Could Apprenticeships Boost the Post-Brexit Economy?
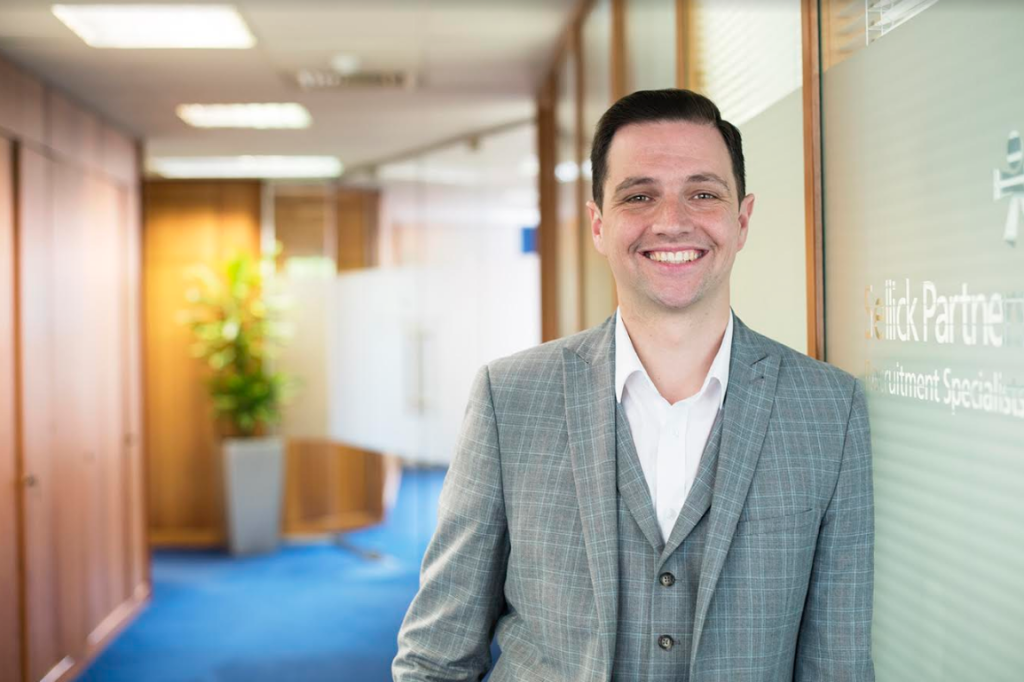
Could Apprenticeships Boost the Post-Brexit Economy? : The Apprenticeship and Levy report from the Office for National Statistics (ONS) has shown a 6.6 percent rise in the number of apprenticeships started in the 2018/19 academic year, compared with the previous year. This comes as wage growth in the UK reached its highest rate since 2008. The economy is growing and businesses are tentatively hiring, with our own analysis at Sellick Partnership showing a seven percent rise in temporary placements and a 17 percent rise in permanent placements over the past 12 months. Yet this could all grind to a halt in the event of a no-deal Brexit, with the International Monetary Fund this week warning that such a scenario is one of the chief threats to the global economy. And a no-deal has just become increasingly likely thanks to the appointment of Boris Johnson as Prime Minister. But could apprenticeships help businesses to navigate the turbulent waters ahead? As we can assess from the ONS data, many companies already see the value in hiring apprentices. This may be partly down to the government’s Apprenticeship Levy, which allows companies to reinvest funds they contribute to the levy into the training of their own apprentices. But there are many other benefits to apprentices that business owners would be wise to consider when planning for Brexit and the upheaval this could cause. Employer brand is everything When times are tough, businesses need the very best talent working for them and this is only possible if you have a strong employer brand. The benefit with apprentices is that you have the opportunity to mould them to your own culture and way of working. Apprentices are often – though not always – in the first stage of their career and have not yet become accustomed to a single way of working. This means business owners can ensure they become the right fit for the company and represent it in the best possible way. The investment you make in apprentices is very often repaid in their loyalty and commitment to the business, helping you to create a strong workforce and equally strong company culture and brand. Plugging your own unique skills gaps While skills gaps in certain sectors like STEM are widely reported and known, your business is likely to have its own specific needs. Apprenticeships can help you to plug those gaps, as you are able to choose from a wide array of apprentice programmes to find one that fits your requirements. With Brexit already resulting in a loss of EU talent, there may well be further shortages in the months and years ahead. Businesses that move now to identify potential shortfalls could find that apprentices are an effective way to prevent those talent gaps from appearing in the future. Maximising your existing workforce A common misconception is that apprenticeships are only suitable for school leavers in the early years of their careers. I have personally dealt with a number of more mature and highly experienced apprentices who wish to retrain and explore a new career path. If you are looking at scaling back your workforce or wish to capitalise on the skills and people you already have, you should consider whether an apprenticeship might be a good fit for someone in your existing team. This could help you to retain talent, boost job satisfaction and ensure you have the right people in the right roles during potentially challenging times. Investing in home-grown talent While there are many benefits of apprenticeships to businesses on an individual level, it is also important to consider the advantages to the British economy as a whole. With EU workers leaving the UK at a steady rate since the Referendum, there will undoubtedly be staff shortages in industries predominantly staffed by European nationals. Investing in home-grown talent – through education from school level upwards and training such as apprenticeships – is an effective way to plug this gap and to boost the career prospects of future generations. Apprenticeships can require a lot of investment in time and money from the business owner with no guarantee that the recipient will stay loyal to the company once their apprenticeship ends. Yet in the many years I have recruited apprentices, I have very rarely seen people leave after the first year. In fact, the vast majority go on to become loyal, trusted and highly skilled members of the workforce. In anticipation of the challenges that lay ahead, I would urge business owners to consider this option as an effective means of building the best possible workforce to withstand the turbulent times. Manufacturing & Engineering Magazine | The Home of Manufacturing Industry News
adi Group Looking at the Future with Pre-Apprenticeship Scheme
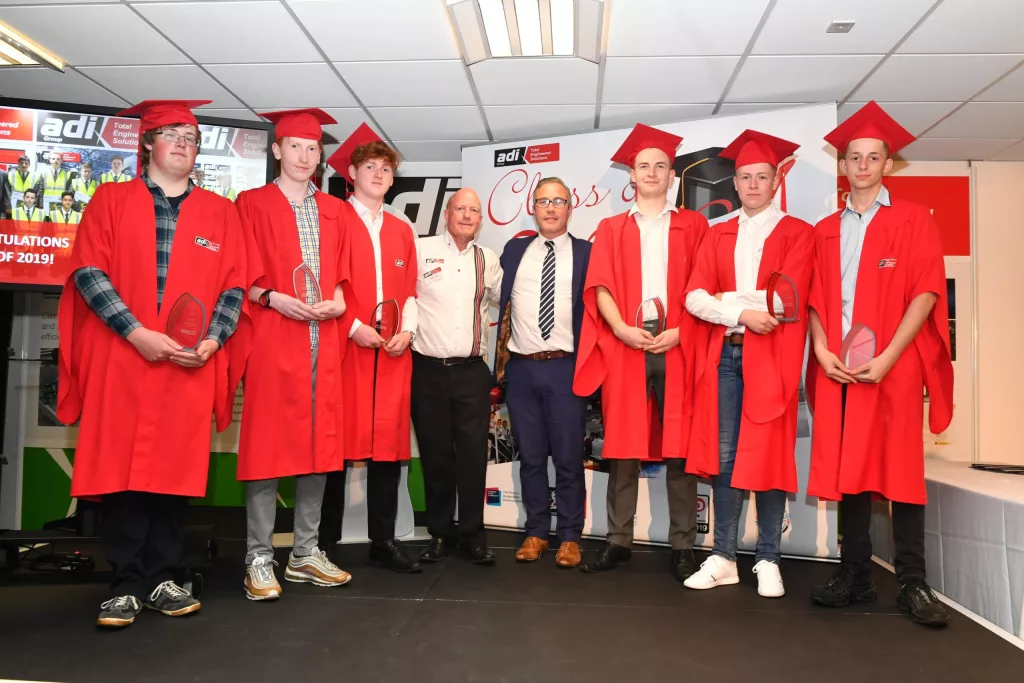
A leading engineering firm’s commitment to addressing the UK skills gap has been celebrated with the graduation of 11 students from its pioneering pre-apprenticeship scheme. In front of a packed audience of influential business leaders, mentors and proud parents, the youngsters, donning university-style graduate gowns, collected their course certificates at adi Group’s headquarters in Kings Norton, Birmingham. And, underlining the scheme’s achievements, it was announced on the night that two lucky students would move on to a full-time apprenticeship at the multi-disciplined engineering firm. Discussing his achievements, Bromsgrove student Lewis Smith, 16, said: “It’s really been a unique experience. I know now that when it comes to applying for full-time work in the future, I’ll have something over the competition. “Mechanical and electrical engineering are two sectors to get great experience in, so I’m really looking forward to what the future might hold.” “Everyone was really welcoming and friendly,” said 16-year-old Travis Cashmore about the experience. “The mentors made it really easy to get used to the work, so I do feel like I have some great skills to take into full-time work.” The firm’s pre-apprentice scheme, which was the first to launch in the UK, offers local students aged 14 to 16 the chance to learn hands-on engineering skills in a real working environment. For one afternoon a week for two years, talented youngsters get the chance to earn an EAL accredited qualification. Past students on the successful programme have included 17-year-old Abbie Beaver, now a fabrication and welding apprentice at the firm, and one of the top female engineers in the UK, as named by the Women’s Engineering Society. Commenting on the night and the students’ achievements, adi Group strategic account director James Sopwith said: “At adi we firmly believe in the need to expose youngsters to potential new career pathways at a much earlier age. “Last night was not only evidence of the success of our approach, but also a demonstration of how committed we are to making our communities much more sustainable. “Our investment in these students extends far beyond just delivering quality local jobs, it’s also part of an ethos here at adi to engineer a better future, where businesses and schools of all sectors work together to improve prospects across the region. “As a company that works with some of the biggest brands in the world, we’re looking forward to showing these students even further the exciting work available on UK soil.” Far from just being just an adi initiative, the company has drawn up a guide for other UK businesses to copy their model and create similar partnership with local schools. The scheme is especially relevant after Government figures recently revealed that over 20,000 engineering candidates would be needed annually to fill roles at companies in the West Midlands alone. As one of the companies that has already exceeded its commitment to having five per cent of its full-time workforce made up of apprentices by 2020, James is confident adi is delivering on the youth skills front. “We’ve really been ahead of the curve when it comes to apprenticeships,” he said. “What we’re hoping to do is equip thousands of young people with the practical skills that businesses need, but we can’t do it alone. “Right now, we’re calling on companies across the region to follow the path we have set up with pre-apprenticeships and address the UK skills gap before it is too late.” The adi Group is a major Birmingham engineering firm with over 30 specialist divisions serving household names across the UK and the Republic of Ireland. Manufacturing & Engineering Magazine | The Home of Manufacturing Industry News
MGTS Increases Apprentices for Food and Drink Industry
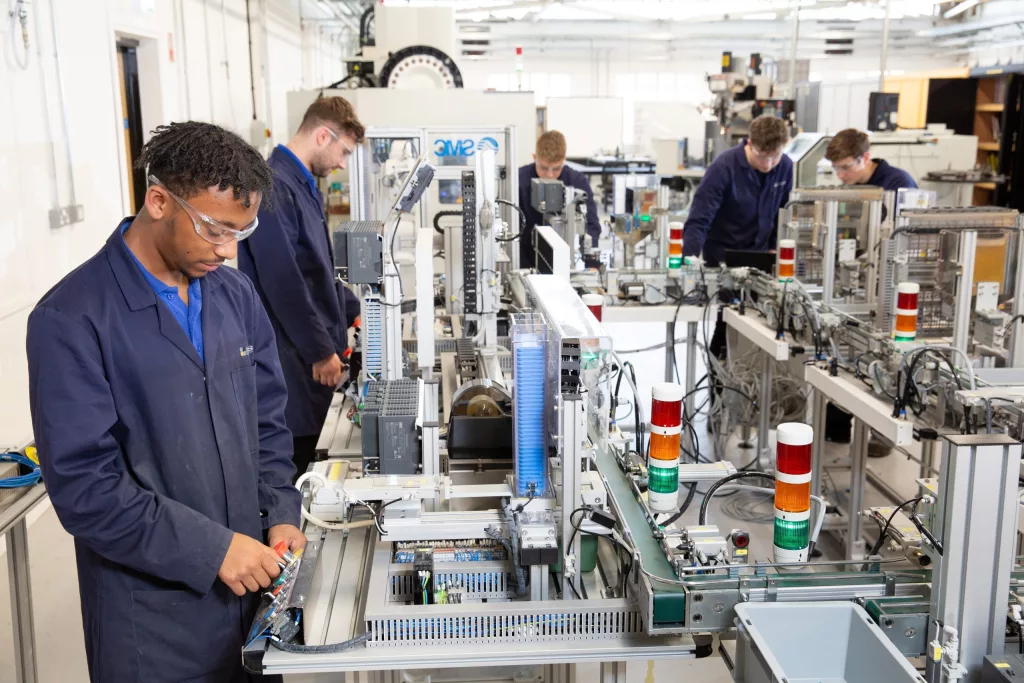
Midlands based MGTS, a leading specialist training provider for engineering food maintenance and food process manufacturing industries, announced it had doubled its capacity in delivering apprenticeships for the food and drink industry. The employer-led and membership-based charity is celebrating this announcement with an official opening on Friday, 5 July by Redditch MP, Rachel Maclean. MGTS already train 800 apprentices at any one time across the whole of the engineering industry. It has invested in its Redditch facility and has doubled the space devoted to apprenticeship training for the food industry by 355m2, refurbishing and equipping this space with industry standard equipment. The additional workspace supports the demand of an ever-growing food and drink engineering maintenance apprenticeship programme. MGTS has already delivered this apprenticeship programme for seven years at its engineering academy within Reasheath College with increasing numbers of starts each year. The additional space enables MGTS to build on its offering to budding engineers from around the UK and local firms. Already working with the cream of the food and drink industry, including Müller, Arla, Ferrero, Dairy Crest, Morrisons and Heineken, this expansion will help the whole of the food and drink industry to recruit much needed, highly skilled engineers. David Bridgens, CEO of MGTS, said: “The country needs skilled engineers and that applies particularly to the food and drink industry. We are playing our part by increasing the numbers of apprentices. This would mean that our yearly intake capacity would be 100; circa 50 at each site. This is a fantastic time to build a career in food process manufacturing and we can help individuals develop the necessary skills and businesses recruit a trained workforce. Its’ a win-win for everyone involved.” Naboth Tinarwo of Arla Foods added: “Engineering and maintenance skills are of vital importance to the food and drink sector. Our dairy industry like any other in the UK is faced with massive engineering skills shortage needed to drive efficiency, innovation and productivity. “Arla Foods and MGTS have been tirelessly working together for the past 10 years to developing these engineering skills and will continue to do so in order deliver these capabilities. Arla foods welcomes the huge investment and commitment that MGTS is putting into increasing of training capacity and infrastructure, and I am convinced that we share the same ambition and we will continue to recruit more apprenticeships through this programme.” Brandon Smith, an apprentice from Morrisons, commented on his apprenticeship: “Since starting my career as an engineer I have noticed myself viewing everyday situations a lot more logically. It has introduced me to new subjects I never thought I would be interested in.” For more information about the event or apprenticeships for the food and drink industry, visit www.mgts.co.uk or contact Ian Amis on 02476 630333. Manufacturing & Engineering Magazine | The Home of Manufacturing Industry News
Case Study – Holly Dore’s Work Experience at Superior
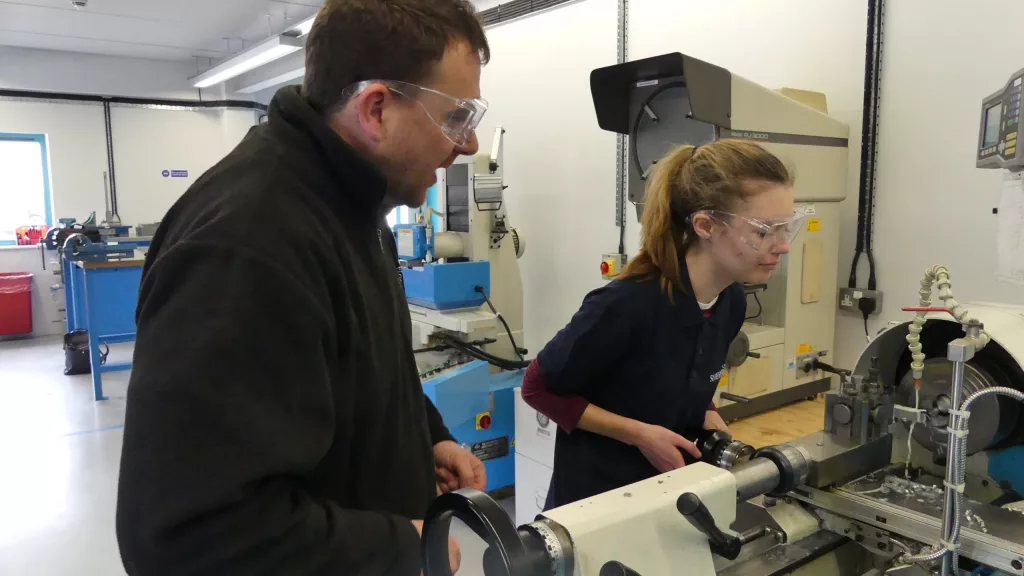
Work Experience : Holly Dore, 17, from Blandford, is set to become an apprentice in September at Superior, based in Ferndown, Dorset. She is currently studying for her A-levels in physics, biology, chemistry and Level 3 Core Maths at Queen Elizabeth’s School in Wimborne. Before signing up for an apprenticeship, she joined the team at Superior, a leading manufacturer of high integrity o-rings and seals, for work experience so that she could find out more about the company. Q: When did you start your work experience at Superior? A: I had three days of work experience in 2018 and then came back for three more days in April 2019. Q: How did you hear about Superior? A: At our school we have an apprenticeship fair, so there are loads of different companies there. I went round to speak to the different companies and the Superior team were really nice. I asked if they offered work experience and they said that they did. Superior also runs The QEube event at my school’s annual ACE Festival, which is a sports and charity event. Q: What did you do on your work experience? A: Last year I made a brass g-clamp and a g-clamp screw, and then I made several screws of different types to see which one is best. This year, I was involved in solving a real engineering problem (Holly was involved in solving a real engineering problem, it wasn’t set up – this was a real scenario where Holly made a part to support one of our manufacturing facilities) where parts were getting stuck on a sensor. We made a small acrylic guard for the machine, which was then given to the quality team to test. We made it using the CNC mill and tested it where we realised that it needed another groove and so we re-wrote the programme that I drew for the machine. We also made a an O-ring jig using a manual lathe. I was using the programme on the computer for the CNC lathe, so you draw the programme on the computer and then it will make the part for you. The training manager has been helping me during my work experience, I got to walk around and see what other people were doing in different departments. I am proud of everything that I have done, as I wouldn’t get to do any of it normally. Q: Would you recommend work experience to other young people? A: I think work experience is really valuable. Before I came to Superior, I knew that I wanted to work in engineering and I’ve always been interested in science, but it’s quite a broad term, so I wasn’t sure what that entailed and what parts I would enjoy. Now that I have finished the work experience, I realise that this is something that I really want to do. It’s good fun. Q: In September, you will join Superior’s in-house Academy. What made you choose to go onto an apprenticeship? A: An apprenticeship made more sense to me because you can gain a degree with Superior and you can learn practical skills rather than just sitting in a lecture hall at university, and you get to do it within a company. Superior has its own in-house Apprenticeship Academy on-site, offering apprenticeships to students as young as 16. It gives apprentices the chance to learn about engineering, science and manufacturing and all apprentices are given the opportunity to gain a degree. Manufacturing & Engineering Magazine | The Home of Manufacturing Industry News
Sony Launches Innovative Apprenticeship Scheme
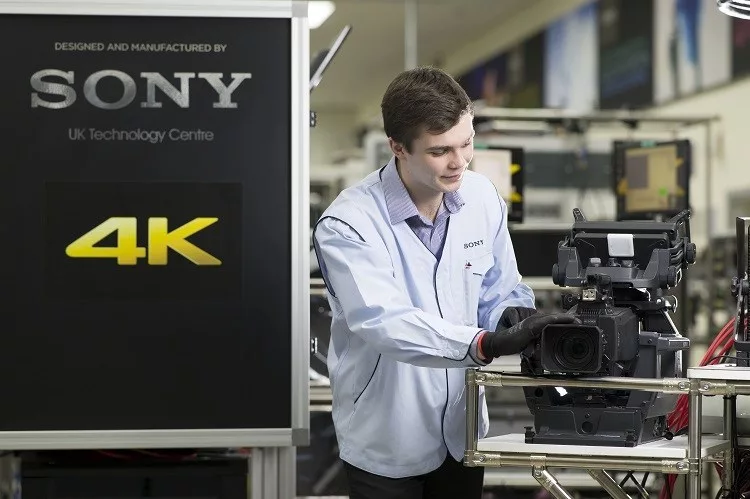
Sony UK Technology Centre, one of Wales’ leading manufacturers, is calling on innovative, driven, and passionate individuals to sign up for its new apprenticeship. Sony UK TEC Apprenticeship scheme, which is now in its sixth consecutive year, officially launched on February 1st with applicants encouraged to apply before the February 28th closing date. The industry-leading initiative supports career-driven individuals to further their education and gain qualifications throughout the scheme. The company’s onsite academy drives and coordinates their full studies, all while the apprentices gain invaluable working experience at one of the world’s leading manufacturing sites. During the four-year scheme apprentices will get the opportunity to work across a variety of departments, including Software Engineering, Production Engineering, and Development Engineering and Robotics. They will help to develop internationally renowned products including 4K broadcast technology, the Raspberry Pi, smart office solution Nimway, and smart city technology. Over 30 apprentices have taken part in the successful internal scheme since its inception, with all participants praising its diverse offering. Cecilia Fritz, Head of HR and Training Strategy said an apprenticeship with Sony UK TEC opens up a “vast wealth” of opportunity for any student looking to advance and develop their career. “Our apprenticeship is a thorough and diverse programme which offers new starters an in-depth insight into all aspects of Sony UK TEC’s highly successful engineering operation. We believe that this varied approach creates highly skilled and well-rounded team players and opens up a vast wealth of opportunities to them within the industry as a result. At the end of their four years, they are fully equipped with the ability, and knowledge, to become some of the sector’s brightest engineering talents and to drive genuine progression in the fields of technology and manufacturing,” said Cecilia Fritz. To apply for a place in the Sony UK TEC Apprenticeship scheme applicants must have a minimum of five GCSEs, including a B or above in Maths, and Cs or above in Science and English. Applications close at midnight on February 28th, with assessments due to take place on March 21st. Manufacturing & Engineering Magazine | The Home of Manufacturing Industry News
3 Big Changes Impacting Engineering In 2017
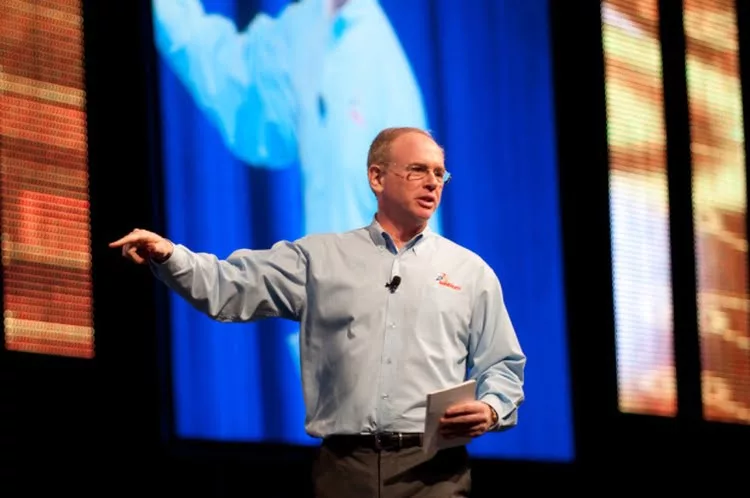
3 Big Changes Impacting Engineering In 2017 : The year has only just begun, but the engineering industry is already off at full force with three big changes happening now that you need to know about. Engineering software is finally moving to the cloud The first change happening that you need to know about is that engineering software is finally starting to move to the cloud. Engineers at computer aided design (CAD) gathered in Cambridge to showcase their improvements in the cloud software. The big picture for this new advancemens is that with CAD software running on the cloud it will enable engineers to collaborate in real time. It is believed that the time for change has arrived, Jon Hirschtick the Chief Executive Officer of Onshape said, I believe the work weâre doing can improve the way every manufactured product on earth is designed. Small firms are taking a hit The second change for 2017 is that business rates are becoming ticking time bombs for small companies in the UK. The government is aiming to give all businesses a fair deal and are establishing a £3.6bn transitional fund to help businesses facing big jumps in rates. However, these changes are being met with backlash as smaller businesses will be facing massive hikes while larger retailers benefit from reduced cuts. Christopher Richards from the Engineering Employers Federation said, “The inclusion of plant and machinery in business rates bills represents a tax on productive investment and undermines the international competitiveness of UK manufacturing.” Mastership may be the future of engineering The third change happening in 2017 is that there will be an introduction of an apprenticeship levy from April 2017, this means that employers will be able to take advantage of the available subsides and specifically be able to offer a higher skill degree level. A mastership is a level 7 apprenticeship degree with is the equivalent to a masterâs degree, the mastership is aimed at both employees with some experience or people who have already followed an academic trajectory. The mastership is built on a strong two-way commitment where employers invest in their employeeâs future. Words by Jim Starbuck Manufacturing & Engineering Magazine | The Home of Manufacturing Industry News
Apprentice Recruitment Drive Kicks Off At Bentley Motors
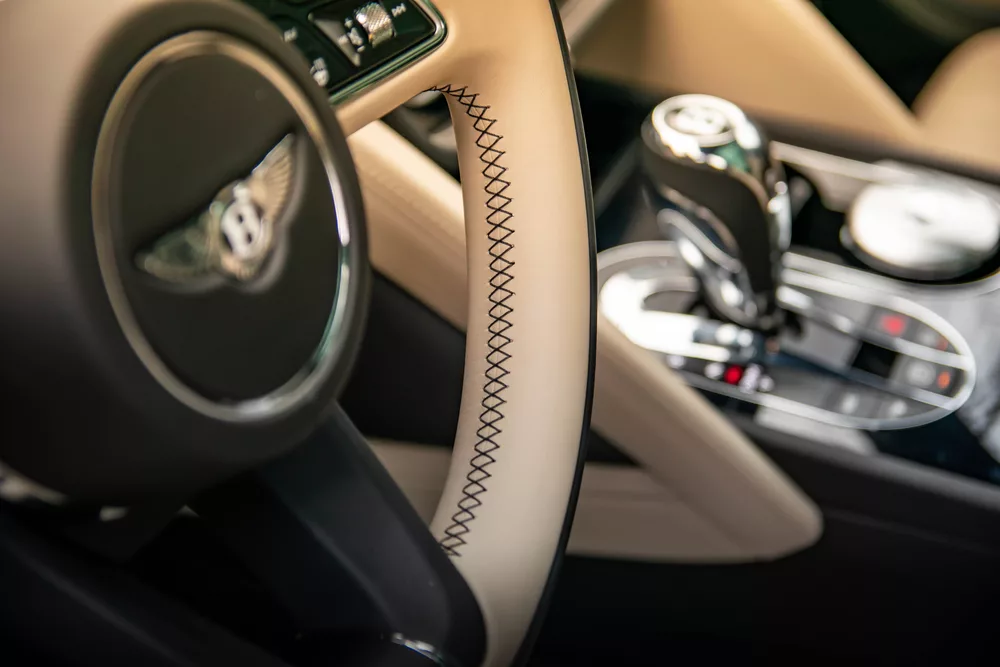
Working across a range of operations at Bentley Motors, the firm will welcome 42 apprentices in September 2016. Those eager to get involved can apply from March 12 with the online application process lasting six weeks. The day also marks an open day at Bentley Motors headquarters where those considering an apprenticeship with the company can learn more about its work, the sorts of careers available within the business, and why it has become one of the world’s leading luxury can manufacturers. The company’s apprentice scheme has run for over four decades offering an invaluable way of achieving academic recognition and relevant vocational qualifications alongside tailored development within Bentley Motors. In preparation for the recruitment drive, board member for human resources Marlies Rogait noted how Bentley Motors’ training provided the sorts of foundations people need to let their skills flourish. Across a range of fields, apprentices can learn the knowledge and expertise needed to push their professional careers to the next level. The drive is part of the company’s continued investment in people, recognising that its future relies on the next generation. Bentley Motors is not “afraid to challenge” he said, adding that it will continue to develop and add to its “highly-skilled and passionate” workforce. Most of the apprentices will begin on the newly developed manufacturing programme run by Bentley Master Trainers. This scheme aims to develop skills in areas such as wood, leather, mechatronics, paint and production maintenance. The other apprentices will have various focuses such as sales and marketing, engineering, purchasing and human resources Former production apprentice Matthew Farrell said Bentley Motors’ apprenticeship scheme was an ideal way to pursue both academic, technical and personal development goals. One of Bentley Motors’ current production engineers, Farrell said the programme provided an invaluable knowledge base across engineering operations with an important focus on the next generation of motorcar design. Manufacturing & Engineering Magazine | The Home of Manufacturing Industry News