Leicester Technology Centre to Boost Flow Control Engineering
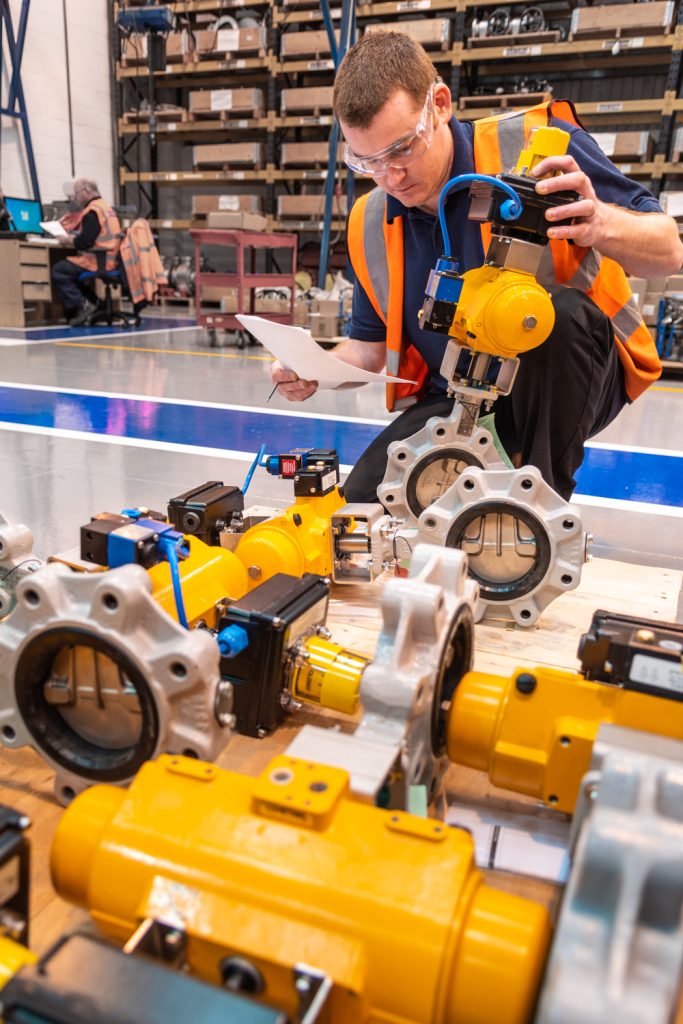
Leicester Technology Centre to Boost Flow Control Engineering : ERIKS UK has opened a new facility within its Flow Control Technology Centre in Leicester, which brings together specialist knowledge and components in all aspects of industrial flow control systems under one roof. The centre employs 34 people, and comprises of a workshop for repairing, designing, and upgrading pumps and valves, as well as an ‘Automation Cell’ where ERIKS develops and builds complete flow control solutions. The facility is staffed by engineers from a wide range of disciplines who collaborate to deliver turnkey flow control solutions such as in-line blending and formulating, automatic dosing, dilution, filling, batching, filtration and clean-in-place systems. By basing the team at the Leicester site, every stage of the design and production process can be carried out in one place. This includes the assembly of bare shaft pumps, testing and certification of valves and actuators, and mounting whole solutions onto skids ready to integrate with whatever direct control system the end user operates. “Developing specialist flow control and dosing systems demands specialist knowledge, a comprehensive understanding of a wide range of components and access to these parts at competitive prices. By bringing all the expertise and production capabilities together, we can deliver tailored solutions that help customers reduce production downtime, improve health and safety, and increase the reliability of their processes and assets,” said Andy Silver, ERIKS’ Flow Control Director. Manufacturing & Engineering Magazine | The Home of Manufacturing Industry News
Sony Launches Innovative Apprenticeship Scheme
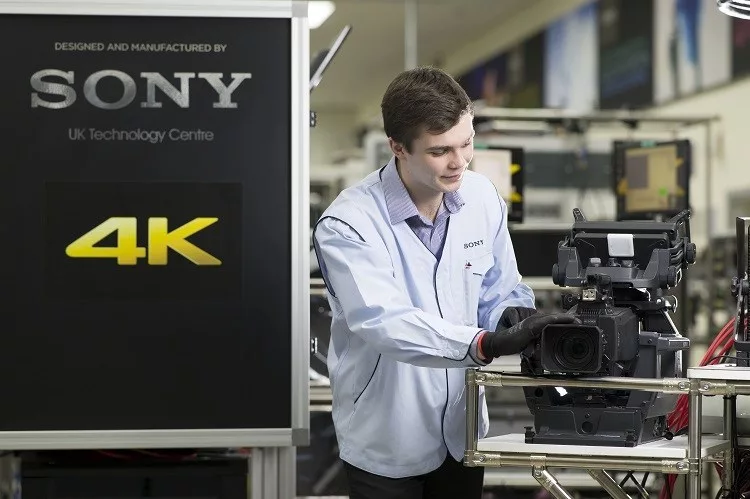
Sony UK Technology Centre, one of Wales’ leading manufacturers, is calling on innovative, driven, and passionate individuals to sign up for its new apprenticeship. Sony UK TEC Apprenticeship scheme, which is now in its sixth consecutive year, officially launched on February 1st with applicants encouraged to apply before the February 28th closing date. The industry-leading initiative supports career-driven individuals to further their education and gain qualifications throughout the scheme. The company’s onsite academy drives and coordinates their full studies, all while the apprentices gain invaluable working experience at one of the world’s leading manufacturing sites. During the four-year scheme apprentices will get the opportunity to work across a variety of departments, including Software Engineering, Production Engineering, and Development Engineering and Robotics. They will help to develop internationally renowned products including 4K broadcast technology, the Raspberry Pi, smart office solution Nimway, and smart city technology. Over 30 apprentices have taken part in the successful internal scheme since its inception, with all participants praising its diverse offering. Cecilia Fritz, Head of HR and Training Strategy said an apprenticeship with Sony UK TEC opens up a “vast wealth” of opportunity for any student looking to advance and develop their career. “Our apprenticeship is a thorough and diverse programme which offers new starters an in-depth insight into all aspects of Sony UK TEC’s highly successful engineering operation. We believe that this varied approach creates highly skilled and well-rounded team players and opens up a vast wealth of opportunities to them within the industry as a result. At the end of their four years, they are fully equipped with the ability, and knowledge, to become some of the sector’s brightest engineering talents and to drive genuine progression in the fields of technology and manufacturing,” said Cecilia Fritz. To apply for a place in the Sony UK TEC Apprenticeship scheme applicants must have a minimum of five GCSEs, including a B or above in Maths, and Cs or above in Science and English. Applications close at midnight on February 28th, with assessments due to take place on March 21st. Manufacturing & Engineering Magazine | The Home of Manufacturing Industry News
Pryme Group Opens Manufacturing Centre
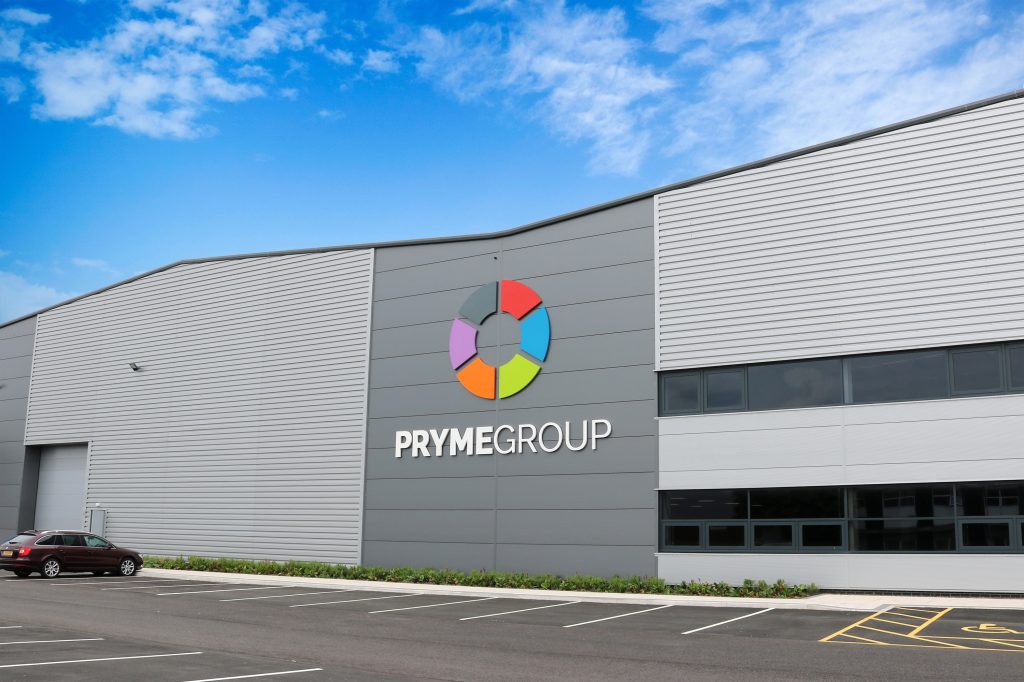
The new, state-of-the-art facility of integrated manufacturing specialist, Pryme Group has been officially opened by Norma Redfearn CBE, elected mayor of North Tyneside. Following £10 million investment, the company has been relocated from nearby Ryton to a purpose-built engineering services and manufacturing centre at the Tyne Tunnel Estate. “We are extremely grateful that Norma took time out of her busy schedule of looking after the interests of the North East business community to visit Pryme Group and find out more about us as a company,” said Angus Gray, CEO of Pryme Group. “I’m excited about what the future holds for the business and the local area. While work is still continuing to allow the site to operate at full capacity, we’ve taken the decision to move staff into the new building slightly earlier than planned to meet demand for our services,” Angus added. With operations across the UK and headquarters in Dundee, Pryme Group provides integrated manufacturing solutions for the oil and gas, aerospace and defence industries. The business expects to more than double its current workforce in North Tyneside from 70 to 150 in the next five years and is actively recruiting for new personnel, including CNC operators. To date, Pryme Group has invested £4.2 million in equipment and CNC machinery with new technology and increased efficiencies expected to result in a boost to revenue and improved on-time delivery .The North East LEP has also provided additional grant funding of £1.35 million through the government’s Local Growth Deal; allowing UK Land Estates to build the unit in North Shields speculatively at a cost of £4.5 million. “I am delighted Pryme Group has invited me to be part of its official opening on Tyne Tunnel Estate. This facility marks exciting times for the company and the prospect of new jobs being created is also great news for our local residents. The council look forward to working with Angus and his team as they continue their growth plans in the region,” said Welcoming Pryme Group to the borough, Norma Redfearn CBE. Pryme Group recently signed new contracts with energy sector clients – totalling more than £3.5 million – for fabrication and machining services with all work to be carried out at the new facility.
Sheffield Opens Three Advanced Engineering Centres
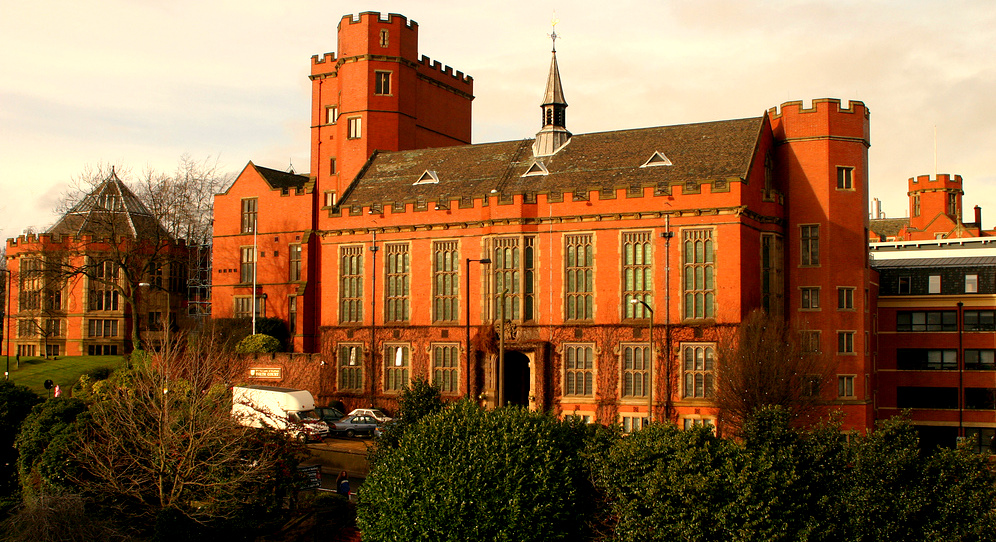
Three new multi-million pound research centres have been opened by the University of Sheffield in the region, aiming to further boost the city’s reputation as a hub for advanced engineering. The new centres could also boost the reputation of the Northern Powerhouse as a leader in advanced research, innovation and engineering. The Royce Translational Centre (RTC), the Laboratory for Verification and Validation (LVV), and the Integrated Civil and Infrastructure Research Centre (ICAIR) are all located within the Sheffield City Region’s Advanced Manufacturing Innovation District. RTC has been set up to evolve novel materials and processing techniques developed by research teams and make them accessible for trial by industry. It is home to Royce@Sheffield and the metals research group of AMRC, the National Metals Technology Centre (NAMTEC). LVV will enable research into the design and operation of advanced engineering structures when exposed to real-world vibration and environmental conditions, allowing testing of both full structures and substantial components. Experimental data, computer modelling and machine learning will allow industry to produce lighter, safer designs for a range of industrial sectors. ICAIR will enable experimental tests for investigating both underground and above ground constructed infrastructure. It can integrate data, AI, robotics and advanced manufacturing techniques to the field of infrastructure. The centres are working with companies to help develop new technologies, using research to cut costs and lead times, which could potentially transform industrial processes and businesses. They form part of a £47 million investment, part funded by the European Regional Development Fund (ERDF), UK research and Innovation (UKRI) and the University of Sheffield. The site is already home to the University of Sheffield’s Advanced Manufacturing Research Centre (AMRC) Factory 2050 – the UK’s first advanced factory, dedicated to conducting collaborative research, component manufacturing and developing machining technologies.
FBX Solutions Helps LoneStar Group with Massive Move
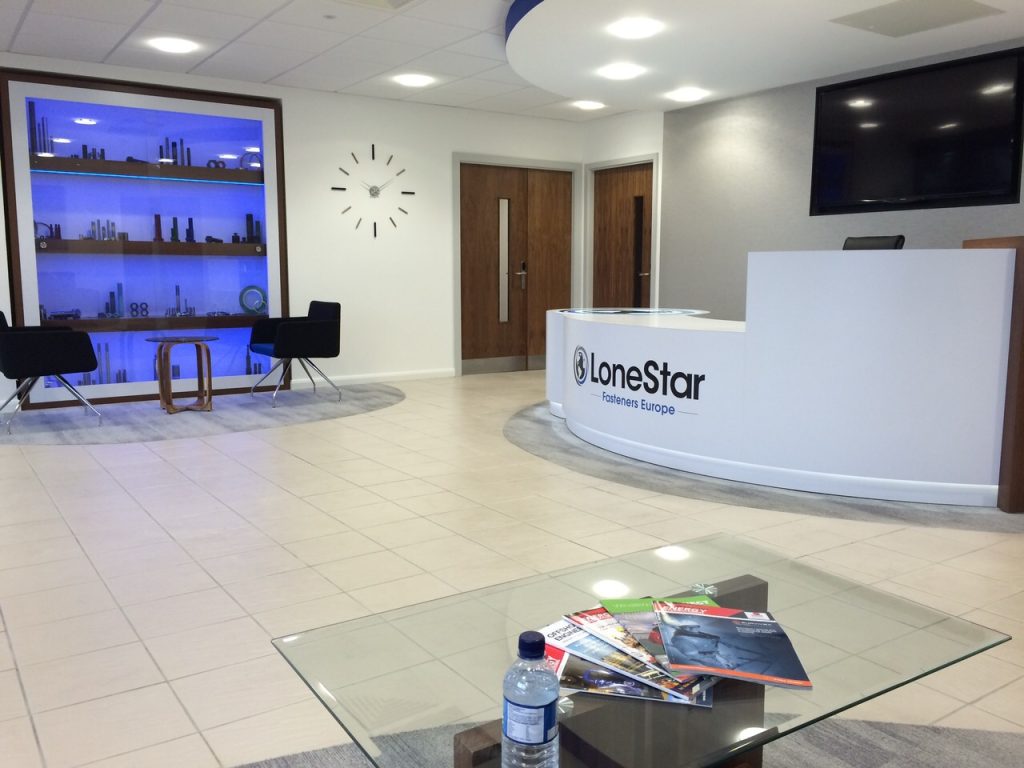
When multi-national engineering group LoneStar needed someone to manage a huge consolidation and relocation project in the West Midlands they knew exactly who to turn to for help – FBX Solutions. LoneStar manufactures and supplies high-performance fasteners, sealing and precision-engineered components for the global energy markets and the company wanted to combine three sites and a head office into one. And the brains behind the move were FBX, who project managed the whole process from start to finish. The result was a new £7.5million, 115,000 sq ft manufacturing and distribution centre of excellence at Universal Point in Steelmans Road, Wednesbury, near junction 9 of the M6 which saw PRD Fasteners, Eurofast Petrochemical Supplies and Triplefast International form LoneStar Fasteners Europe. Set up in 2012 by Managing Director Frank Blahuta, FBX provides a unique service to help small-medium sized businesses in the manufacturing and logistics industries get the maximum value out of their facilities, whether through relocation or optimizing their current one. They were approached by VABS (Value Added Business Solutions) to project manage integrating the company’s three existing sites in the West Midlands – two at Willenhall and one at Bilston – plus a head office in Wednesfield, all operating under one roof. Frank explained: “It was quite a significant process taking three limited companies on four different sites and bringing them under one company’s management on a single site. “We had to look at the size of each space, how they utilised that space and how efficient the companies ran to what they needed. The work included the consolidation of repeated functions across the three limited companies, including HR departments and finance departments, so there was a lot of work to do. “Then running parallel with that, we were asked to look at the prospect of relocating LoneStar to a new site, so we looked at brand new builds and existing builds and how much space they would need. We needed a 115,000 sq ft facility and there was one that had just come onto the market – the old Dreams For Beds distribution centre just off the M6. “So, we put a plan in place with architects, designers and a construction company, leased the building and managed the whole design and redevelopment of the new site.” FBX then picked up and managed the whole move into the new premises, which saw 268 staff move in over two floors. A spokesperson for the LoneStar Group, said: “Appointing FBX Solutions to programme manage our business relocation and consolidation project was the best decision we made. Their industry knowledge and expertise, combined with their professional and reliable attitude throughout, made them an invaluable resource to our company. “Having them onboard meant the whole process ran as seamless as possible and I would recommend the team at FBX Solutions to any business who want to grow, become more efficient or relocate.”