The headlines around electric vehicles (EVs) have been less than optimistic recently. While the news cycle is negative, the reality is that we must continue to push for the electrification of all transportation to align with global climate targets. So, what can automakers and OEMs do to support the electric shift? Here, Mark Barfield, engineering manager at power resistor manufacturer Cressall, shares his insight.
About 26 million EVs have been sold to date, according to the International Energy Agency. That includes plug-in hybrids, which have an internal combustion engine alongside a battery. But what appears to be an impressive figure is just a fraction of the total car stock of 1.3 billion. While sales have been on the increase, slow charging times and the need for comprehensive charging infrastructure remain barriers and recent negative press around the EV rollout could hamper EV update.
As we head into 2024, the most crucial piece of news surrounding the UK’s EV rollout relates to the Government’s U-turn on the ban on new petrol and diesel-powered vehicles, pushing back the deadline from 2030 to 2035.
Consumer attitudes
We all know that most people need to work to an imminent deadline in order to make a change. This goes for the shift to EVs too. Consumers now have an extra five years to consider how and when they’re going to go electric, and they’re likely to take advantage of that extra time.
According to The Society of Motor Manufacturers and Traders (SMMT), in September 2023, prior to the ban being announced, the battery EV market share grew for the 41st consecutive month with over 45,000 drivers making the switch.
But this growth is likely to stall. The Government’s U-turn will certainly raise concerns around EVs’ ability to replace ICE vehicles. Is the charging infrastructure up to scratch right now? Can EVs deliver the vehicle range required for all drivers? This in turn generates issues for manufacturers.
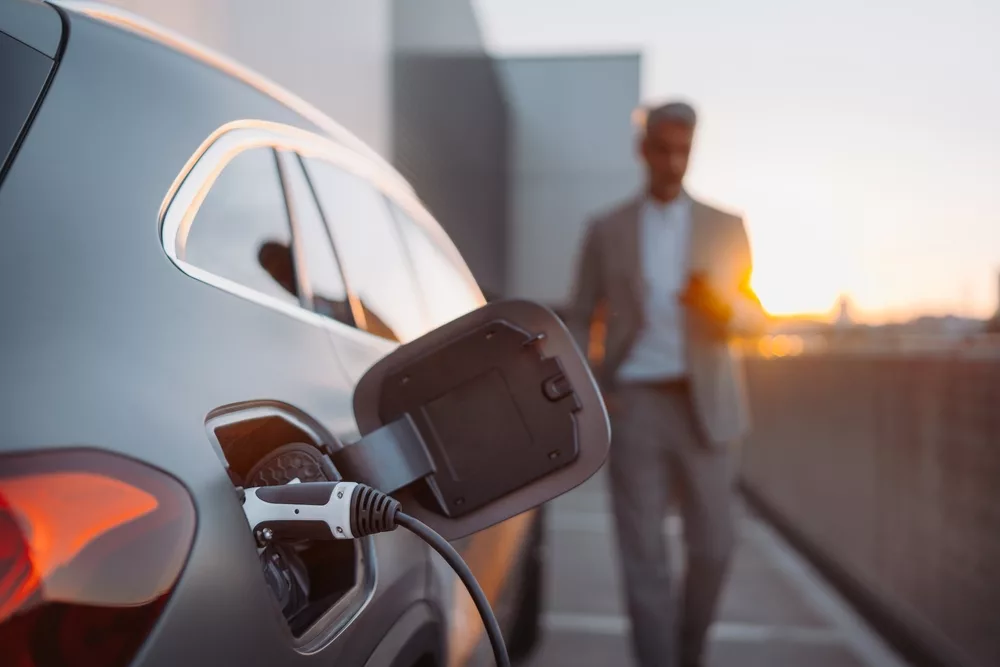
Manufacturers’ challenges
Even for car manufacturers located outside of the UK, the change in deadline is a huge nuisance. As the UK is a crucial market for European automakers, many have been working towards the 2030 deadline for their entire fleet to ensure that all vehicles are prepared for UK travel. Many have used the deadline to direct product development strategy.
Immediately off the back of the deadline announcement, several manufacturers announced that they’ll still be proceeding with their own internal deadlines with Stellantis committing to 100 per cent zero emission new car and van sales in the UK and Europe and Nissan committing to go all-electric ahead of the new legislative deadline by 2030.
In part, this is because it’s simply too late to change strategy but it’s also down to the UK EV sales scheme which requires manufacturers to sell an increasing proportion of zero emission cars each year. Up to 22 per cent of sales must be zero-emission by 2024 and 80 per cent by 2030 or manufacturers risk a fine of £15,000 per vehicle. So how can automotive manufacturers ensure their fleets are still successful on the UK market?
Reliable technology
While ensuring the sale of EVs has just got harder, the key to the industry’s success is ensuring vehicles are up to scratch and manufacturers’ brands are trusted. And that comes with a manufacturer that uses the technology and innovation to ensure vehicle safety and reliability.
Take regenerative braking technology as an example. It’s a key process in a successful EV power system that ensures any excess energy produced when a vehicle decelerates is converted back into electrical energy and stored in the battery. This increases EV range and therefore reliability over long distances.
Cressall’s EV2 is a dynamic braking resistor (DBR), which is an essential component of an EV regenerative braking system. If the battery is full or there is a failure, the EV2 removes this excess energy from the system to prevent damage.
Its modular design means that up to five units can be combined in a single assembly to achieve a power rating up to 100 kW. Its extensive design range works up to 1500 Volts terminal to terminal and a resistance of up to 20 ohms (Ω) per single module. This flexibility means the resistor can be adapted to suit any EV application — from small cars to large HGVs.
The EV shift is coming, just not as quickly as we once expected. For consumers and automakers, time is still ticking. It’s important to ensure the EV fleet is prepared for the future and consumers concerns are alleviated by producing reliable vehicles made using technology designed specifically for widespread EV adoption.
Manufacturing & Engineering Magazine | The Home of Manufacturing Industry News