Starliner Mission Patches Designs Have Been Released
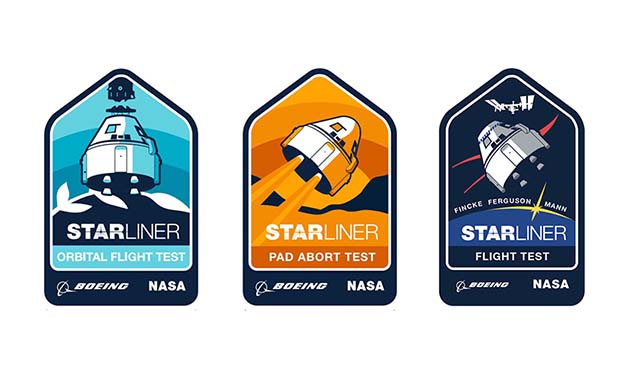
Mission patches are more than collectibles – they are a long-standing tradition that tell the incredible story of human spaceflight. For decades, astronauts of every historic endeavor have been personally involved in designing these emblems, and the three new CST-100 Starliner flight test patches are no exception. “The Starliner program represents many firsts for Boeing, so we wanted to make sure a mix of employees who have designed, built and tested the spacecraft could influence their look and feel,” said Boeing astronaut Chris Ferguson. Ferguson championed the development of the Orbital Flight Test, Pad Abort Test and Crew Flight Test patches. The design phase was a team sport with Starliner employees, Boeing Creative Services, and NASA astronauts Nicole Mann, Mike Fincke and Eric Boe. “Their shapes, colors and symbols were chosen to highlight each mission’s significance,” Ferguson said. As an example, each of the three patches are five-sided, representing the spacecraft’s five phases of development, as well as the five available seats on service missions to the International Space Station. Be on the lookout for them to show up, along with other space merchandise, on the Boeing Store Space Shop. Orbital Flight Test patch: Over the past half-century, Boeing has played an integral role in every U.S. human spaceflight program. The olive branch on this patch nods to that history as a reference to the Apollo 11 moon landing patch, and to NASA as the agency welcomes Boeing to the era of commercial human spaceflight services. With shades of blue representing our methodical steps to reach low Earth orbit, this patch was ultimately inspired by the image of Starliner first docking to the Boeing-built International Docking Adaptor attached to the International Space Station. Pad Abort Test patch: Drawing inspiration from the scenic New Mexico desert where the test will take place, the varying colors of orange represent the steps we took to qualify the Starliner’s abort system, beginning at the component level and graduating to an integrated test level. The patch depicts the spacecraft’s four Launch Abort Engines, which would get the Starliner crew module and its passengers away from a dangerous situation while on the launch pad or through ascent. The sun represents the rise of a new age in human spaceflight that puts safety of crew members at the forefront of all we do. Crew Flight Test patch: Boeing astronaut Chris Ferguson, and NASA astronauts Nicole Mann, Mike Fincke and Eric Boe, worked with Starliner employees from across the country to develop a patch that pays homage to the national importance of the Starliner program. The red vector coming off the sides of the spacecraft represents NASA’s insignia, known as the “meatball,” as a symbol of our collaboration with America’s space agency. The dark blue background represents low Earth orbit and the iconic Boeing blue hue. A yellow sunburst following the curvature of the Earth symbolizes the dawn of a new era in human spaceflight with the first orbital flight of a crewed commercial spacecraft. The full depiction of the International Space Station portrays the Starliner’s first destination in space. Manufacturing & Engineering Magazine | The Home of Manufacturing Industry News
Building Structure for Aerospace Manufacturer Has Been Announced
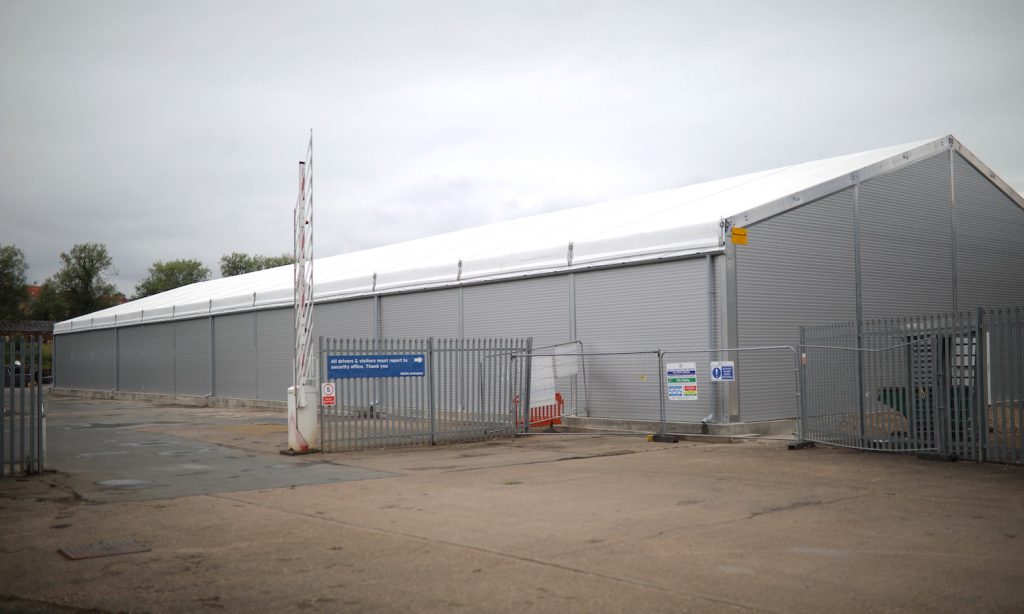
Building Structure for Aerospace Manufacturer Has Been Announced : The building structure of aerospace manufacturer Mettis’ new factory in Redditch, Worcestershire, has been announced. The plans were initially reported back in April, with the next phase of the project involving the installation of six new machines which will be fully automated to run 24 hours a day. The company plans to start trials for the fully automated production of aerospace components later in the year, and aims to enter production in early 2020. The factory will enable the expansion of the company’s machining business, with components being produced using the onsite forges and machines in the factory. This will lead to a reduction in the processing and transporting time for customers. Mettis has built the factory in response to a number of multi-million-pound aerospace contracts that were awarded to the company. The advanced levels of automation will enable Mettis to further reduce lead times for customers. The new factory will be the first new facility of this scale Mettis has built in many years and demonstrates its commitment to manufacturing in the UK, creating jobs and investing in its future. Manufacturing & Engineering Magazine | The Home of Manufacturing Industry News Manufacturing & Engineering Magazine (MEM), is a the leading UK based monthly print & digital publication focused on promoting innovation in manufacturing and engineering available here in the UK. We cover : SUSTAINABILITY (Waste & Water Management, Recycling, Energy); INMOTION (Rail, Marine, Aerospace, Automotive, Defence); INFRASTRUCTURE (Oil & Gas, Nuclear, Construction); Healthcare (Medical), TECHNOLOGY(Printed, Connected, Software, Composite); MANUFACTURING (Chemical, Metals, Plastics, Electronics, Electrical); CONSUMER GOODS(Furniture, Electrical, Electronics, Food) to name but a few. We have over 50,000 views of each issue of MEM on average in 2022 and go to print monthly and also publish in our newsletter, (each issue is available free for 12 months digitally). Our focus is aligned across the next 12 months with our global media partnerships around Trade Events and also contains original content.
CRP Technology Welcomes the Cutting-Edge Windform FR1
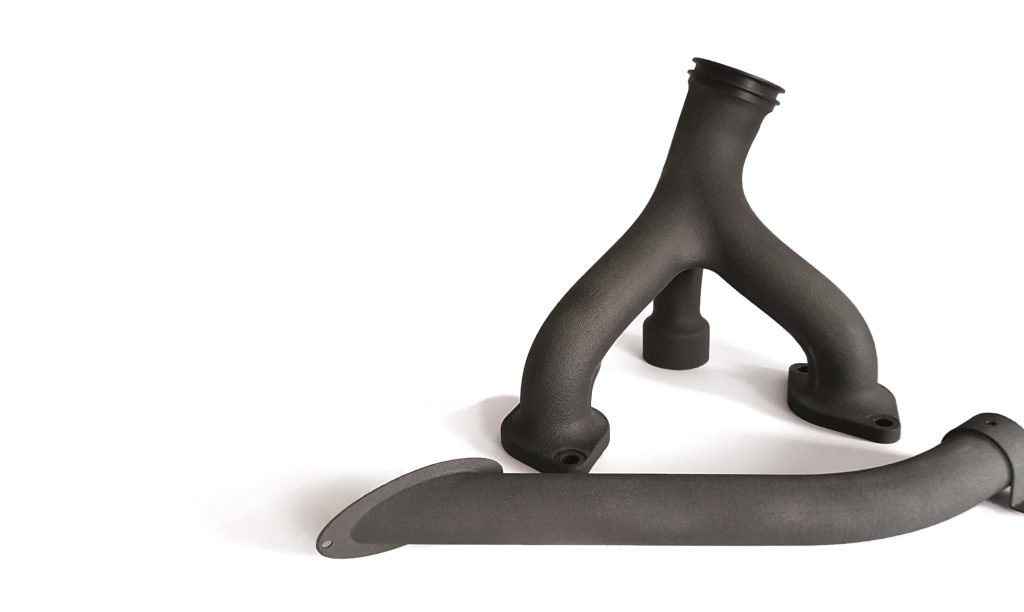
CRP Technology Welcomes the Cutting-Edge Windform FR1 Since mid-90’, CRP Technology has been changing the rules of additive manufacturing, smashing records and setting models nowadays that apply to the 3D printing technology with polyamide materials. A clear sign of this continued performance is Windform® FR1 (FR stands for Flame Retardant), the new-born material from the Windform® TOP-LINE family of composite materials for Additive Manufacturing. It is intended to become a game-changing material in the field of 3D printing for its uniqueness: it is the first Flame Retardant (UL 94 V-0 rated) material for Additive Manufacturing which is carbon fiber reinforced. It is also passed successfully the FAR 25.853 12-second vertical and 15-second horizontal flammability tests as well as the 45° Bunsen burner test. “Only a few days from the launch of a new range of Windform materials, the P-LINE for HSS technology – commented Franco Cevolini, VP and CTO at CRP Technology – I’m very proud to launch a new revolutionary composite material from the Windform® TOP-LINE family of materials for Laser Sintering technology. Our aim is to constantly produce technological breakthroughs. With Windform® FR1 we can steer you toward the proper solution for your projects” Windform® FR1 is halogen free polyamide-based material, that combines superior mechanical properties with excellent stiffness and lightweight. Owing to its flame-retardant quality, this high-performance polyamide based composite material is suitable for Aircrafts and Aerospace applications (interior parts, cockpit, cabin components, air conditioning piping, air ducts, air outlet valves); Automotive and Transportation parts (vehicle interiors, housing and enclosure assemblies); Consumer goods and Electronics (lighting, appliances) and in general for any parts requiring flame retardant rating. Windform FR1 is ideal for high feature detail applications requiring FAR 25.853 fire retardant compliancy. Windform® FR1 is also suitable for the manufacturing of components with detailed surface resolution. “We will not stop here- added Franco Cevolini – we will continue our work on renewal and technological expansion in the field of Additive Manufacturing. Stay tuned!” Manufacturing & Engineering Magazine | The Home of Manufacturing Industry News
BAE Systems Calls for Nationwide Effort to Develop Skills for Industry 4.0
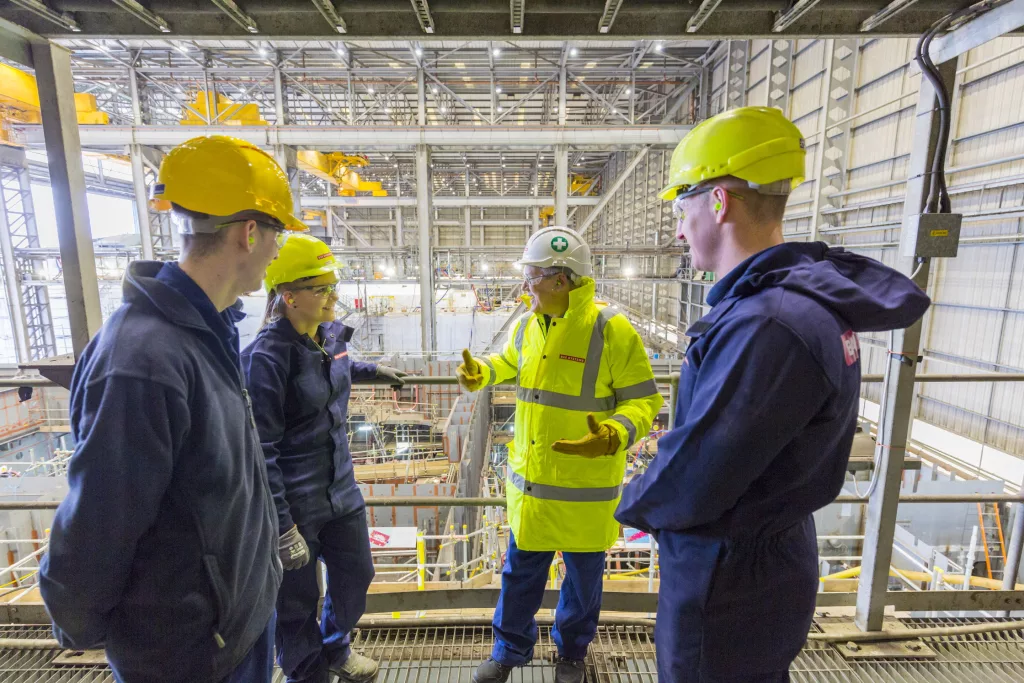
BAE Systems Calls for Nationwide Effort to Develop Skills for Industry 4.0 : BAE Systems has called today for a concerted and co-ordinated effort by industry, Government and the education sector to ensure the UK can fully benefit from the digital revolution and Industry 4.0. Nigel Whitehead, Chief Technology Officer at BAE Systems, stated that defence, aerospace, engineering and manufacturing sectors need to work together and prioritise investment in digital and ‘soft skills’, upskilling and retraining and supporting supply chains and SMEs, to respond to the expected levels of complexity in industrial and business systems and unprecedented demand from technologies such as artificial intelligence, for the Industry 4.0. Mr Whitehead also suggested that businesses in these sectors need to create a more diverse, inclusive and flexible workplace by reflecting different working preferences and lifestyles. To help address the UK’s shortage of engineers, he called for a nationwide programme of activity to improve the perception of science, technology, engineering and maths (STEM) subjects and careers and for the engineering industry to consider recruiting more people with highly applicable skills that traditionally are more associated with arts subjects, such as creativity and problem solving. In its whitepaper – ‘Future Skills for our UK Business’ – BAE Systems sets out six guiding principles for the development of skills in the UK in an environment of rapid technological change and fierce global competition: 1. Create a more diverse, inclusive and flexible workplace for the employees of tomorrow; the UK must attract and retain top class talent; 2. Commit to retraining and upskilling; it is vital for innovation and growth that employees continue to learn throughout their careers; 3. Prioritise investment in digital, soft and behavioural skills; to give the employees the broad range of technical and people skills needed to succeed in the modern workplace; 4. Continue to support suppliers and the SME community so that they can develop skills in the digitally-enabled workplace; successful and innovative partners help the UK economy thrive; 5. Continue to improve the perception of STEM subjects and careers; encouraging graduates and young people into a dynamic and rewarding industry; 6. Continue to champion vocational training; working with Government to ensure training is funded and prioritised. At a launch event hosted at the Company’s state-of-the-art Academy for Skills & Knowledge in Samlesbury, Lancashire, Nigel Whitehead, said: “I am personally really excited by the opportunities in today’s highly connected world and what the future will bring, but we cannot be complacent. By taking tangible action now and capitalising on the ambition of young people coupled with the UK’s traditions and advantages – education, strong legal frameworks, technical innovations and leadership – we can exploit the digital revolution and compete on the world stage.” Joining Mr Whitehead at the event in Samlesbury, Dr Hayaatun Sillem, Chief Executive of the Royal Academy of Engineering added: “Failure to successfully prepare for the impact of technological disruption means we will put at risk our ability to benefit from the opportunities created by digital transformation and other waves of technological change.” BAE Systems invests £90m annually in skills in the UK, providing world-class training facilities for its employees and education to ensure its current and future workforce are trained to the highest standards. At any given time, there are approximately 2,500 apprentices and graduates in training across its UK business. Manufacturing & Engineering Magazine | The Home of Manufacturing Industry News
New Partnership to Develop the Fastest Commercial Airline
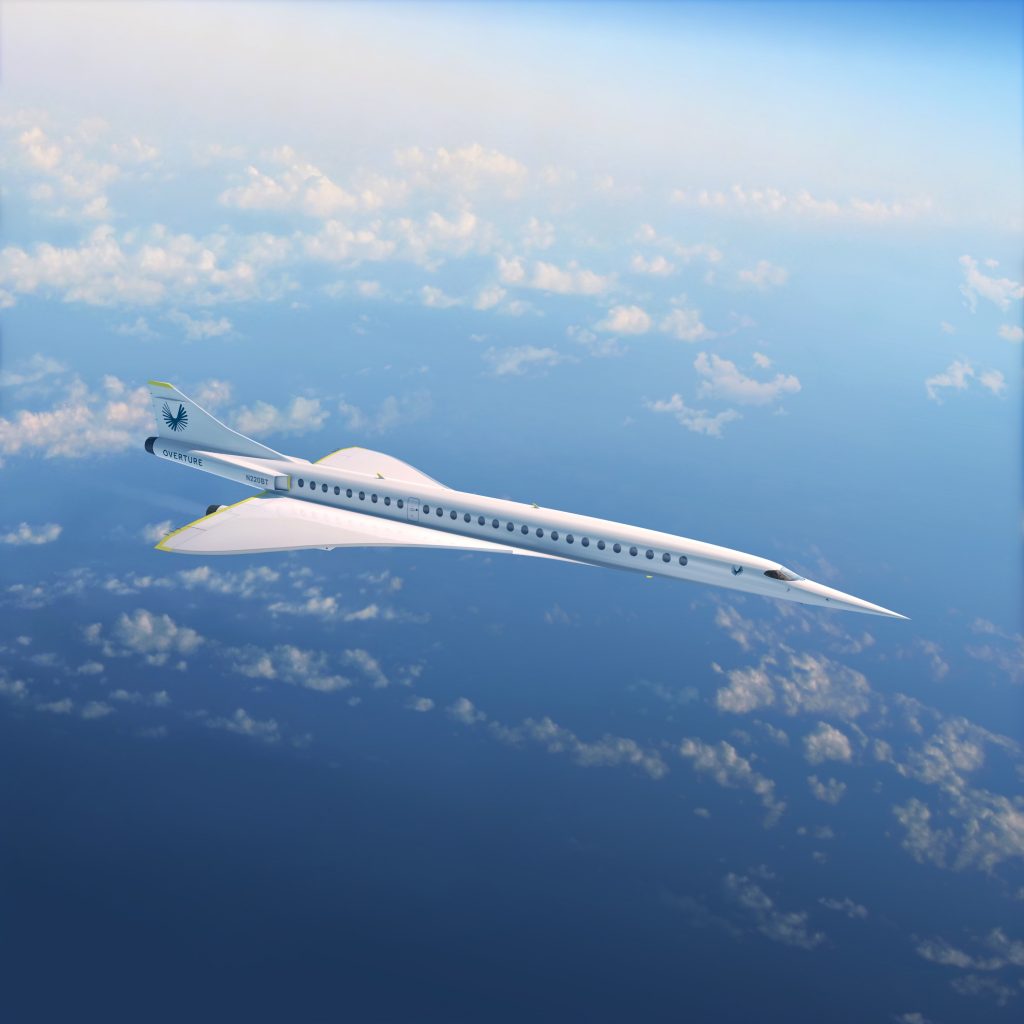
Dassault Systèmes has announced that Boom Supersonic is deploying the 3DEXPERIENCE platform in order to accelerate the design and development of Overture, its Mach-2.2 commercial airliner, with an aim to make supersonic travel mainstream and affordable. Boom Supersonic is using Dassault Systèmes’ “Reinvent the Sky” industry solution experience based on the 3DEXPERIENCE platform to support product development from concept through manufacturing and certification. By using this industry-leading solution, Boom Supersonic can cut development time of its first prototype in half and improve product quality by reducing program complexity, inefficiency, costs and resources, thus lowering the barriers to market entry. “Overture takes new advances in aerodynamics, materials, and propulsion and uses them to revolutionize long-haul commercial airline travel. We need powerful design tools to deliver our vision of a supersonic future, and that is exactly what Dassault Systèmes provides,” said Joshua Krall, co-founder and VP, technology, Boom Supersonic. “As a startup, we aren’t constrained by legacy software systems and aim to keep IT costs low. We quickly and easily deployed Dassault Systèmes’ 3DEXPERIENCE platform and expect to scale up to hundreds of users as our project matures.” In response to increasing passenger travel and demand for new products and services, aerospace startups, new market entrants and small original equipment manufacturers (OEMs) are shaking up traditional aviation industry dynamics with new and emerging aircraft design concepts that aim to overcome technical challenges of the past. Tailored for product innovation by small OEMs and startups, “Reinvent the Sky” offers scalable access to digital design and simulation applications in a single, secure, and standards-based environment. Boom Supersonic’s engineers, program managers and chief test pilot can collaborate in real time to define requirements, access and reuse common processes and parts with full traceability. “Aerospace companies are working to deliver faster, lighter, more efficient aircraft without sacrificing passenger comfort,” said David Ziegler, Vice President, Aerospace & Defense Industry, Dassault Systèmes. “Smaller innovators need tools for their product development programs that offer them the infrastructure of more established companies yet allow them to stay nimble and incur minimal IT-related expenses. The 3DEXPERIENCE platform delivers this support. Boom Supersonic can create the next generation passenger experience with digital applications that have long been at the core of the industry’s major milestones.” Boom Supersonic is currently building XB-1, its two-seat demonstrator aircraft, to prove key technologies for supersonic flight. Once operational, the company’s flagship airliner, Overture, will become the fastest commercial airplane in history, flying Mach 2.2 from New York to London in 3.25 hours and from Tokyo to San Francisco in 5.5 hours.
Sofitec Expands Its Capabilities in Complex Sheet Metal
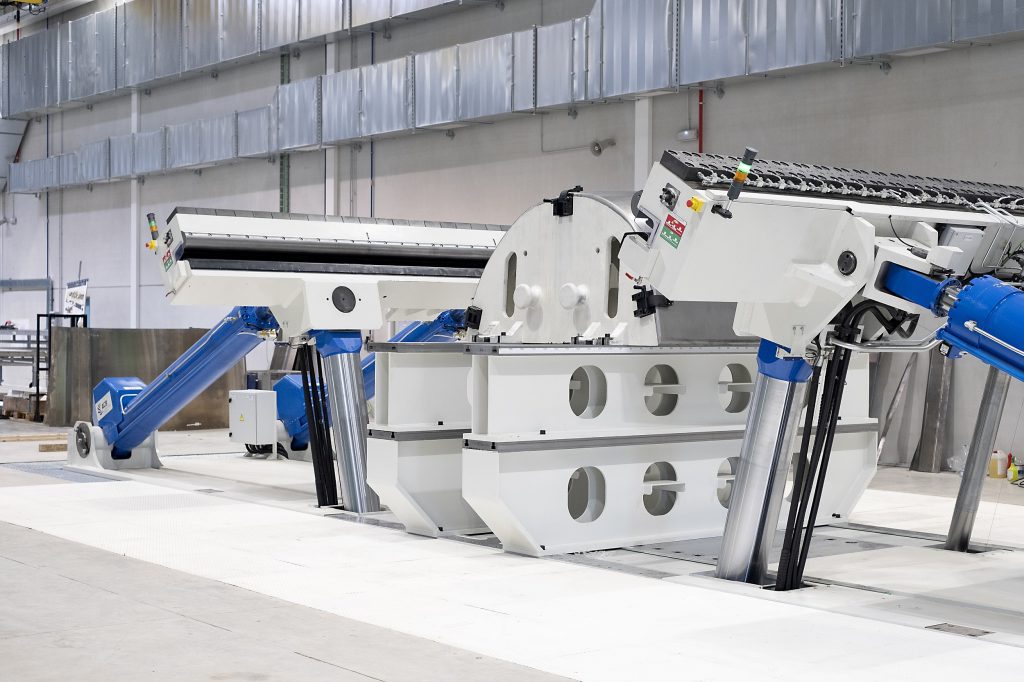
Sofitec, a company specialized in aerostructures manufacturing and assembly, is accomplishing the launch of a new area of complex sheet metal processes for the aeronautical industry. With an investment of 20 million euros, the company began last year the expansion of its facilities, as part of which it has recently acquired two new equipment that will increase its technological capabilities and diversify its products and processes catalogue. Concretely, Sofitec has incorporated into its technological fleet a stretch forming machine specially indicated for cold plastic deformation processes. This type of metalworking improves the properties of the treated material by exceeding its inherent elastic limit, making the final shape of the piece stronger (after even machining operations) and reducing the possibility of defects in its interior curvature. Also, the new equipment will allow the application of simple, complex curvatures and non-uniform geometries, thanks to its stretching force of up to 600 tons. The company has also acquired, as part of this technological expansion, a 5-axis trimming machine of high performance and precision, with which it improves its capacity for the machining of large dimension elements, thanks to its mobile bridge system and aerial guidance. It is expected that the new facilities under construction, annexed to the current ones, will be fully operational in the last quarter of 2019. With an area of 11,600 sqm -which will be added to the existing 38,000- will allow the company to increase its available capacity by 80%, in addition to raise its turnover. Along with the mentioned areas, the expansion also includes the launch of an automatic baths line for anodizing of metallic materials, cleaning, and penetrant dye inspection; and a robotic painting line. Manufacturing & Engineering Magazine | The Home of Manufacturing Industry News
Plans for the UK Space Sector Announced
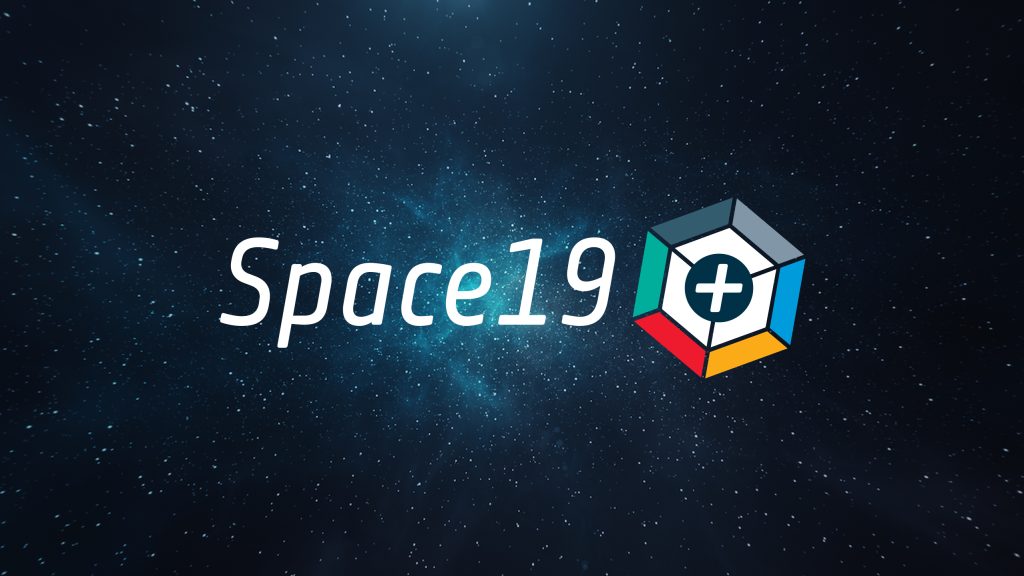
UK priorities for Space 19+ It takes place as the UK government prepares for Space19+, the European Space Agency’s (ESA) Ministerial level Council meeting, which will set out the ESA’s priorities and funding for its future work. The conference will be an opportunity to discuss the sector’s priorities, particularly in the area of how the ESA’s funding should be set to best support the UK sector. Included in the agenda are keynote addresses from: Chris Skidmore MP, Minister of State for Universities, Science, Research and Innovation, and Magali Vaissiere, Director, Telecommunications and Integrated Applications and Head, ECSAT, Harwell UK, European Space Agency. The National Space Programme and a Sector Deal for space The seminar also comes as industry and Government work towards a National Space Programme, with ambitions for launch in April 2020, as part of a Sector Deal. It also follows the Prosperity from Space strategy which sets out the sector and government priorities for earth observation, global connectivity, in-space robotics and access to space. Sessions will consider how best the Programme and a Sector Deal can support the continued growth of the sector and what more needs to be done to reduce the skills gap, support access to finance and utilise the regulatory framework to enable the sector to grow. Sector developments and the future of international collaboration The discussion takes place as work continues on the development of spaceports within the UK and the Government announces new funding to support the development of horizontal spaceflight in the UK and delegates will discuss what more the Government should do to support the funding, customer base and the delivery of infrastructure needed to enable the UK’s own launch capabilities. The agenda also discusses the UK’s future relationship with Europe and other key international clusters and options for both ensuring UK companies can expand into other markets and are able to attract international investment and talent post-Brexit – and with the development of the UK’s own Global Satellite System following its withdrawal from Galileo still on the table. The Defence Space Strategy We also expect discussion on the Defence Space Strategy which is expected before the seminar, and is due to set out the Government plans to tackle emerging space-based threats to commercial and military satellites. Delegates will discuss the feasibility of the plans set out in the strategy and the role that the MoD and other government and public bodies can play as an anchor customer to the industry to utilise government procurement as a leaver to support industry growth. Manufacturing & Engineering Magazine | The Home of Manufacturing Industry News
Manufacturer Wins Aircraft Seating Contract
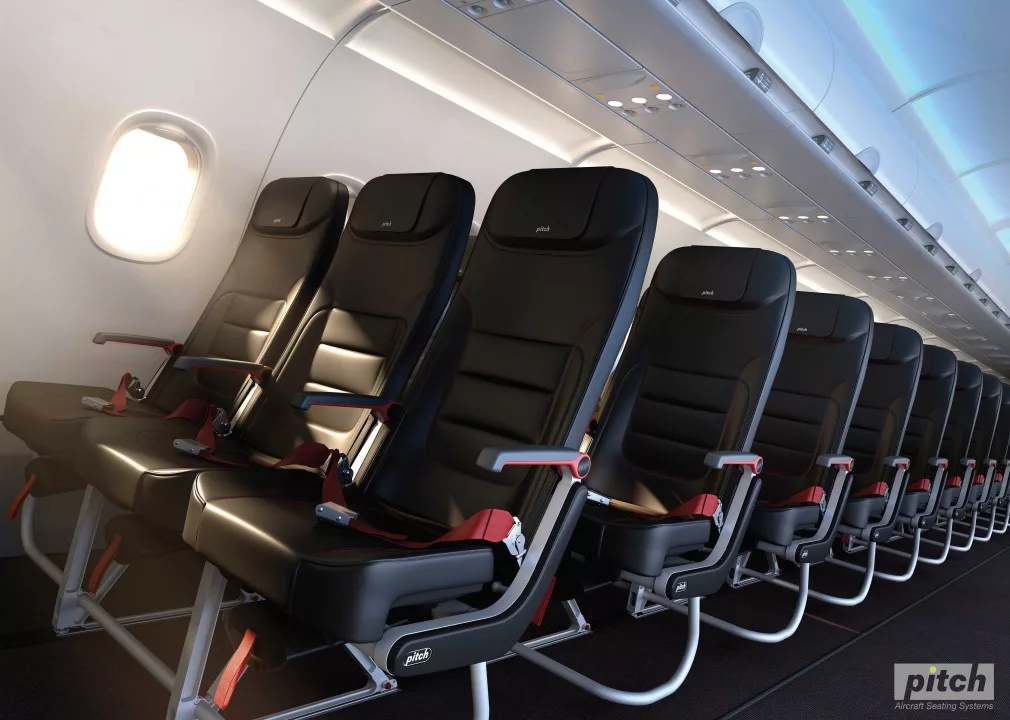
A contract has been agreed for Lisburn-based aerospace manufacturer Causeway Aero to become the manufacturer for aircraft seating systems supplier Pitch Aicraft Seating Systems. The announcement was made in advance of both companies attending the Aircraft Interiors Expo (AIX), taking place in Hamburg, Germany, starting with 2 April. “We have a great product in a buoyant market and our decision to appoint Causeway Aero as contract manufacturer, given their team, systems, certification and new manufacturing facility, puts us in a highly competitive position to support the increasing global demand for our products,” said Gary Doy, chief executive of PITCH. The contract win follows Causeway Aero’s acquisition of Belfast Aircraft Stress Engineers (BASE) in October of last year. “This is a day to celebrate the aerospace industry in Northern Ireland. We are delighted that Pitch has appointed Causeway Aero as their contract manufacturer and we will now be moving full steam ahead to engage with the Northern Ireland supply chain to ensure that we deliver for Pitch,” said Michael Rice, chief executive of Causeway Aero. “I’ve no doubt in my mind that one of the key decisions for Pitch was not only Causeway Aero’s ability to deliver quality and on time every time, but also the experience of Northern Ireland’s supply chain. We have some of the best engineering and manufacturing companies in Northern Ireland; suffice to say the proof is in their delivery, quality and performance year on year,” Michael added. Manufacturing & Engineering Magazine | The Home of Manufacturing Industry News
Boeing CEO Sends a Message to the Aviation Community
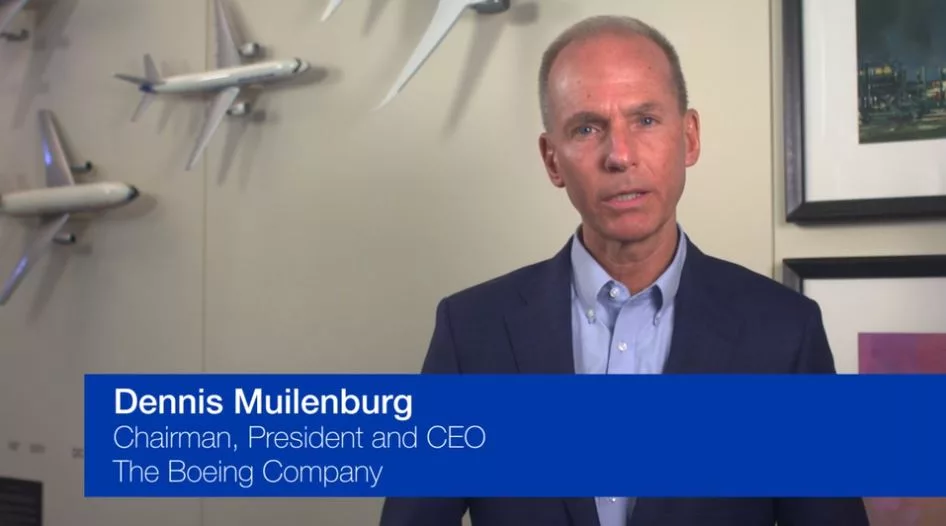
We know lives depend on the work we do, and our teams embrace that responsibility with a deep sense of commitment every day. Our purpose at Boeing is to bring family, friends and loved ones together with our commercial airplanes—safely. The tragic losses of Ethiopian Airlines Flight 302 and Lion Air Flight 610 affect us all, uniting people and nations in shared grief for all those in mourning. Our hearts are heavy, and we continue to extend our deepest sympathies to the loved ones of the passengers and crew on board. Safety is at the core of who we are at Boeing, and ensuring safe and reliable travel on our airplanes is an enduring value and our absolute commitment to everyone. This overarching focus on safety spans and binds together our entire global aerospace industry and communities. We’re united with our airline customers, international regulators and government authorities in our efforts to support the most recent investigation, understand the facts of what happened and help prevent future tragedies. Based on facts from the Lion Air Flight 610 accident and emerging data as it becomes available from the Ethiopian Airlines Flight 302 accident, we’re taking actions to fully ensure the safety of the 737 MAX. We also understand and regret the challenges for our customers and the flying public caused by the fleet’s grounding. Work is progressing thoroughly and rapidly to learn more about the Ethiopian Airlines accident and understand the information from the airplane’s cockpit voice and flight data recorders. Our team is on-site with investigators to support the investigation and provide technical expertise. The Ethiopia Accident Investigation Bureau will determine when and how it’s appropriate to release additional details. Boeing has been in the business of aviation safety for more than 100 years, and we’ll continue providing the best products, training and support to our global airline customers and pilots. This is an ongoing and relentless commitment to make safe airplanes even safer. Soon we’ll release a software update and related pilot training for the 737 MAX that will address concerns discovered in the aftermath of the Lion Air Flight 610 accident. We’ve been working in full cooperation with the U.S. Federal Aviation Administration, the Department of Transportation and the National Transportation Safety Board on all issues relating to both the Lion Air and the Ethiopian Airlines accidents since the Lion Air accident occurred in October last year. Our entire team is devoted to the quality and safety of the aircraft we design, produce and support. I’ve dedicated my entire career to Boeing, working shoulder to shoulder with our amazing people and customers for more than three decades, and I personally share their deep sense of commitment. Recently, I spent time with our team members at our 737 production facility in Renton, Wash., and once again saw firsthand the pride our people feel in their work and the pain we’re all experiencing in light of these tragedies. The importance of our work demands the utmost integrity and excellence—that’s what I see in our team, and we’ll never rest in pursuit of it. Our mission is to connect people and nations, protect freedom, explore our world and the vastness of space, and inspire the next generation of aerospace dreamers and doers—and we’ll fulfill that mission only by upholding and living our values. That’s what safety means to us. Together, we’ll keep working to earn and keep the trust people have placed in Boeing. Manufacturing & Engineering Magazine | The Home of Manufacturing Industry News
3D Printing Helps Build Wind Tunnel
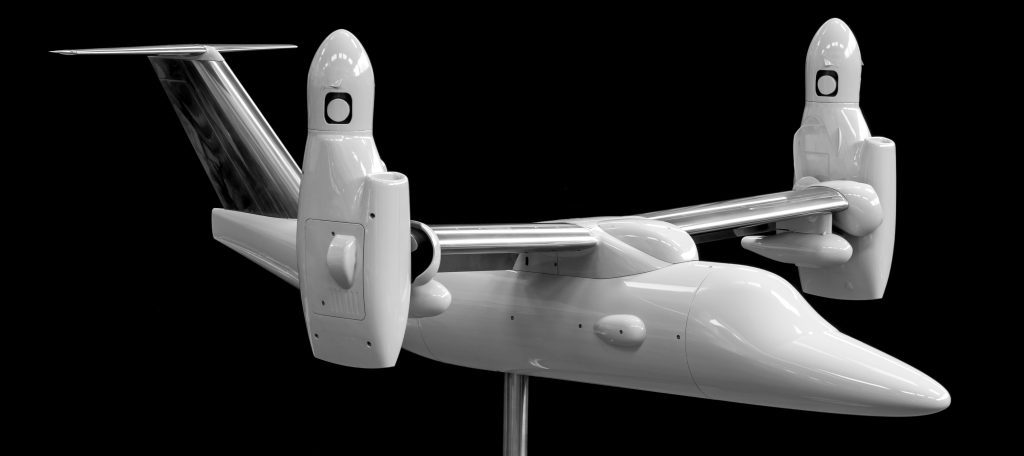
The new wind tunnel model of the LEONARDO tiltrotor AW609 manufactures developed by CRP Technology for Leonardo Helicopter Division (Leonardo HD, formerly known as Agusta Westland) is among the most interesting and significant applications in the aerospace sector. This project allowed CRP Technology, once again, to highlight the perfect union between advanced 3D printing technology (Selective Laser Sintering) and Windform® high-performance composite materials. Thanks to the Windform® materials, it was possible to complete and test the model in the wind tunnel within a very short time, with excellent results and with high-performing mechanical and aerodynamic properties. The project related to the manufacturing of some external parts (nose and cockpit, rear fuselage, nacelles, external fuel tanks, fairings) of the wind tunnel model (1:8.5 scale) for the prototype of the new LEONARDO HD tiltrotor AW609, made by Selective Laser Sintering technology and Windform® XT 2.0 Carbon-composite material, both supplied by CRP Technology. This model was designed, manufactured and assembled under the supervision of Leonardo Helicopter Division by Metaltech S.r.l. for a series of dedicated low speed wind tunnel tests. The tests were intended to cover a standard range of flight attitudes to be performed at Leonardo HD wind tunnel facility and at Politecnico of Milan for the high angles of flight envelope. During the different test sessions various external geometries have been changed and checked in order to understand all the aerodynamic phenomena. The external main components redesigned and manufactured include: fuselage and nose components, fairings, nacelles and spinner shapes, empennage, wings and flaperons. As part of a thorough review of the aircraft behavior, Leonardo Helicopter Division has performed a high speed test campaign at NASA Ames Unitary Plan 11 by 11 foot transonic wind tunnel.