Cambridge Nanotherm Meets LED Thermal Substrate Demand by Expanding Manufacturing
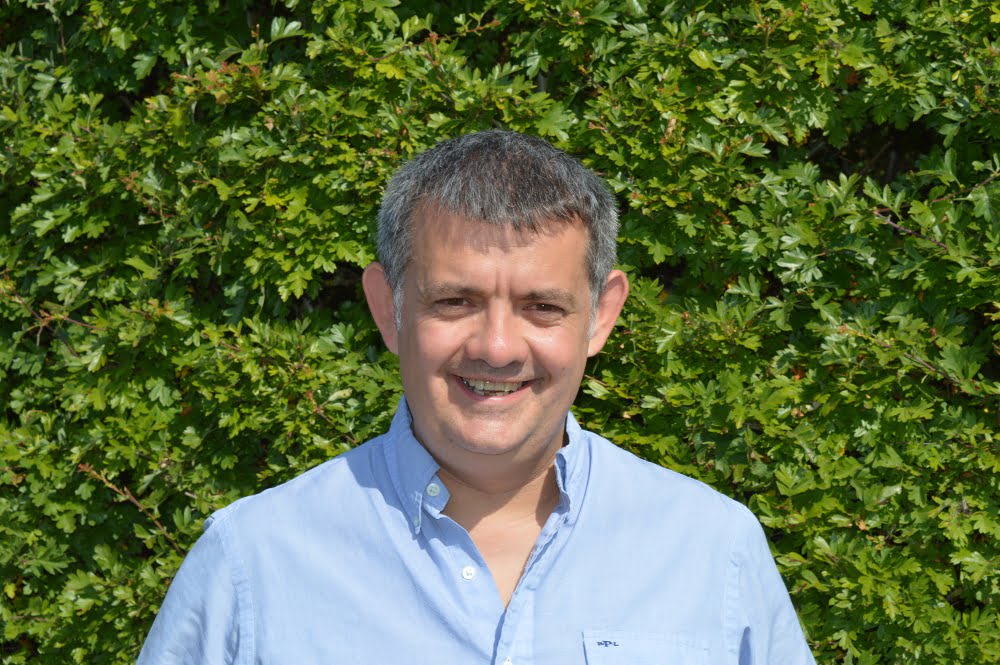
Thermal interface company Cambridge Nanotherm has expanded its manufacturing capabilities to meet demand for LED thermal substrates. Its technology is a thin electrically insulating coating with high thermal conductivity for metal cored PCBs (MCPCBs). Andy Matthews, Cambridge Nanotherm COO, commented: Our MCPCBs offer designers a distinct thermal advantage. “Demand for our solutions has therefore been strong, and weâre currently engaged with most of the top ten LED manufacturers. “As a result, weâve expanded our manufacturing routes to cater to a much broader variety of requirements. “Weâre working with some of the best PCB and thin-film circuitisation companies so we can offer a range of options.” High-definition, high-volume Through its network of thin-film manufacturers and PCB it is offering capabilities including: fast turn-around prototyping, high-definition thin-film circuitisation, and high-volume production. Standards including automotive ISO/TS 16949:2009 and industry-specific SGS standards can be applied. Some standard products are covered by UL recognition. The companyâs process converts the surface of the PCBâs aluminium core into a high-integrity electrically insulating but thermally conductive Al2O3 ânanoâ-ceramic. This depends on the circuitisation route chosen. 100% UK manufacturing A spokesman for the firm said: 100% of Cambridge Nanothermâs production of its nanoceramic is in the UK. PCB circuitisation partners are spread across the globe, including in the UK like â Spirit Circuits, for example â and it depends on customer requirements as to which one the company uses. The layer can be grown to different thicknesses to meet varying electrical isolation requirements and is generally between 10-30µm. Itâs the thinness of this layer that provides the exceptional thermal conductivity, said the firm. With 10µm, thermal performance is 115W/m.K far exceeding anything else available on the market. Conductivity can be as high as 152W/m.K, and the insulator can be created as thin as 3µm. A thin copper layer is then bonded to the ceramic using a thin (typically 4µm) layer of adhesive creating a PCB compatible with standard PCB production lines that support MCPCBs.