and strategy. The additional funding aims to provide a more valuable and quality level of assistance from a local Manufacturing Growth Manager that has years of industry experience. An in-depth business diagnostic (via ‘GROWTHmapper’) and comprehensive action plan will be provided as part of the new programme, alongside improvement grants starting from £1000. In response to company feedback, a series of manufacturing themed workshops have also been added and will be available from Summer 2019 to help bridge current skills needs within manufacturing businesses and support future skills requirements in line with Industry 4.0. “In October 2016, we were given the task of setting up a programme capable of delivering over £10.3m of dedicated business support to SME manufacturers and I’m delighted to say that, thanks to the hard work of the staff and the Manufacturing Growth Managers on the ground, we have achieved that,” explained Martin Coats, Operations Director of Oxford Innovation. “Over the course of the last two and a half years we have helped more than 2000 SMEs to identify and overcome barriers to their growth and this has added millions of pounds to the local economy and created in excess of 3000 jobs, safeguarding thousands more in the process.” He continued: “Supporting manufacturers is not easy and you need a tailored approach, delivered by experts who understand what it is like working in industry. “The Local Enterprise Partnerships (LEPs) and local Growth Hubs have seen first-hand the value we add to firms in their respective areas and this has resulted in their commitment to support us for another two and a half years. “To make the most of this, we have joined forces with Oxford Innovation to deliver the extension of the programme and this will make us the country’s largest business support organisation, primarily focusing on manufacturing.” The Manufacturing Growth Programme is available to small to medium-sized manufacturers who have an intention to grow, increase competitiveness and improve productivity while increasing turnover, creating new jobs and introducing new products/services and processes. It is available to businesses in the West Midlands, Yorkshire and Humber, parts of the East Midlands, the South East and now within the Solent and Enterprise M3 regions. Dean Barnes, Regional Director of the Manufacturing Growth Programme added: “The £11.8m extension will provide enhanced support to more SME manufacturing businesses, as well as having the opportunity to add further value to those companies we have already supported. “Our Manufacturing Growth Managers are trusted experts that understand the language MDs are talking and, through a new manufacturing diagnostic tool, can guide them on making the right decisions, before bringing in specialists on specific issues they are facing or opportunities they’re looking to explore.” He concluded: “Accessing MGP has never been easier. The process is slick, the scope of support is tailored to each company’s needs, the diagnostic provides an in-depth look into their business and the results, as already proven, are making a real difference in terms of increased turnover, jobs and new products/processes.”
Redditch Manufacturer One of the First for ISO 45001 Accreditation
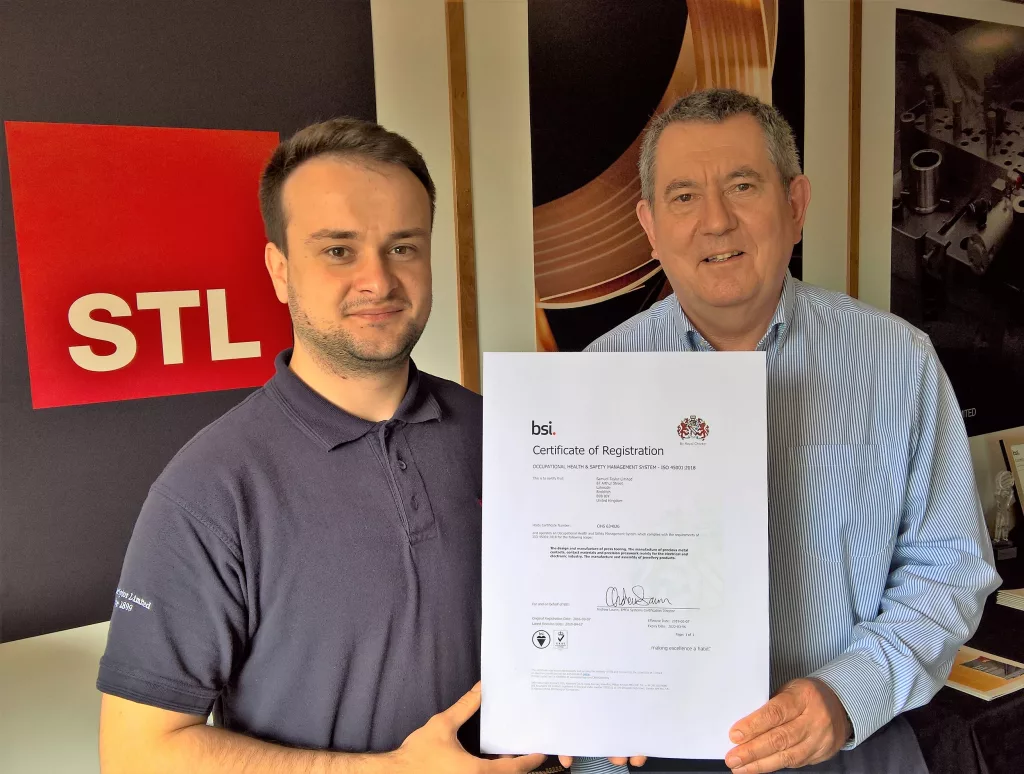
Redditch-based presswork and metal contact specialist Samuel Taylor Limited (STL) are one of the first 100 companies in the UK to attain the conversion from BS18001 to ISO45001 standard accreditation for Health and Safety. The feat also makes STL one of the first manufacturers in the UK to achieve ISO 45001, demonstrating the company’s ongoing commitment to maintaining a world class, safe working environment. The new ISO standard helps organizations by providing a framework to improve employee safety, reduce workplace risks and create better, safer working conditions. The process towards compliance was a team effort of STL Company Secretary Richard Pick, Quality Assurance Manager Bogdan Dumitru and Production Manager Paul Booth, as well as external consultants Temple Quality Management Systems. However, STL Quality Assurance Manager Bogdan Dumitru emphasizes that the key to successful transition was the commitment of all employees: “The journey to ISO 45001 accreditation was very much an employee led approach, placing a significant emphasis on employee participation and consultation. Employee input is essential in order to develop effective ways of protecting our workforce. If employees are given the opportunity to participate in shaping safe work systems, particularly by getting involved at the planning stage, they are more likely to identify the reasons for taking a particular action, help find practical solutions, and comply with the end result”. Company Secretary Richard Pick adds: “Obtaining the ISO 45001 certification was a direct follow up to the OHSAS 18001 accreditation, which STL already held. Therefore, the transition to ISO45001 took only 3-4 months, since the back bone of the integrated management systems were already in place. “We are fortunate at STL to have a talented, loyal workforce. Gaining the accreditation demonstrates our ongoing commitment to maintaining a safe, efficient working environment for the people that we value the most”. Manufacturing & Engineering Magazine | The Home of Manufacturing Industry News
Inspekto and Cosmo EU Announce Partnership at Control 2019
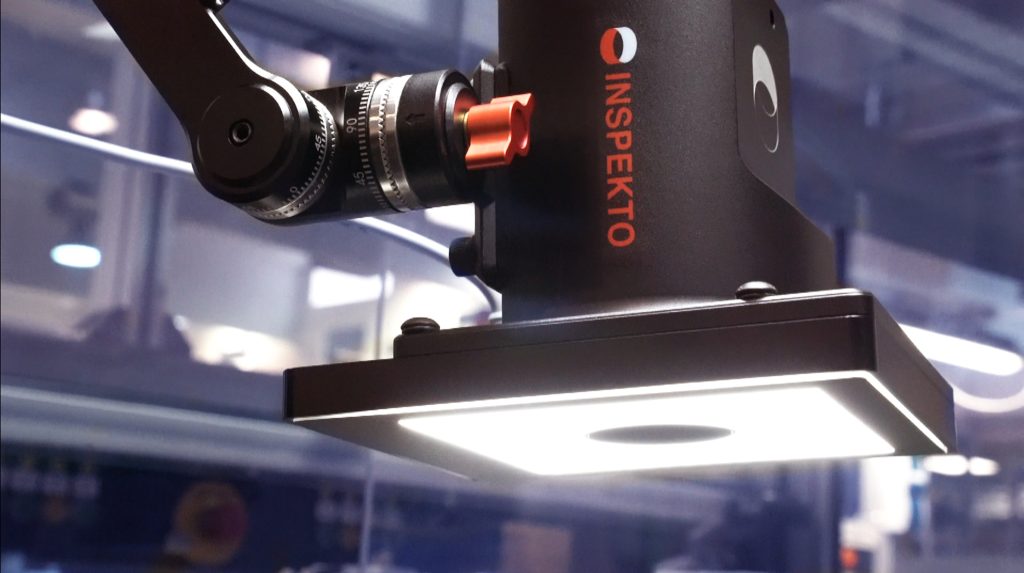
To offer the latest in quality management to its clients, Cosmo EU will showcase live the Autonomous Machine Vision INSPEKTO S70 system at Control 2019 in Stuttgart, Germany, from May 7 to 10. Cosmo EU is an international leading industrial testing company, with more than 40 years of experience in the sector. At Control, Cosmo EU will exhibit a wide range of their products. These include their DF-2820 laminar-flow sensor, flow testers such as the AR-R220, and leak testing devices such as the LS-R902, the LS-R700 and LS-R910. All of these devices will be shown in operation on stand 6220 in hall 6. With the INSPEKTO S70 Autonomous Machine Vision system, Cosmo EU is making a strong move into the quality inspection sector, providing its many customers with an inspection system that is 1000 times faster to install, at 1/10 the price than any traditional solution. The two companies will be demonstrating an installation deployed at a world-leading German automotive manufacturing brand. The installation provides inline quality assurance for inner cylinder bores: Cosmo devices make sure that a cylinder bore is fully sealed, while the INSPEKTO S70 System establishes if the milling is accurate and if the various assembly parts are mounted correctly. “The collaboration between Cosmo and Inspekto eliminates integration-related difficulties for the final customer,” explained Thomas Porysek, CEO of Cosmo EU. “In fact, the two devices integrate seamlessly, meaning that they can provide our customer with a system that is ready to be used and offers the double advantage of efficient leak testing and Autonomous Machine Vision.” “Control is the ideal venue to launch this exciting partnership,” added Harel Boren, CEO of Inspekto. “The collaboration between our two firms opens new paths for the industry, providing Cosmo’s clients with a unique quality assurance (QA) system that combines the precision of Cosmo’s leak detecting devices with the convenience of Total QA. This also brings additional impact to customer-lines productivity and profitability.” The INSPEKTO S70 system is already in use at plants of leading manufacturers in a variety of sectors. Less than six months after launching, Inspekto has a commercial footprint of over 2,871 industrial plants worldwide and is the leader in Autonomous Machine Vision. For more information, visit www.inspekto.com. Cosmo EU is an international leader in leak, flow and ring testing for numerous applications. Among their clients are world-wide renowned companies from the automotive sector, the chemical and pharmaceutical industry, the food industry, and electrical engineering.
Covestro Expands Its Production Lines
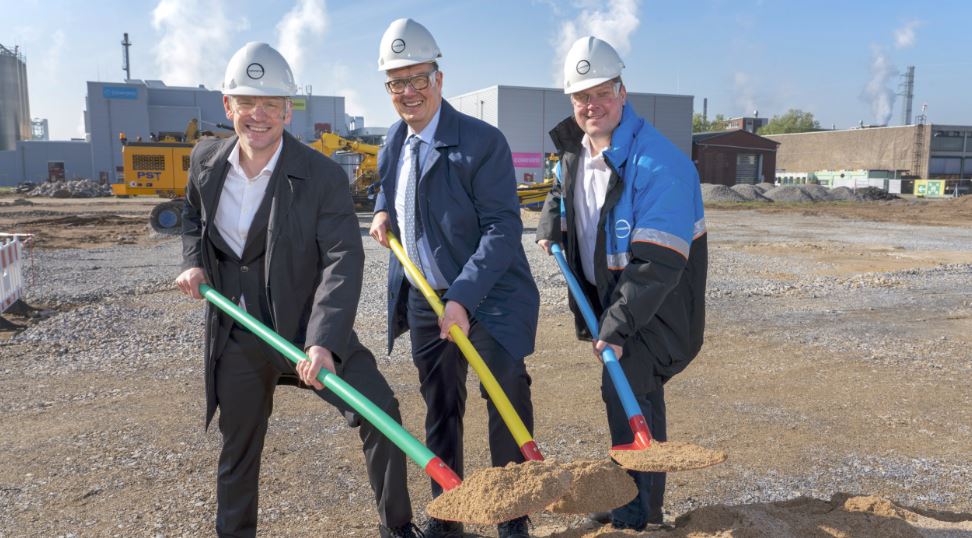
An expansion project has been launched by Covestro AG to add new production lines for high-quality polycarbonate films at its manufacturing site in Dormagen, Germany. Part of the company’s €100 million global capacity expansion plan, the investments aims to help meet growing demand in all regions. The project has been scheduled for completion by the end of 2020, including the addition of new coextrusion lines for the production of multi-layer flat films. The new manufacturing unit further underscores the Dormagen site’s importance as a competence centre for speciality films, according to chief technology officer Dr. Klaus Schäfer. The company is investing in “promising” technologies and applications, such as in cars, medical products and security cards, announced Covestro. By employing “the latest technology”, the plant will enable Covestro to supply customers “faster and with higher quality,” explained Dr. Thorsten Dreier, global head of Covestro’s film business. The company, said Dreier, is currently working on several projects and the new manufacturing unit will help bring them to market maturity faster. The multi-layer flat films to be manufactured at the site are increasingly used in identity documents as they can embed security features while offering protection against counterfeiting. Covestro’s Dormagen facility specialises in polycarbonate flat films, and comprises production, a technical centre for film processing, a showroom and research laboratories. Covestro announced plans to expand its global film business in July last year, which were then said to include investments in Thailand, China, Germany and the US. In Thailand for example, the company is currently building a new production facility in Map Ta Phut, with completion set for the end of the year. The company is also progressing well with the conversion of its coextrusion line in Guangzhou, China, with first products already being delivered to customers. Covestro expects to build new films capacities in China in the second phase of the expansion plan. In the US, the company said it has already improved efficiency and expanded its film production unit in South Deerfield, Massachusetts.
Why RFID Is the Future of Tool Tracking
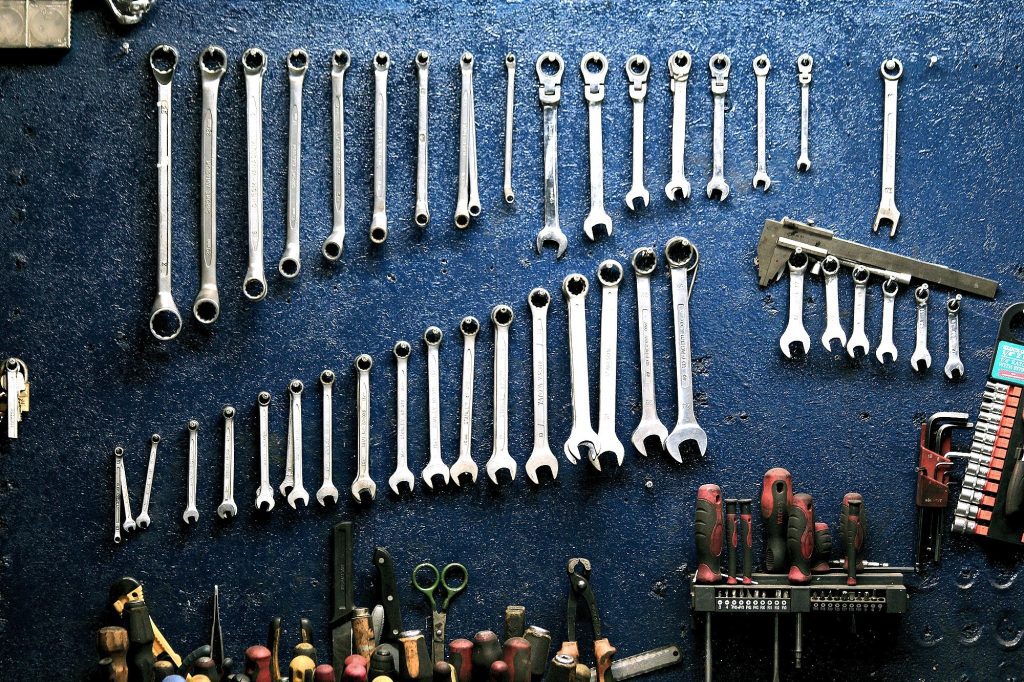
Radio Frequency ID (RFID) technology has transformed supply chain management over the past two decades; yet the limitations of fixed readers in both accuracy and range have constrained deployment, leaving many organisations reliant on the more accurate but resource draining manual handheld readers. As organisations in every sector wrestle with the challenges of customer expectation/ cost pressures / regulatory demands, Sabesan Sithamparanathan, Founder and CEO, PervasID, explains how the near 100% detection accuracy and extended range of the next generation of fixed RFID readers will enable retailers/ medical providers/ manufacturing/industrial firms to automate every aspect of the supply chain and drive tangible operational benefits. Lack of Control For manufacturing companies, the ability to track tools throughout the workplace is essential – not only from a cost management perspective but also regulatory compliance. No firm can afford to discover key items have been left on site – especially if that site is an airplane engine. The use of RFID tags would appear an obvious solution. To date, however, the limitations of fixed RFID reader technology, especially in this ‘tag dense’ environment, has deterred adoption. Traditional fixed readers have been unable to deliver the detection accuracy required to justify investment. In any area with a high number of RFID tags, from medical equipment storage to industrial tool boxes or retail stores, there are simply too many dead spots due to signal reflections: the more tags, the lower the accuracy. At best in these environments, detection capacity can reach 85-90%. Add in the limitation in reliable read distance – typically no more than 2-3 metres, plus the time it can take to complete the read process – several weeks in a retail store, and fixed RFID readers have been unable to demonstrate a compelling business case. Yet the demand is clear: Organisations want the ability to remotely and continuously track items in any location. They want to leverage the item level information provided by RFID to support better supply chain control, drive down stock and asset levels, lower losses, improve customer satisfaction and automate regulatory compliance. And they want to do this without the manual overhead associated with hand held or carriage-based RFID readers, or the significant – and unaffordable – cost associated with Active tag solutions. Accuracy Transforms Business Case The latest generation of fixed RFID reader technology addresses all of these limitations by using advanced signal processing to dynamically move the dead spots and achieve near error-free system. In addition to eradicating dead spots and achieving close to 100% accuracy, this game changing approach also extends the read distance to up to 20 metres, enabling one reader with five antennas to cover up to 400 square metres. Furthermore, with the addition of location functionality, the next generation RFID reader system shows in which zone a tagged item is located, enabling organisations to inexpensively and effectively monitor RFID tagged items over large areas With a wider read range, better detection accuracy and fewer antennas, this approach fundamentally addresses the previous constraints to RFID adoption. For manufacturing and industrial companies, the ability to accurately read an entire toolbox in real-time transforms the process: the toolbox is read as it is opened; an engineer removes the specific tools required, closes the box, and it is read again – providing a complete record of what items have been removed, when. The process is completed in reverse when the items are returned, providing not only an audit trail of items used, by whom, but also the essential regulatory safeguard to ensure equipment is not left in situ during maintenance.
Pump Industry Awards Announces Winners
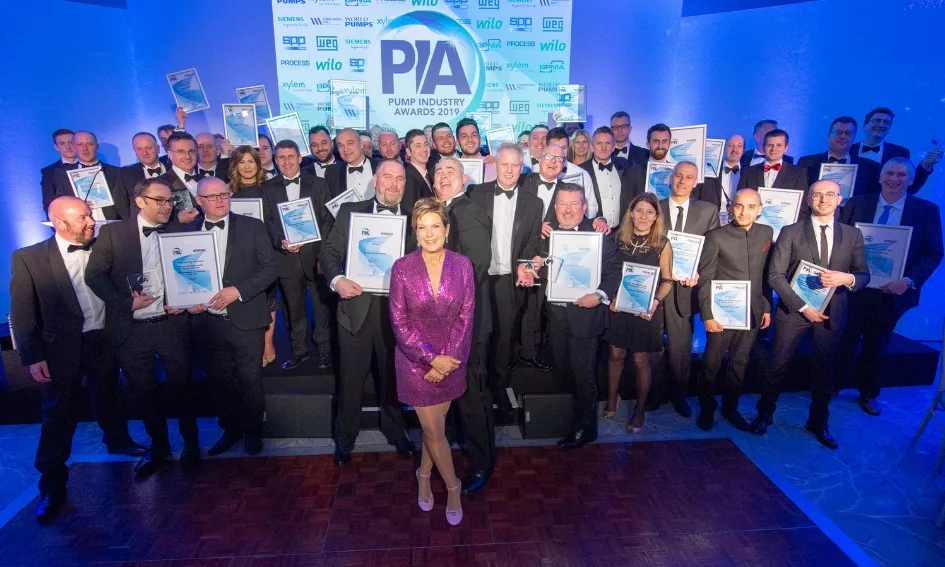
The 2019 Pump Industry Awards organised by the British Pump Manufacturers Association has crowned its winners. The ceremony staged at Heythrop Park Resort in Oxfordshire and led by host, presenter Penny Smith together with BPMA president Richard Harden, featured nine winner categories. Xylem’s Flyght concertor won the Product of the Year category, while Tomlinson Hall scored a double, winning distributor of the year plus a Lifetime Achievement award for MD Tony Keville. The full list of winners includes: Product of the Year sponsored by Process Engineering: Xylem Water Solutions for its Flygt Concertor XPC Projects of the Year sponsored by Wilo: Campion Pumps and Irish Water – Inniscarra Dam Project Environmental Contribution of the Year. sponsored by SPP Pumps, Armstrong Fluid Technology – Armstrong Tango Parallel Pumping Solution. Manufacturer of the Year sponsored by Siemens: Wilo UK Distributor of the Year sponsored by WEG: Tomlinson Hall Supplier of the Year sponsored by Xylem Water Solutions: John Crane Engineer of the Year sponsored by World Pumps: SPP Pumps – Reuben d’Orton-Gibson Judges’ Special Award sponsored by Tomlinson Hall: Siemens Lifetime Achievement Award, sponsored by BPMA: Tony Keville, MD Tomlinson Hall “We’re delighted our award has gone to such a deserving winner and send our congratulations to all this year’s finalists and winners,” said Process Engineering commercial director Mike Turner, who presented the Product of the Year award. Manufacturing & Engineering Magazine | The Home of Manufacturing Industry News
Dairy Manufacturer Considers Plant Closure
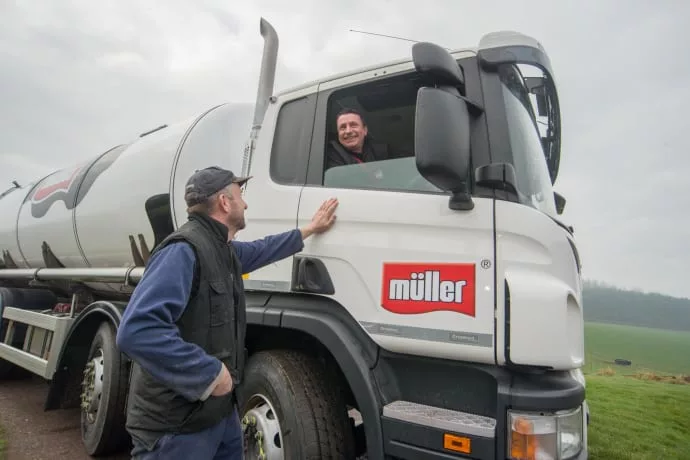
In an attempt to save £100 million, dairy giant Müller is considering closing one if its manufacturing sites. Müller Milk & Ingredients has announced plans to review its network of dairies as part of its Project Darwin programme, which was launched in February. A 45-day consultation process will be starting to assess the current and future utilisation and capacity requirements at its network of six dairies and then the outcome could be determined. The six dairies under review are Bellshill in Scotland, Manchester, Foston, Droitwich, Severnside and Bridgwater. “Project Darwin is making excellent progress with the whole workforce fully engaged in securing a vibrant, progressive future for our fresh milk business and very positive collaboration with customers who share our desire to reinvigorate this important sector,” said Müller Milk & Ingredients chief executive Patrick Müller. “It is a matter of considerable regret that we must consult on steps which could result in a restructuring of our dairy network and capacity but we must ensure the sustainability of our business and address potential over-capacity in our network,” he continued. Furthermore, the business has also revealed plans to enter a logistics partnership with Culina Group, a Müller Group sister company. From 1st June Culina Group will assume day to day management control of MMI Distribution and all 2,500 employees will remain part of Müller UK & Ireland and will see no change to their terms and conditions of employment. Responsible for MMI Distribution and all of the current MMI logistics leadership team will be Ian Smith of Culina Group. MMI Distribution will assume control from the point that vehicles have been loaded for delivery at MMI’s network of six dairies to the point that products are successfully delivered directly to customers or to our network of depots. Tanker operations bringing milk from farms to MMI’s dairies will continue to be managed by MMI, as before. “The distribution business partnership with Culina Group, a sister company within Müller Group, will put together the two major chilled logistics networks in the UK, ensuring that we can further build upon our reputation for great customer service at the lowest cost,” added Patrick Müller. Manufacturing & Engineering Magazine | The Home of Manufacturing Industry News