Aerojet Rocketdyne Creates Rocket Engine with 3D Printer
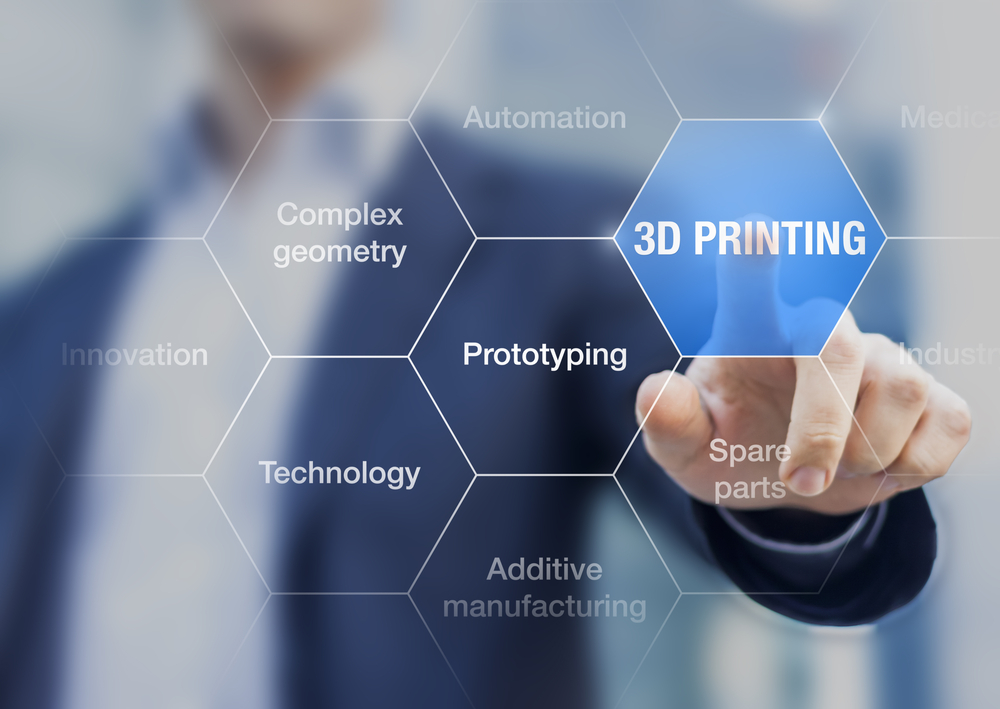
US-based rocket and missile propulsion manufacturer, Aerojet Rocketdyne has successfully conducted a number of what is called hot-fire tests of its newest rocket engine, the first to be produced by 3D printing technology. The RL 10 upper-stage rocket engine features a core main injector constructed by additive manufacturing technology and is hoped to pave the way for widespread use of the technology in the aerospace and defence sector. Formed in 2013 at the merger of Aerojet and Pratt and Whitney Rocketdyne, Aerojet Rocketdyne has fast become a leader in the aerospace and defence sector, building of the wealth of experience its compatriot businesses bring. The company manufactures and supplies propulsion and energetics to the space, missile defense and strategic systems, tactical systems and armaments areas, in support of domestic and international markets. Testing of its latest rocket engine was carried out alongside the RAMS programme, a research project conceived by the US Air Force and NASA’s Glenn Research Center. The research is geared toward showcasing the potential of additive manufacturing, particularly as it used to manufacture complex components fit for large rocket engines. Eileen Drake, CEO and President of Aerojet Rocketdyne said that the incorporation of additive manufacturing, i.e. 3D printing, was a key strategy in the companyâs growth and would help to deliver more affordable products while not compromising of the every time accuracy needed by the sector. Selective laser melting (SLM) was employed to create the core main injector. It involves using a high-powered laser beam to fuse powered metal together to produce complex, detailed parts. The state-of-the-art manufacturing process produces amongst the most durable components possible which are, of course, perfectly-suited to the extreme conditions to which rocket engines are privy. This is by no means Aerojet Rocketdyneâs first flurry in additive manufacturing and the company has already developed a range of products using the technology. The RL 10 however marks the companyâs most complex use of the technology and is good vision of what the future may like for both the US company and the sector more broadly.