Featuring Furniss and White: Interview with Sam Scholes, Development Manager
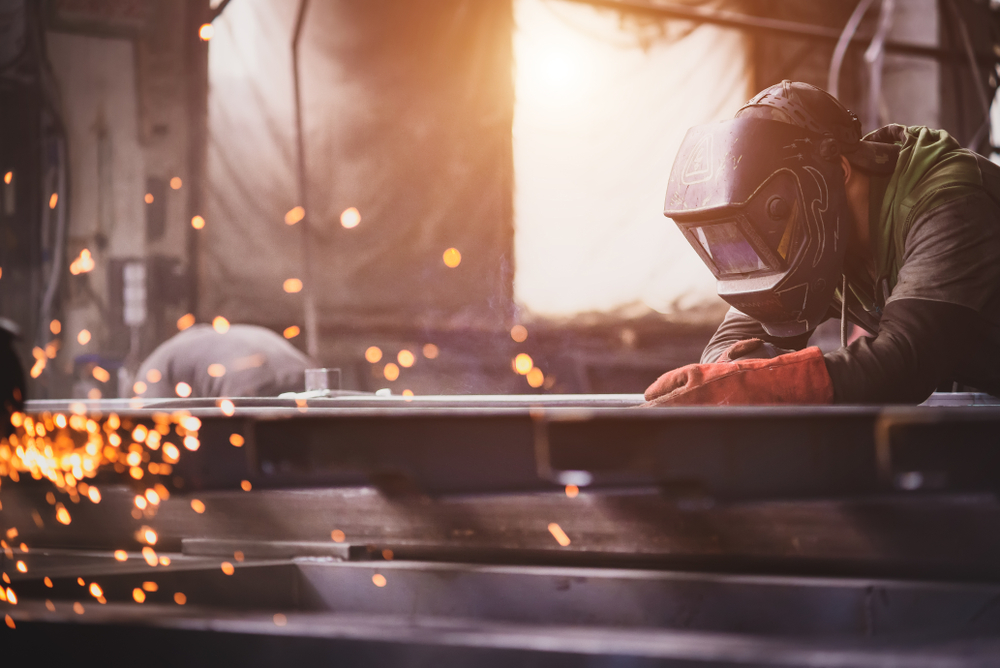
Furniss and White – The Complete Engineered Solution (The Following is a Promoted Article) The ability to produce accurate castings is one much-revered across sectors, providing businesses with the key advantages in speed and quality needed to remain competitive. With precisely that capability, Furniss and White, one of the UKâs leading castings specialists, in fact, does a whole lot more and, having innovated the process â as well as developing fabrication services alongside â the company has quickly become the first and last step in engineering excellence. From humble beginnings in 1980, Furniss and White has since enjoyed phenomenal growth in the metal castings and fabrication industry, and the company is showing no sign of slowing down. Now specialising in highly advanced and accurate castings as well as hosting fabrication and assembly services, Furniss and White effectively offers the complete engineering solution, acting as a one-stop-shop for its clients in the oil and gas, defence and marine sectors. A key strategy responsible for Furniss and Whiteâs long-standing reputation and success in the foundry industry, has been its commitment to investment; the company has, most recently, carried out a major improvement of its facilities. As part of its five-year investment programme, the company has just renewed its heat treatment facilities to the tune of some £1m. The state-of-the-art, new furnace is capable of heat-treating up to 5t of material at a time and utilises a 51,000l jet-chilling process post-heat. The facilities not only meet, but exceed, current specifications on quality and health and safety, achieving a transfer time of just 30 seconds. Recognising the sheer pace at which both the castings and fabrication sectors innovate, as well as the increasingly demanding requirements of clients, Furniss and White has also taken time to develop strands of its own â inaugurating a new division dedicated solely to research and development. With help from tax consultancy firm, Howard Lynch, the company has capitalised on government support for R&D investment and has been able to form a new strand dedicated to innovation. The department, which comprises a team of qualified technicians and engineers, is headed up by acting-consultant, Professor John Campbell OBE, a man widely-regarded as one of the worldâs leading experts in the castings industry. As a result of his appointment some five years ago, Furniss and White has undergone waves of major change â not least in the adoption of state-of-the-art CNC technology. Sam Scholes, Development Manager at Furniss and White details further: Our R&D team stressed that, if we were to continue to keep pace with the market as well as open new doors for the future, we needed to improve the precision of our castings. From a strong partnership with Simpsons Patterns, weâre now able to offer the high quality castings that clients need. From the customerâs original 3D model, Simpsons Patterns is able to create a 3D CNC-cut pattern from which we can then produce a highly accurate mould to cast from. Using CNC tooling effectively guarantees that the pattern is an exact replica of the initial drawing therefore maximising client satisfaction. The ability to work exactly to a clientâs brief is, of course, of significant advantage â providing the clientâs model is fine-tuned to a degree wherein itâs not only cast-able but also not susceptible to failure later down the line. In that respect, Furniss and White need not worry. Having invested in the latest 3D visualisation software, Solid Cast, the firm is able to generate an accurate 3D interactive graphic which provides an insight into how molten metal flows into the mould. The model is solidified on-screen as it would be during the casting process. With the simulation technology (provided by AF Software), the company is able to identify potential flaws or material discrepancies at an early stage â something Scholes is keen to stress provides benefits to both the company and its clients. Finding a flaw in a product as a result of a defective mould is a real headache for customers, asserts Scholes. They have to take the product off the machine, send it back to the castings service, get the design re-drafted (if theyâre able to) and then re-commence production. Every stage represents major financial outlay and a significant amount of time for both the client and the caster, and so getting the job right first time is absolutely critical. With Solid Cast, thatâs exactly what weâre able to do. With the employment of AFâs Softwareâs technology, Furniss and White has significantly improved its first time radiography pass rate (comparable to KPIs), achieving a remarkable NDT pass rate of 92%. Previously, one of companyâs engineers would draft a 2D drawing and conduct various calculations so as to predict the path and behaviour of the molten metal as it is poured into the mould. Guesswork has since been replaced by point blank accuracy, and the company can deliver the every time excellence required by clients. Much of its new capabilities have to be, in part, attributed to the new partnerships it has fostered with suppliers without which, Scholes admits, There would be no Furniss and White. Priding itself on maintaining a largely local supply chain, the company is rewarded with both faster lead times as well as the opportunity to widen and enhance its services. In addition to its positive relationship with Simpsons Patterns, for instance, Furniss and White is also able to call upon nearby Insight NDT to support Non-Destructive Testing (NDT) and radiography services. Scholes describes the testing specialist as a solid partner, adding: The team at Insight have been truly invaluable. NDT plays a major role in the fabrication sector and itâs imperative that we continue to provide that service to customers. Theyâre able to turnaround a dayâs worth of casting in little more than a week, assigning casts a pass or fail mark. More than that, theyâve grown in line with what need: investing in larger vehicles to convey our larger castings. In recent years, businesses have become so much more