Dassault Systèmes Partners with Advanced Manufacturing Research Centre
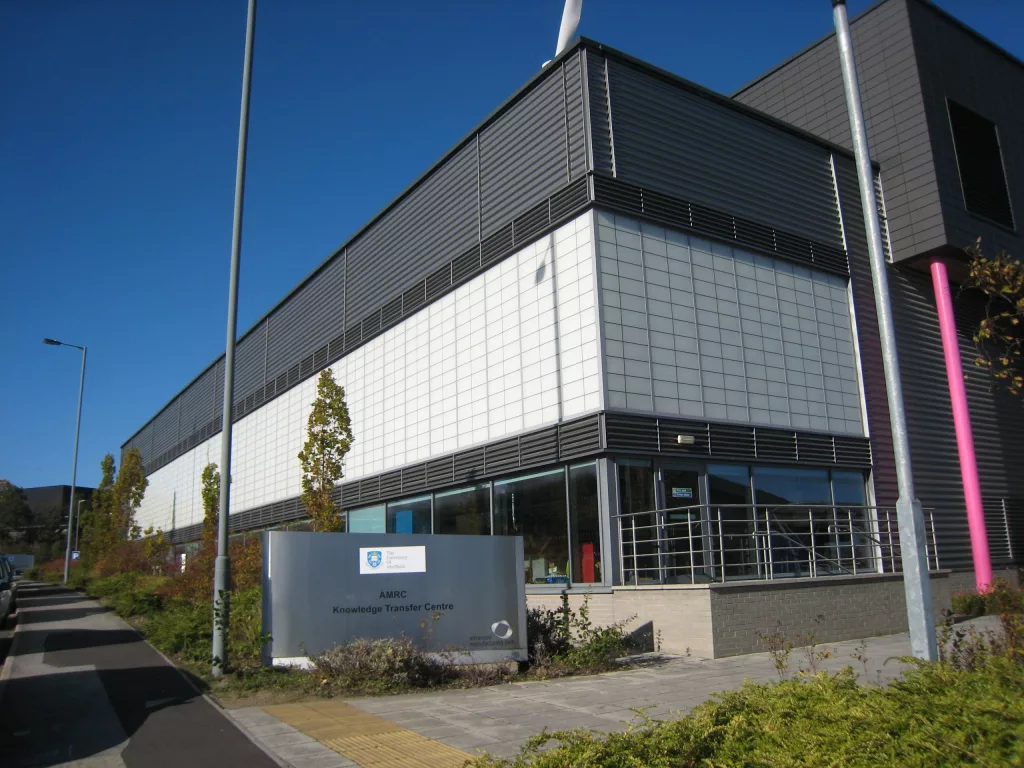
Dassault Systèmes has announced that it has become a member of the Advanced Manufacturing Research Centre (AMRC) in Sheffield, to support the UK manufacturing industry as it embraces automation, robotics and visualisation at all levels. The AMRC, part of the High Value Manufacturing Catapult, is a world-class research centre for advanced manufacturing, developing sustainable solutions to improve UK productivity, talent and skills. By introducing new ways of automatically assembling complex products and using advanced technologies such as robotics, augmented reality and large-volume metrology, the AMRC addresses the key operational challenges its partners face as they develop the factories of the future through digital transformation. Séverine Trouillet, Global Affairs Director, EuroNorth at Dassault Systèmes said: “We strongly believe that we have entered the Industry Renaissance, a new era where experience will be at the heart of everything we do, from the way we innovate to the way we produce goods. The tools of the Fourth Industrial Revolution, whether automation, robotics or visualisation, are the basis on which we are building a radically new world where entire sectors will be turned upside down. No industry will be transformed quite as much as manufacturing, which is why we are proud to be joining the AMRC and helping its members adopt a digital-first way of thinking, but also create the Future of Manufacturing at the heart of the industrial North.” As part of its AMRC membership, Dassault Systèmes will work closely with UK manufacturers to help deliver the Made Smarter Commission’s goal of transforming manufacturing through the adoption of digital industrial technologies. Working with the AMRC, Dassault Systèmes will help manufacturing maximise the benefits of virtualisation and modeling technologies to innovate faster, improve public–private collaboration and become sustainability champions in the UK. Last year, Corporate Knights – the gold standard for sustainability analysis – ranked Dassault Systèmes No. 1 among the top 100 most sustainable companies in the world. The ranking recognised Dassault Systèmes’ holistic sustainability strategy, from reducing its environmental footprint, to developing the workforce of the future and driving the definition of new business models in today’s Industrial Renaissance. Dassault Systèmes will also support UK industry as it tackles business transformation challenges, whilst turning the UK into the most innovative economy in the world through the use of game-changing technology. To celebrate its membership, Dassault Systèmes will also be engaged in a Made Smarter initiative, recently launched at the AMRC, to create an open-access Smart Factory test bed, which will allow companies to improve their productivity, reduce defects and time to market. Commenting on the news, Rab Scott, Head of Digital at the AMRC said: “British manufacturing has a track record of being among the most innovative and inventive in the world; it was the home of the First Industrial Revolution and it aspires to be the home of the Fourth Industrial Revolution. With Dassault Systèmes as a Tier 1 partner, the AMRC is ideally placed to deliver the sustainable step-changes in productivity that the UK economy desperately needs. Its suite of digital technologies strengthens the AMRC’s portfolio of advanced manufacturing capabilities and puts us in the forefront of Industry 4.0 research and development.” As the innovation hub of the Northern Powerhouse, the AMRC will work with Dassault Systèmes to help the industry prepare the workers of tomorrow. By anticipating the roles required for the future, and by digitally capturing the expertise of retiring engineers, it will be possible to minimise the risk an ageing workforce poses to the UK economy, ensuring that the manufacturing memory of its industrial base is not lost. This will allow for the continuity of innovation in the engineering process, whilst providing a platform for new roles to emerge in a world where information, innovation and production all benefit from the combined access to real and virtual worlds. A strong supporter of British innovation and knowledge sharing, Dassault Systèmes has been involved with the High Value Manufacturing Catapult’s National Composites Centre (NCC) for a number of years. It has helped develop new methods and technologies that have turned the centre into the UK’s hub for design and rapid manufacturing of high quality composite products. Leveraging the learning from its involvement with the NCC and the Bristol & Bath Science Park, Dassault Systèmes will bring similar opportunities to businesses and R&D labs at the AMRC. Manufacturing & Engineering Magazine | The Home of Manufacturing Industry News
McLaren Reveals New £50m Research Centre
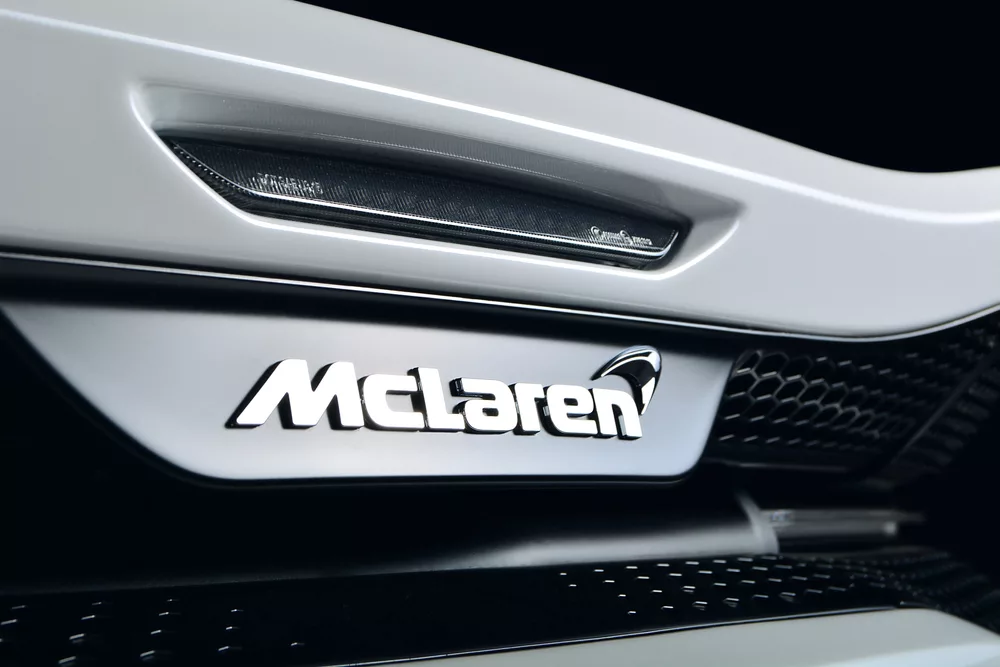
McLaren Automotive has announced the first details of its new Composites Technology Centre, which will be based near the Advanced Manufacturing Research Centre (AMRC) at the University of Sheffield. The Composites Technology Centre, which will be set in more than four acres and housed in a purpose built 7,000 sqm building, will be the first purpose-built facility outside of the current McLaren campus in Woking, Surrey. It was formed through a partnership with the motorsport giant, the University of Sheffield and Sheffield City Council. The new centre will be responsible for the development and manufacture of carbon fibre chassis, which will be used in future McLaren Automotive cars. It will reportedly make use of the latest automated manufacturing technology and techniques in conjunction with the AMRC. Work on the new centre is due to start soon, with the first pre-production carbon fibre chassis expected to be delivered in the second half of 2017, with the facility expected to be in full production by 2020. The new centre will also create more than 200 new jobs through combined investment of almost £50m, and will potentially save the company as much as £10m. It is also hoped that the new centre will add £100m of gross value added (GVA) to the local area by 2028, with opportunities for expansion thereafter potentially doubling that number to £200m. Bringing the production of carbon fibre chassis in-house increases the average value percentage of a McLaren car sourced in the UK by almost 8 per cent, from the current average of around 50 per cent, depending on the model. At the launch event at the AMRC in Sheffield, Mike Flewitt, CEO of McLaren Automotive commented: The now-iconic McLaren F1 was the worldâs first road car to be built with a carbon fibre chassis and every car built more recently by McLaren Automotive has the same. Creating a facility where we can manufacture our own carbon fibre chassis structures is therefore a logical next step. We evaluated several options to achieve this objective but the opportunity created by the Advanced Manufacturing Research Centre at the University of Sheffield was compelling. At the AMRC, we will have access to some of the worldâs finest composites and materials research capabilities, and I look forward to building a world-class facility and talented team at the new McLaren Composites Technology Centre. Article taken from The Manuacturer Manufacturing & Engineering Magazine | The Home of Manufacturing Industry News
AMRC Launches AMOS Project to Develop Pioneering Additive Manufacturing Repair Technique for Aerospace Industry
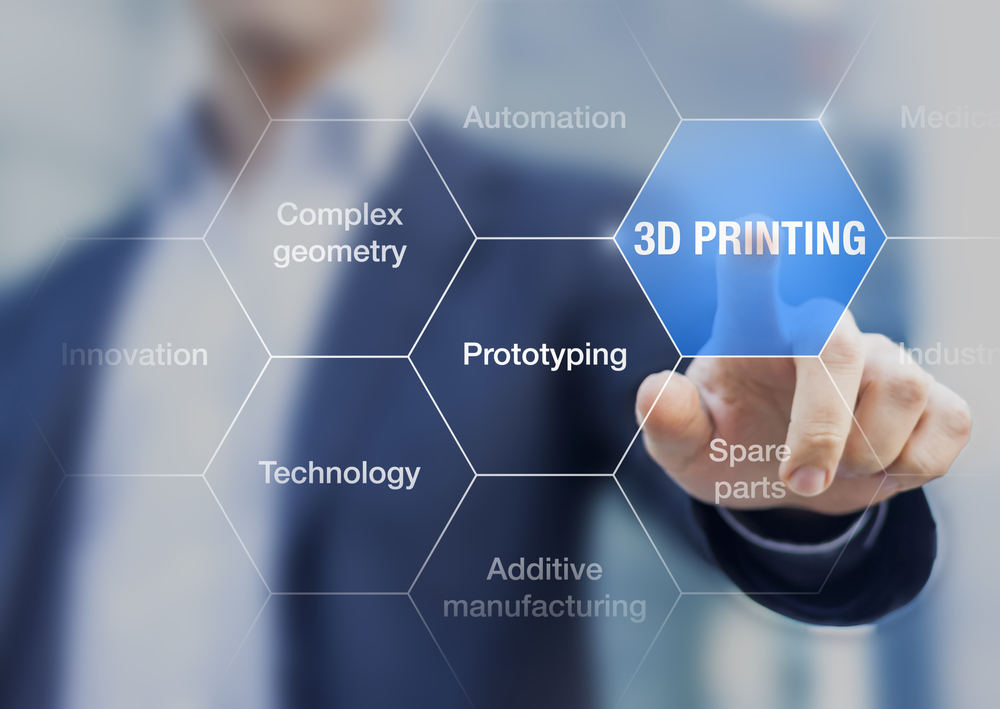
Experts in additive manufacturing at the Nuclear Advanced Manufacturing Research Centre (AMRC) are leading the way on a global scale in respect of developing pioneering repair and maintenance technologies for the aerospace industry. The research has been dubbed the AMOS project, a somewhat smaller a mouthful than Additive Manufacturing Optimisation Simulation platform for repairing and remanufacturing of aerospace components. It combines the intelligence, experience and resources of key manufacturers and researchers in Europe and Canada, and is led by University of Sheffield AMRC. The project is primarily geared toward exploring the potential of different direct energy deposition methods. The techniques entail combining conventional welding tools with automated control technologies with a view to increasing the accuracy with which metal powder or wire can be both deposited and melted. Since all manner of direct energy deposition techniques are evident across businesses within the aerospace sector â favoured for their ability to precision-manufacture parts to a degree elsewhere unseen â such research could provide the opportunity for further sector development and even open up AM technology to neighbouring sectors. The AMOS project will look specifically at those technologies already in use by partner or available on the market. Processes up for investigation and potential improvement include the wire-feed gas tungsten arc process, currently utilised for manufacturing the Nuclear AMRCâs bulk additive cell. Indeed, the Nuclear AMRC forms a key driver for the research and experts may well look into further technologies made use of by the research hub, including other AM techniques such as powder diode laser. From their investigations and research, industry professional and scientists alike are hoping to identify a way in which AM technology can be used to repair key aerospace components like landing gear and turbine blades. If found successful, such innovation could reduce both the time and cost associated with repair and maintenance works considerably. The initiative would could also improve the environmental identity of the sector as a whole, minimising material wastage during the process and, furthermore, prolonging the life of components which are both expensive to manufacture and properly dispose of. Dr Rosemary Gault, European Project Coordinator at the University of Sheffield AMRC was keen to stress the importance of the research, highlighting that while the sector is wholly dedicated to innovation, particularly in additive manufacturing, there is little focus on developing technologies specifically for repair and maintenance. Hoping to fill the gap, the AMOS project will inspect closely the various stages and aspects involved within the additive manufacturing process. Of significant interest will be how to maintain the integrity of the metal deposited as well as how to improve the precision of the deposition process, itself. With the help of technology specialists, researchers will also be looking to identify the advantages that automated control technologies represent to additive manufacturing technology in addition to fine-tuning the assembly of the net to produce a final, seamless â and therefore more durable â shape. As a final aside, and perhaps as a result of those findings, the AMOS project is expected to draw conclusions as to how strategies of additive manufacturing repair can be incorporated within the design of components in order to further improve efficiencies and lengthen the life cycle of parts. As such, it may well mark the creation of industry-complaint, best practice method with which to repair and maintain aerospace parts. The AMOS project consortium comprises a total of nine partners, spanning the globe from Canadian universities â McGill and Ottawa, and three further aerospace manufacturers, to Franceâs Central de Nantes and DPS. Also in the line-up are Swedenâs GKN Aerospace Engine Systems and, of course, the UKâs AMRC. It is thus made up of some of the biggest names in the sector and brings together the knowledge and specialisms of top research organisation, tier one manufacturers, and additive manufacturing and technology professionals. With such a broad range of high level expertise, it is unlikely the project will prove without positive conclusion.