Hexagon partners with additive manufacturing R&D centre
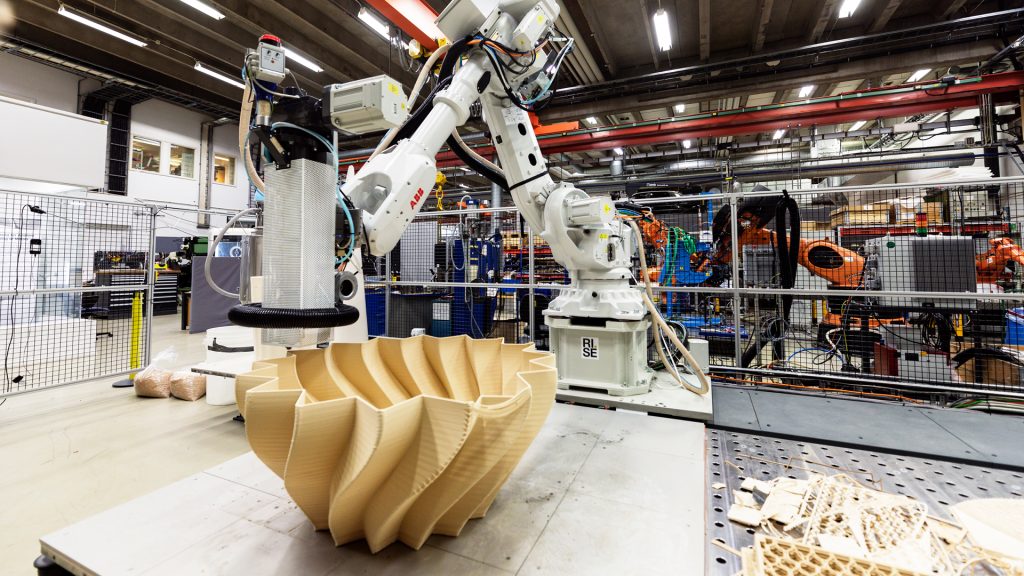
Hexagon has partnered with Research Institutes of Sweden (RISE), a national research and development (R&D) centre, to provide software that will help meet a Swedish initiative to advance the use of additive manufacturing (AM) technologies and accelerate the adoption of innovative and sustainable processes in European industry. Established by RISE to increase the accessibility of AM across industrial sectors, the new Application Center for Additive Manufacturing will be overseen by a consortium of industry leaders and provide manufacturers with access to a host of AM technologies, including software solutions from Hexagon for AM and quality control. Industrial applications of AM are demonstrating value and gaining acceptance, but there remain numerous manufacturing challenges that must be resolved before barriers to adoption can be drastically lowered. In addition to the relative nascency of AM, significant challenges include a lack of skilled labour, insufficient understanding of the behaviour of new materials, the limitations of hardware and software solutions, and the absence of consistent AM process standards. The new Application Center for Additive Manufacturing provides an independent and risk-free environment where manufacturers can “test before they invest” with the centre’s state-of-the-art facilities. Manufacturers such as Volvo, Siemens Energy, and Ericsson will use the centre to evaluate and validate entire AM ecosystems through collaboration with researchers, scientists, industry experts, and partners. Members of the centre will gain access to a variety of world-leading industrial metal AM and post-processing capabilities: Two powder-bed fusion systems from SLM Solutions a twin-laser SLM 280 2.0 and an SLM 125 HL A directed energy deposition (DED) system from AddUp — a Modulo 400 A metal binder jetting (MBJ) system from Digital Metal, a Markforged company A hot isostatic press (HIP) from Quintus Technologies A H3000 post-processing and finishing system from RENA The centre will also support the exploration of 3D printing with polymers and ceramics, providing several on-site fused deposition modelling (FDM), stereolithography (SLA), and selective laser sintering (SLS) systems, providing members a test bed for most AM and post-processing technologies. Using the full breadth of Hexagon’s software portfolio, manufacturers will be able to explore the possibilities that AM offers for industrial applications, orchestrate high-quality manufacturing from concept to product, and build their 3D printing capabilities. This includes design for AM (DfAM), process planning and optimisation for metal AM processes, including the emerging high-volume technologies systems on-site and hybrid manufacturing. Members will also be able to use polymer and composite-based methods more effectively by refining both the part design and process in digital reality before any material is used. Dr. Seyed B. Hosseini, director of the Application Center for Additive Manufacturing, said: “The Application Center for Additive Manufacturing is a unique co-creation platform where industrial partners along the entire ecosystem will work together with the target of increasing the utilisation of additive manufacturing across various sectors. Hexagon’s participation is a milestone for us, as we massively strengthen our competence in design and process simulation for additive manufacturing. “Being able to work closely and at an early stage of projects with the Hexagon team will bring the crucial ability to reduce the number of iterations in the entire value chain, and I’m confident that we will also offer valuable input back on how Hexagon’s software is being adopted by the industry and together drive forward even better solutions.” Mathieu Pérennou, additive manufacturing solutions director at Hexagon’s Manufacturing Intelligence division, said: “This collaboration offers a completely unique opportunity for companies to explore and test product development at the new centre, demonstrating the possibilities additive manufacturing holds for all industries. It’s a win for the entire industry, with the partnership combining our years of expertise in driving 3D printing innovation with access to the most cutting-edge tools and R&D teams. Our partnership with RISE will allow companies to explore the capabilities of our software, accelerate its improvement, and spur on Industry 4.0 with the digitalisation of additive manufacturing workflows.” The centre will also act as a catapult for small and medium enterprises, serving Sweden’s automotive, telecom, maritime, energy, and heavy industries. Catalytic collaboration between manufacturers and providers of materials, machinery, and software is expected to help validate and advance new technologies that resolve problems and address challenges from powder, to print, to parts. Manufacturing & Engineering Magazine | The Home of Manufacturing Industry News
Land Rover Engineers Developing 3D-Printed Glove
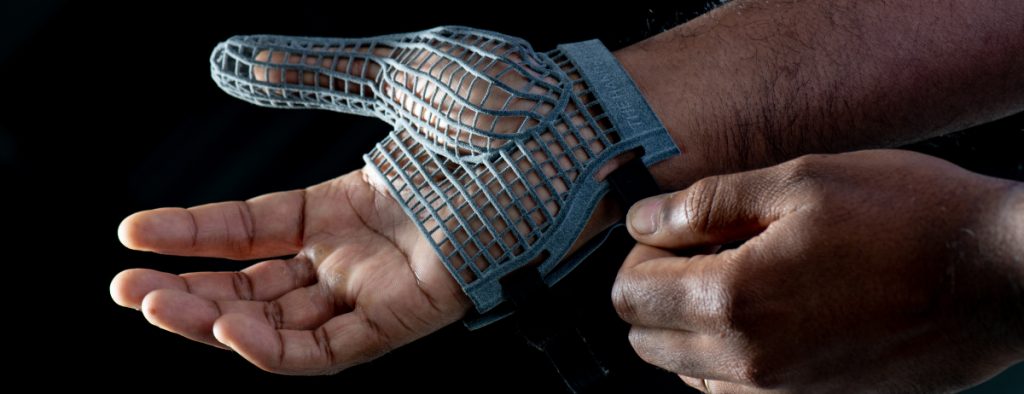
Land Rover Engineers Developing 3D-Printed Glove : Engineers from Jaguar Land Rover are working on a lightweight 3D-printed glove that could help better protect employees from the threat of a musculoskeletal disorder. The glove is designed for people working on the production line, such as those required to fit clips or fasteners into the chassis during assembly of JLR’s luxury vehicles. “The health and wellbeing of our workforce remains our priority across all factories and facilities. Technologies like the 3D-printed glove allow us to use the world-leading expertise and equipment we have in-house to protect the hands of our makers, developing equipment that will make Jaguar Land Rover a great place to work, now and in the future,” said additive manufacturing strategic engineer Chris Noble. Engineers at JLR’s Gaydon site, which is home to one of the largest 3D printing facilities in the UK, are using the company’s advanced manufacturing expertise to design and 3D print a lattice-style structure which would provide support to reduce muscle fatigue, but also be flexible and comfortable enough to wear during an eight-hour shift. In the short term the gloves will support workers across JLR’s facilities, helping to protect against musculoskeletal disorders. Manufacturing & Engineering Magazine | The Home of Manufacturing Industry News Manufacturing & Engineering Magazine (MEM), is a the leading UK based monthly print & digital publication focused on promoting innovation in manufacturing and engineering available here in the UK. We cover : SUSTAINABILITY (Waste & Water Management, Recycling, Energy); INMOTION (Rail, Marine, Aerospace, Automotive, Defence); INFRASTRUCTURE (Oil & Gas, Nuclear, Construction); Healthcare (Medical), TECHNOLOGY(Printed, Connected, Software, Composite); MANUFACTURING (Chemical, Metals, Plastics, Electronics, Electrical); CONSUMER GOODS(Furniture, Electrical, Electronics, Food) to name but a few. We have over 50,000 views of each issue of MEM on average in 2022 and go to print monthly and also publish in our newsletter, (each issue is available free for 12 months digitally). Our focus is aligned across the next 12 months with our global media partnerships around Trade Events and also contains original content.
Renishaw Supports INEOS TEAM UK in America’s Cup bid
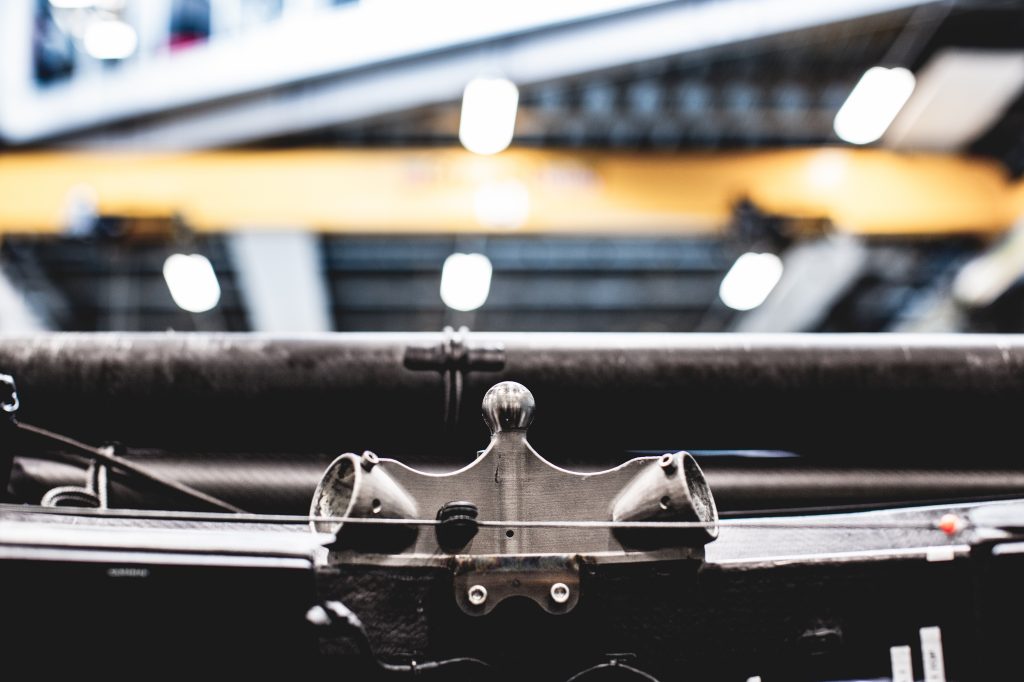
Global engineering company Renishaw is supporting Sir Ben Ainslie and INEOS TEAM UK in their bid to bring the America’s Cup home to Britain. As the team’s official precision measurement and additive manufacturing (AM) partner, Renishaw will contribute its engineering expertise to aid and fast track the build process as they bid to win the 36th America’s Cup in 2021. Renishaw is a world-leading engineering business with core expertise in precision measurement and position encoding. The company is also the only UK manufacturer of metal additive manufacturing machines, which it produces at its plant in Miskin, South Wales. The America’s Cup is the oldest international trophy in world sport and one that Britain has never won. First won by America in 1851, the competition was turned into a challenge trophy, open to sailing clubs from around the world. INEOS TEAM UK was formed to challenge for the America’s Cup in 2021, with petrochemical and manufacturing company INEOS making the biggest ever investment in the competition. British sailing legend and INEOS TEAM UK Principal, Sir Ben Ainslie, will skipper the yacht. The AC75 boat will be a 75-foot foiling mono-hull built and equipped with some of the best of British technology. To aid the team in building the technologically advanced boat, Renishaw is supplying its products and expertise in the fields of metal additive manufacturing, position encoders, manufacturing process control and Raman spectroscopy. This will include contributing to the design optimisation and manufacture of 3D printed metal parts, for example structural components; digital position feedback to improve the boat’s performance, including monitoring control surfaces; and material analysis. “Renishaw is proud to again contribute our expertise to the British America’s Cup challenge, having supported Sir Ben’s team for the 2017 challenge in Bermuda,” explained Chris Pockett, Renishaw’s Head of Communications. “It means a great deal to us that our past contributions have been recognised and that we will be a key partner for INEOS TEAM UK, providing a range of innovative solutions and becoming an integral part of its engineering team.” “Leading manufacturing technologies are crucial to the performance of the boat,” added Pockett. “From giving real-time position feedback during racing, to the use of metal additive manufacturing for lightweight, highly complex components, we are very excited about the contribution that we can make to the performance of the boat.” Sir Ben Ainslie, Team Principal and Skipper of INEOS TEAM UK, said, “We’re really excited to be working with Renishaw. They’ve been a fantastic partner to us and we’re really looking forward to the challenge to bring the Cup home in 2021 with their support.” “We chose to work with Renishaw because they have such a breadth of world-class engineering and scientific design knowledge,” added Mark Chisnell, Technology Coordinator at INEOS TEAM UK. “They are a fantastically resourced company with great facilities and people.”
CRP Technology Welcomes the Cutting-Edge Windform FR1
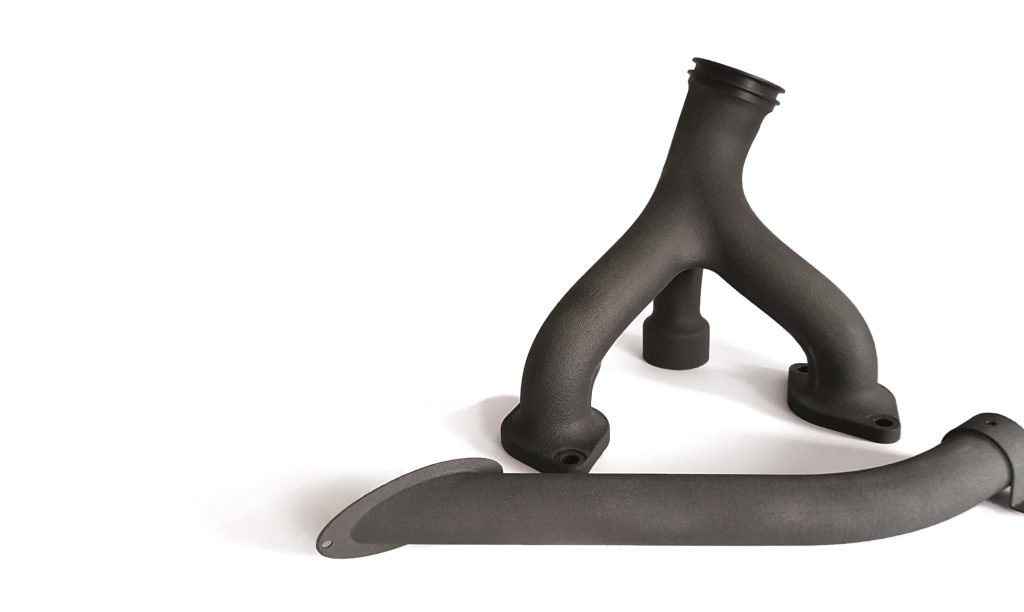
CRP Technology Welcomes the Cutting-Edge Windform FR1 Since mid-90’, CRP Technology has been changing the rules of additive manufacturing, smashing records and setting models nowadays that apply to the 3D printing technology with polyamide materials. A clear sign of this continued performance is Windform® FR1 (FR stands for Flame Retardant), the new-born material from the Windform® TOP-LINE family of composite materials for Additive Manufacturing. It is intended to become a game-changing material in the field of 3D printing for its uniqueness: it is the first Flame Retardant (UL 94 V-0 rated) material for Additive Manufacturing which is carbon fiber reinforced. It is also passed successfully the FAR 25.853 12-second vertical and 15-second horizontal flammability tests as well as the 45° Bunsen burner test. “Only a few days from the launch of a new range of Windform materials, the P-LINE for HSS technology – commented Franco Cevolini, VP and CTO at CRP Technology – I’m very proud to launch a new revolutionary composite material from the Windform® TOP-LINE family of materials for Laser Sintering technology. Our aim is to constantly produce technological breakthroughs. With Windform® FR1 we can steer you toward the proper solution for your projects” Windform® FR1 is halogen free polyamide-based material, that combines superior mechanical properties with excellent stiffness and lightweight. Owing to its flame-retardant quality, this high-performance polyamide based composite material is suitable for Aircrafts and Aerospace applications (interior parts, cockpit, cabin components, air conditioning piping, air ducts, air outlet valves); Automotive and Transportation parts (vehicle interiors, housing and enclosure assemblies); Consumer goods and Electronics (lighting, appliances) and in general for any parts requiring flame retardant rating. Windform FR1 is ideal for high feature detail applications requiring FAR 25.853 fire retardant compliancy. Windform® FR1 is also suitable for the manufacturing of components with detailed surface resolution. “We will not stop here- added Franco Cevolini – we will continue our work on renewal and technological expansion in the field of Additive Manufacturing. Stay tuned!” Manufacturing & Engineering Magazine | The Home of Manufacturing Industry News
Productivity Without Compromise at EMO Hannover 2019
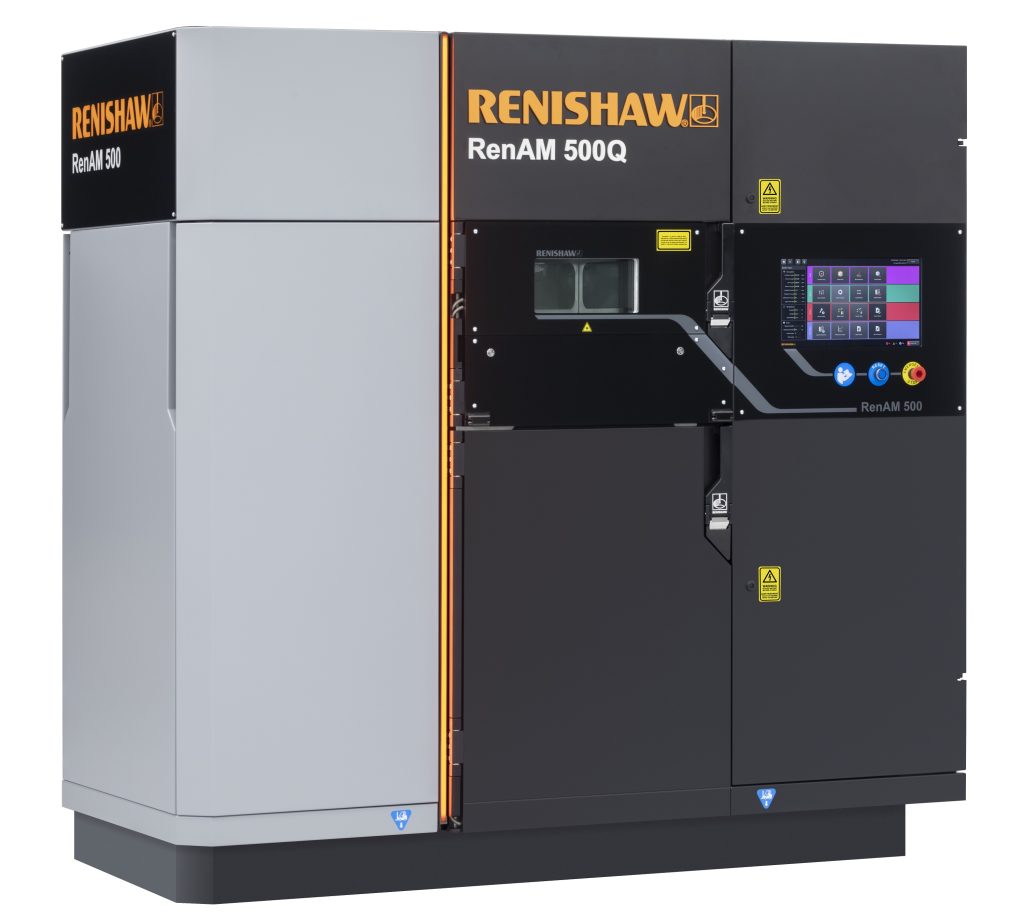
From September 16th to 21st September 2019, global engineering technologies company Renishaw will showcase its productivity through its leading additive manufacturing (AM) hardware and software at EMO Hannover 2019, in Germany. In hall 9, on a dedicated AM stand, Renishaw will demonstrate its range of products for high-quality, productive AM technologies including its latest system; the four-laser RenAM 500Q. Featuring four 500 W lasers, the compact machine greatly improves productivity in the most commonly used platform size whilst increasing the quality of the components being built. The RenAM 500Q speeds up the manufacturing process by up to four times, broadening the market appeal of metal AM into applications that were previously uneconomic, driving the technology into new industries. By positioning the machine competitively, Renishaw has ensured that customers benefit from reduced cost per part, without compromising on the precision or quality of a standard single-laser system. A critical technology at the heart of the RenAM 500Q is the optical system and control software. Laser beams enter the system via four channels, where they are dynamically focussed and directed into a single, thermally controlled galvanometer (‘galvo’) mounting. The galvo mounting houses four pairs of digitally controlled guided mirrors, which guide the lasers to cover the entire working area of the powder bed. “Renishaw’s additive manufacturing machines and optical systems are designed, engineered and manufactured in-house, giving us exceptional control over system performance,” explained Robin Weston, Marketing Manager at Renishaw’s Additive Manufacturing Products Division. “Using an innovative design for the optical system and by incorporating digital controls and dynamic focussing, all four lasers can address the powder bed simultaneously – improving the speed, productivity and capability of the machine.” “Additive manufacturing is a key enabler of the optical system,” continued Weston. “AM is used to build the galvanometer mounting and it allows tighter packaging of mirrors and the incorporation of internal conformal cooling channels to maintain precise thermal stability.” Renishaw is an innovator and leader in creating stable process environments, so is well placed to manage the additional process emissions caused by multiple lasers. An inert gas recirculation system, including a cyclone pre-filter and gas intercooler, preserve filter life and provide consistent clean processing conditions throughout the duration of the build. The new system builds on the safety and usability features of the single-laser RenAM 500M, incorporating dual SafeChange™ filters with automated changeover to minimise manual intervention. Additional studies have shown that powder condition is maintained for maximum reuse, further reducing part costs. Companies are already experiencing the benefits of the RenAM 500Q. Renishaw recently initiated a collaboration with Sandvik Additive Manufacturing to supply the company with the high productivity multi-laser system. This installation will complement Sandvik’s existing technologies and substantially increase the company’s printing capacity, strengthening its position in the growing AM market. The two companies also intend to collaborate in areas such as materials development, AM process technologies and post-processing. Renishaw is also contributing its AM expertise to help a variety of businesses develop new products. For example, Mountain bike brand, Atherton Bikes is working with Renishaw to additively manufacture titanium lugs for the company’s bike frames. By using the RenAM 500Q, the company can increase production rates, quickly developing and customising parts to the requirements of the rider. Whereas traditionally a lot of tooling is required, additive manufacturing is an entirely digital process, meaning that the lugs can be modified in CAD and reproduced efficiently and to a high standard. As more companies adopt additive manufacturing technology, Renishaw has launched its AM Guide to offer manufacturers support and advice. The Guide is a dedicated area of the company’s website that educates and informs customers as well as the wider engineering community. The Guide contains videos, case studies, feature articles, industry news and opinion pieces to highlight to readers the variety of opportunities available when using additive manufacturing technologies. The AM Guide also contains a collection of technical articles written by the company’s industry experts, including popular LinkedIn blogger, Marc Saunders and Martin McMahon, an expert in AM applications.
CRP USA Attended AMUG 2019 as Speaker
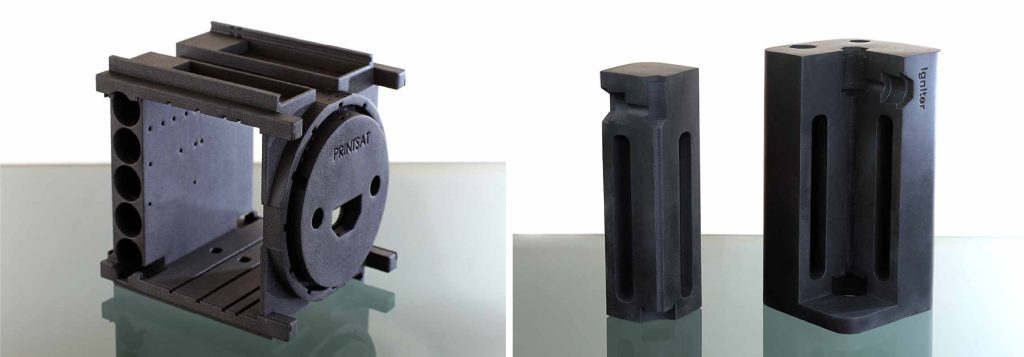
CRP USA will be attending Additive Manufacturing Users Group (AMUG) as speaker. The 31st edition of AMUG will be held from 31st March to 4th April, 2019, at the Hilton Chicago, in Chicago, Illinois. At the 2019 edition Stewart Davis will be presenting the paper: “Construction of CubeSatellite used to dispense TubeSatellites using Additive Manufacturing”. The speech is set for 1st April, 2PM, at the International Ballroom, Hilton Chicago, in the track: “Aerospace/Transportation”. Stewart Davis will explain how the use of Windform composite materials, originally developed for the Motorsports industry by CRP Technology, is now finding many uses in space exploration. Mr. Davis will also demonstrate the effectiveness of additive manufacturing and the use of Windform as a structural material for space applications. Hightlighted at AMUG will be the case study that follows the successful construction and launch of the TuPod. CRP USA works alongside key space industry leaders. Based in Mooresville, North Carolina, CRP USA employs a highly skilled staff that specializes in the manufacturing and creation of end-use parts and prototypes built from Windform high performance composite materials for LS technology. With new projects and new developing perspectives in the field of AM, CRP USA has been the technological partner of space applications such as the construction of a CubeSat in additive manufacturing, gathering the interest of the most important bodies involved in space engineering. Additive Manufacturing Users Group (AMUG) Conference brings together engineers, designers, managers, and educators from around the world to share expertise, best practices, challenges, and application developments in additive manufacturing. AMUG is a global community focused on accelerating the education and advancement of additive manufacturing and 3D Printing.