Luxonic Reveals Company’s Expansion Plans in Basingstoke
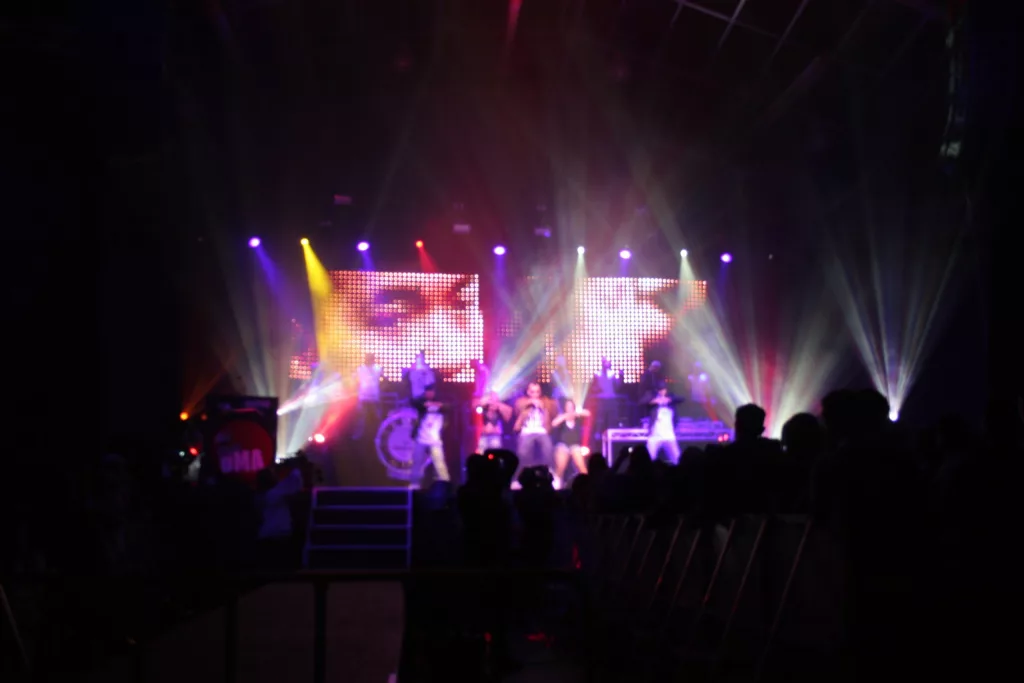
Lighting designer and manufacturer Luxonic has revealed its plans to expand the companyâs headquarters in Basingstoke after the business hailed record financial results from what it called a “landmark year”. Construction work has begun on the new site, which will include more than 17,000 sq ft of space and will be split into two areas – one for storage and the other for production. Production is expected to start early next year and be fully populated by the middle of next year. Nick Tavare, Managing Director, commented: “We are all very excited for the Basingstoke expansion. “At every stage of planning, the emphasis has been on building a hub for production that utilises lean manufacturing methods, and will improve the output efficiency of all our luminaires, whilst maintaining the high level of quality Luxonic is synonymous with.” The expansion has come on the back of a “commercially and financially successful year” for Luxonic. Earlier this year, the company celebrated its 30th anniversary with a rebrand and new offices in Glasgow and London. After this came Luxonic posting record profits after sales soared past the £20 million mark for 2015/16, a rise of nearly 30% from the previous year. Tavaré added: “Luxonic have had a fantastic 2016, with a fresh rebrand and new offices alongside unprecedented financial accomplishments. “The Basingstoke expansion continues our rise as the UK’s leading luminaire innovator, and will allow Luxonic to keep producing forward-thinking, high quality products and delivering excellence in customer service into 2017.” Two years ago, Luxonic expanded its production facilities in Basingstoke to meet a rise in demand for LEDs. Soon before this the company completed a 10-month project, costing around £750,000, by consolidating its manufacturing on to one site at its Priestley Road headquarters. Managing director Nick Tavaré said the work required extensive re-organisation of the factory, where two mezzanine assembly areas have been installed increasing the production area by 30 per cent. The investment also included new automated equipment. Manufacturing & Engineering Magazine | The Home of Manufacturing Industry News
H.C. Starck Appoints New Executive Board Member
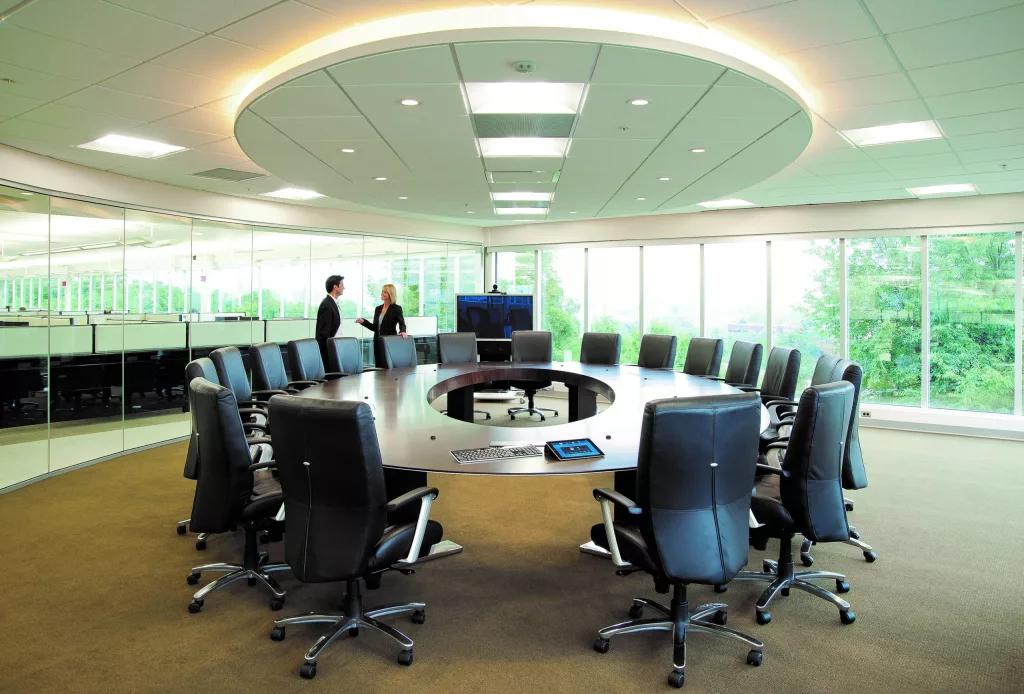
Global manufacturer of metal and ceramic powders, H.C. Starck, has appointed Dr Dennis Schulze to serve as a member of the executive board and chief financial officer of the firm. Dr Engelbert Heimes will stay on as chairman of the executive board of the group on an ongoing basis. Schulze will replace Dr Matthias Schmitz, who is leaving the business to take on a new professional role. Schulze served as CFO of Douglas Group for the last three years. Between 1999 and 2012, he worked at The Carlyle Group, most recently as a managing director in Germany. Dr Heimes said: We look forward to working with Dennis Schulze. His broad experience in Private Equity and financing will be a great asset to the further development of the H.C. Starck Group, which he is already familiar with from his time at Carlyle. Schmitz joined H.C. Starck Group in July 2014 as member of the executive board and financial director. During this time, he made substantial contributions to the companyâs further development, including the groupâs successful refinancing, the company says. Dr Heimes added: We sincerely thank Matthias Schmitz for all his hard work and dedication to the H.C. Starck Group. Meanwhile, Dr Jan Lösch has now been appointed to the executive management of HC Starck GmbH, where he will serve as managing director. He will have responsibility for accounting and controlling. Dr Jens Knöll will assume the position of the chairman of the executive management of the company in addition to his duties as chief operating officer of HC Starck Group. Dr Michael Reià remains member of the executive management. Manufacturing & Engineering Magazine | The Home of Manufacturing Industry News
Oxford Instruments Sells Wire Business for £14m
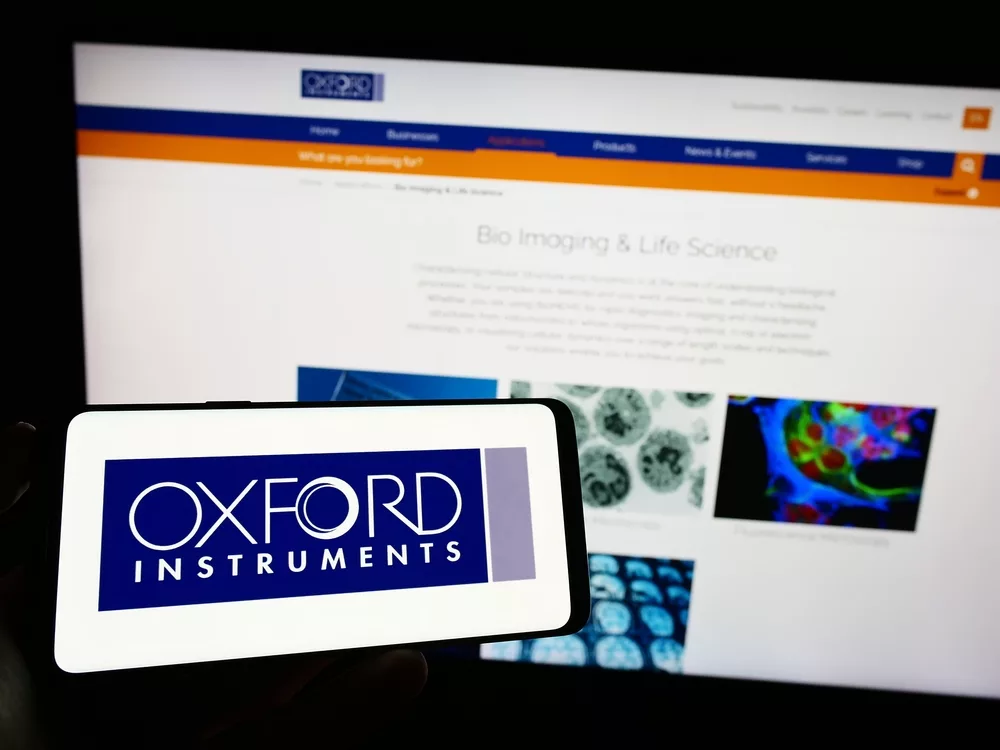
Listed manufacturer and supplier of high technology tools and system for research and industry, Oxford Instruments, have sold its superconducting wire business in a £14 million deal. A subsidiary of Nasdaq-listed Bruker Corporation, Bruker Energy and Supercon Technologies (BEST) has now acquired Oxford Instruments Superconducting Wire (OST) for a full cash sum of £14.13 million. Formerly part of Oxford Instrumentsâ industrial products sector, OST supplies superconducting wire to be used in magnetic resonance imaging (MRI) scanners and other medical and scientific applications. Based in New Jersey, the business generated a £3.4 million operating profit on revenues of £42.4 million in the year ended March 31, 2016. Oxford Instruments said that the disposal represents the next step in the groupâs strategy of actively managing its portfolio. Previously, the company had reported challenges within the superconducting wire markets mainly because of pricing pressures exerted by MRI system manufacturers and a declining demand for wire. Chief Executive, Ian Barkshire, commented: “After a comprehensive review of our portfolio, the board has determined that our Superconducting Wire business is no longer core to the group’s long-term strategic vision. “The divestment will allow increased focus across the group on our chosen market segments and the cash proceeds will enable us to reduce our net debt, in line with our strategy to deliver enhanced shareholder value.” Earlier in the month, Oxford Instruments reported a 3.7% fall in H1 adjusted profit before tax. The interim dividend stood at 3.7 pence per share, while the company expected a benefit from currency of approximately £7 million to operating profit in 2017/18 financial year. Adjusted profit before tax down 3.7 pct; reflecting lower sales in OI Healthcare and continued weakness in Superconducting Wire. The company expects to deliver a current year performance in line with last year Source text for Eikon: Further company coverage: (Bengaluru Newsroom) Manufacturing & Engineering Magazine | The Home of Manufacturing Industry News
Rolls-Royce shares dip despite success in cost-cutting turnaround plan
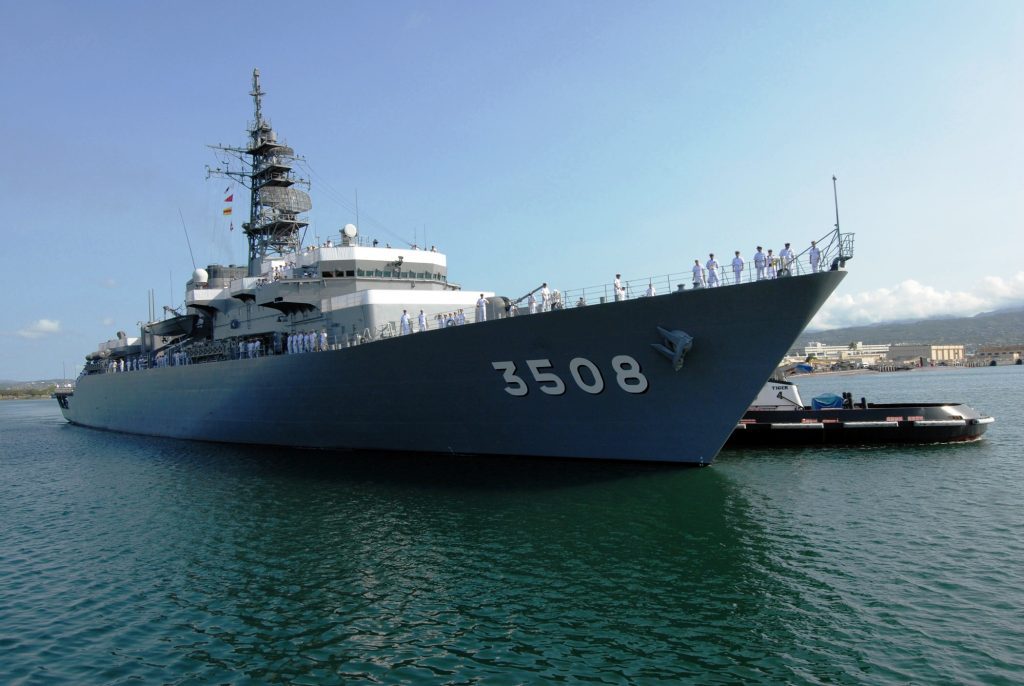
Rolls-Royce share price dropped today despite the group saying its huge cost-cutting drive is likely to be at the top end of its targeted range. The manufacturing giant is one year in to a turnaround programme to reset its finances after posting five consecutive profit warnings in the 20 months leading to November 2015. In a trading update today, the UK-based group said its 2016 outlook remained unchanged and its cost savings are expected to be at the top end of its £150-200m range. Chief executive Warren East said at an investor event today that the transformation has taken slightly longer than he would have hoped, as it has taken longer than anticipated to appoint a string of new executives including a new chief operating officer, Simon Kirby, and a new chief financial officer, who will join early next year. The group said there were “no signs of recovery yet” in offshore oil and gas markets and that its marine engineering and equipment making orderbook remained “very weak” with further falls in revenue expected next year. Among some of its other divisions, it said civil aerospace demand remained strong, the defence outlook was “positive overall”, though its power systems markets reflected weaker demand for industrial engines and service. Rolls-Royce’s shares were down 2.6 per cent to 735p in early afternoon trading. Although best known for the cars bearing its name, Rolls-Royce now designs and makes engines primarily for fighter jets, commercial aircraft, ships and nuclear submarines.
Manufacturers collaborate on 3D audio system at Yamaha conference
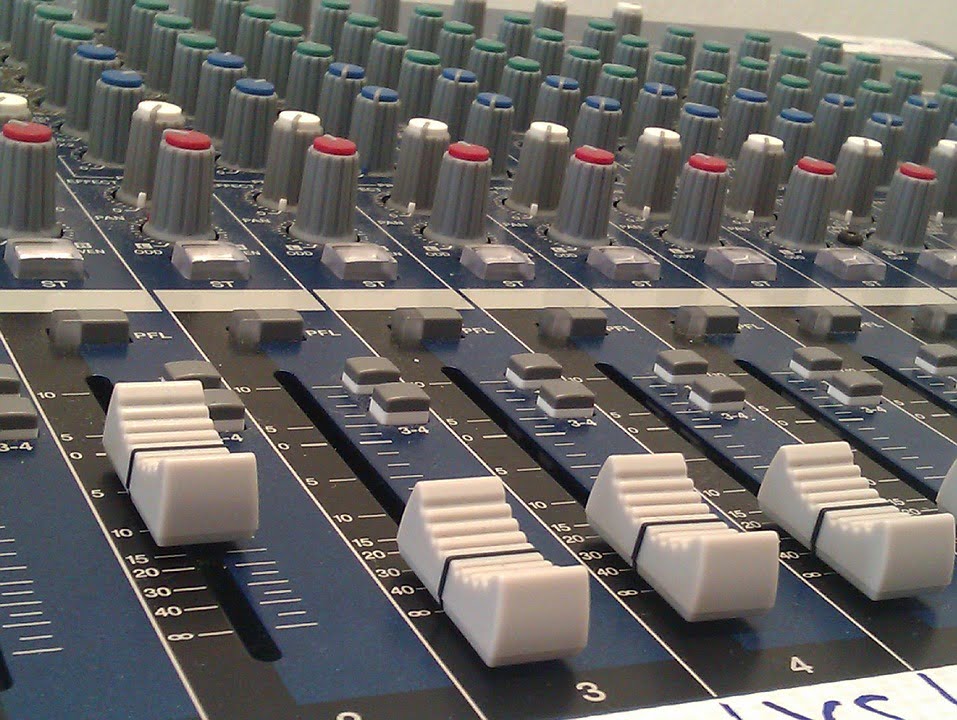
Yamaha Music Europeâs tenth annual system designerâs conference saw 120 delegates gather at the Valencia campus of Berklee College of Music to experience a cross-industry collaboration from Yamaha, Barco, Dolby and Unique Cinema Systems. Hosted at the Palau de les Arts Reina Sofia, the conference allowed audio professionals to meet and discuss the latest trends in technology and best practice prevalent around Europe. This yearâs theme, âMulti-channel Audio for Entertainment and Professional Communication,â incorporated multiple manufacturers for the first time, with companies including Barco, Dolby Laboratories, Nexo, Revolabs, Steinberg Media Group and Unique Cinema Systems joining Yamaha. Attendees could visit three demonstration rooms hosting seminars featuring bespoke audio systems. One session dedicated to three-dimensional audio reproduction led by Barco, Dolby Laboratories, Unique Cinema Systems and Yamaha featured a lecture theatre set up supporting the Yamaha AFC3, Dolby Atmos and Barcoâs IOSONO Immersive Sound specifications within a single, shared system. The system comprised a 10m x 8m x 4m truss, featuring 56 Nexo and Yamaha loudspeakers and driven by networked Nexo and Yamaha power amplifiers. The Dante and MADI-based system was managed by a single Yamaha MRX7-D signal processor, which merged the three multi-channel inputs from a Yamaha AFC3 active field control processor, a Dolby Atmos RMU processor (controlled by Nuage Digital Audio Workstation) and an IOSONO core processor. Another room, Studio 81, saw a full scale Dante network with switches, i/o racks, mixing consoles and DSP engines being demonstrated. It also featured a Disklavier grand piano integrated with Yamahaâs MusicCast wireless audio distribution system to. Meanwhile, a full conference system was installed in Sala B (Hall B) to showcase multi-channel wired and wireless microphone systems, local PA for conferencing and distant communication using a combination of technologies, including automatic echo cancelling. In addition to the three main demonstration rooms, a number of other topics â including applications of software-defined media, immersive audio solution concepts and design, 2.4GHz wireless microphone technologies and 2D/3D live sound limitations and perspectives â were up for discussion at the event in Aula Magistral hall.
Are Mazda’s designs the best around?
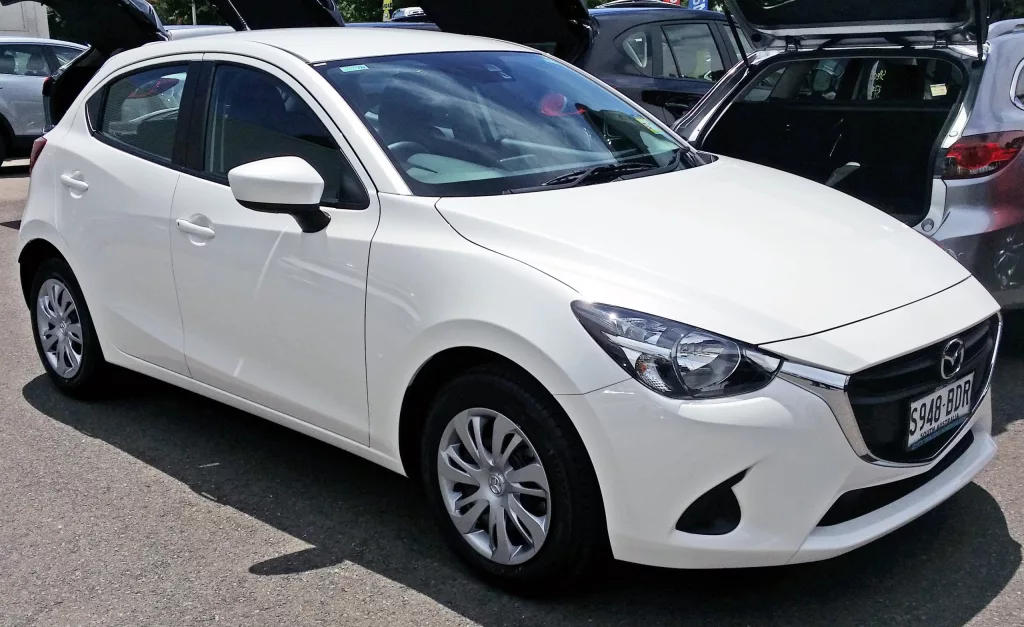
Are Mazda’s designs the best around? : It’s hard to think of a car maker with a better-looking range of cars than Mazda. From the smallest 2 to the largest CX-9. Mazda speaks about a ‘design language’ more than most manufacturers, stuff that typically can be jargon and not prevent a car from looking like a dog’s dinner despite all those lovely PowerPoint slides of some waterfalls and a spiralised cucumber. But whatever the language behind the ‘Kodo – Soul of Motion’ design philosophy that Mazda employs, I’ll happily speak with it. Mazda has a habit of lurching around between generations of car trying to reinvent itself. Such an approach can reveal an overall lack of confidence and direction in what is going on. You don’t have to look too far up the road towards some of Mazda’s Japanese counterparts for current evidence. But back in 2011, Mazda relaunched itself with a suite of technologies called SkyActiv and the Kodo design language to style its next generation of models. And they all looked lovely, looking as good as they drove for once. Now a potential crossroads has arrived. For at the LA motor show, we have the first Mazda to be replaced since it went Kodo and SkyActiv: the second-generation CX-5. Thankfully, the new car is a subtle evolution of the existing theme rather than the complete rethink we’ve tended to see from Mazda over the years. They must know they’re on to something with this Kodo… So much so that Mazda now wants its models to be seen as “art”, according to design chief Ikuo Maeda. It’s quite a claim and, even as someone who has seen the Mona Lisa on the canvas, I’m not confident of knowing art when I see it or whether or not a car qualifies. To hell with it, though: the new CX-5 is another Mazda that looks great and is a step up again from its already handsome predecessor. If Mazda can keep this up over the next few years as it replaces the rest of its range, they may have to clear a corner of The Louvre for the next MX-5for it’ll be such a stunner. Leonardo da Vinci would approve. Probably. Manufacturing & Engineering Magazine | The Home of Manufacturing Industry News
G F Tomlinson Starts Work on Nottingham Manufacturing Site
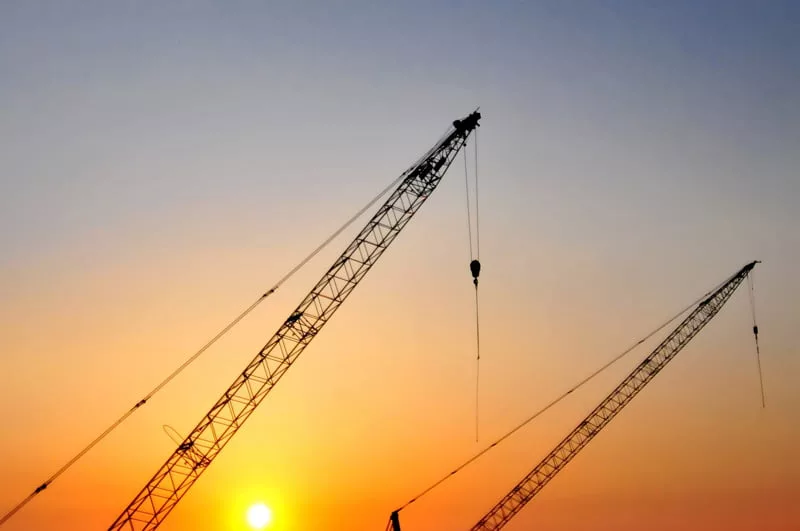
G F Tomlinson has started work on a new multi-million pound manufacturing research site in Nottingham. A ground-breaking ceremony to mark the beginning of construction on the Advanced Manufacturing Building (AMB) for the University of Nottingham was held on Thursday, November 10. The 9,011m2 training and research site is being developed on a former brownfield site at the University’s Jubilee Campus. It forms part of an expansion to the University’s Faculty of Engineering and will feature teaching spaces, laboratories, modern workshops and offices for research activities, including nano-scale production, robotics and large-scale aerospace demonstrator components. The project team features project managers Turner and Townsend, architects Bond Bryan, engineers Arup and cost managers Currie and Brown (previously Sweett). The development has been part funded by £5 million from D2N2 Local Enterprise Partnership and a £1 million contribution from the Wolfson Foundation to develop a modern clean room for the investigation of 3D printed pharmaceutical devices. Once completed, the building will have enough capacity for 699 staff, students and researchers. Andrew Sewards, Managing Director for G F Tomlinson said: “This scheme truly demonstrates the University of Nottingham’s position as a beacon in manufacturing research. The completed scheme will be home to world-class research facilities and revolutionary research activity, helping to nurture collaboration and innovation between education and industry. “Having successfully delivered a number of schemes previously on the Jubilee Campus, we are excited to be working with the University of Nottingham once again, bringing our expertise in education and large-scale manufacturing buildings, to benefit the university and the city of Nottingham.” Professor Andy Long, Pro-Vice-Chancellor for the Faculty of Engineering at the University, added: “The new facility will host several world-leading research groups and accommodate some of the most advanced manufacturing technologies related to automation, precision manufacturing, 3D printing and light weight composite materials.” Manufacturing & Engineering Magazine | The Home of Manufacturing Industry News
Cambridge Nanotherm Meets LED Thermal Substrate Demand by Expanding Manufacturing
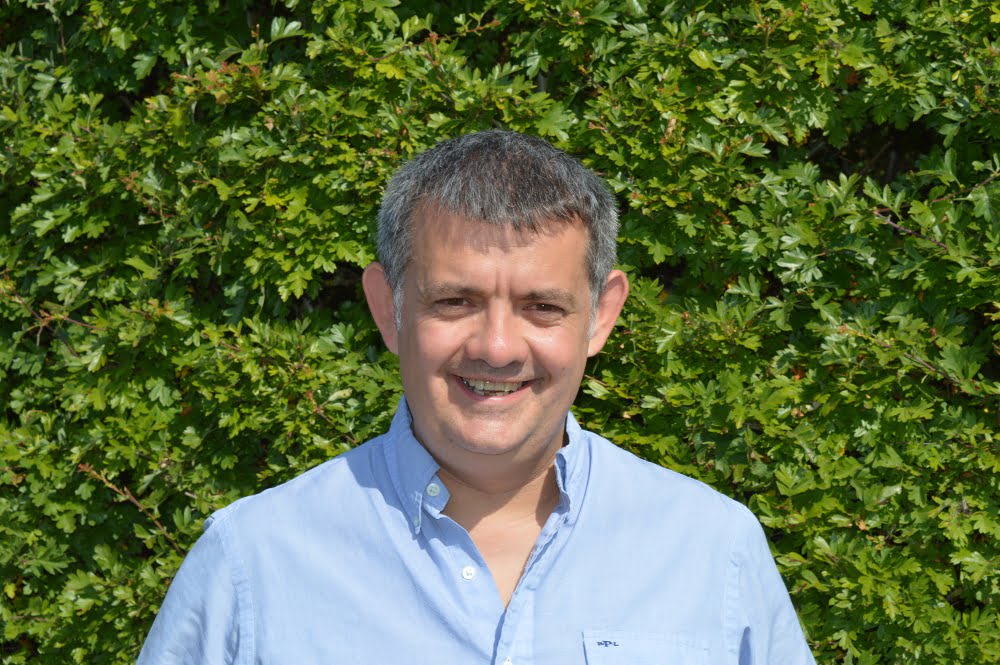
Thermal interface company Cambridge Nanotherm has expanded its manufacturing capabilities to meet demand for LED thermal substrates. Its technology is a thin electrically insulating coating with high thermal conductivity for metal cored PCBs (MCPCBs). Andy Matthews, Cambridge Nanotherm COO, commented: Our MCPCBs offer designers a distinct thermal advantage. “Demand for our solutions has therefore been strong, and weâre currently engaged with most of the top ten LED manufacturers. “As a result, weâve expanded our manufacturing routes to cater to a much broader variety of requirements. “Weâre working with some of the best PCB and thin-film circuitisation companies so we can offer a range of options.” High-definition, high-volume Through its network of thin-film manufacturers and PCB it is offering capabilities including: fast turn-around prototyping, high-definition thin-film circuitisation, and high-volume production. Standards including automotive ISO/TS 16949:2009 and industry-specific SGS standards can be applied. Some standard products are covered by UL recognition. The companyâs process converts the surface of the PCBâs aluminium core into a high-integrity electrically insulating but thermally conductive Al2O3 ânanoâ-ceramic. This depends on the circuitisation route chosen. 100% UK manufacturing A spokesman for the firm said: 100% of Cambridge Nanothermâs production of its nanoceramic is in the UK. PCB circuitisation partners are spread across the globe, including in the UK like â Spirit Circuits, for example â and it depends on customer requirements as to which one the company uses. The layer can be grown to different thicknesses to meet varying electrical isolation requirements and is generally between 10-30µm. Itâs the thinness of this layer that provides the exceptional thermal conductivity, said the firm. With 10µm, thermal performance is 115W/m.K far exceeding anything else available on the market. Conductivity can be as high as 152W/m.K, and the insulator can be created as thin as 3µm. A thin copper layer is then bonded to the ceramic using a thin (typically 4µm) layer of adhesive creating a PCB compatible with standard PCB production lines that support MCPCBs.
Key Manufacturing Figures Present Research in Brussels
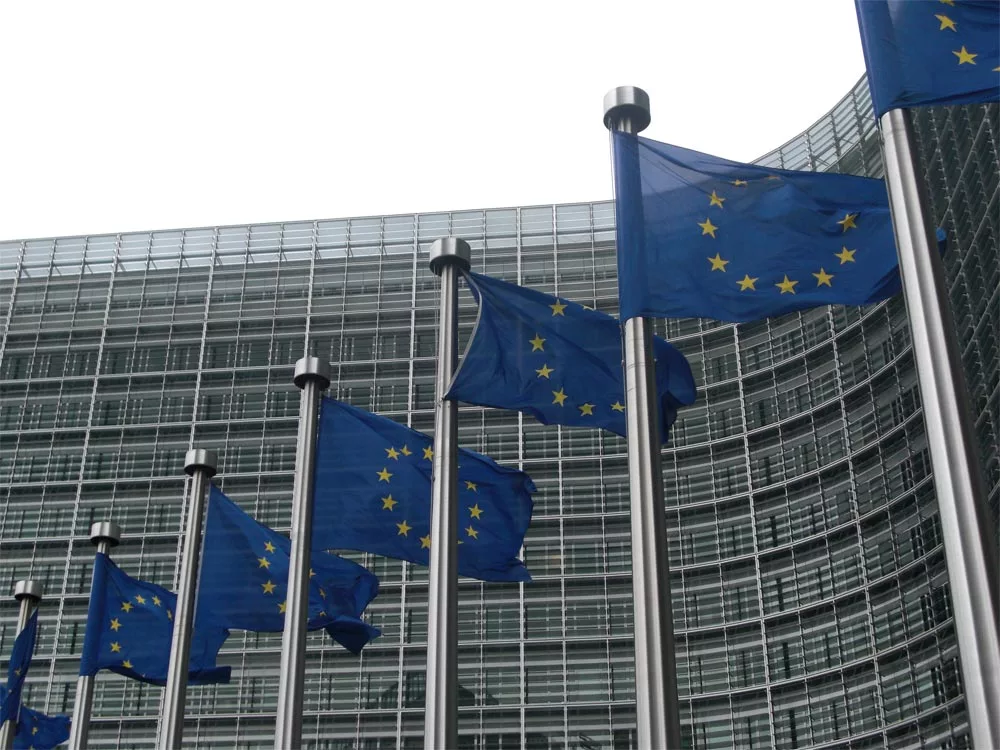
Leading figures from manufacturing, policy, academia and research presented the research results of the EU funded scheme at an event in Brussels on October 18. The âuse-it-wiselyâ scheme, funded under the FP7 framework and running until the end of this year, is addressing sustainability challenges in six sectors: office furniture, shipping, trucks, space products, mobile rock crushers and power plant turbines. It comprises 20 partners from nine countries throughout Europe across manufacturers, researchers and their customers. Project co-ordinator from VTT Technical Research Centre of Finland, Goran Granholm, commented: Through effective upgrade innovation, we can achieve sustainable solutions for demanding customers. This will help industry struggling with keeping abreast of global competition, new technologies and changing requirements. Research programme officer with the European Commissionâs DG Research and Innovation, Erastos Filos, added: [The project] has created innovative frameworks and tools using virtual reality [and] augmented reality, as well as business models that allow European manufacturers to face the challenges of rapidly changing markets. Karin Verploegen, representing Gispen, a Dutch industrial designer, said that her aim was to prolong the lifespan of furniture through the implementation of the principles of the circular economy. Gispen and Dutch research institute TNO together developed two tools to enhance sustainable business practices. RD Velhoâs Tommi Mannerjoki talked about research carried out on upgrades of mobile rock crushers. With new technologies becoming accessible in 3D scanning, augmented reality and additive manufacturing, Mannerjoki and his project partners in Metso Minerals researched how to easily gather 3D information from mobile crushing machines and how to manufacture single parts. A professor with Chalmers University of Technology, Björn Johansson, worked with Volvo during the scheme to enhance factory floor changes in the production of truck cabs. Johansson outlined the challenges of continuous changes in the production environment and the subsequent requirements for the production system to be continuously upgraded. Manufacturing & Engineering Magazine | The Home of Manufacturing Industry News
Vauxhall Opens Police Car Factory at Luton Car Manufacturing Plant
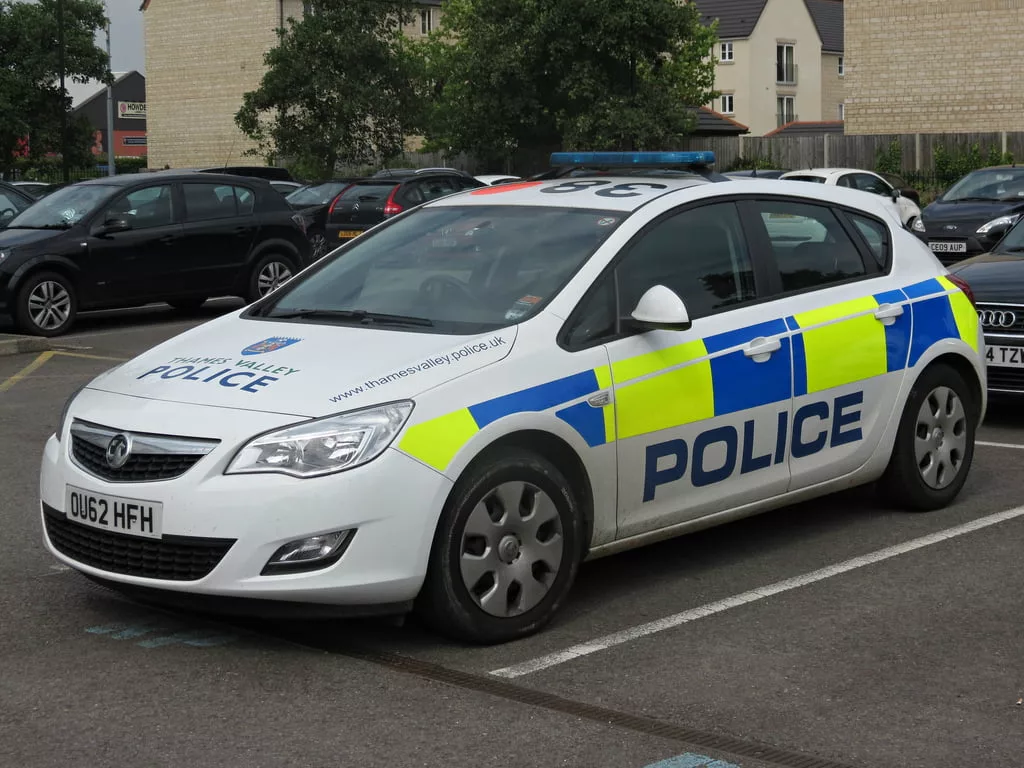
Vauxhall has officially opened its police car factory at its car manufacturing plant in Luton Car Manufacturing Plant, Bedfordshire. The car manufacturer says it is the largest facility of its kind in Europe and will convert 2,500 vehicles every year. These will include cars and vans to be used by Police forces, as well as Ambulance and Fire services throughout the UK. The new site will bring 50 jobs to the area and has been created after moving production in-house from its former location in Millbrook, Bedfordshire. The firm says that supplier companies across the country will also benefit with 90% of blue-light content, the materials used to convert a standard car in to a Police car, sourced from UK suppliers. Among the local companies involved is Luton based Border Engineering, the makers of brackets and AV Engineering in Royston who make fascia mouldings. A number of vehicles will be converted to be used by the emergency services at the facility in Luton with cars including Mokka, Insignia, Astra and Corsa, and CVs, such as Movano, Combo and the Luton built Vivaro vans. Vauxhall says it is the sole manufacturer to offer a one stop shop for blue light vehicles. Everything is done in-house from testing to converting and, eventually, remarketing of decommissioned vehicles. Vauxhallâs Manager of Special Vehicles, Dick Ellam, commented: Through our flexible production facility, Vauxhall is able to offer a one-stop shop purchasing experience to UK emergency services. We can deliver a wide choice of car and van models, specifically designed and rigorously-tested to meet the stringent demands of our emergency services. We can also supply turn-key vehicle solutions that enable rapid turnaround of replacement vehicles, plus we can now offer a unique in-house de-commissioning and re-marketing service. Vauxhall says it is the number one supplier to Police fleets with a 70% market share of competitive segments. Vauxhall Opens Police Car Factory at Luton Car Manufacturing Plant Manufacturing & Engineering Magazine | The Home of Manufacturing Industry News