Ford Becomes the First to Make Foam and Plastic from Recycled CO2
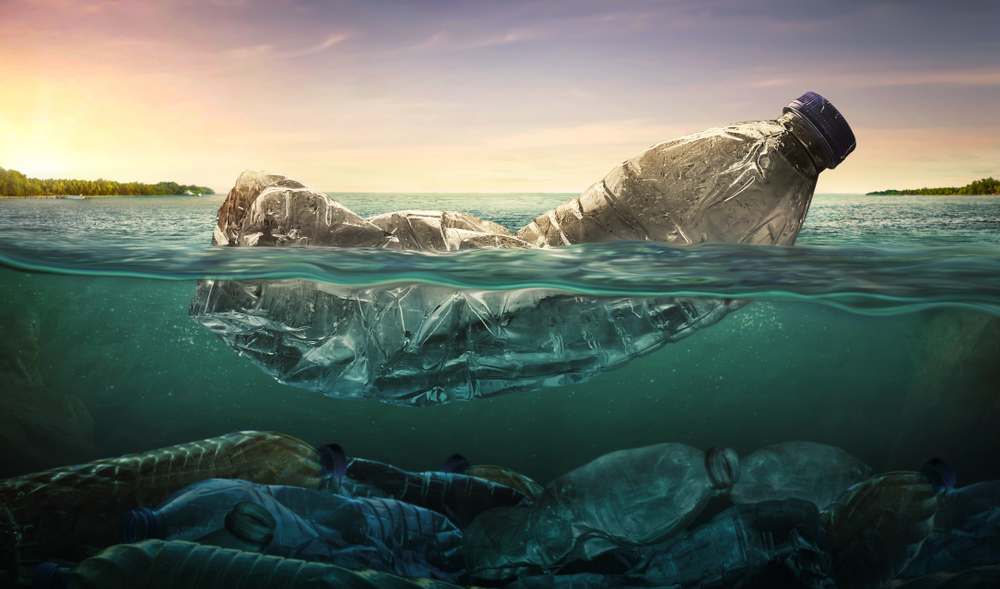
Leading automotive manufacturer, Ford Motor Company has become the first to create both foam and plastic components by harnessing capturing carbon dioxide. Made with up to 50% carbon dioxide-based polyols, the material â used widely for a number of vehicle components â has been proven to meet even the most stringent automotive test standards and could be rolled out across Fordâs entire car line. Since 2013, Ford has partnered with a number of experts in sustainability. This latest wave of innovation comes a result of collaborating with US-based firm, Novomer â a company specialising in CO2 capture and re-use in manufacturing settings. Should the new, effectively recycled, materials be employed in seating and underhood applications, the company has suggested a reduction in its petroleum use by some 270,000t. Using the CO2-derived foam composite will therefore reduce the use of fossil fuels and non-renewable energy sources in Fordâs production process significantly â something of growing consideration for investors and consumers alike. Debbie Mielewski, Senior Technical Leader of Sustainability at Ford senior, was keen to emphasise that such an innovation was wholly motivated by the desire to reduce the multinational firmâs carbon footprint as well as operate more responsibly toward the environment. And as Mielewski points out, Ford are certainly leading the charge; this is just one in several developments in CO2 capture and re-use by Ford and could encourage wider participation amongst the sector. The targeting of foam and plastic products by the automotive leader is no accident. According to the British Plastic Federation (BPF), the manufacturing of plastics accounts for as much as 4% of the worldâs overall oil use. Moreover, a significant amount of greenhouse gases (including CO2) are released into the atmosphere during plastics production owing to their hydrocarbon composition. Transforming how plastics are produced, i.e. by introducing a more sustainable point of origin, could see a drastic reduction in net CO2 emissions which are current released at a rate of over a kilo per second. For nearly 20 years, researchers at Ford have worked hard to pioneer more sustainable foam and plastic products; in the US, for instance, foam made from soy is present in every vehicle. In fact, the F-150 model is almost entirely made out of recycled products, including: coconut fibre boot liners, mirror gaskets made from recycled tires and soy, and interior carpeting made out of recycled T-shirts and denim.