ZAF Energy Systems Opens Research and Development Facility
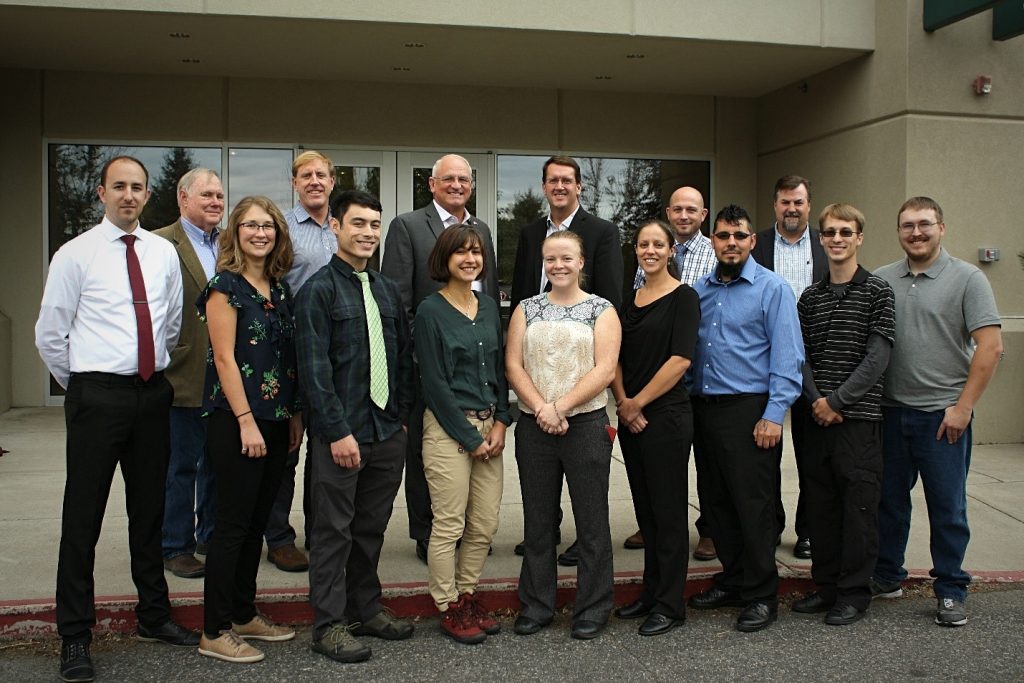
ZAF Energy Systems Inc. (ZAF), a developer of next-generation battery technologies, announced the opening of its new state-of-the-art research and development facility in Bozeman, Montana. ZAF’s team of scientists and engineers at the 8,000-square-foot facility are developing advancements in the company’s proprietary nickel-zinc (NiZn) battery technologies with an emphasis on continued performance improvements and cost reduction. The facility is located near Montana State University and will have a working public-private partnership with the university for advanced research. “Our proximity to and partnership with the top talent at Montana State University’s Energy Research Institute will enable ZAF to stay at the forefront of battery technologies,” said Randy Moore, ZAF president and CEO. “The research to be done at our new facility is critical not only to making further performance and cost improvements to our current products but will also keep us ahead of the market for zinc battery technologies.” The new R&D facility complements ZAF’s 35,000-square-foot low rate initial production (LRIP) facility that opened in October 2017 in Joplin, Missouri, where the company’s nickel-zinc (NiZn) cells and batteries are being produced. Recent investments from public and private sources have helped ZAF hire employees, expand production, forge strategic supply chain partnerships, and begin commercializing its NiZn batteries on a global scale. On November 16, ZAF CEO Randy Moore will provide an overview of the company’s nickel zinc battery technology at the Workshop on Zinc Battery Technology hosted by NAATBatt International at the Advanced Science Research Center at the City University of New York (CUNY). ZAF’s NiZn batteries have potential uses in a wide range of applications including: automotive, heavy trucking, remote telecom, renewable energy, and marine. NiZn batteries are poised to disrupt the $50 billion conventional lead-acid battery market with their ability to provide twice the storage capacity and three times the power of legacy lead-acid batteries in a smaller, lighter package. They provide a powerful and affordable alternative to their lead-acid counterparts while generating a lower environmental impact.
Torqeedo Launches Lithium-Ion Battery for the Marine Market
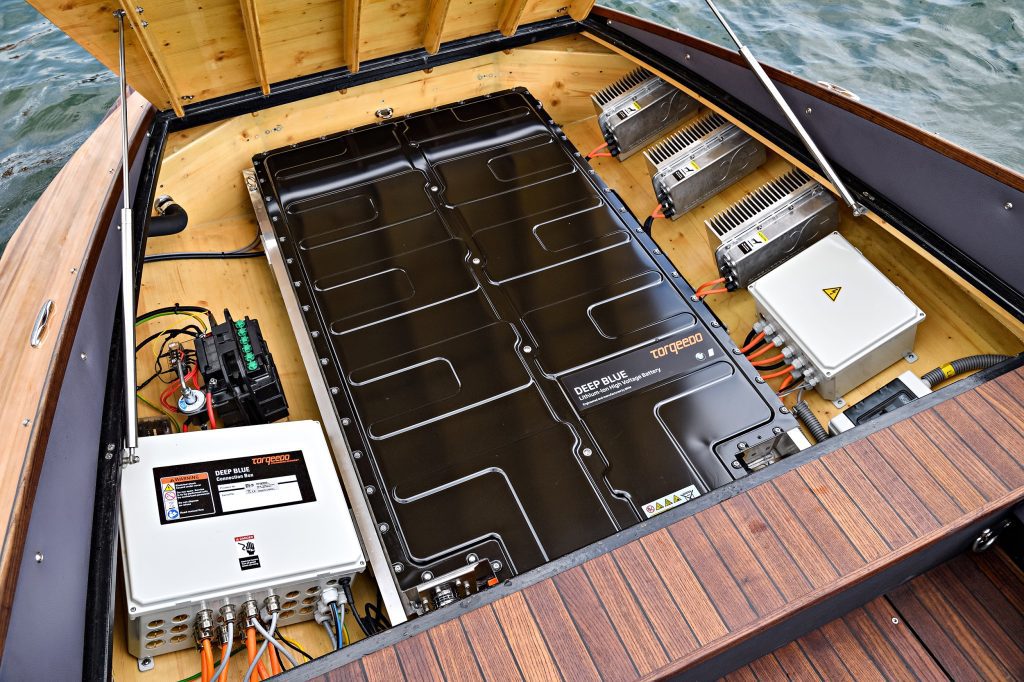
Torqeedo continues to bring the best of automotive technology to the marine market with a more than 30% capacity increase for its Deep Blue lithium-ion battery with technology by BMW i. The new 40 kWh Deep Blue battery (i3-type) brings the latest in automotive-grade lithium-ion technology to the marine industry, offering an increase in energy storage capacity with no increase in footprint. “The Deep Blue series of high-power electric motors are now available in 25 kW, 50 kW or 100 kW power ratings and in outboard, inboard or saildrive configurations. This means larger, faster and more types of boats can now experience the convenience and luxury of clean electric propulsion,” said Torqeedo CEO, Christoph Ballin. “The 40 kWh Deep Blue battery not only extends the range of Deep Blue-powered vessels by more than 30%, it also provides plenty of storage capacity for all onboard needs,” he continued. Produced at the BMW plant in Dingolfing, Germany, the high-capacity battery consists of eight modules, each with 12 storage cells. It has been tailored by Torqeedo so that it is suitable for the marine environment, modifying characteristics such as external shock protection and cooling. Torqeedo also continues its offer of a nine-year limited battery capacity warranty. The new Deep Blue battery features an industry leading energy density of 144 Wh/kg and a comprehensive safety system. It can be charged up to 75% capacity in as little as 1.5 hours when properly equipped and with adequate shore power. Torqeedo is the market leader for electric mobility on the water. Founded in 2005 in Starnberg, Germany, the company develops and manufactures electric and hybrid drives from 0.5 to 100 kW for commercial applications and recreational use. Its products are characterized by an uncompromising high-tech focus, maximum efficiency and complete systemintegration. Torqeedo is part of the DEUTZ Group, one of the world’s leading independent suppliers of diesel and natural gas engines
Dyson Streaks Ahead in Battery Storage Sector
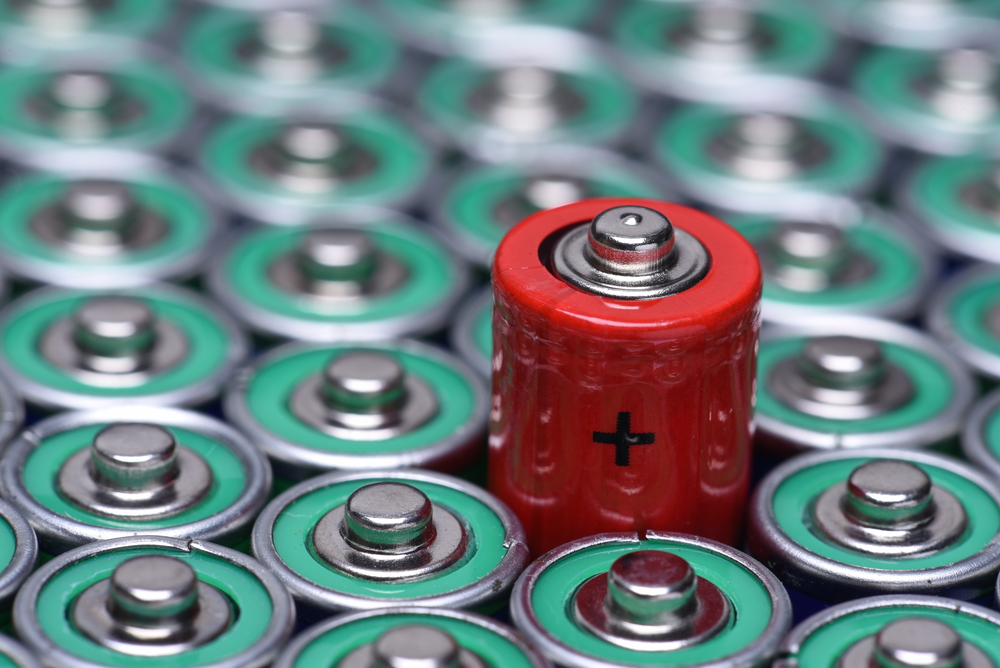
World-leading vacuum cleaner manufacturer, Dyson has ambitions to diversify its product range and has announced plans to conduct further pioneering research and development into battery technology. The home-grown, multibillion pound UK company, approaching its 25th anniversary, has already invested over £100m over the past five years researching batteries and their potential in the future. Max Conze, Chief Executive of Dyson has, however, pledged that that figure will rise to £1bn by the year 2020. He insisted that energy storage and, in particular, energy density, was the greatest engineering challenge in the 21st century. The company is hoping to produce statistical data and innovative designs that support the development of batteries for future use. It is has suggested that a battery capable of twice the energy density and storage of existing batteries would be of significant benefit to mobility in the future. Dyson has, for a number of years, expressed a keen interest in the battery market. Back in 2014, the company took a shareholder stake in the US-based battery manufacturer, Sakti3, before acquiring the company outright. Sakti3 is known for developing solid-state lithium-ion batteries, a much lighter and more powerful series of batteries than those currently on the market. Before the merger, the vacuum cleaner specialist has also previously some $15bn in Sakti3âs researc hand development programme â an investment which contributed to the invention of a battery with twice the storage capacity and at less than a third of the cost. And while the last weekâs budget may have brought bad news to many, it has in fact provided a stepping stone for Dyson on its route to battery prestige. The government has awarded the company £16m to continue its research into increasing battery storage and energy density. Despite renewed emphasis on battery storage, the company continues to carry out major research in a number of sectors including anything from aerodynamics to robotics and artificial intelligence. And with robot vacuum cleaners surely on the near horizon, Dyson remains at the top of its game in the vacuum cleaner industry, and on its way up in a good number of other lucrative sectors.
UK Consortium Set Up to Improve Battery Technology
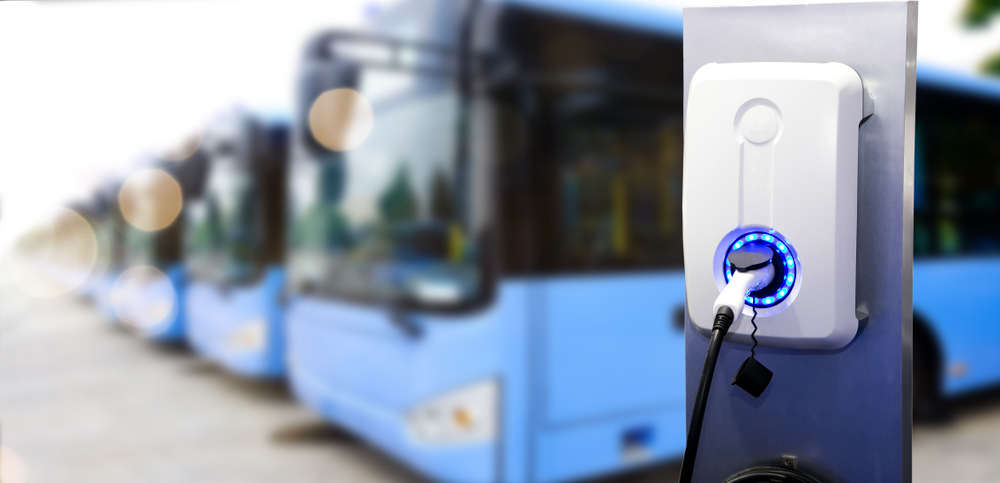
A consortium of British companies has been given extra funding towards the five and a half million pound project that is aimed at taking battery technology to the next level key to the future of high performance vehicles with low carbon emissions. The UK Automotive Battery Supply Chain is fronted by AGM Batteries and includes Johnson Matthey Battery Systems, Cosworth, Warwick Manufacturing Group and Dukosi. Although the UK already has a strong base for battery research the UK automotive industry gets most of its batteries from abroad. The UK Automotive Battery Supply Chain project is hoping that not only will there be further innovation of battery technology but also grow the number of batteries that are produced domestically. The extra funding for the project has come from the Advanced Propulsion Centre. This ten year, one billion pound partnership between government and industry was set up a little over two years ago in 2013 with the objective of building the UK’s capabilities from research to development and finally industrialisation of these new low carbon technologies. This funding along with the amount invested by the companies involved will allow the UK to cost effectively manufacture cutting edge battery technology. Talking about the creation of the consortium AGM Batteries director of business development Ian Whiting highlighted the UK’s existing strengths in battery research and automotive manufacturing and that bringing together the specialisms of each company will allow them to take it to the next level. Each member of The UK Automotive Battery Supply Chain project brings a different specialism to the table each needed to make the project a success. AGM Batteries will be responsible for scaling up these new cells to a real world manufacturing level while Warwick Manufacturing Group brings expertise in design for manufacturing and electro-chemistry. Dukosi brings battery management and ‘on-cell’ electronics.