Concrete Answer: How the Industry Is Dealing with Excessive Emissions
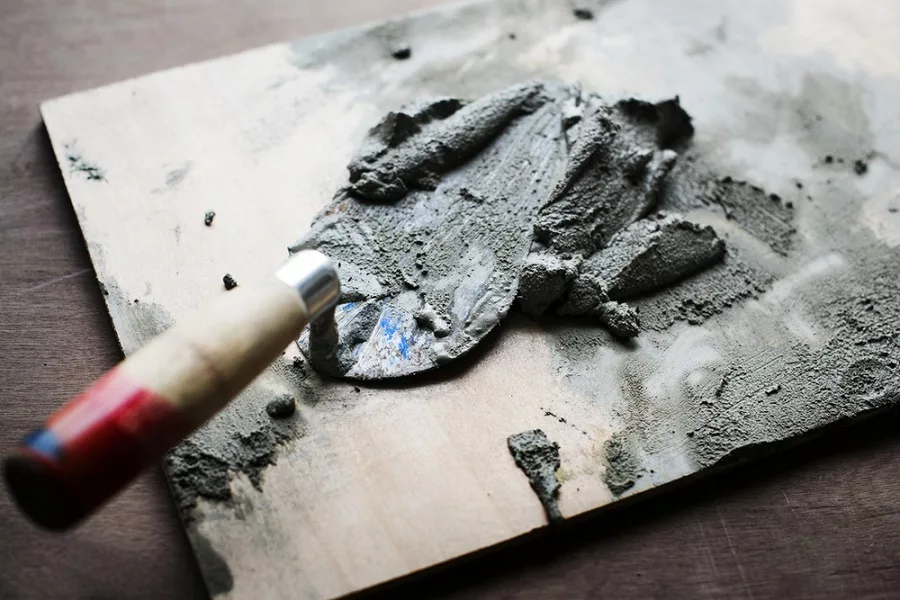
Cement is mixed with water, sand and aggregate to be made into concrete, the most used building material in the world. Utilised in virtually every form of construction, concrete is the base for our schools, buildings and homes. But despite the fact that it is used so widely, concrete is hiding something of a dark secret. The fact is that cement production is now the second largest industrial cause of carbon dioxide emissions across the world. Concrete is doing a serious amount of damage to the environment, and as all industries look to reduce their carbon footprint, it is necessary that those involved in concrete product do the same. Some would suggest that the obvious answer is that we should stop using so much of the stuff – but unfortunately it is not quite that simple. A society built on concrete As a society we have become extremely reliant on concrete both as a part of general infrastructure, and its virtually unlimited variety of uses. Industrial cement producer Hanson lists sectors ranging as wide as energy and waste treatment to flood defence and property as requiring cement and concrete. As concrete barrier specialist Maltaward state in this blog post, concrete is also vital for so many day-to-day issues taken for granted – including controlling traffic and providing security to the public. In short; we would struggle to function without access to cement and concrete, which it why it is necessary to be realistic about finding a solution to this problem, rather than trying to reduce our dependence on concrete entirely. Some worrying statistics Nevertheless, there are some very concerning statistics hanging around regarding concrete and cement, and what it means for the planet. For example, research shows that five per cent of all global CO2 emissions comes purely from the production of cement and the growing size of the world’s population also means that it is estimated that cement product is likely to increase by as much as 23% by 2050. It is unsustainable for us to continue current methods of concrete production at the same rate, let alone this potential rise in the use of the material. Thankfully, however, it has been recognised that the industry does have a problem in terms of the emissions that it is producing. The change needs to happen as soon as possible, however, as many cities around the world are undergoing rapid development and require a great deal of concrete to keep up with the pace. Too long without a change The most widely used type of concrete across the world is known as Portland cement. The product was patented nearly 200 years ago and very little has changed in the production process since then. While the enduring longevity of this form of concrete is impressive, it is does point to the problem that the whole process did not take into account issues such as emissions or carbon footprint. Portland cement is produced mostly with limestone, and to create the desired form of the cement, the limestone must be heated to very high temperatures of around 1,500 degrees. This is environmentally hazardous for a couple of reasons: firstly, a great deal of fuel is required to create that heat, and also that at these temperatures, limestone begins to chemically decompose which creates a compound called calcium oxide. The fact that this process has been used for so long means that it can be difficult to convince the industry to change. New ideas and technologies are slowly coming through While it can be very difficult to make a whole industry re-think its approach to the product that it produces, there has been some progress with some companies coming up with interesting new technologies and ideas. One example of this is CarbiCrete which uses slag from steel factories instead of Portland cement in order to produce concrete. The slag contains the calcium, oxides and silicates necessary to produce a very similar product. The world needs more innovative concepts like this in order to produce the levels of concrete necessary for the estimated level of human expansion, without the scenario being so damaging to the environment. Another popular concept is that of CarbonCure which utilises waste CO2 in the concrete production process. This reduces the amount of Portland cement required and actually produces a superior product. Manufacturing & Engineering Magazine | The Home of Manufacturing Industry News
Modern Technology for Traditional Houses
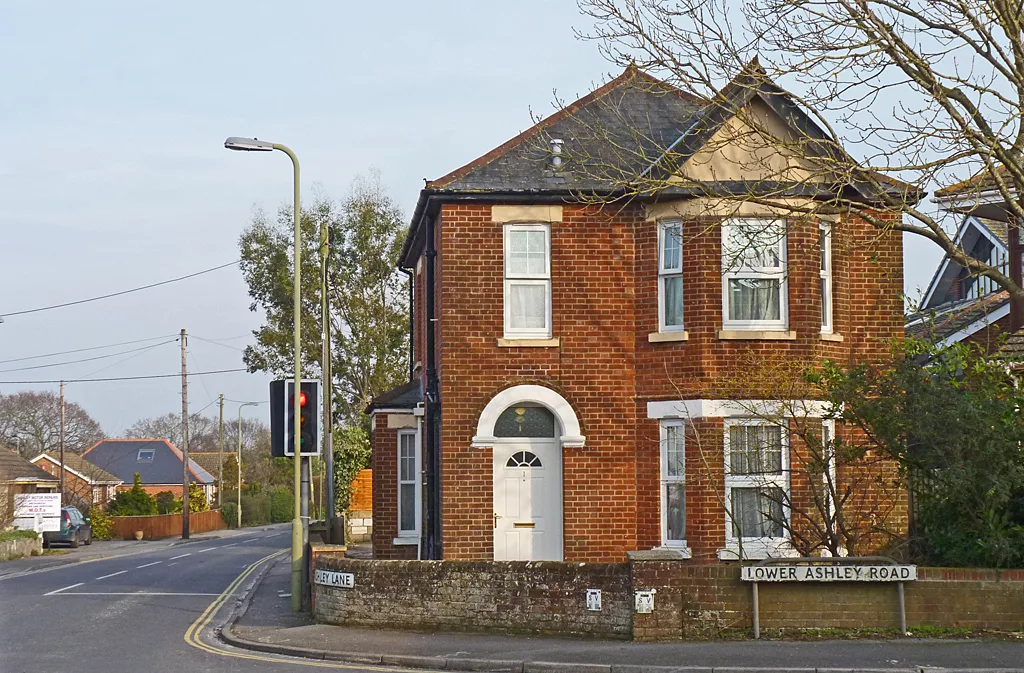
Modern Technology for Traditional Houses : Matthew Knight, Technical Engineer at IG Lintels, has described how the IG team used modern manufacturing methods to deliver arch brick feature lintels to compliment the traditional style of beautiful homes in Nottingham. What challenges did this project present? The main challenge on this job was that the houses required a walk through arch to the main entrance door. To achieve the architect’s vision for the project, we needed to ensure the steel soffit wasn’t visible on the bottom of arch as people would physically walk through it. As this was a live site, we also needed to develop a solution that reduced the need for skilled labour on site. Another challenge we faced was the tight time restraints on this project, the client required a short lead time so it was also important to take this into consideration during the design process. What solutions were developed to overcome these challenges and why did you choose these options? The way in which we overcame the first challenge was to supply a feature brick radius arch lintel which was faced to the front, rear and underside, by doing this no steelwork was visible on the arch. To overcome the tight time restraints, we came up with a solution to meet the clients’ needs and deliver the results on a short time scale. Our production team manufactured all the steel backing lintels and then we received a consignment of the brick type used on site, we only needed to cut and bond the bricks to the already made lintels, shortening the lead time and meeting the customers’ requirements. What is your favourite architectural feature on this project? The feature brick entrance arches which we supplied throughout the site on the two house types were definitely my favourite architectural features on this project. We used modern techniques to save time on site while still delivering a solution which complimented the traditional style of houses. Why did you enjoy working on this project? I enjoyed working on this project as it gave me the opportunity to work closely with the architect throughout the project. We designed and supplied a range of products that met the logistical requirements of the client without compromising the aesthetics of the design. We delivered a solution that perfectly complimented the traditional style of these homes. Manufacturing & Engineering Magazine | The Home of Manufacturing Industry News
Kalsi Plastics Moves to Bigger and Better Facilities
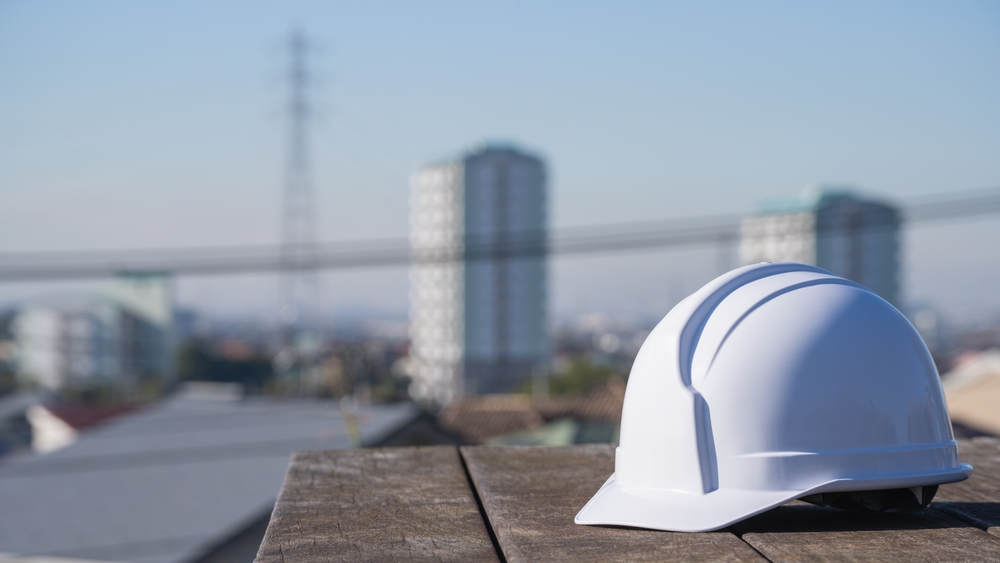
Birmingham-based, Kalsi Plastics, has moved to new, state-of-the-art facilities following a hike in turnover and a successful bid for lucrative funding. The company has carved a leading reputation in the plastics industry, establishing itself as a choice manufacturer and supplier of high quality, maintenance free plastic products for use in construction. Since its founding in 1993, Kalsi Plastics has developed a vast range of products, including: rainwater systems, soil waste systems, sewer systems and building materials. Each are manufactured by the companyâs in-house extrusion and injection moulding facilities with products certified to meet, and exceed, British Standards. The new purpose-built facilities in Sparkhill will provide the extra production capacity needed by the business as demand for its products soar. Construction is under way at the site and the 80,00 sq ft facilities are expected to be fully operational by the summer this year. In turn, Kalsi Plastics is predicted to increase its staffing levels with the employment of up to 20 new staff. As such, the new facilities will not just be a major boost for the company but also the local area from which many of its staff are sourced. The development is backed by Barclays Asset Finance. The banking group has provided £3.5m in funding which covers the construction of the new facilities as well as a number of new extrusion lines to be fitted inside. Kalsi Plastics has enjoyed a close relationship with the back for over 20 years and Andy Perry, Relationship Director at Barclays in Birmingham expressed his support for this latest investment. Kalsi Plastics has enjoyed year on year growth over the past ten years and its turnover has increased to in excess of £30m. The company has made committed investments in all aspects of the business over the last three years, and much of its success can be attributed to its dedication to emerging technologies. Amongst an eco-friendly fleet and the innovation evident in its products, this latest investment is sure to spell new promise for the Birmingham manufacturer.